利用尾矿资源制造的釉料及其上釉工艺的制作方法[0002]随着经济社会的高速发展,人们的生活质量日益提高,且消费观念也不断转变,要求陶瓷制品既要有实用性,又要有艺术性和观赏性。现有釉色按烧成温度可分成高温釉和低温釉;按外表特征可分透明釉、乳浊釉、颜色釉、有光釉、无光釉、裂纹釉(开片)、结晶釉坐寸ο[0003]根据陶瓷生产的K2O-AL2O3-S12三元系统相图及铁氧化物在不同条件下的显色原理:釉料中的铁含理及分散度越高,其着色力越强,颜色越深。还原烧成时,Fe203+C0 — 2Fe0+C02,温度越高,越有利于氧化铁的还原,颜色越深。在烧成过程中,随着烧成气氛,铁含量不同,FeCVFe2O3比例发生变化,因此产生不同的色彩变化。在高温下釉层熔体产生分相,分离为贫Fe2O3的连续基质与富的液滴,由于气氛及温度对液相粘度和表面张力的影响发生液滴的聚集,再次发生分相与析晶,在反应过程中有可能产生多次分相现象,随着釉层的流动,产品各部位的FeCVFe2O3比例发生变化,因而产生各式各样颜色不相同,色彩丰富的黑里红釉产品。 [0004]我国铁矿资源丰富,储藏量极大,开采提纯后其尾矿渣均没有被利用,全国每年产生的尾矿渣超过亿吨,仅德化阳山铁矿其选矿厂至今留下的尾矿就达400万吨之多,这些尾矿堆积如山,不仅严重污染了周围,同时也浪费了大量的资源。尾矿占用大量土地,造成水土流失及环境污染等问题,解决又是刻不容缓的,因此急需研制出一种实用的,可大批量利用尾矿进行再生产的技术,解决尾矿的综合利用。[0005]在目前的生产中,色釉陶瓷产品为了达到呈色稳定、无色差、减少釉面缺陷,一般均采用二次烧成工艺,这种生产方法的缺点在于:坯体先进行一次素烧,排除坯体中的结构水和有机物,使得碳酸盐分解排出气体避免釉层出现针孔;表面颜色和图案效果变化少,由于所有颜色均由坯土料调色获得,故色彩种类较少,加上生产时布料方法的限制,只能布出一些固定图案,图案变化单一。
[0006]为了解决上述问题,本发明的目的在于:提供一种将尾矿渣利用到工艺陶瓷及陶瓷釉料中,达到废物的综合利用,变废弃尾矿为再生资源,降低了工艺陶瓷、釉料的生产成本的陶瓷釉料。
[0007]为了达到上述目的,本发明的技术方案为:利用尾矿资源制造的釉料,由长石40~65%、石英10~25%,铁矿尾矿15~30%,石灰石0~10%,高岭土 0~10%及骨灰0~10%构成,其组分重量配比为:1~5份K 2 O、1~8份A L 2 O 3、55~70份S i O 2、I~5份P 2 O 5、1飞份N a20、l~8 份 F e203、5~15 份 C aO 及 I~8 份 MgO。[0008]其中,骨灰为动物骨头烧成的灰,成分以磷酸钙为主,经高温灼烧,生成P205。
[0009]本发明的有益效果在于:本发明将尾矿渣利用到陶瓷釉料中,达到废物的综合利用,变废弃尾矿为再生资源,提高资源综合利用率,减少环境污染,保持经济的可循环发展,同时降低了釉料的生产成本。
[0010]本发明的另一个目的在于:还提供了一种采用一次烧成工艺,使得产品质量达到二次烧成的效果,降低产品的能耗的陶瓷釉料的上釉工艺。
[0011]为了达到上述目的,本发明的技术方案为:一种以上所述利用尾矿资源制造的釉料的上釉工艺,步骤一,将上述物料,放进球磨机内球磨,加水,球磨时间为8~10小时,并经均匀混合搅拌和充分溶解后,制得釉浆,釉浆的细度控制在万孔筛筛余0.01%以下;
步骤二,将上述经球磨好的釉浆从球磨机放出,存入储浆池内搅拌;
步骤三,釉浆过200目筛,将充分悬浮的釉浆涂敷于坯体表面,浓度为38~46波美度,釉浆在坯体表面的厚度在0.2^1.2 mm;
步骤四,高温烧结:对坯体进行高温烧结,且高温烧结温度为1000°C~1300°C,高温烧结时间为15小时,高温烧结结束后随炉冷却至室温,便制得陶瓷制品。
[0012]作为本发明的进一步改进,步骤三对坯体进行擦水处理,并进行干燥,坯体水分控制在5%以下。
