一种耐酸碱腐蚀的碳化硅多孔支撑体的制作方法【技术领域】,进一步涉及碳化硅多孔支撑体的制备技术。[0002]陶瓷膜在水处理、高温烟气处理方面获得了越来越广泛的应用,在环境保护中发挥了重要作用。但其在应用过程中也暴露出不少问题,现有以氧化铝为主要材质的陶瓷膜支撑体的主要问题是难以在强腐蚀性环境下长期使用。[0003]研究表明,纯氧化铝多孔支撑体在100°C的10wt%氢氧化钠溶液中腐蚀8h后,其强度损失达80%以上,在100°C的20被%硫酸溶液中腐蚀8h后强度也下降了近10%。主要原因在于:(1)氧化铝的两性特征在本质上决定了其耐腐蚀性能的不足;(2)为降低氧化铝多孔支撑体的烧成温度,采用了粘土等作为烧结助剂,氧化硅组分成为导致支撑体耐碱性能差的原因之一,而矿物中的杂质金属离子则是减弱其耐酸性能的重要原因;(3)为了保证支撑体高的连通气孔特性,往往采取欠烧方式,未完全发育的烧结颈成为支撑体被腐蚀和破坏的薄弱环节。[0004]支撑体材质面向不同应用领域有莫来石、堇青石、碳化硅等。US8011519B2专利中所述莫来石多孔过滤管,在硝酸和氢氧化钠热溶液中腐蚀4个循环后(腐蚀条件为:pH值分别为0.5和13.5,溶液温度为95°C,每个循环在酸/碱溶液中腐蚀24h),强度保持率只有80%左右。堇青石质支撑体的耐碱性能显著改善,在100°C的10wt%氢氧化钠溶液中腐蚀8h后,其强度仅下降12%左右,但在100°C的20被%硫酸溶液中腐蚀8h后强度保持率仅为55%,耐酸性能较差。[0005]在高温除尘应用方面,ZL201010297960.0、ZL201210103839.9、ZL201010234149.8和ZL200810017051.X均涉及 以碳化硅为主要材质的支撑体,通过碳化硅的高热导率和较低的热膨胀系数,改善了高温除尘用陶瓷膜的抗热震性,但这些方法均采用了 7%以上的陶瓷结合剂,结合剂易与烟气中的烟粒形成低共熔相,从而破坏支撑体的耐高温和耐腐蚀性能。此外,将碳化硅支撑体用作为水处理膜支撑体时,陶瓷结合剂也将是易被酸碱腐蚀的薄弱相。[0006]ZL201010525702.3所述的高纯度单相碳化硅多孔体可通过反应烧结、高温排硅与再结晶相结合的方法得到,但受反应生成碳化硅的碳形貌的影响,孔结构不佳。CN102389719所述方法可以得到高耐腐蚀性能的SiC陶瓷膜支撑体,但其在800°C左右空气中煅烧去除起结合作用的有机粘结剂后,仅依靠细颗粒碳化硅表面氧化的二氧化硅将坯体结合,致使预烧坯体强度低,最终产品合格率低,其次,它通过细颗粒的蒸发一凝聚作用沉积在粗颗粒颈部形成结合相,由于原料中细颗粒较少,形成的结合相较少,导致其强度偏低,此外,其再结晶温度较高(高于2200°C ),部分碳化硅气相沉积在支撑体表面并生长成大晶粒,增加了表面粗糙度,不利于后续在其表面制备陶瓷膜的工艺。ZL200910155765.1中采用纳米碳化硅与粗碳化硅为原料在2200-2250°C下得到性能优异的再结晶碳化硅多孔材料,这种方法的不足是使用了 16%以上的纳米碳化硅,且再结晶温度也在2200°C,成本显著提高。
[0007]本发明的目的在于提供一种耐酸碱腐蚀性能优异的碳化硅多孔支撑体,以解决现有陶瓷膜支撑体的上述不足。
[0008]为实现上述目的,本发明的技术方案是:
[0009]一种耐酸碱腐蚀的碳化硅多孔支撑体,原料重量份组成为:
[0010]碳化娃粉:粗颗粒和细颗粒混合料100份
[0011]烧结助剂:氧化铝0.5份-6份、稀土氧化物0.5份~7份
[0012]无机结合剂:硅溶胶,以固体含量计,0.5份~5份
