专利名称:陶瓷纳米复合纤维的静电纺丝制备方法陶瓷纤维种类繁多,性能优异,有着广泛的应用。纳米材料根据属性的不同,可以 分成金属纳米材料、半导体纳米材料、纳米陶瓷材料、有机纳米材料等,当上述纳米结构单 元与其他材料复合时则构成纳米复合材料。纳米复合材料由于其优良的综合性能,特别是 其性能的可设计性,被广泛应用于航空航天、国防、交通、体育等领域,纳米复合材料则是其 中最具吸引力的部分。纳米复合材料是指由两种或两种以上的不同材料组成,而三围尺度 中至少一维为纳米数量级的复合材料。纳米复合材料的应用主要有磁性材料、介电材料、静电屏蔽材料、光学材料和敏感 材料等。随着研究的层层深入,复合纳米材料在性能上的优越性尽显无疑,成为当今高分子 化学和物理、无机化学和材料化学等许多学科交叉的前沿领域。静电纺丝技术的产生发展, 也为复合纳米纤维材料提供了一个更加简单高效、易于实现的途径。目前,通过静电纺丝技术制备陶瓷纳米复合纤维的方法主要是将两种或两种以上 的陶瓷前驱体溶于溶剂,添加可纺高聚物,制备成纺丝液,经过静电纺丝制备和烧结两个步 骤后得到陶瓷纳米复合纤维。但是,此类方法存在着局限性首先,使用这种方法制备陶瓷 纳米复合纤维,两种或两种以上的陶瓷必须有前驱体并可以与高聚物匹配混合,再制得可 纺溶液,这就导致了该方法制备得到的陶瓷纳米复合纤维的种类较少;其次,纺丝液所选用 的可纺高聚物须同时满足多种陶瓷前驱体的电纺要求,这缩小了可纺高聚物的可选范围; 最后,所选溶剂必须可以同时溶解多种陶瓷前驱体,这又限制了溶剂的可选种类。由于以上 的限制条件,通过现有方法制备得到的陶瓷纳米复合纤维的种类少,不能满足日益增长的 科研及生产多样性的需求。
本发明的目的是提供一种陶瓷纳米复合纤维的静电纺丝制备方法,解决了现有技 术中存在的原料选择条件限制多,可选组分范围小,制备得到的陶瓷纳米复合纤维种类少, 不能满足科研及生产多样性的问题。本发明所采用的技术方案是,一种陶瓷纳米复合纤维的静电纺丝制备方法,该方 法按以下步骤具体实施步骤1 按体积百分比,称取粒径为10nm-300nm的陶瓷纳米颗粒3% -10%,陶瓷 前驱体3% -20%,可纺高聚物5% -30%,溶剂40% -89%,总体积为100% ;步骤2 将步骤1中称取的可纺高聚物加入到溶剂中,在水浴中加热并磁力搅拌, 制得粘度均勻的可纺高聚物溶液;步骤3 将步骤1中称取的陶瓷前驱体加入到步骤2中得到的可纺高聚物溶液中,在水浴中加热并磁力搅拌,陈化2_12h,得到成分均勻的陶瓷前驱体可纺溶液;步骤4 将步骤1中称取的陶瓷纳米颗粒加入到步骤3中得到的陶瓷前驱体可纺 溶液中,在水浴中保持恒温,对溶液进行分散,持续搅拌l_2h,然后对混合溶液进行超声波 分散0. 5-lh和恒温溶胀0. 5-lh,形成成分均勻的陶瓷纳米颗粒/陶瓷前驱体/可纺高聚物 纺丝液;步骤5 将步骤4中得到的纺丝液倒入注射器,采用削平的注射针头作为喷射细 流的毛细管,静电纺丝过程中电压为10-40kV,收集距离为10-30cm,纺丝液推进速度为 0. 5-2. 