一种硅砖用新型环保矿化剂的制备方法和使用方法[0002]硅砖所用的矿化剂在硅砖生产中的作用是加速石英在烧成时转化为低密度的变体(鳞石英和方石英),并且不降低其耐火度,并能防止砖坯烧成时因发生过度膨胀而产生疏松和开裂。[0003]目前国内硅砖生产使用的矿化剂大多为氧化钙、氧化亚铁系列,其中铁鳞的制备通常需要干燥、细磨、筛分等生产工艺;石灰乳的制备需要消化、湿磨、调配、陈腐等生产工艺,然后,石灰与铁鳞共磨后以石灰乳的形式加入坯料中,并要求铁鳞中含Fe203+Fe0>90 %。铁鳞是在钢材加热和轧制过程中,由于表面受到氧化而形成氧化铁层,氧化铁层剥落下来形成的鱼鳞状物。铁鳞的主要组成是Fe2O3和FeO,而在硅砖生产过程中起主要矿化作用的是Fe0( 二价铁),FeO和SiO2在约1178°C即达到最低共熔点产生液相,促进烧成中形成的亚稳方石英通过溶析作用向鳞石英转变。因此要求铁鳞中FeO的含量大于80%。但由于铁鳞的产生过程可知,如果钢材加热和轧制在温度、环境等方面的要求不同,则产生的铁鳞成分也会有很大的区别,这是一个完全不受控的过程。当铁鳞供不应求的时候,则大量不合格的铁鱗鱼目混珠,造成娃砖广品合格率的大幅度下降;并且,如果铁鱗中Fe2O3量过多,Fe2O3会促进2C0=C02+C反应,使碳素在硅砖的气孔中沉积和石墨化,从而引起焦炉炉体的疏松,因此通常要加一部分MnO 来代替Fe2O3,同时MnO的加入对于提高焦炉硅砖的导热率也有极大的帮助。[0004]综上所述,矿化剂具有稳定的氧化亚铁含量对砖砖质量至关重要。随着焦炉大型化的进程,对焦炉用硅砖的要求也越来越高,高导热率、鳞石英转化率的提高,真比重的提高等,这样就对大型焦炉用生产所需各个环节,尤其是保证硅砖矿物相转化的矿化剂的要求也提出了更高的要求。
[0005]本发明的目的是为了解决上述技术问题存在的不足,提供一种成本低、工艺简单、FeO含量大于80%,化学成分稳定、且利于娃砖生产过程中亚稳方石英向鳞石英转变的矿化剂以及它的制备方法和使用方法。[0006]本发明所采用的技术方案是:以锰矿选矿剩余的尾矿材料为初始料,进行二次加工,通过颗粒整形,磨细加工,再加入一定数量铁质物质,烘干处理制备而得。[0007]我国的锰矿绝大多数属于贫矿,必须进行选矿处理。但由于多数锰矿石属细粒或微细粒嵌布,并有相当数量的高铁矿和共(伴)生有益金属,锰矿选矿方法为机械选(包括洗矿、筛分、强磁选和浮选),以及火法富集、化学选矿法等,因此无论是那种选矿方法,选矿后的尾矿则具有大量的铁质物质和含CaO和MnO物质。[0008]原锰矿尾矿的主要原始指标:Fe0+Fe203的重量占尾矿总重量的40_50%,FeO占FeCHFe2O3总重量的60-65% ;CaO的含量占尾矿总重量的8-10%。
[0009]步骤一、原锰矿尾矿粗选,利用重选、浮选选出Al2O3等其它杂质,浮选时加入的NaOH溶液量是尾矿量的I一2倍;
[0010]步骤二、把粗选后的尾矿料,经过150-200°c下烘干;
[0011]步骤三、把干燥后的尾矿料,在粉碎设备中进行细粉碎,其粒度分布在3 — 1mm、l-0mm、0-0.088mm、lum_5 μ m 的粒度区间;
[0012]步骤四、把粉碎后的尾矿料,用造粒机造粒风选,风选造粒后的形状为直径为
0.088-0.099mm球型,从而得到这种球型尾矿产品;
