一种钢管柱混凝土的侧浇方法及所用的钢管柱结构的制作方法 【技术领域】。 [0002]现有建筑工程中,由于钢管柱承重性能良好,在受力较大部位能有效减小混凝土柱体积,目前越来越普遍的应用于工程结构的竖向支撑。有些钢管柱高度较高,通常由多根钢管焊接而成。钢管柱内浇筑有混凝土。 [0003]现有技术浇筑有混凝土的方法是通过布料管从钢管顶部完成混凝土的浇筑。存在以下不足:1、在钢结构施工中,一般是先安装柱和梁后再安装压型钢板;故在浇筑下节钢管内的混凝土时,外框水平梁板还未施工完毕,没有施工平台进行施工。所以只能搭设临时施工平台进行浇筑施工,临时施工平台通常离地面较高,还需要设置爬梯,人员只能站在空间窄小的临时施工平台上进行操作,有较大安全风险。 [0004]2、在进行浇筑时,无法进行上部钢管柱、钢梁、压型钢板的安装,只能等下节钢管浇筑完成后才能进行后续工作,影响施工效率,延误工期。
[0005]3、由于浇筑时,外框压型钢板还未铺设,布料管只固定在钢梁上,周转效率低,花费时间过长。
[0006]本发明的目的在于,提供一种钢管柱混凝土的侧浇方法及所用的钢管柱结构,以在进行下节钢管的浇筑时,可以同时进行上部钢管柱、钢梁、压型钢板的安装,从而提高施工效率,缩短工期,及克服现有技术的不足。
[0007]本发明的技术方案是这样实现的:
本发明的一种钢管柱混凝土的侧浇方法为,所述钢管柱是由多节钢管焊接而成;该方法是先在上节钢管的侧壁开浇筑孔之后,然后再将上节钢管与下节钢管焊接;在浇筑下节钢管内的混凝土时,将混凝土泵送管从侧面插入上节钢管的浇筑孔内完成对下节钢管内混凝土的烧筑。
[0008]前述方法中,在用混凝土泵送管从侧面完成下节钢管内混凝土的浇筑时,应控制好泵车的泵送力度,使混凝土沿钢管内的空腔垂直下落,利用混凝土下落产生的动能来达到混凝土的自密实。
[0009]前述方法中,混凝土浇筑过程采用分层浇筑,层高不大于I米;在对每层进行浇筑时,应用振捣棒采用快插慢拔方式对混凝土逐点振捣,每点振捣时间不少于20s振捣时应顺序移动不得漏振;同时管外配合人工木槌敲击;每层振捣至混凝土表面平齐,不再明显下降,不再出现气泡,表面泛出灰浆时,再进行上一层浇筑。
[0010]前述方法中,混凝土的浇筑高度应使下节钢管内混凝土成型面距浇筑孔孔底距离不小于500mmo
[0011]前述方法中,所述浇筑孔在专业工厂采用划孔方式加工而成;划孔方式是通过划刀的旋转在钢管侧壁划出浇筑孔,划下来的圆片作为堵片备用,待浇筑完成后,再通过堵片将浇筑孔封闭焊接。
[0012]前述方法中,所述混凝土的浇筑是在完成钢管柱外框水平结构后进行,钢管柱外框水平结构上设有混凝土泵送管支撑。
[0013]用于上述方法的本发明的一种钢管柱结构为,该钢管柱结构包括上节钢管和下节钢管,上节钢管与下节钢管焊接,上节钢管的侧壁上设有浇筑孔,浇筑孔内侧设有加强环。
[0014]前述钢管柱结构中,所述浇筑孔的孔径为200mm,浇筑孔的中心距离上节钢管与下节钢管的焊缝距离为300mm。
[0015]前述钢管柱结构中,所述浇筑孔内壁接有加强环,加强环的内孔与浇筑孔孔径相同;加强环的宽度为50mm,加强环厚度与上节钢管的壁厚相同;加强环与上节钢管内壁的贴合面为弧面,弧度与上节钢管内壁弧度相同。