5mL/h,环境温度为10_50°C,环境湿度为50% -75%,按照静电纺丝技术制备成陶瓷 纳米颗粒/陶瓷前驱体/可纺高聚物的复合纳米纤维;步骤6 将步骤5中得到的复合纳米纤维经过650°C -1200°C烧结,得到陶瓷纳米复合纤维。本发明的有益效果是,对于原料选择条件宽,可选范围大,制备得到的纳米复合陶 瓷纤维种类显著增多,可以满足科研及生产多样性的要求,为陶瓷纳米复合纤维的制备提 供了 一个新方法。对本发明进行详细说明。本发明的陶瓷纳米复合纤维的静电纺丝制备方法,按以下步骤实施步骤1 按体积百分比,称取粒径为10nm-300nm的陶瓷纳米颗粒3% -10%,陶瓷 前驱体3% -20%,可纺高聚物5% -30%,溶剂40% -89%,总体积为100% ;所述陶瓷纳米颗粒选取金属氧化物、金属氮化物、无机物氮化物、无机物碳化物 中的一种或几种,包括有二氧化钛、氧化锌、氧化镁、氧化钙、二氧化锆、五氧化二钒、氧化 铁、氧化钴、氧化镍、氧化铝、二氧化锰、二氧化锡、氧化铅、氧化铬、氧化镉、二氧化硅、氧化 硼、氧化砷、碳化硅、碳化硼、氮化硅、氮化硼、无机碳化物、无机氮化物。所述陶瓷前驱体选取钛酸丁酯、正硅酸乙酯、醋酸锌、氯化锰、氯化锡、乙酸锌、乙 酸镍、硝酸钡、硝酸铁、硝酸铈、硝酸钇、硝酸铟、硝酸锆、硝酸银中的一种。所述可纺高聚物选取聚乙烯吡咯烷酮、聚乙二醇、聚丙烯腈、聚乙烯醇缩丁醛、聚 丙烯酸钠、聚甲基丙烯酸甲酯、聚乙烯醇、纤维素、尼龙66、间亚苯基间苯二酰胺、弹性多肽、 重组蛋白、聚酰亚胺、聚乳酸或聚苯并咪唑中的一种。所述溶剂选取去离子水、乙醇、丙酮、氯仿、异丙醇、甲醇、甲苯、四氢呋喃、苯、苄 醇1,4_ 二噁烷、丙醇、二氯甲烷、四氯化碳、环己烷、环乙酮、苯酚、吡啶、三氯乙烷、乙酸、甲 酸、六氟异丙醇、六氟丙酮、N,N- 二甲基乙酰胺、乙腈、N-甲基吗啉-N-氧化物、1,3- 二氧戊 环、甲基乙基酮或N-甲基吡咯烷酮中的一种。步骤2 将步骤1中称取的可纺高聚物加入到溶剂中,在水浴中加热并使用磁力搅 拌仪进行搅拌,制得具有一定粘度的可纺高聚物溶液;步骤3 将步骤1中称取的陶瓷前驱体加入到步骤2中得到的可纺高聚物溶液中, 在水浴中加热并使用磁力搅拌仪进行搅拌,陈化2-12h,得到成分均勻的陶瓷前驱体可纺溶 液;步骤4 将步骤1中称取的陶瓷纳米颗粒加入到步骤3中得到的陶瓷前驱体可纺4溶液中,在水浴中保持恒温,然后对溶液进行分散,为防止局部过热和加快陶瓷纳米颗粒分 散,需要持续搅拌l_2h,然后对混合溶液进行超声波分散0. 5-lh和恒温溶胀0. 5-lh,形成 成分均勻的陶瓷纳米颗粒/陶瓷前驱体/可纺高聚物纺丝液;步骤5 将步骤4中得到的纺丝液倒入注射器,采用削平的注射针头作为喷射细 流的毛细管,静电纺丝过程中电压为10-40kV,收集距离为10-30cm,纺丝液推进速度为 0. 5-2. 5mL/h,环境温度为10_50°C,环境湿度为50% -75%,按照静电纺丝技术制备成陶瓷 纳米颗粒/陶瓷前驱体/可纺高聚物的复合纳米纤维;步骤6 将步骤5中得到的复合纳米纤维经过650°C -1200°C烧结,得到陶瓷纳米复合纤维。