[0013]有机粘结剂1份~4份
[0014]造孔剂0.2份~10份
[0015]润滑剂0.5份~3份
[0016]水 12份~25份;
[0017]制备方法为:
[0018](I)按所述重量份比例混料、捏合、练泥、陈腐制成泥料;
[0019](2)将泥料挤制成生坯,将生坯在空气氛围中于200°C~850°C的温度下煅烧脱脂并去除有机造孔剂,得煅烧料;
[0020](3)将煅烧料在惰性氛围或真空条件下分段煅烧,先在1600°C~1750°C保温0.5h ~3h,然后在 1800°C~2000°C保温 0.5h ~3h,再在 2050°C~2200°C保温 0.5h ~4h得到碳化硅多孔支撑体。
[0021]所述碳化娃粉粗颗粒和细颗粒混合料中粗颗粒粒径为10 μ m~100 μ m,细颗粒粒径小于2 μ m,粗颗粒占碳化硅总质量百分数为55%~85%。
[0022]优选方案,所述粗颗粒为20 μ m~40 μ m,所述细颗粒粒径小于0.7 μ m。
[0023]所述氧化铝为α -氧化铝粉、Y -氧化铝粉、铝溶胶中的一种或几种。
[0024]所述稀土氧化物为氧化钇、氧化铈、氧化镧中的一种或几种。
[0025]所述硅溶胶为碱性硅溶胶,其固体粒子含量优选在10%~40%之间,粒子直径范围优选为20nm~lOOnm。硅溶胶在碳化硅生坯高温煅烧后起到过渡粘结的作用,在高温烧制过程中也起到一定的造孔作用。
[0026]所述造孔剂为碳粉、淀粉、聚乙烯、聚甲基丙烯酸甲酯中的一种或几种。
[0027]所述粘结剂为聚乙烯醇、聚乙二醇、淀粉及其衍生物、纤维素醚及其衍生物中的一种或多种。
[0028]所述润滑剂为桐油、大豆油、菜籽油等中的一种或多种。
[0029]所述分段煅烧工艺为:在惰性氛围或真空条件下,通过①从室温至1600°C~1750°C,升温速率为5°C /min~30°C /min,②在1600°C~1750°C保温0.5h~3h,③从1600°C ~1750°C 至 1800°C ~2000°C,升温速率为 5°C /min ~30°C /min,④在 1800°C ~2000°C保温 0.5h ~3h,⑤从 1800°C~2000°C至 2050°C~2200°C,升温速率为 5°C /min ~300C /min ;⑥在 2050°C~2200°C保温 0.5h ~4h。
[0030]下面对本发明做进一步解释和说明:[0031]本发明碳化硅多孔支撑体的制备方法,包含以下几个方面:
[0032](I)将固态原料(碳化硅粉、烧结助剂、粘结剂、造孔剂等)和液态原料(硅溶胶、润滑剂、水)按(I)中比例分别预混合,然后将液态原料逐步加入到固态原料中混合,进一步经捏合、练泥、陈腐制成塑性泥料。
[0033](2)将泥料通过模具挤出成型,干燥后得到生坯,在空气氛围下200°C~850°C煅烧脱脂并去除有机造孔剂;
[0034](3)将经步骤(2)煅烧的制品在惰性氛围或真空条件下,通过①室温到1600°C~1750 °C,升温速率为 5 °C /min ~30 V /min,②在 1600 V ~1750 V 保温 0.5h ~3h,③ 1600°C~1750°C到 1800°C~2000°C,升温速率为 5°C /min ~30°C /min,④在 1800°C~2000°C保温 0.5h ~3h,⑤ 1800°C ~2000°C 到 2050°C ~2200°C,升温速率为 5°C /min ~300C /min ;⑥在2050°C~2200°C保温0.5h~4h的烧成制度获得碳化硅多孔支撑体。
[0035]本发明的显著特点是:
