一种氯化氢合成炉石墨燃烧室耐高温浸渍处理方法[0002]氯化氢合成炉石墨燃烧室是氯化氢合成炉的关键部件。目前国内外采用石墨-钢-石墨结构的副产蒸汽氯化氢合成炉,其合成炉下段的石墨燃烧室制品多数采用酚醛树脂进行浸溃处理,但耐高温效果不理想,在使用过程中容易造成石墨爆裂的问题。最近有采用聚四氟乙烯对石墨制品进行耐高温抗氧化性浸溃处理的研究报导,但由于聚四氟乙烯与石墨本体没有较好的粘合性,浸溃物易析出,实际使用效果不理想。因此,氯化氢合成炉石墨燃烧室的耐高温抗氧化性能,使氯化氢合成生产的连续运行和安全性、实用性都受到一定的限制。
[0004]本发明专利的技术解决方案是:[0005]针对氯化氢合成炉石墨燃烧室耐高温浸溃处理在生产实践中存在的问题,本发明专利所述氯化氢合成炉石墨燃烧室采用聚硅氧烷有机硅水溶性分散液进行耐高温浸溃处理,氯化氢合成炉石墨燃烧室制品经分步浸溃、固化和热干燥处理等工序过程,在石墨制品的表面和孔隙中广生稳定的抗氧化相,提闻石墨制品的抗氧化效果,解决石墨材料处理中浸溃物附着量少且深度不均匀的难题,提高氯化氢合成炉石墨燃烧室制品在高温状态下的抗氧化性能,增强石墨燃烧室制品的机械强度和耐腐蚀稳定性,延长氯化氢合成炉石墨燃烧室的使用寿命。[0006]本发明所述的一种氯化氢合成炉石墨燃烧室耐高温浸溃处理方法,是米用聚娃氧烷有机硅对氯化氢合成炉石墨燃烧室制品进行耐高温浸溃处理,其工艺方案是:先配制36-42%质量百分比的六甲基二硅氧烷和0.06-8%质量百分比的聚二甲基硅氧烷水溶性分散液为浸溃液,将浸溃液加入到浸溃罐中加温到50-85°C,将石墨燃烧室制品置于浸溃罐中,抽真空到460-580mmHg,保持浸溃1.6-2.4小时,再加压至0.6-0.9Mpa,保持浸溃4_6小时,如此反复2-3次后,将石墨燃烧室制品从浸溃罐中的浸溃液里取出,以5-15°C/h的升温速度,经28-42小时由室温逐渐升温到320°C进行固化和干燥处理,使浸溃的石墨燃烧室制品充分固化和干燥,即完成氯化氢合成炉石墨燃烧室制品的浸溃处理工艺,得到具有较好耐高温性能的氯化氢合成炉石墨燃烧室制品。[0007]所述采用聚硅氧烷有机硅对氯化氢合成炉石墨燃烧室制品进行耐高温浸溃处理方法,还包括采用38-42%环甲基硅氧烷和0.08-8%聚二甲基硅氧烷水溶性分散液为浸溃液,将浸溃液加入到浸溃罐中加温到50-85°C,将石墨燃烧室制品置于浸溃罐中,抽真空到460-580mmHg,保持浸溃1.6-2.4小时,再加压至0.6-0.9Mpa,保持浸溃4_6小时,如此反复2-3次后,将石墨燃烧室制品从浸溃罐中的浸溃液里取出,以5-15°C /h的升温速度,经28-42小时由室温逐渐升温到320°C进行固化和干燥处理,使浸溃的石墨燃烧室制品充分固化和干燥,即完成氯化氢合成炉石墨燃烧室制品的浸溃处理工艺,得到具有较好耐高温性能的氯化氢合成炉石墨燃烧室制品。[0008]所述的一种氯化氢合成炉石墨燃烧室耐高温浸溃处理方法的工艺方案,是采用38%六甲基二硅氧烷和0.08%聚二甲基硅氧烷水溶性分散液为浸溃液,将浸溃液加入到浸溃罐中加温到65°C,将石墨燃烧室制品置于浸溃罐中,抽真空到480mmHg,保持浸溃2小时,再加压至0.7Mpa,保持浸溃6小时,如此反复3次后,将石墨燃烧室制品从浸溃罐中的浸溃液里取出,先在室温下干燥3小时,然后以9°C /h的升温速度在80-160°C温度区间干燥9小时,再以6°C /h的升温速度在170-280°C温度区间干燥18小时,以5°C /h的升温速度在290-320°C温度区间干燥6小时,使浸溃的石墨燃烧室制品充分固化和干燥,即完成氯化氢合成炉石墨燃烧室制品的浸溃处理工艺,得到具有较好耐高温性能的氯化氢合成炉石墨燃烧室制品。