本发明制备方法的原理在于首先,本发明的方法要控制陶瓷纳米颗粒与陶瓷前驱体在纺丝液中所占的比例, 比例大则在静电纺丝过程中不能得到复合纳米纤维,比例过小则不能得到陶瓷纳米复合纤 维。其次,在纺丝液的制备过程中加入陶瓷纳米颗粒,与现有技术相比,扩大了电纺复 合纳米纤维的制备范围,增加了陶瓷纳米复合纤维的制备种类1)、当同一种陶瓷的前驱体 和纳米颗粒混合时,本发明的方法相当于增加了纤维中的陶瓷相的含量,烧结后可制得更 致密的纳米陶瓷纤维;2)、当前驱体与纳米颗粒为不同种陶瓷时,本发明得到的纳米复合纤 维中可包括无前驱体的陶瓷材料和前驱体不能与高聚物制成可纺溶液的陶瓷材料,得到的 复合纤维种类增多;3)、现有的部分陶瓷前驱体的溶剂以及可纺高聚物的体系不同,不能混 合制备可纺溶液,而本发明中陶瓷纳米颗粒对于溶剂体系无要求,可制得的复合纤维种类 显著增多。实施例1按体积百分比,称取粒径为IOnm的碳化硼(B4C)纳米颗粒3 %,醋酸锌15 %,聚乙 烯醇(简称PVA)为10%,去离子水为72%,总体积为100%。将PVA加入到去离子水中,在 水浴中加热并磁力搅拌,制得具有一定粘度的PVA溶液。然后将醋酸锌溶于该PVA溶液,加 热搅拌并陈化2h,得到成分均勻的醋酸锌/PVA溶液。再将B4C纳米颗粒加入到该醋酸锌/ PVA溶液中,持续搅拌lh,然后对混合溶液进行超声波分散0. 5h,并恒温溶胀0. 5h,形成成 分均勻的B4C/醋酸锌/PVA纺丝液。将该纺丝液倒入注射器,采用削平的注射针头作为喷射 细流的毛细管,静电纺丝过程中电压为40kV,收集距离为10cm,纺丝液推进速度为0. 5mL/ h,环境温度为10°C,环境湿度为75%,经过静电纺丝技术制备成B4C/醋酸锌/PVA复合纳 米纤维;将复合纳米纤维经过1200°C烧结,得到B4C/ZnO复合纳米纤维。相同组分及实验条件下,本发明方法制得的B4CVZnO复合纳米纤维与现有方法得 到的复合纳米纤维主要技术参数见表1实施例1。实施例2按体积百分比,取粒径为300nm的氮化硅(Si3N4)纳米颗粒4%,正硅酸乙酯8%, 聚乙烯吡咯烷酮(PVP) 5%,异丙醇83%,总体积为100%。将聚乙烯吡咯烷酮(PVP)加入到 异丙醇中,在水浴中加热并磁力搅拌,制得具有一定粘度的PVP溶液。然后将正硅酸乙酯溶 于PVP溶液,加热搅拌并陈化12h,得到成分均勻的正硅酸乙酯/PVP溶液。再将Si3N4纳米 颗粒加入到溶液中,持续搅拌lh,然后对混合溶液进行超声波分散0. 5h,并恒温溶胀0. 5h,形成成分均勻的Si3N4/正硅酸乙酯/PVP纺丝液。将纺丝液倒入注射器,采用削平的注射 针头作为喷射细流的毛细管,静电纺丝过程中电压为10kV,收集距离为30cm,纺丝液推进 速度为2. 5mL/h,环境温度为50°C,环境湿度为50%,经过静电纺丝技术制备成Si3N4/正硅 酸乙酯/PVP复合纳米纤维;将复合纳米纤维经过1000°C烧结,得到Si3N4/Si02复合纳米纤 维。相同组分及实验条件下,本发明方法制得的Si3N4/Si02复合纳米纤维与现有方法 得到的复合纳米纤维特征见表1实施例2。