一种高强度低密度闭孔玻化微珠的制备方法[0002]闭孔玻化微珠在诸多领域中作为轻质填充骨料和绝热、防火、吸音、保温材料使用。在建材行业中,用玻化微珠作为轻质骨料,可提高砂浆的和易流动性和自抗强度,减少材性收缩率,提高产品综合性能,降低综合生产成本。在石油气井注水泥作业用油井水泥作为减轻剂。闭孔玻化微珠是由有一定粒径的珍珠岩矿砂在垂直阶梯加热方式下达到一定温度后由内到外均匀膨胀,膨胀颗粒表面又经瞬间高温玻化,经降温后形成连续玻质化的颗粒表面,而内部保持着完整的多孔、中空空心结构。独特的生广方式决定了广品保持了珍珠岩天然无机化学成份的纯度。该产品结构特征是颗粒表面呈微毛细孔并呈连续玻质化光泽,内部呈现数个或数十个微小球状堆积,色泽洁白。产品容重分布在Iio~350kg/立方,粒度分布在5~1500 μ m,具有质轻、绝热、防火、耐高低温、抗老化、吸水率小、化学稳定性好等优异特性,是一种环保型高性能新型无机轻质绝缘材料。[0003]目前,市场上制 备闭孔玻化微珠主要是以珍珠岩矿粉为原料,在干燥预热后再进入成珠炉。成珠炉由多个加温区段组成,对珍珠岩矿粉进行逐段加热,使矿粉渐进式受热膨胀,矿粉表面有一个塑变软化过程,更利于形成玻璃质外壳,有利其表面玻化,气孔封闭,生产出闭孔玻化珍珠岩产品。闭孔玻化微珠产品生产的流程大多数按照粉碎一分选一烘干预热一球化一冷却一分选一烘干一包装工序进行,其中以烘干预热、球化为重要工序,需要重点控制。球化炉的加热方式有电加热、天然气加热、煤气加热等几种,其中以电加热和天然气加热较为常见。珍珠岩矿粉烘干预热后一般由提升机送到球化炉炉体上端,矿粉由炉体上端自由落体落下,在下降过程中球化炉驿矿粉进行逐级加热。玻化微珠下降到球化炉体下部时,在炉体下部的旋风收集器和布袋收集器将已成形的玻化微珠抽走并冷却,同时将产生的大部分粉尘收集。玻化微珠冷却并收集后通过漂浮法将产品分离出来,并进行收集、烘干,包装成成品。[0004]然而,现在大多数闭孔玻化微珠产品的生产设备普遍存在着一些问题,如矿粉提升到炉体上部的释放问题,如何能做到均匀释放,没有粘连结块产生;矿粉在自由落体下降时由于重力的作用外形成型不好,很多呈水滴状而不是规则的球状,使产品的玻化温度较高,成品抗压强度较低,不能满足产品的使用要求;产品在炉体熔化形成玻璃质表面时与炉体内部产生粘连结块的现象等。以上制作方法的各种原因造成的成珠率低,产品成本较高,均较明显地影响了闭孔玻化微珠的成品率。
[0005]本发明所要解决的技术问题是提供一种高强度低密度闭孔玻化微珠的制备方法,该制备方法能够制得直径50 — 250 μ m的闭孔玻化微珠,且闭孔玻化微珠壁厚较均匀,成型形状好,抗压强度高。[0006]为解决上述技术问题,本发明所采取的技术方案是:一种高强度低密度闭孔玻化微珠的制备方法,采用以下步骤: (1).选料:选用膨润土含量〈10%,膨胀系数大于7-10倍以上的I级珍珠岩作为基础原
料;
(2).粉碎分级:将粗粉后的珍珠岩矿石粉碎并在超细磨粉机中磨细分级,所用矿粉的粒径范围为5 - 15 μ m之间;
(3).浸润助熔:将筛选出来的矿粉在浸润池中与Li2CO3A溶性助熔剂搅拌浸泡,浸润剂为重量比例1.3:1000的Li2CO3与水的饱合溶液,浸润温度< 20°C ;
(4).烘干预热脱水分散:用气流干燥机将浸润过助熔剂的矿粉烘干、预热、脱水,解块并分散,烘干预热脱水温度为380 - 4700C ;
(5).空心玻化:将烘干好的矿粉从成珠炉内自下向上输送,成珠炉内的旋转气流带动粉料上升并逐级加热玻化,空心球化,矿粉在成珠炉内的停留时间在10 - 15秒,空心球化温度为 1050°C— 1150°C ;
(6).收集:在成珠炉顶部安装有引风机产生负压,使玻化完成的微珠上升并快速冷却空心球化,使用旋风除 尘器和布袋除尘器达到分级收集的目的;
(7).分选:利用产品的重力用风选机采用漂浮法对冷却后的玻化微珠进行分选;
(8).检验:对筛选好的闭孔玻化微珠进行抽样,检验其抗压强度、破球率、粒径分布、吸水率。
[0007]在上述所述的I级珍珠岩,其主要化学成分要求如下=SiO2 70%土,H2O 4-6%,Fe203〈l%,Al2O3 12%土,RO 1-1.3%, R2O 6-8% (R0 是 CaO 和 Mg0;R20 是碱金属氧化物 K2O 和Na2O ;)。
