专利名称:一种苎麻纤维及其用途以及苎麻纤维的提取和制备方法 我国是世界上麻类资源最为丰富的国家之一,我国不但麻类资源丰富,而且麻纺织行业的生产能力和纺织产品在国际上也有了一定的竞争力,目前我国麻类纺织品主要有苎麻纺织品、亚麻纺织品、大麻纺织品、罗布麻纺织品、黄洋麻纺织品、剑麻纺织品等。在健身、安全、防治疾病等纺织品新市场中,苎麻、亚麻、大麻等麻类纤维开发的功能性麻纺织品不仅许多是符合绿色消费的环保产品,而且已被公认为是一种典型的原料性保健纺织品。但是现在技术中对麻类纤维的提取和制备的方法,还存在以下问题譬如,麻纤维粗糙,公支数比较低,不能获得高支优质麻纱,麻纤维的染色性能差;譬如,纤维脱胶技术不完善,纤维的自身结构结晶度高,定向度高。麻纤维制备过程中对水的浪费大,对环境污染大等。在提取和制备麻纤维时,加工过程不合理,对纤维损伤大,对纤维的制成率偏低,造成经济效益低。因此,需要改进目前麻纤维的提取和制备工艺,获得符合要求的高质量麻纤维,并进而通过对该麻纤维具体运用,获得高质量的纺织品。
本发明的目的在于提供一种优质的苎麻纤维和使用了该麻纤维制造出来的纯麻纱、混纺纱、以及麻纤维和其他纤维的混合物(如无纺布的原料),以及一种苎麻纤维的提取和制备方法。本发明的人工提取的苎麻纤维,其特征在于,该苎麻纤维为2500-4500公支,甚至4500公支以上;该苎麻纤维制成的纯苎麻纱为32S-60S的纱线,甚至可以为60S以上的纱线;该苎麻纤维制成的混合、混纺纱为40S-120S的纱线,甚至可以为120S以上的纱线。而目前苎麻纤维可以达到的纤维细度一般在1500-1800公支,长度50-60mm,纤维挠曲度差,纯麻纱最高只能纺21S(英支),远远满足不了市场的需求。本发明的苎麻纤维,在此又可称为超细纤维麻。本发明的苎麻纤维,可以做成直接可用于纺织品的纯麻纱,也可以将其与动物纤维、植物纤维、化学纤维一起进行混纺或者混合,含有该麻纤维的纯麻纱以及混合、混纺纱也落入本发明的保护范围之内。本发明还提供了一种苎麻纤维的提取和制备方法。现有麻纤维不能纺高支优质纱的原因主要是麻纤维中含有大量果胶、色素、蜡质、木质素等等,果胶等粘连包裹在纤维表面和内部,故纤维难以有效分离和牵伸。木质素使纤维脆化、手感差、颜色暗淡,以及麻纤维分子结构结晶度高、取向度高。这些使得纤维弹性可挠度大大降低。而目前麻纤维提取和制备工艺不能很好解决上述问题,存在纤维强度损伤大、难以控制最佳分裂度等问题,这使得我们难以获得优质麻纤维。例如,就苎麻纤维而言,苎麻纤维目前获取单纤维脱胶方法采用碱煮法为主,主要有二煮法、二煮一练法、二煮一漂法和二煮一漂一练法等。其获取的纤维细度在1500-1800公支,长度50-60mm,纤维挠曲度差,纯麻纱最高只能纺21S(英支),远远满足不了市场的需求。本发明采用特殊的苎麻纤维提取和制备工艺,能够克服现有技术中存在的种种问题,从而首次能够在工业应用中获得实用的高支纤维纱。本发明的方法获得的苎麻纤维可达2500-4500公支甚至4500公支以上,而且纤维分子取向度、结晶度变小,纤维膨松,卷曲性大大提高,其提取和制备采用新工艺二煮二漂高温分裂法。