实施例3按体积百分比,取粒径为30nm的氧化钛(TiO2)纳米颗粒8%,钛酸丁酯12%,聚乙 烯醇缩丁醛(PVB) 30%,二氯甲烷50%,总体积为100%。将聚乙烯醇缩丁醛(PVB)加入到 二氯甲烷中,在水浴中加热并磁力搅拌,制得具有一定粘度的PVB溶液。然后将钛酸丁酯加 入到PVB溶液中,加热搅拌并陈化4h,得到成分均勻的钛酸丁酯/PVB溶液。再将TiO2纳米 颗粒加入到钛酸丁酯/PVB溶液中,持续搅拌2h,然后对混合溶液进行超声波分散0. 5h,并 恒温溶胀0. 5h,形成成分均勻的TiO2/钛酸丁酯/PVB纺丝液。将纺丝液倒入注射器,采用 削平的注射针头作为喷射细流的毛细管,静电纺丝过程中电压为30kV,收集距离为20cm, 纺丝液推进速度为2mL/h,环境温度为20°C,环境湿度为60%,经过静电纺丝技术制备成 TiO2/钛酸丁酯/PVB复合纳米纤维;将复合纳米纤维经过800°C烧结,得到Ti02/Ti02复合 纳米纤维。相同组分及实验条件下,本发明方法制得的Ti02/Ti02复合纳米纤维与现有方法 得到的复合纳米纤维主要技术参数见表1实施例3实施例4按体积百分比,取粒径为IOOnm的氮化硼(BN)纳米颗粒6%,硝酸铝20%,聚乙二 醇(PEG) 25%,丙酮49%,总体积为100%。将聚乙二醇(PEG)加入到丙酮中,在水浴中加 热并磁力搅拌,制得具有一定粘度的PEG溶液。然后将硝酸铝加入到PEG溶液中,加热搅拌 并陈化6h,得到成分均勻的硝酸铝/PEG溶液。再将BN纳米颗粒加入到硝酸铝/PEG溶液 中,持续搅拌2h,然后对混合溶液进行超声波分散0. 5h,并恒温溶胀0. 5h,形成成分均勻的 BN/硝酸铝/PEG纺丝液。将纺丝液倒入注射器,采用削平的注射针头作为喷射细流的毛细 管,静电纺丝过程中电压为30kV,收集距离为20cm,纺丝液推进速度为1. 5mL/h,环境温度 为40V,环境湿度为60%,经过静电纺丝技术制备成BN/硝酸铝/PEG复合纳米纤维;将复 合纳米纤维经过650°C烧结,得到BNAl2O3复合纳米纤维。相同组分及实验条件下,本发明方法制得的BNAl2O3复合纳米纤维与现有方法得 到的复合纳米纤维主要技术参数见表1实施例4。实施例5按体积百分比,取粒径为250nm的氧化铜(CuO)纳米颗粒10%,硝酸钡3%,聚丙 烯酸钠(PAAS) 15%,去离子水72%,总体积为100%。将聚丙烯酸钠(PAAS)加入到去离 子水中,在水浴中加热并磁力搅拌,制得具有一定粘度的PAAS溶液。然后将硝酸钡加入到 PAAS溶液中,加热搅拌并陈化8h,得到成分均勻的硝酸钡/PAAS溶液。再将CuO纳米颗粒 加入到硝酸钡/PAAS溶液中,持续搅拌1. 5h,然后对混合溶液进行超声波分散lh,并恒温溶 胀0. 5h,形成成分均勻的CuO/硝酸钡/PAAS纺丝液。将纺丝液倒入注射器,采用削平的注射针头作为喷射细流的毛细管,静电纺丝过程中电压为15kV,收集距离为15cm,纺丝液推 进速度为lmL/h,环境温度为10°C,环境湿度为50% %,经过静电纺丝技术制备成CuO/硝酸 钡/PAAS复合纳米纤维;将复合纳米纤维经过700°C烧结,得到Cu0/Si02复合纳米纤维。