[0008]本发明采用上述技术方案所设计的一种高强度低密度闭孔玻化微珠的制备方法,可以使珍珠岩矿粉的熔融速率加快,并促使矿粉在克服重力因素的影响中完成球化,玻化微珠的球化效果好,能源利用率高,成球率高,效果好。
[0009]图1表示本发明高强度低密度闭孔玻化微珠制备方法的工艺流程图;
图2表示本制备方法采用的生产设备结构示意图;
图3表示本发明使用的成珠炉的结构示意图。
[0010]下面结合附图对本发明一种高强度低密度闭孔玻化微珠的制备方法作具体发明。
[0011]参见图1,图2,图3,本发明高强度低密度闭孔玻化微珠制备方法,采用以下工艺步骤:
(I).选料:选用膨润土含量〈10%,膨胀系数大于7-10倍以上的I级珍珠岩作为基础原料,I级珍珠岩的主要化学成分要求如下:Si02 7 0%土,H2O 4-6%,Fe203〈l%,Al2O3 12%土,RO1-1.3%,R2O 6-8%ο其中,RO是CaO和MgO,R2O是碱金属氧化物K2O和Na20。
[0012](2).粉碎分级:将粗粉后的珍珠岩矿石粉碎并在超细磨粉机I中磨细分级,所用矿粉的粒径范围为5 — 15 μ m之间;
(3).浸润助熔:将筛选出来的矿粉通过传输装置2在助熔剂浸润池3中与Li2CO3水溶性助熔剂搅拌浸泡,浸润剂为重量比例约1.3:1000的Li2CO3和水的饱合溶液,浸润温度< 20 0C ;
⑷.烘干预热脱水分散:将浸润助熔后的矿粉通过传输装置4输送到烘干预热隧道炉5,用烘干预热隧道炉5将浸润过助熔剂的矿粉烘干、预热、脱水,解块并分散,烘干预热脱水温度为380 - 470 0C ;
(5).空心玻化:将烘干好的矿粉经过收集输送装置6通过成珠炉下部的进料口7进入成珠炉9,进料口 7下部装有鼓风机8使矿粉向成珠炉9炉体上部流动,并通过控制鼓风机8的流量控制矿粉的上升高度。成珠炉9的炉体内安装有高度不同的旋流片14和导流气管15,通过压缩空气气流产生的压差保证含有矿粉的气流按要求在限定区域内旋转上升,同时矿粉微粒在旋转气流中跟随气流产生一定的自转,在炉体内不同高度安装有不同数量的超高温电阻带16作为加热元件,对矿粉进行逐级加热、使矿粉在成型时间内完成软化、玻化、空心球化,避免表面熔融的玻化微珠与成珠炉9炉内侧壁或其它物品相接触形成结炉现象。矿粉的球化时间根据闭孔玻化微珠的要求,矿粉在成珠炉9内的停留时间在10 -15秒,最终空心球化温度为1050°C — 1150°C ;
(6).收集:在成珠炉9 顶部安装有引风机13产生负压,使玻化完成的微珠上升并在成珠炉9顶通过冷却装置10快速冷却空心球化,使用旋风除尘器11和布袋除尘器12达到分级收集的目的;
(7).分选:利用产品的重力用风选机采用漂浮法对冷却后的玻化微珠进行分选;
(8).检验:对筛选好的闭孔玻化微珠进行抽样,检验其抗压强度、破球率、粒径分布、吸水率。
[0013]本发明上述制备方法能够制得直径50 — 250 μ m的闭孔玻化微珠。
[0014]本发明所述的成珠炉9 申请人:已经对此申请了专利,申请号为201420160180.5,参见图3,在成珠炉9的炉体从下到上依次设置内腔贯通的粉料输送区、升温加热区、高温瞬膨区、冷却区及输出区,矿粉微粒是从该成珠炉底部进入,在克服重力的作用下,球化了的闭孔玻化微珠从成珠炉顶部得到了收集,这样制得的空心玻璃微珠壁厚较均匀,抗压强度得到了很大的提高。
[0015]本发明和传统的闭孔玻化微珠制作方法相比,在矿粉加热玻化时,通过特制的成珠炉,矿粉由成珠炉的底部向顶部移动,使每个空心玻璃微珠的壁厚较均匀,有效地提高了玻璃原料微粉的球化率和成珠率,还显著提高了产品的抗压强度,同时由于导流旋流装置的作用,很好的避免熔融的玻璃微珠与成珠炉内的炉壁和其它元器件碰撞,有效地减少了结炉和粘连现象的产生。
一种高强度低密度闭孔玻化微珠的制备方法
- 专利详情
- 全文pdf
- 权力要求
- 说明书
- 法律状态
查看更多专利详情
下载专利文献
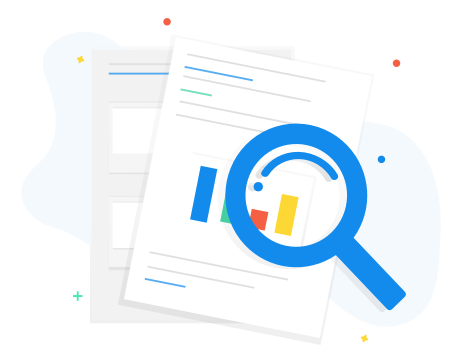
下载专利
同类推荐
-
赵友谊梁晓怿, 赵欣侯卫权
您可能感兴趣的专利
-
杨金龙杨守华施晓旦, 郭和森施晓旦, 郭和森
专利相关信息
-
王圣茂保罗·斯莱克王世杰陈发荣, 赵正杨