[0013]步骤五、把球型尾矿98-99份和含有亚铁的铁鳞1-2份进行搅拌混合均匀得到这种矿化剂。
[0014]在步骤一中,重选的过程 利用不同比重的物质矿粒在运动的介质中由于其运动状态-运动速度、方向、途径的不同而得到分选;同时为了进一步除去尾矿中的Al2O3要加入过量的NaOH溶液,因为氧化铝是两性氧化物,它和碱反应,而氧化铁不和碱反应,待充分反应后将氧化铁过滤出来即可。因为,在硅砖生产中,Al2O3的存在不仅会增加在高温下硅石中液体形成的趋势,而且会延缓硅石的分解,当它与普通催化剂混合时,还会降低其活性。
[0015]因此,步骤一是为了去除杂质,提高FeO的含量。
[0016]其中步骤三中尾矿料的粒度3-lmm占1_2%,lum_5 μ m占3-5% ;采用这种超微粉结合以及最佳的颗粒配比,使矿化剂在硅砖配料混合中均匀分布,反应更充分,加速了硅砖制品中α-石英一亚稳方石英一鳞石英的转变,从而抑制了残余石英的产生的量;另外,颗粒间的空隙,几乎被超微粉全部填充,从而减少硅砖制品的裂纹,从而提高了硅砖制品的致密度,
[0017]其中步骤四中尾矿产品造粒成球形,是为了加大矿化剂微粒的比表面积使反应更充分,加快硅砖中的亚稳方石英向鳞石英转变。
[0018]经过步骤一到四(粗选、整形、磨细)后生产成球型尾矿的指标为=FeCHFe2O3的重量占尾矿总重量的58-65%,FeO占FeCHFe2O3总重量的80-85%,CaO的含量占尾矿总重量的10-15%,MnO的含量占尾矿总重量的2-3%,余量为杂质。
[0019]余量的杂质有ZnO、CuO和PbO等,这些并不影响矿化剂的使用性能。
[0020]本发明的使用方法:把这种矿化剂与水进行混合充分搅拌,形成浆体混合物,把浆体混合物加入到硅砖初始料中即可,浆体混合物加入量为硅砖初始料总重量的0.8-1.2%,最佳加入量为1.1%。
[0021]在这一步骤中矿化剂与水进行混合充分搅拌,矿化剂中的CaO与水反应生成Ca (OH) 2,形成石灰乳。
[0022]另外,加入矿化剂量的多少是非常重要的,加入矿化剂量太多,使晶相转变太快,烧成控制难于控制,易产生裂纹,废品率加大;加入矿化剂量太少,使晶相转变太慢,会使产品中的残留石英过多,造成二次体积膨胀过大。当矿化剂浆体混合物加入量为硅砖初始料总重量的0.8-1.1 %之间时,硅砖中的鳞石英的转变率逐渐提高,当加入量为1.1%时,鳞石英的转变率达到最高,当加入量为1.1-1.2%之间时,硅砖中的鳞石英的转变率逐渐降低。[0023]本发明的有益效果在于:
[0024]我国是有色金属生产大国,而有色金属矿山的尾矿量达70%~95%,既造成了大量资源损失于尾矿中,尾矿对环境等也产生了很大的危害。因此,有色金属尾矿的治理及综合开发利用是当前迫在眉睫问题。
[0025]本发明利用非常廉价的锰矿尾矿制备硅砖制品的矿化剂,不需再另外加入石灰和MnO,因此本发明不仅把生产成本降到最低,而且工艺简单,缩短了整个的工艺流程;同时本发明还加速了硅砖制品中α -石英一亚稳方石英一鳞石英的转变,抑制了残余石英的产生的量,所形成的液相缓冲了由于转化过程体积膨胀所产生的应力,提高了砖坯的热震稳定性和强度等指标,同时防止了焙烧过程中制品的疏松和开裂现象。由于MnO存在,也在一定程度上提高了硅砖的导热性能。
[0026]利用本发明生产硅砖的性能指标为:真密度为2.326—2.330g / cm3,重烧线变化为0.06-0.08%,荷重软化温度为1680-1690°C,导热率(平板法)1.9_2.0W / m.K。