相同组分及实验条件下,本发明方法制得的CuCVSiO2复合纳米纤维与现有方法得 到的复合纳米纤维主要技术参数见表1实施例5。实施例6按体积百分比,取粒径为200nm的碳化硅(SiC)纳米颗粒5%,硝酸锆10%,尼龙 66为20%,N-甲基吡咯烷酮65%,总体积为100%。将尼龙66加入到N-甲基吡咯烷酮中, 在水浴中加热并磁力搅拌,制得具有一定粘度的尼龙66溶液。然后将硝酸锆加入到尼龙66 溶液中,加热搅拌并陈化7h,得到成分均勻的硝酸锆/尼龙66溶液。再将SiC纳米颗粒加 入到硝酸锆/尼龙66溶液中,持续搅拌1. 5h,然后对混合溶液进行超声波分散0. 5h,并恒 温溶胀lh,形成成分均勻的SiC/硝酸锆/尼龙66纺丝液。将纺丝液倒入注射器,采用削 平的注射针头作为喷射细流的毛细管,静电纺丝过程中电压为25kV,收集距离为25cm,纺 丝液推进速度为2mL/h,环境温度为40°C,环境湿度为65%,经过静电纺丝技术制备成SiC/ 硝酸锆/尼龙66复合纳米纤维;将复合纳米纤维在1100°C烧结,得到SiCArO2复合纳米纤 维。相同组分及实验条件下,本发明方法制得的SiCArO2复合纳米纤维与现有方法得 到的复合纳米纤维主要技术参数见表1实施例6。实施例7按体积百分比,取粒径为30nm的等量氧化镉(CdO)和氮化硅(Si3N4)纳米颗粒共 5%,氯化锰10%,聚乳酸(PLA) 20%,六氟丙酮65%,总体积为100%。将聚乳酸加入到六 氟丙酮中,在水浴中加热并磁力搅拌,制得具有一定粘度的聚乳酸溶液。然后将氯化锰加入 到聚乳酸溶液中,加热搅拌并陈化10h,得到成分均勻的氯化锰/聚乳酸溶液。再将CdO和 Si3N4纳米颗粒加入到氯化锰/聚乳酸溶液中,持续搅拌lh,然后对混合溶液进行超声波分 散lh,并恒温溶胀0. 5h,形成成分均勻的CdO/Si3N4/氯化锰/聚乳酸纺丝液。将纺丝液倒入 注射器,采用削平的注射针头作为喷射细流的毛细管,静电纺丝过程中电压为10kV,收集距 离为10cm,纺丝液推进速度为0. 5mL/h,环境温度为10°C,环境湿度为50%,经过静电纺丝 技术制备成cdo/si3N4/氯化锰复合纳米纤维;将复合纳米纤维经过iioo°c烧结,得到cdo/ Si3N4/Mn02复合纳米纤维。相同组分及实验条件下,本发明方法制得的Cd0/Si3N4/Mn02复合纳米纤维与现有 方法得到的复合纳米纤维主要技术参数见表1实施例7。实施例8按体积百分比,取粒径为50nm的等量氧化铁(Fe203)、氮化硼(BN)纳米颗粒共 5%,等量的乙酸镍10%,聚乙醇酸(PGA) 20%,六氟代异丙醇65%,总体积为100%。将聚 乙醇酸加入到六氟代异丙醇中,在水浴中加热并磁力搅拌,制得具有一定粘度的聚乙醇酸 溶液。然后将乙酸镍加入到聚乙醇酸溶液中,加热搅拌并陈化llh,得到成分均勻的乙酸镍 /聚乙醇酸溶液。再将Fe203、BN纳米颗粒加入到乙酸镍/聚乙醇酸溶液中,持续搅拌1. 5h, 然后对混合溶液进行超声波分散lh,并恒温溶胀lh,形成成分均勻的Fe203/BN/乙酸镍/聚 乙醇酸纺丝液。将纺丝液倒入注射器,采用削平的注射针头作为喷射细流的毛细管,静电纺