[0016]由于采用了上述技术方案,本发明与现有技术相比,本发明的方法是采用侧向浇筑下节钢管的混凝土,所以在浇筑过程中,不影响上层钢管柱、钢梁、桁架模板的施工,可以同步施工,工作面不相互影响,提高了钢结构安装效率,缩短工期。由于本发明的方法是在外框水平梁板结构施工完毕后再进行下节钢管的浇筑,所以人员可以站在外框水平梁板结构进行浇筑施工,大大降低了安全风险。浇筑简便,无需使用布料机即可浇筑,节省布料机转运时间,钢管柱混凝土浇筑时间大大缩短。缩短施工工期,减少人工费用的支出。
[0017]图1是本发明的施工方法示意图;
图2是现有技术的施工方法示意图;
图3是本发明施工方法所用的钢管柱结构;
图4是图3的三维视图;
图5是采用划孔方式划下的堵片。
[0018]图中的标记为:1-上节钢管,2-下节钢管,3-浇筑孔,4-加强环,5-混凝土,6_焊缝,7-堵片,8-混凝土泵送管,9-钢管柱外框水平结构,10-混凝土泵送管支撑,11-施工平台,12-爬梯,13-布料管。
[0019]下面结合附图和实施例对本发明作进一步的详细说明,但不作为对本发明的任何限制。
[0020]本发明的一种钢管柱混凝土的侧浇方法,如图2所示,所述钢管柱是由多节钢管焊接而成;该方法是先在上节钢管I的侧壁开浇筑孔3之后,然后再将上节钢管与下节钢管2焊接;在浇筑下节钢管内的混凝土 5时,将混凝土泵送管8从侧面插入上节钢管的浇筑孔内完成对下节钢管内混凝土的浇筑。在用混凝土泵送管8从侧面完成下节钢管2内混凝土5的浇筑时,应控制好泵车的泵送力度,使混凝土沿钢管内的空腔垂直下落,利用混凝土下落产生的动能来达到混凝土的自密实。混凝土浇筑过程采用分层浇筑,层高不大于I米;在对每层进行浇筑时,应用振捣棒采用快插慢拔方式对混凝土逐点振捣,每点振捣时间不少于20s振捣时应顺序移动不得漏振;同时管外配合人工木槌敲击,根据声音判断混凝土是否密实;每层振捣至混凝土表面平齐,不再明显下降,不再出现气泡,表面泛出灰浆时,再进行上一层浇筑。混凝土的浇筑高度应使下节钢管2内混凝土成型面距浇筑孔3孔底距离不小于500mm。所述浇筑孔3在专业工厂采用划孔方式加工而成;划孔方式是通过划刀的旋转在钢管侧壁划出浇筑孔,划下来的圆片作为堵片7备用,待浇筑完成后,再通过堵片将浇筑孔封闭焊接。混凝土的浇筑是在完成钢管柱外框水平结构9后进行,钢管柱外框水平结构上设有混凝土泵送管支撑10。
[0021]用于上述方法的本发明的一种钢管柱结构的结构示意图如图3和图4所示,该钢管柱结构包括上节钢管I和下节钢管2,上节钢管I与下节钢管2焊接,上节钢管I的侧壁上设有浇筑孔3,浇筑孔3内侧设有加强环4。浇筑孔3的孔径为200mm,浇筑孔3的中心距离上节钢管I与下节钢管2的焊缝6距离为300mm。浇筑孔3内壁接有加强环4,加强环4的内孔与浇筑孔3孔径相同;加强环的宽度为50mm,加强环厚度与上节钢管I的壁厚相同;加强环4与上节钢管I内壁的贴合面为弧面,弧度与上节钢管I内壁弧度相同。
实施例
[0022]本例以位于广州市珠江新城核心商务区的富力盈凯广场项目为例,该项目地下5层,地上65层,为高层建筑,结构形式为框架-核心筒结构,核心筒为钢筋混凝土剪力墙结构,外筒结构由地下16根、地上为20根钢管混凝土柱组成侧端支撑体系,外筒与内筒设窄翼热轧H型钢件为楼盖梁、梁上铺压型钢板,上浇IlOmm厚混凝土板。
