一种高质量氮化铝陶瓷基片的微波快速烧结方法[0002]氮化铝陶瓷是近几年发展起来的一种新型陶瓷材料,由于其导热率高和绝缘性能好而使其在许多领域有着广泛的应用,其优良的热性能、机械性能使其在高功率封装以及多芯片组装等领域用作高散热基板,大有取代氧化铍、碳化硅及氧化铝的趋势,在微电子、光电子、电力电子及功率电子等领域具有广阔的应用前景。从市场增长率来看,它是目前市场增长最快的陶瓷材料之一,据Keramont公司统计,欧、美、日等国的氮化铝基片的市场需求增长率分别为60%、80%和40%,封装的市场增长率接近100%。在国内,氮化铝基片的市场需求也在急剧增长。[0003]氮化铝陶瓷作为一种新型的高导热非氧化物陶瓷材料,目前国内还没有可供借鉴的成熟工艺和工艺设备,国外对氮化铝制备技术报道也很少。氮化铝陶瓷是一种难烧结的非氧化物材料,在高温下无熔点,直接升华,氮化铝陶瓷的烧结通常采用添加烧结助剂的常压烧结或在高温加压的热压条件下烧结而成。热压烧结的设备成本高且一次烧结量较少,烧结周期长且烧结损耗较大,造成氮化铝陶瓷基片的成本偏高,难以适应激烈的市场竞争。常压烧结所需设备相对简单,生产成本低,但烧结温度高,易变形,不易致密化,造成氮化铝陶瓷基片的质量无法保障。
[0004]本发明要解决的技术问题是,针对现有技术存在的缺陷,提出一种新的高质量氮化铝陶瓷基片的快速烧结方法, 采用此方法,可以加快烧结进程,在较低的温度、较短的时间内,在常压下烧结出致密的高质量氮化铝陶瓷基片。具有升温速度快,烧结温度低,保温时间短,性能较好,节约能源,生产效率高的特点,适合大规模生产。[0005]本发明的技术解决方案是,所述高质量氮化铝陶瓷基片的快速烧结方法为:将排胶后的氮化铝陶瓷基片坯体放入微波烧结腔内的辅热保温结构内,叠放整齐,片与片之间均匀的撒上氮化硼粉末,辅热保温结构由氧化铝纤维板、氮化硼匣钵以及高纯石墨板构成,微波烧结频率为2.45GHz,通入含氢6~10%的氮气氛,常压微波烧结温度1700~1750°C,升温速率为8~10°C /min,保温2小时,随炉冷却,至400°C以下时开炉取出,得到致密的高质量氮化铝陶瓷基片烧结体。[0006]本发明的工作原理是:利用微波能转化为分子的动能和热能,以一种“体加热的方式”整体均匀加热,不易变形,且由于微波的活化性能,在较低的温度致密烧结氮化铝陶瓷基片,成本大幅度下降,再结合高纯石墨板的微波反射效果及还原性气氛的激发,通过含氢的氮气氛在烧结后期的晶界净化,最终得到高质量的氮化铝陶瓷基片。[0007]本发明的有益效果是,微波烧结是利用微波加热对材料进行烧结,它同传统的加热方式不同,传统的加热是依靠发热将热能通过对流、传导或辐射方法传递至被加热物质而达到某一温度,热量从外向内传递,烧结时间长,能耗高;而微波烧结是利用微波具有的特殊波段与材料的基本结构耦合而产生热量,材料的介质损耗使其材料整体加热的一种加热方式,再结合特殊的微波烧结结构和烧结工艺快速均匀烧结,因而具有烧结温度低、保温时间短、改善烧结环境、能耗低等一系列优势。故微波加热的效率高,比传统方法省电30~70%,大大降低了生产成本,而且工业微波炉结构简单,自动化运行,易于维护。
[0008]为了更清楚地说明本发明的实施例,下面对实施例中需要使用的附图做简单的介绍,显而易见地,下面描述的附图仅仅是本发明的一些实施例,不能认为是对本发明的保护范围的限制。