[0009]所述的一种氯化氢合成炉石墨燃烧室耐高温浸溃处理方法的工艺方案,还包括采用40%环甲基硅氧烷和0.08%聚二甲基硅氧烷水溶性分散液为浸溃液,将浸溃液加入到浸溃罐中加温到70°C,然后将石墨制品置于浸溃罐中,抽真空到460mmHg,保持浸溃2小时,再加压至0.7Mpa,保持浸溃6小时,如此反复2次后,将石墨燃烧室制品从浸溃罐中的浸溃液里取出,先在室温下干燥3小时,然后以8°C /h的升温速度在80-160°C温度区间干燥10小时,再以5.50C /h的升温速度170-280°C温度区间干燥20小时,以5°C /h的升温速度在290-320°C温度区间干燥6小时,使浸溃的石墨燃烧室制品充分固化和干燥,即完成氯化氢合成炉石墨制品的浸溃处理工艺,得到具有较好耐高温性能的氯化氢合成炉石墨燃烧室制品O
[0010] 实施例一:一种氯化氢合成炉石墨燃烧室耐高温浸溃处理方法的工艺方案,是选取显气孔率为14%、体积密度为1700kg/cm3的石墨材料制成氯化氢合成炉石墨燃烧室制品,采用38%六甲基二硅氧烷和0.08%聚二甲基硅氧烷水溶性分散液为浸溃液,将浸溃液加入到浸溃罐中加温到65°C,将石墨燃烧室制品置于浸溃罐中,抽真空到480mmHg,保持浸溃2小时,再加压至0.7Mpa,保持浸溃6小时,如此反复3次后,将石墨燃烧室制品从浸溃罐中的浸溃液里取出,先在室温下干燥3小时,然后以9°C /h的升温速度在80-160°C温度区间干燥9小时,再以6°C /h的升温速度在170-280°C温度区间干燥18小时,以5°C /h的升温速度在290-320°C温度区间干燥6小时,使浸溃的石墨燃烧室制品充分固化和干燥,即完成氯化氢合成炉石墨制品的浸溃处理工艺,得到具有较好耐高温性能的氯化氢合成炉石墨燃烧室制品。
[0011]实施例二:一种氯化氢合成炉石墨燃烧室耐高温浸溃处理方法的工艺方案,是选取显气孔率为15%、体积密度为1800kg/cm3的石墨材料制成氯化氢合成炉石墨燃烧室制品,采用40%环甲基硅氧烷和0.08%聚二甲基硅氧烷水溶性分散液为浸溃液,将浸溃液加入到浸溃罐中加温到70°C,然后将石墨制品置于浸溃罐中,抽真空到460mmHg,保持浸溃2小时,再加压至0.7Mpa,保持浸溃6小时,如此反复2次后,将石墨燃烧室制品从浸溃罐中的浸溃液里取出,先在室温下干燥3小时,然后以8°C /h的升温速度在80-160°C温度区间干燥10小时,再以5.50C /h的升温速度170-280°C温度区间干燥20小时,以5°C /h的升温速度在290-320°C温度区间干燥6小时,使浸溃的石墨燃烧室制品充分固化和干燥,即完成氯化氢合成炉石墨制品的浸溃处理工艺,得到具有较好耐高温性能的氯化氢合成炉石墨燃烧室制 品。
一种氯化氢合成炉石墨燃烧室耐高温浸渍处理方法
- 专利详情
- 全文pdf
- 权力要求
- 说明书
- 法律状态
查看更多专利详情
下载专利文献
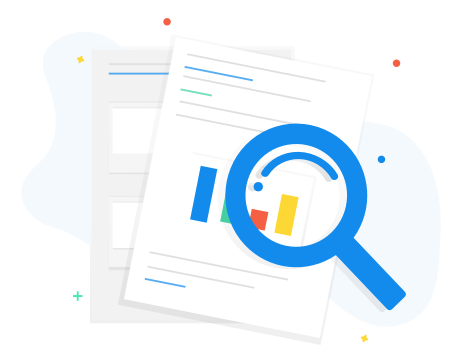
下载专利
同类推荐
-
范颖芳, 张世义范颖芳, 张世义盛蕾, 盛志义盛蕾, 盛志义
您可能感兴趣的专利
-
盛蕾, 盛志义克里斯托弗·罗斯田维熙
专利相关信息
-
吴建峰朱安会, 马洪章伍增平, 许又高伍增平, 许又高李进, 邹祥李进, 邹祥