7丝过程中电压为30kV,收集距离为20cm,纺丝液推进速度为2mL/h,环境温度为40°C,环境 湿度为55%,经过静电纺丝技术制备成Fe203/BN/乙酸镍/聚乙醇酸复合纳米纤维;将复合 纳米纤维经过1100°C烧结,得到Fe203/BN/Ni0复合纳米纤维。相同组分及实验条件下,本发明方法制得的Fe203/BN/Ni0复合纳米纤维与现有方 法得到的复合纳米纤维主要技术参数见表1实施例8。实施例9按体积百分比,取粒径为IOOnm的等量碳化硅(SiC)、碳化硼(B4N)、纳米颗粒共 5%,硝酸铟10%,间亚苯基间苯二酰胺20%,间甲酚65%,总体积为100%。将间亚苯基 间苯二酰胺加入到间甲酚中,在水浴中加热并磁力搅拌,制得具有一定粘度的间亚苯基间 苯二酰胺溶液。然后将硝酸铟加入到间亚苯基间苯二酰胺溶液中,加热搅拌并陈化12h,得 到成分均勻的硝酸铟/间亚苯基间苯二酰胺溶液。再将SiC、B4N纳米颗粒加入到硝酸铟/ 间亚苯基间苯二酰胺溶液中,持续搅拌1. 5h,然后对混合溶液进行超声波分散lh,并恒温 溶胀lh,形成成分均勻的SiC/B4N/硝酸铟/间亚苯基间苯二酰胺纺丝液。将纺丝液倒入 注射器,采用削平的注射针头作为喷射细流的毛细管,静电纺丝过程中电压为25kV,收集距 离为25cm,纺丝液推进速度为1. 5mL/h,环境温度为25°C,环境湿度为65%,经过静电纺丝 技术制备成SiC/B4N/硝酸铟/间亚苯基间苯二酰胺复合纳米纤维;将复合纳米纤维经过 1100°C烧结,得到SiC/B4N/In203复合纳米纤维。相同组分及实验条件下,本发明方法制得的SiC/B4N/In203复合纳米纤维与现有方 法得到的复合纳米纤维主要技术参数见表1实施例9。实施例10按体积百分比,取粒径为150nm的等量氧化镍(NiO)、二氧化硅(SiO2)、二氧化锆 (ZrO2)纳米颗粒共5%,氯化锡10%,聚苯乙烯(PS) 20%,丁酮65%,总体积为100%。将 聚苯乙烯加入到丁酮中,在水浴中加热并磁力搅拌,制得具有一定粘度的聚苯乙烯溶液。然 后将氯化锡加入到聚苯乙烯溶液中,加热搅拌并陈化12h,得到成分均勻的氯化锡/聚苯乙 烯溶液。再将Ni0、Si02、Zr02纳米颗粒加入到氯化锡/聚苯乙烯溶液中,持续搅拌2h,然后 对混合溶液进行超声波分散lh,并恒温溶胀lh,形成成分均勻的Ni0/Si02/Zr02/氯化锡/ 聚苯乙烯纺丝液。将纺丝液倒入注射器,采用削平的注射针头作为喷射细流的毛细管,静电 纺丝过程中电压为25kV,收集距离为25cm,纺丝液推进速度为1. 5mL/h,环境温度为25°C, 环境湿度为65%,经过静电纺丝技术制备成Ni0/Si02/Zr02/氯化锡复合纳米纤维;将复合 纳米纤维经过1100°C烧结,得到Ni0/Si02/Zr02/Sn02复合纳米纤维。相同组分及实验条件下,本发明方法制得的Ni0/Si02/Zr02/Sn02复合纳米纤维与 现有方法得到的复合纳米纤维主要技术参数见表1实施例10。