[0013]坯体的质量也会影响到烧后的制品的釉面效果。坯体质量主要控制坯体的擦洗及坯体水分,在坯体擦水过程中,要经常换水,保持所有水的干净,坯体上的灰尘及杂质要清除干净,否则产品会出现缩釉、掉釉或针孔等缺陷。坯体水分较多或不均匀时,在上釉时坯体各部位所吸收的釉量不均匀,造成釉层厚度不一,容易产生色差,坯体擦水后进行干燥,在上釉时坯体水分控制在5%以下。
[0014]作为本发明的进一步改进,步骤三中釉浆浓度为40-43波美度,釉浆在坯体表面的厚度在0.5~1.0 mm。
[0015]需对釉浆进行200目筛过滤,防止粉尘污染。釉浆在坯体表面的厚度厚,呈色深;釉浆在坯体表面的厚度浅,且容易导致釉面的光泽度差,色釉的厚度比透明釉要厚些,控制在0.5-1.0 mm,在上釉过程中要控制釉浆的浓度,每施若干件坯体后,用浓度计进行测量,保证釉浆的浓度保持在一定范围内。杯类陶瓷产品的内釉采用皮球或板车内胎压缩喷釉,内釉喷好后要让其余釉顺着杯口方向自然流掉或甩掉,不能流向杯底,否则会造成重釉,烧后产生深浅色,外表面因施内釉而造成污染的釉浆也要及时擦洗干净。在上釉过程中要经常对釉浆搅拌,防止浆沉淀、分层,导致产品烧后色彩不稳定。
[0016]作为本发明的进一步改进,步骤四中的高温烧结温度为1280° C。
[0017]作为本发明的进一步改进,步骤四中,陶瓷制品为相框工艺瓷时,高温烧结温度为1050°C。
[0018]本发明的有益效果在于:本发明通过严格控制生产工艺,充分使用铁矿尾矿,采用一次烧成工艺,使得产品质量达到二次烧成的效果,降低产品的能耗;将尾矿渣利用到工艺陶瓷及陶瓷釉料中,达到废物的综合利用,变废弃尾矿为再生资源,提高资源综合利用率,减少环境污染,保持经济的可循环发展,同时降低了工艺陶瓷、釉料的生产成本。
[0020]一种以上所述利用尾矿资源制造的釉料的上釉工艺,步骤一,将上述物料,放进球磨机内球磨,加水,球磨时间为8~10小时,并经均匀混合搅拌和充分溶解后,制得釉浆,釉浆的细度控制在万孔筛筛余0.01%以下;
步骤二,将上述经球磨好的釉浆从球磨机放出,存入储浆池内搅拌;
步骤三,釉浆过200目筛,将充分悬浮的釉浆涂敷于坯体表面,浓度为38~46波美度,釉浆在坯体表面的厚度在0.2^1.2 mm;
步骤四,高温烧结:对坯体进行高温烧结,且高温烧结温度为1000°C~1300°C,高温烧结时间为15小时,高温烧结结束后随炉冷却至室温,便制得陶瓷制品。
[0021]步骤三对坯体进行擦水处理,并进行干燥,坯体水分控制在5%以下。
[0022]坯体的质量也会影响到烧后的制品的釉面效果。坯体质量主要控制坯体的擦洗及坯体水分,在坯体擦水过程中,要经常换水,保持所有水的干净,坯体上的灰尘及杂质要清除干净,否则产品会出现缩釉、掉釉或针孔等缺陷。坯体水分较多或不均匀时,在上釉时坯体各部位所吸收的釉量不均匀,造成釉层厚度不一,容易产生色差,坯体擦水后进行干燥,在上釉时坯体水分控制在5%以下。
[0023]步骤三中釉浆浓度为40-43波美度,釉浆在坯体表面的厚度在0.5~1.0 mm。
[0024]需对釉浆进行200目筛过滤,防止粉尘污染。釉浆在坯体表面的厚度厚,呈色深;釉浆在坯体表面的厚度浅,且容易导致釉面的光泽度差,色釉的厚度比透明釉要厚些,控制在0.5-1.0 mm,在上釉过程中要控制釉浆的浓度,每施若干件坯体后,用浓度计进行测量,保证釉浆的浓度保持在一定范围内。杯类陶瓷产品的内釉采用皮球或板车内胎压缩喷釉,内釉喷好后要让其余釉顺着杯口方向自然流掉或甩掉,不能流向杯底,否则会造成重釉,烧后产生深浅色,外表面因施内釉而造成污染的釉浆也要及时擦洗干净。在上釉过程中要经常对釉浆搅拌,防止浆沉淀、分层,导致产品烧后色彩不稳定。
[0025]步骤四中的高温烧结温度为1280° C。
[0026]步骤四中,陶瓷制品为相框工艺瓷时,高温烧结温度为1050°C。
[0027]通过严格控制生产工艺,充分使用铁矿尾矿,采用一次烧成工艺,使得产品质量达到二次烧成的效果,降低产品的能耗;将尾矿渣利用到工艺陶瓷及陶瓷釉料中,达到废物的综合利用,变废弃尾矿为再生资源,提高资源综合利用率,减少环境污染,保持经济的可循环发展,同时降低了工艺陶瓷、釉料的生产成本。