[0023]在该项目中,钢管柱支撑结构使用较多,钢管柱高度高,工程量大。为了满足工期要求,在该项目中,对传统钢管柱混凝土的浇筑技术(见图1)进行了创新,采用侧向浇筑(见图2)技术。该技术是在每根钢管一端的侧壁上加工一个浇筑孔3,浇筑孔的孔径与混凝土泵送管配套,孔径为200mm,浇筑孔的中心位于两节圆钢管焊缝上方300mm处(见图3)。为了不影响钢管的整体性能,对浇筑孔进行了加固处理,在浇筑孔内壁焊接一个加强环4,加强环4的内孔与浇筑孔3孔径相同;加强环的宽度为50mm,加强环厚度与上节钢管I的壁厚相同;加强环4与上节钢管I内壁的贴合面为弧面,弧度与上节钢管I内壁弧度相同。浇筑时,将混凝土泵送管8直接伸入浇筑孔进行下节钢管2的砼浇筑,并控制好泵车的泵送力度,令混凝土在空腔内垂直下落,利用混凝土下落产生的动能来达到混凝土的自密实。浇筑过程中,必须由专人对混凝土的质量进行监控,及时作好塌落度检测,对有和易性、塌落度不达标等现象的混凝土坚决不准使用。为了确保钢管柱混凝土浇筑的密实度及振捣效果,采用分层振捣,分层高度不大于I米。振捣棒插入混凝土内,要快插慢拔,振捣时应逐点移动,按顺序进行,不得漏振,每点振捣时间不少于20s。同时管外配合人工木槌敲击,根据声音判断混凝土是否密实,每层振捣至混凝土表面平齐不再明显下降,不再出现气泡,表面泛出灰浆为止。可用手电筒照射入钢管柱内进行检查。施工过程中需确保施工现场机械、水、电、照明等正常运行,让浇筑工作连续不中断地进行。浇筑完成后将浇筑孔用堵片7封闭焊接。堵片7是在划浇筑孔时,从钢管上划下来的圆片,其尺寸刚好与浇筑孔配套。为了防止焊接时高温对下节钢管柱混凝土造成不良影响,因此在浇筑时,混凝土成型面距离浇筑孔孔底的距离不能小于500mm。
[0024]由于本发明是在钢管柱外框水平结构上进行浇筑施工,因此故无需搭设狭小的施工平台,人员转移方便,对施工人员的安全起到了重大作用。但由于钢管柱处楼层临边,在施工过程中,仍需做好安全措施,施工前,应逐级进行安全技术教育及交底,落实所有安全技术措施和人身防护用品,未经落实时不得进行施工。
[0025]本例的施工方法,在浇筑钢管柱混凝土时,上部钢管柱、钢梁等均可以照常施工,工作面错开可同步施工,可缩短钢结构安装工期。由于浇筑方便,节省了浇筑时间。同时,由于不需使用布料机,则无需塔吊配合进行转运,塔吊可进行材料的吊运,不影响其它施工工序的正常施工,大大缩短了工期。
[0026]本例在施工中,还应注意以下问题:
1、浇筑孔3的位置要严格按设计钻孔,位置过高或过低,均会对钢管柱结构造成影响,且会对烧筑施工造成不便。
[0027]2、浇筑孔3加固需严格按设计进行,假如不按设计加固,会对整体钢结构的性能造成影响。
[0028]3、浇筑混凝土时,加以振动棒振捣,保证混凝土成型质量。控制混凝土成型面离圆洞底部距离不小于500mm,保证混凝土不因焊接而受损。
[0029]4、封闭焊接浇筑孔3处的堵片7时,应严格控制焊接质量,不允许出现渗漏。
[0030]5、施工过程中做好临边防护,不要将混凝土溅射至建筑外。造成安全事故。
[0031]本发明作为一项新技术,在本工程钢结构施工中具有不可替代的作用,得到了成功的应用。有效解决了钢结构体系中钢管柱混凝土浇筑困难、上下工作面无法同时施工、安全风险大等问题。本发明可以为以后的钢结构体系施工提供一个借鉴。
一种钢管柱混凝土的侧浇方法及所用的钢管柱结构制作方法
- 专利详情
- 全文pdf
- 权力要求
- 说明书
- 法律状态
查看更多专利详情
下载专利文献
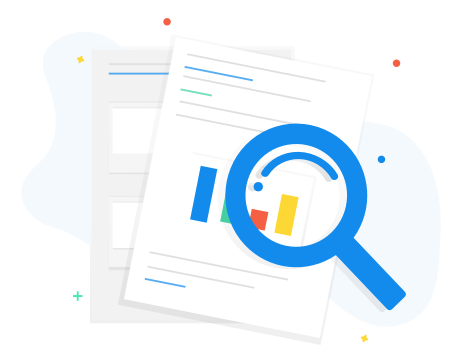
下载专利
同类推荐
-
于吉涛张鹏飞肖燎宋运来
您可能感兴趣的专利
-
鱼智浩黄晓东, 张韬黄晓东, 张韬黄晓东, 张韬黄晓东, 张韬
专利相关信息
-
许金锔, 吴清瑶杨鼎宜, 李 浩杨鼎宜, 李 浩