[0036](I)优选由氧化铝与稀土氧化物组成的烧结助剂来实现纯碳化硅多孔陶瓷在相对较低的温度下实现液相烧结,降低其烧成温度,该助剂在高温下(1800~2000°C)形成能溶解高活性碳化硅细粉的液相,通过液相的溶解及传质作用使分散的碳化硅细粉在粗颗粒间形成强的结合颈,一方面显著提高了支撑体的强度,另一方面,细粉迁移后留下了大量空位,形成了连通大孔结构,可有效降低流体通过支撑体的阻力,有助于提高陶瓷膜的过滤通量;随着热处理温度的进一步升高(2050~2200°C),液相烧结助剂与碳化硅在惰性气氛下反应形成气相产物并从孔隙中逸出,减少了碳化硅晶界上的薄弱相,使界面结构更为纯净,进一步改善了碳化硅支撑体的耐酸碱腐蚀性能。
[0037](2)有机粘结剂与硅溶胶结合剂在不同温度区间分别发挥结合剂的作用,确保了支撑体生坯和煅烧坯体在搬运、加工中所需的强度,减少了工艺过程的破损,提高了成品 率。
[0038](3)通过低温造孔与高温造孔协同作用,即空气条件下低于850°C的有机物分解与碳氧化的造孔及惰性氛围或真空下1600°C以上氧化物助剂与碳化硅反应形成气相产物的造孔,提高了支撑体的孔隙率及开孔度。
[0039]与现有技术相比,本发明的有益效果为:
[0040](I)低温造孔与高温造孔相结合,提高了支撑体的孔隙率及开孔度:空气条件下低于850°C的煅烧,使有机物分解和碳氧化,形成了低温造孔;在1600°C以上惰性或者真空条件下,氧化铝、稀土氧化物及氧化硅(源于硅溶胶)与碳化硅反应形成气相产物,该产物的逸出实现了高温造孔。
[0041](2)无机结合剂硅溶胶的使用,不仅使支撑体在有机粘结剂分解后仍具有较高的强度,减少了支撑体的低温破损率,而且其最终形成的氧化硅在高温下(1600~1750°C)与碳化硅反应生成气相逸出,可进一步提高支撑体的孔隙率。
[0042](3)使用亚微米级碳化硅及适宜的液相烧结助剂,有利于碳化硅细粉在高温下(1800~2000°C)溶解于液态的烧结助剂中,并在粗颗粒间沉淀析出形成烧结颈,溶解一沉淀过程形成了含有少量液相烧结助剂的碳化硅颈部,而在随后更高温度(2050~2200°C)的热处理中使大部分烧结助剂与碳化硅反应生成气相逸出,使颈部界面洁净化,提高了碳化硅支撑体的耐腐蚀性能。[0043](4)通过本发明得到的碳化硅多孔支撑体的孔隙几乎全部为开口气孔,孔隙形貌较好(如图1所示),气孔率在35%~55%之间,抗弯强度达到40MPa~llOMPa,在20wt%的硫酸中于90°C腐蚀IOOh后强度保持率大于88%,在20wt%的氢氧化钠溶液中于90°C腐蚀IOOh后强度保持率大于92%。与氧化铝陶瓷膜支撑体、氧化物结合碳化硅陶瓷膜支撑体相t匕,本发明得到的支撑体开孔度、孔形貌、处理效率以及耐腐蚀性能更优;与文献报导的再结晶碳化硅陶瓷膜支撑体相比,其烧成温度更低,在同等孔径、孔隙率条件下强度更高,更有利于后续制膜工艺。不同陶瓷膜支撑体的主要性能对比如表1所示。
[0044]表1不同材质陶瓷膜支撑体性能对比
[0045]
一种耐酸碱腐蚀的碳化硅多孔支撑体制作方法
- 专利详情
- 全文pdf
- 权力要求
- 说明书
- 法律状态
查看更多专利详情
下载专利文献
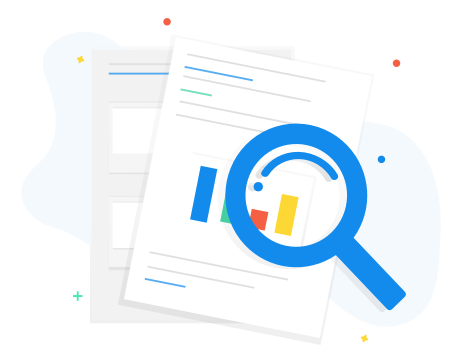
下载专利
同类推荐
-
陈海标, 潘锋陈海标, 潘锋陈海标, 潘锋陈海标, 潘锋
您可能感兴趣的专利
-
庄钰坪杨志峰刘建龙包娟娟
专利相关信息
-
邓树军姜忠, 杨建民姜忠, 杨建民姜忠, 杨建民L·T·坎哈姆, C·P·巴雷特郭兴忠