主要原理在传统获取单纤维原理上,进一步对纤维进行分裂,可使纤维表面分裂解,纤维可比原纤维细30%左右,纤维内部分子膨松、手感柔软。
本发明中提取、制备优质高支苎麻纤维的工艺方法简称两煮两漂高温分裂法,其特点在于进行苎麻纤维的提取和制备时,含有两次漂白、两次碱煮,并且进行高温分裂的步骤。具体而言,两次漂白分别为氯漂和氧漂,氯漂使用浓度为3-8G/L(克/升)的次氯酸钠,温度35-45℃,时间40-80分钟。氧漂用双氧水4-6G/L,温度80-100℃,时间40-80分钟。碱煮进行两次,第一次用烧碱进行碱煮。高温分裂在两煮两漂后进行,高温分裂时采用浓度为100-140G/L的纯碱,温度100-140℃,时间1.5-2.5小时。
对苎麻纤维的提取和制备,其步骤还可以进一步限定为浸酸→水洗→一煮→水洗→一漂→酸洗→二煮→水洗→二漂→高温分裂→水洗→给油→脱水→烘干注采用上述方法提取、制备苎麻纤维的说明苎麻纤维是由一个细胞组成的单纤维,其纤维长度是麻类植物纤维中最长的。麻纤维中存在着大量的果胶、腊质、木质素等不利于纺高支优质麻纱的杂质,采用上述步骤可以有效提取、制备苎麻纤维,其中对所涉及重要步骤详细描述如下1浸酸采用浸酸去除纤维表面的色素等杂质,溶解一部分果胶、腊质、木质素等杂质。本发明人通过多次试验发现将所用硫酸浓度控制在2-10G/L,温度40-60℃,时间1-2小时时,能取得好的技术效果。其中,针对苎麻原料杂质含量的不同,可以对硫酸含量进行适当调节,对杂质含量高的原料硫酸浓度可以在上述范围内稍微高些,而对杂质含量低的原料硫酸浓度则可以稍微低些。
优选地,将硫酸浓度控制在4-8G/L,温度控制在45-55℃,时间控制在75-110分钟时,去除色素和溶解的效果会更好。
2碱煮碱煮要进行两次,即上述步骤中的一煮和二煮。碱煮的目的是为了溶解纤维表面的果胶、腊质、木质素等杂质及半纤维素,使得纤维组织膨松,手感柔和。为达此目的,将碱煮条件控制为烧碱用量50-150G/L,时间为1.5-2小时,温度为90-140℃(采用的温度较高,目的是为了使纤维组织更为膨松,烧碱深入纤维内部,除净杂质)。这样就能获得较佳的碱煮效果,使获得的纤维组织更为蓬松,烧碱深入纤维内部,并有效除净杂质。
优选地,将碱煮条件设定为如下条件可以获得更好的技术效果烧碱用量70-120G/L,时间为100-115分钟,温度为110-130℃。
3漂白漂白采用两漂法,即上述步骤中的一漂和二漂。
采用二漂法,先氯漂,即一漂,去除纤维杂质,特别是去除纤维中的木质素,使纤维白净、手感柔和。氯漂时,使用浓度为3-8G/L的次氯酸钠,温度35-45℃,时间40-80分钟。再氧漂,即二漂,目的使分子结构膨松,纤维更光滑,使粘连的杂质与纤维脱离,纤维有效分离和容易牵伸,用双氧水4-6G/L,温度80-100℃,时间40-80分钟。
优选地,氯漂时,使用浓度为4-7G/L的次氯酸钠,温度35-45℃,时间50-70分钟。氧漂时,用双氧水4-6G/L,温度80-100℃,时间55-75分钟。此时,可以获得更好的漂白效果。