[0028]实施例1
将长石52%、石英12%,铁矿尾矿21%,石灰石4%,高岭土 5%及骨灰6%,其组分重量配比为:2 份K 2 0、6 份A L 2 O 3、63 份 S i O 2、4份卩 2 O 5、4 份N a20、7 份F e203、10 份C aO及6份MgO的物料,放进球磨机内球磨,加水,球磨时间为8小时,并经均匀混合搅拌和充分溶解后,制得釉浆,釉浆的细度控制在万孔筛筛余0.01% ;将上述经球磨好的釉浆从球磨机放出,存入储浆池内搅拌;釉浆过200目筛,将充分悬浮的釉浆涂敷于坯体表面,浓度为40波美度,釉浆在坯体表面的厚度在0.7 mm ;在釉浆涂敷于坯体表面时,同时对坯体进行擦水处理,并进行干燥,坯体水分控制在3.8% ;高温烧结:对坯体进行高温烧结,且高温烧结温度为1280° C,高温烧结时间为15小时,高温烧结结束后随炉冷却至室温,便制得陶瓷制品O[0029]实施例2
将长石46%、石英22%,铁矿尾矿15%,石灰石5%,高岭土 3%及骨灰9%,其组分重量配比为:3 份K 2 0、7 份A L 2 O 3、58 份 S i O 2、5份卩 2 O 5、3 份N a20、4 份F e203、14 份C aO及4份MgO的物料,放进球磨机内球磨,加水,球磨时间为8.5小时,并经均匀混合搅拌和充分溶解后,制得釉浆,釉浆的细度控制在万孔筛筛余0.008% ;将上述经球磨好的釉浆从球磨机放出,存入储浆池内搅拌;釉浆过200目筛,将充分悬浮的釉浆涂敷于坯体表面,浓度为39波美度,釉浆在坯体表面的厚度在0.4 mm ;在釉浆涂敷于坯体表面时,同时对坯体进行擦水处理,并进行干燥,坯体水分控制在4.2% ;高温烧结:对坯体进行高温烧结,且高温烧结温度为1260° C,高温烧结时间为15小时,高温烧结结束后随炉冷却至室温,便制得陶瓷制品。
[0030]实施例3
将长石59%、石英17%,铁矿尾矿17%,石灰石2%,高岭土 2%及骨灰3%,其组分重量配比为:2 份K 2 0、6 份 A L 2 O 3、70 份 S i O 2、3 份 P 2 O 5、2 份N a20、5 份 F e203、6 份 C aO及6份MgO的物料,放进球磨机内球磨,加水,球磨时间为9小时,并经均匀混合搅拌和充分溶解后,制得釉浆,釉浆的细度控制在万孔筛筛余0.004% ;将上述经球磨好的釉浆从球磨机放出,存入储浆池内搅拌;釉浆过200目筛,将充分悬浮的釉浆涂敷于坯体表面,浓度为42波美度,釉浆在坯体表面的厚度在0.6 mm ;在釉浆涂敷于坯体表面时,同时对坯体进行擦水处理,并进行干燥,坯体水分控制在4.5% ;高温烧结:对坯体进行高温烧结,且高温烧结温度为1280° C,高温烧结时间为15小时,高温烧结结束后随炉冷却至室温,便制得陶瓷制品。
[0031]采用以上陶瓷釉料上釉工艺制作出的陶瓷釉料还具有以下性质:光泽度好;铅溶出量小于2mg/c ;镉溶出量小于0.2mg/L ;热稳定性为200°C_20°C热交换一次不裂;釉面具有较高的艺术性,窑变色彩丰富多样。
[0032]根据上述说明书的揭示和教导,本发明所属领域的技术人员还可以对上述实施方式进行适当的变更和修改。因此,本发明并不局限于上面揭示和描述的【具体实施方式】,对本发明的一些修改和变更也应当落入本发明的权利要求的保护范围内。此外,尽管本说明书中使用了一些特定的术语,但这些术语只是为了方便说明,并不对本发明构成任何限制。
利用尾矿资源制造的釉料及其上釉工艺制作方法
- 专利详情
- 全文pdf
- 权力要求
- 说明书
- 法律状态
查看更多专利详情
下载专利文献
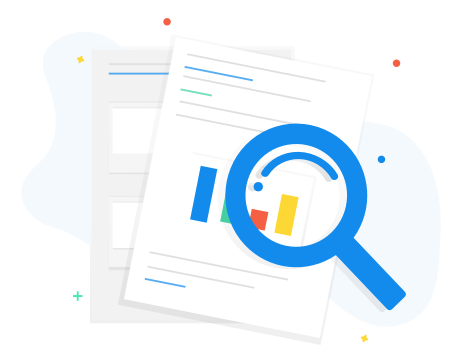
下载专利
同类推荐
-
吴克诚吴克诚李庆华
您可能感兴趣的专利
-
李庆华王新, 王桂英异范道, 金泰翰孙再冉樊传刚, 高元宝
专利相关信息
-
李章大, 周秋兰李章大, 周秋兰杨华明, 彭康J·H·阿伦斯J·H·阿伦斯J·H·阿伦斯