[0027]以下结合实施例进一步说明本发明。
[0028]实施例1
[0029]步骤一、原锰矿尾矿粗选,利用重选、浮选选出Al2O3等其它杂质,其中加入的NaOH溶液量是尾矿量的I倍;
[0030]步骤二、把粗选后的尾矿料,经过150°C下烘干;
[0031]步骤三、把干燥后的尾矿料,在粉碎设备中进行细粉碎,其粒度分布在3-lmm、l_0mm、0—0.088mm、lum-5 μ m 的粒度区间;3_lmm 占 I %, lum-5 μ m 占 3% ;
[0032]步骤四、把粉碎后的尾矿料,用造粒机造粒,造粒后的形状为直径为0.088mm球型,从而得到这种球型尾矿产品;
[0033]步骤五、把球型尾矿98份和含有亚铁的铁鳞2份进行搅拌混合均匀得到这种矿化剂。
[0034]本发明的使用方法:把这种矿化剂与水进行混合充分搅拌,形成浆体混合物,把浆体混合物加入到娃砖初始料中即可,衆体混合物加入量为娃砖初始料总重量的0.8 %。
[0035]实施例2
[0036]步骤一、原锰矿尾矿粗选,利用重选、浮选选出Al2O3等其它杂质,其中加入的NaOH溶液量是尾矿量的1.5倍;
[0037]步骤二、把粗选后的尾矿料,经过190°C下烘干;
[0038]步骤三、把干燥后的尾矿料,在粉碎设备中进行细粉碎,其粒度分布在3-lmm、l-0mm、0-0.088mm、lum-5 μ m 的粒度区间;3_lmm 占 1.5%, lum-5 μ m 占 3.8%:
[0039]步骤四、把粉碎后的尾矿料,用造粒机造粒,造粒后的形状为直径为0.090mm球型,从而得到这种球型尾矿产品;
[0040]步骤五、把球型尾矿98.5份和含有亚铁的铁鳞1.5份进行搅拌混合均匀得到这种矿化剂。
[0041]本发明的使用方法:把这种矿化剂与水进行混合充分搅拌,形成浆体混合物,把浆体混合物加入到娃砖初始料中即可,衆体混合物加入量为娃砖初始料总重量的1.1%。[0042]实施例3
[0043]步骤一、原锰矿尾矿粗选,利用重选、浮选选出Al2O3等其它杂质,其中加入的NaOH溶液量是尾矿量的2倍;
[0044]步骤二、把粗选后的尾矿料,经过200°C下烘干;
[0045]步骤三、把干燥后的尾矿料,在粉碎设备中进行细粉碎,其粒度分布在3-lmm、l_0mm、0—0.088mm、lum-5 μ m 的粒度区间;3_lmm 占 2%, lum-5 μ m 占 5% ;
[0046]步骤四、把粉碎后的尾矿料,用造粒机造粒,造粒后的形状为直径为0.099mm球型,从而得到这种球型尾矿产品;
[0047]步骤五、把球型尾矿99份和含有亚铁的铁鳞1份进行搅拌混合均匀得到这种矿化剂。
[0048]本发明 的使用方法:把这种矿化剂与水进行混合充分搅拌,形成浆体混合物,把浆体混合物加入到娃砖初始料中即可,衆体混合物加入量为娃砖初始料总重量的1.2%。
一种硅砖用新型环保矿化剂的制备方法和使用方法
- 专利详情
- 全文pdf
- 权力要求
- 说明书
- 法律状态
查看更多专利详情
下载专利文献
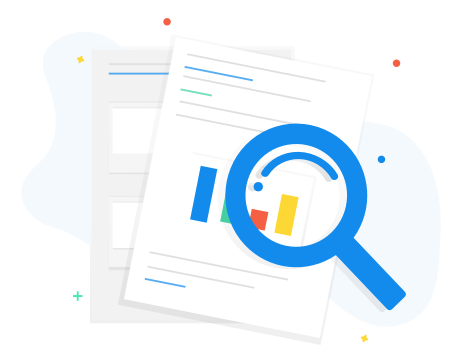
下载专利
同类推荐
-
王黎
您可能感兴趣的专利
-
孙妙囡张乐陵张乐陵陈凯, 陈树德
专利相关信息
-
吴珂李明照埃胡德·马罗姆, 迈克尔·米治里特斯基I·基拉伊