4高温分裂高温分裂的目的是为了使纤维彻底分离,此时需要根据对时间和温度的调节控制纤维细度。通过多次试验和测试,发现在采用前述处理步骤的基础上,采用浓度为100-140G/L的纯碱,温度100-140℃,时间1.5-2.5小时,会获得非常好的高温分裂效果,使得纤维彻底分裂,并获得细度均匀的纤维。
优选地,高温分裂时采用110-130G/L的纯碱,温度110-135℃,时间100-140分钟。
5给油采用植物油,用剂为纤维质量的1-2%,使纤维不粘连在一起,使纤维更柔和,提高了纤维的挠曲度、光洁度、柔软度。
以上各个步骤工艺浴比1∶10-20(每公斤纤维用10-20公斤溶液)。
使用本发明方法制备的苎麻纤维产品,通过试验测定,相关指标为
这些指标要远远优于现有技术生产出来的麻纤维的指标。比如现有技术中苎麻的线密度一般为7.5(dtex),而本发明中实测出的线密度为3.3(dtex)。
使用本发明的方法,可以制得如下性能优异的苎麻纤维、纯麻纱、混纺纱1、用本发明提取的苎麻纤维,一般均在2500公支以上,高的可以达到4500公支,甚至可以达到4500公支以上,而且纤维分子取向度、结晶度变小,纤维膨松,卷曲性大大提高,能够纺32S-60S甚至60S以上的纯苎麻纱(当然也含32S以下的用该发明工艺制成的纯苎麻纱),填补了世界空白。
2、用本发明提取苎麻纤维与各种比例的动物纤维、植物纤维、化学纤维等进行混合、混纺,可以制得40S以上的混合、混纺纱,高的甚至可以达到120S,甚至120S以上(当然也可以制得40S以下的混合、混纺纱)。
3、用本发明提取苎麻纤维可直接进行麻纤维染色,与多种纤维进行混合、混纺,解决由于不同属性纤维后整理及染色的困难,以及直接对麻纤维制作出来的织物进行染色。由此大大提高纯麻织物及苎麻纤维与其他纤维混纺织物的质量,降低消耗,提高产品档次,确保麻织物风格。
4、总之,在苎麻纤维的提取和制备上,由于传统工艺用敲打、冲洗使纤维流失,脱胶不均匀,损伤纤维,在后面的加工工艺中造成纤维大量流失,用本发明生产出来的纤维与传统工艺相比多提取10%的纤维。在浸泡液中,果胶可进一步提纯进行深加工,特别是此项技术的推广运用,由于纤维的脱胶,将大大减少染厂污水排放,减少工作环境对工人的侵害。此项发明对环境的保护,对能源的节约、利用是划时代的,该方法加工出来的麻类织物,除保护原来的抗菌、防紫外线、透气的优点,还变得平整、光滑、舒适,抗皱性能大大改善。
采用本发明能够产生很高的综合效益。本发明首次获得了2500-4500公支,甚至4500公支以上的苎麻纤维,首次获得了纯苎麻纱为32S-60S的纱线,甚至可以为60S以上的纱线,进而还可以将该苎麻纤维制成的混合、混纺纱做成40S-120S的纱线,甚至可以为120S以上的纱线。本发明的方法使得纯麻高支优质纱的工业化生产成为可能,填补了世界纺织业的空白,大大提高了生产效益和经济效益。用该方法获取的麻纤维,可以和植物纤维、动物纤维、化学纤维的混纺变得容易可行,且产品质量更加稳定,产品档次也将大大提升。本发明方法获取的麻纤维可以直接染色,使得色纺麻纱成为可能,将使麻纺产品及麻与其他纤维混纺或交织的产品提升新的市场空间。