[0009]图1为本发明实施例的高质量氮化铝陶瓷基片的微波快速烧结方法中氮化铝陶瓷基片的微波炉内烧结时的示意图。
[0010]
[0011]将排胶后的氮化铝陶瓷基片坯体放入微波烧结腔内的辅热保温结构内,叠放整齐,片与片之间均匀的撒上氮化硼粉末。氮化铝陶瓷基片坯体的最大尺寸不超过150_。微波烧结腔为类似球形或圆柱形状腔体,且以30转/min的速度匀速旋转。辅热保温结构由氧化铝纤维板、氮化硼匣钵以及高纯石墨板构成,如图1所示,高纯石墨板最大尺寸与氮化铝陶瓷基片坯体的最大尺寸一致,能覆盖整个氮化铝陶瓷基片坯体,且上石墨板直接压在氣化招陶瓷基片还体上,两块闻纯石墨板之间的距尚范围是石墨板最大尺寸的1/2至石墨板最大尺寸。微波烧结频率为2.45GHz,通入含氢6~10%的氮气氛,常压微波烧结温度1700~1750°C,升温速率为8~10°C /min,保温2小时,随炉冷却,至400°C以下时开炉取出,得到致密的高质量氮化铝 陶瓷基片烧结体。
[0012]下面结合实施例对本发明作进一步说明。
[0013]实施例1:
排胶后的氮化铝陶瓷基片坯体I放入微波烧结腔内的辅热保温结构内,叠放整齐,片与片之间均匀的撒上氮化硼粉末,氮化铝陶瓷基片坯体I尺寸为150mmX150mmX3mm,微波烧结腔为球形腔体,以30转/min的速度匀速旋转。辅热保温结构由氧化铝纤维板2、氮化硼匣钵3以及高纯石墨板4构成,如图1所示,氮化硼匣钵3的内尺寸是180mmX 180mmX 10Omm,高纯石墨板4尺寸为150mmX 15CtamX8臟,上下石墨板之间的距离为75mm,上石墨板直接压在氮化铝陶瓷基片坯体I上。微波烧结频率为2.45GHz,通入含氢10%的氮气氛,常压微波烧结温度1750°C,升温速率为10°C /min,保温2小时,随炉冷却,至400°C以下时开炉取出,得到致密的高质量氮化铝陶瓷基片烧结体。经测定,制得的氮化铝陶瓷基片的密度为3.26g/cm3,抗弯强度为448MPa,热导率为178 ff/(m.K),烧结后表面光洁度高,呈浅黄色,颜色均匀。
[0014]实施例2:
排胶后的氮化铝陶瓷基片坯体I放入微波烧结腔内的辅热保温结构内,叠放整齐,片与片之间均匀的撒上氮化硼粉末,氮化铝陶瓷基片坯体尺寸为Φ80mmX2mm,微波烧结腔为圆柱形腔体,以30转/min的速度匀速旋转。辅热保温结构由氧化铝纤维板2、氮化硼匣钵3以及高纯石墨板4构成,如图1所示,氮化硼匣钵3的内尺寸是Φ IOOmmX60mm,高纯石墨板4尺寸为ΦSOmmX 5mm,上下石墨板之间的距离为40mm,上石墨板直接压在氮化铝陶瓷基片坯体上。微波烧结频率为2. 45GHz,通入含氢6%的氮气氛,常压微波烧结温度1700°C,升温速率为8°C /min,保温2小时,随炉冷却,至400°C以下时开炉取出,得到致密的高质量氮化铝陶瓷基片烧结体。经测定,制得的氮化铝陶瓷基片的密度为3.25g/cm3,抗弯强度为396MPa,热导率为152 ff/(m.K),烧结后表面光洁度高,呈浅黄色,颜色均匀。
一种高质量氮化铝陶瓷基片的微波快速烧结方法
- 专利详情
- 全文pdf
- 权力要求
- 说明书
- 法律状态
查看更多专利详情
下载专利文献
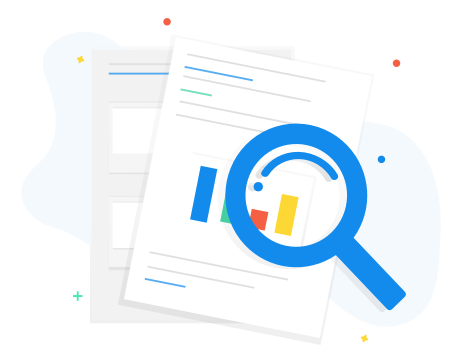
下载专利
同类推荐
-
杨润华金向基王艳辉汤玉斐
您可能感兴趣的专利
-
杨建杨建任丹
专利相关信息
-
陈继新陈继新陈继新李志刚王红云王红云