由于本发明获得的纤维蓬松,可以直接进行染色,性能优良,使用该纤维制造布面料时,可以不进行前处理,与传统工艺相比,该发明大大降低了化工原料的消耗,大约可以节约30%的染化料,工艺时间缩短,用该发明制造的纤维生产的纺织品每吨可节约工业用水300吨,并相应地减少了污水的排放,并节约了大量能源。本工艺果胶、木质素等杂质的去除,使得纤维分子结构膨松,定向度、结晶度降低,从而使得产品得色深浓、鲜艳,色牢度好。
下面结合
对本发明进行更为详细的描述。应当指出的是,下列实施例仅仅是说明性的,并不意味着对本发明的范围进行限定,本发明由所附权利要求及其等同物的范围所限定。
实施例1一种苎麻纤维的提取和制备方法采用两煮两漂高温分裂法,先准备好苎麻原料,再用这些原料进行相应的苎麻纤维提取和制备,整个工艺过程中含有两次漂白、两次碱煮,且进行高温分裂的步骤,两次漂白分别为氯漂和氧漂,氯漂使用浓度为6G/L的次氯酸钠,温度40℃,时间60分钟,氧漂用双氧水5G/L,温度92℃,时间60分钟;碱煮进行两次,第一次用烧碱进行碱煮;高温分裂在两煮两漂后进行,高温分裂时采用浓度为120G/L的纯碱,温度120℃,时间2小时。
实施例2一种苎麻纤维的提取和制备方法采用两煮两漂高温分裂法,先准备好苎麻原料,再用这些原料进行相应的苎麻纤维提取和制备,整个工艺过程中含有两次漂白、两次碱煮,且进行高温分裂的步骤,两次漂白分别为氯漂和氧漂,氯漂使用浓度为8G/L的次氯酸钠,温度35℃,时间80分钟,氧漂用双氧水6G/L,温度85℃,时间80分钟;碱煮进行两次,第一次用烧碱进行碱煮;高温分裂在两煮两漂后进行,高温分裂时采用浓度为100G/L的纯碱,温度140℃,时间1.5小时。
实施例3苎麻纤维的提取和制备方法,以及相应纯麻纱、混纺纱的制备将苎麻原料进行浸酸,硫酸浓度为5g/L,温度55℃,时间90分钟。
捞出苎麻原料,进行水洗。
将水洗后的苎麻原料进行第一次碱煮,即一煮,一煮采用碱煮,条件为烧碱90G/L,时间110分钟,温度120℃。
将一煮后的苎麻原料进行水洗。
漂白苎麻原料。漂白采用氯漂,使用浓度5G/L的次氯酸钠,温度40℃,时间60分钟。
进行酸洗,以除去氯漂中存留下来的氯离子。
将酸洗后的苎麻原料进行第二次碱煮,即二煮。二煮的条件同一煮。
再次进行水洗。
进行氧漂,用双氧水5G/L,温度90℃,时间60分钟。
进行高温分裂。高温分裂时采用120G/L的纯碱,温度120℃,时间120分钟。
进行水洗。
给麻纤维给油。给油时采用植物油,用剂为纤维质量的1.5%。
以上工艺浴比1∶15。
对给油后的纤维进行脱水处理,然后进行烘干,制得苎麻纤维。经检测,其线密度为3.0dtex(3300公支)。
将制得的部分苎麻纤维按常规工艺进行纺纱,可制得40S纯苎麻纱。
将制得的部分苎麻纤维按常规工艺和美国长绒棉纤维进行混纺,制得80S混纺纱(麻纤维55%,棉纤维45%)。
以上步骤中,没有进行具体说明的方法,均是本领域技术人员知晓的常规方法。
实施例4苎麻纤维的提取和制备方法,以及相应纯麻纱、混纺纱的制备除以下特别注明外,该实施例中苎麻纤维的提取和制备,纯麻纱、混纺纱的制备同实施例3。
浸酸时,硫酸浓度为10G/L,温度45℃,时间60分钟。
一煮条件为烧碱50G/L,时间120分钟,温度110℃。
氯漂时使用浓度8G/L的次氯酸钠,温度35℃,时间80分钟。
氧漂时用双氧水4G/L,温度100℃,时间70分钟。
高温分裂时采用130G/L的纯碱,温度135℃,时间120分钟。
给油时采用植物油,用剂为纤维质量的1.8%。
以上工艺浴比1∶20。
制得的苎麻纤维经检测,其线密度为2.5dtex(4000公支)。
将制得的部分苎麻纤维使用棉纺设备按常规工艺进行纺纱,可制得48S纯苎麻纱。
将制得的部分苎麻纤维按常规工艺和美国长绒棉纤维进行混纺,制得100S混纺纱(麻纤维55%,棉纤维45%)。
实施例5苎麻纤维的提取和制备方法,以及相应纯麻纱、混纺纱的制备除以下特别注明外,该实施例中苎麻纤维的提取和制备,纯麻纱、混纺纱的制备同实施例3。
浸酸时,硫酸浓度为4G/L,温度55℃,时间75分钟。
一煮条件为烧碱70G/L,时间115分钟,温度120℃。
氯漂时使用浓度7G/L的次氯酸钠,温度40℃,时间55分钟。
氧漂时用双氧水6G/L,温度80℃,时间75分钟。
高温分裂时采用110G/L的纯碱,温度135℃,时间130分钟。
给油时采用植物油,用剂为纤维质量的2.0%。
以上工艺浴比1∶10。
制得的苎麻纤维经检测,其线密度为2.0dtex(5000公支)。
将制得的部分苎麻纤维利用棉纺生产线进行纺纱,可制得48S纯苎麻纱。
将制得的部分苎麻纤维使用羊绒精纺生产线与羊绒纤维混纺,制得100S混纺纱(麻纤维40%,羊绒纤维60%)。
本发明主要涉及一种优质、高支苎麻纤维,其可以达到2500-4500公支,甚至4500公支以上,以及提取、制备该苎麻纤维的工艺方法,简称两煮两漂高温分裂法。该方法的特点在于进行苎麻纤维的提取和制备时,含有两次漂白、两次碱煮,并且进行高温分裂的步骤。两次漂白分别为氯漂和氧漂,氯漂使用浓度为3-8G/L(克/升)的次氯酸钠,温度35-45℃,时间40-80分钟。氧漂用双氧水4-6G/L,温度80-100℃,时间40-80分钟。碱煮进行两次。高温分裂在两煮两漂后进行,高温分裂时采用浓度为100-140G/L的纯碱,温度100-140℃,时间1.5-2.5小时。本发明还涉及上述苎麻纤维制作出的纯麻纱和混合、混纺纱。
一种苎麻纤维及其用途以及苎麻纤维的提取和制备方法
- 专利详情
- 全文pdf
- 权力要求
- 说明书
- 法律状态
查看更多专利详情
下载专利文献
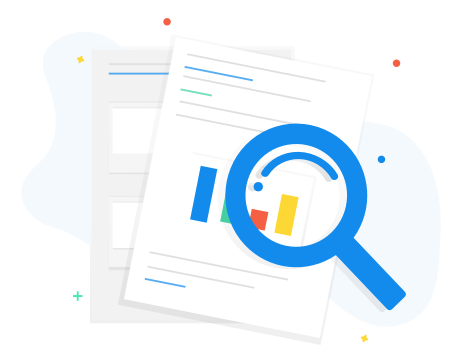
下载专利
同类推荐
-
代淑梅, 李秋园代淑梅, 李秋园代淑梅, 李秋园乔瓦尼·曼布里尼, 索尼娅·塞拉菲尼乔瓦尼·曼布里尼, 索尼娅·塞拉菲尼
您可能感兴趣的专利
-
马延和马延和马延和F-J·明特, J·博斯曼F-J·明特, J·博斯曼迈克尔·H·埃利, 迈克尔 H 埃利
专利相关信息
-
吕伟民D·索默, U·斯图茨李晓杰, 车景超李晓杰, 车景超古斯塔沃·帕拉西奥