实施例11按体积百分比,取粒径为200nm的等量氮化硼(BN)、氮化硅(Si3N4)、二氧化钛 (TiO2)纳米颗粒共5%,硝酸铈10%,聚丙烯腈(PAN) 20%,二甲基乙酰胺65%,总体积为 100%。将聚丙烯腈加入到二甲基乙酰胺中,在水浴中加热并磁力搅拌,制得具有一定粘度 的聚丙烯腈溶液。然后将硝酸铈加入到聚丙烯腈溶液中,加热搅拌并陈化12h,得到成分 均勻的硝酸铈/聚丙烯腈溶液。再将BN、Si3N4, TiO2纳米颗粒加入到硝酸铈/聚丙烯腈溶 液中,持续搅拌2h,然后对混合溶液进行超声波分散lh,并恒温溶胀lh,形成成分均勻的BN/Si3N4/Ti02/硝酸铈/聚丙烯腈纺丝液。将纺丝液倒入注射器,采用削平的注射针头作 为喷射细流的毛细管,静电纺丝过程中电压为25kV,收集距离为25cm,纺丝液推进速度为 1. 5mL/h,环境温度为25°C,环境湿度为65 %,经过静电纺丝技术制备成BN/Si3N4/Ti02/硝 酸铈/聚丙烯腈复合纳米纤维;将复合纳米纤维经过1100°c烧结,得到BN/Si3N4/Ti02/Ce02 复合纳米纤维。相同组分及实验条件下,本发明方法制得的BN/Si3N4/Ti02/Ce02复合纳米纤维与 现有方法得到的复合纳米纤维主要技术参数见表1实施例11。实施例12按体积百分比,取粒径为250nm的等量碳化硅(SiC)、氧化铁(Fe2O3)、碳化硼(B4C) 纳米颗粒共5%,硝酸钇10%,聚乙内酯(PCL) 20%,环己烷65%,总体积为100%。将聚乙 内酯加入到环己烷中,在水浴中加热并磁力搅拌,制得具有一定粘度的聚乙内酯溶液。然后 将硝酸钇加入到聚乙内酯溶液中,加热搅拌并陈化12h,得到成分均勻的硝酸钇/聚乙内酯 溶液。再将SiC、Fe203、纳米颗粒加入到硝酸钇/聚乙内酯溶液中,持续搅拌1.5h,然后对混 合溶液进行超声波分散lh,并恒温溶胀lh,形成成分均勻的SiC/Fe203/B4C/硝酸钇/聚乙 内酯纺丝液。将纺丝液倒入注射器,采用削平的注射针头作为喷射细流的毛细管,静电纺丝 过程中电压为25kV,收集距离为25cm,纺丝液推进速度为1. 5mL/h,环境温度为25°C,环境 湿度为65%,经过静电纺丝技术制备成SiC/Fe203/B4C/硝酸钇复合纳米纤维;将复合纳米 纤维经过1100°C烧结,得到SiC/Fe203/B4C/Y203复合纳米纤维。相同组分及实验条件下,本发明方法制得的SiC/Fe203/B4C/Y203复合纳米纤维与现 有方法得到的复合纳米纤维主要技术参数见表1实施例12。表1各个实施例本发明制备与现有方法得到的复合纳米纤维特征比较表 综上所述,本发明的方法扩大了可纺高聚物和溶剂的可选范围,制备出的纳米复 合陶瓷纤维直径分布平均,长径比高,柔韧性好,所涉及的实验工艺步骤简单,产品成功率 高,再现性好,为不能共同电纺的陶瓷材料制备复合纳米纤维提供了一个简易高效、易于实 现的方法,可广泛应用于太阳能敏化电池、磁性材料、燃料电池、介电材料、人工骨替代材 料、静电屏蔽材料、光学材料、敏感材料、过滤材料、催化剂、药物释放载体等领域。
本发明公开了一种陶瓷纳米复合纤维的静电纺丝制备方法,该方法按以下步骤具体实施步骤1按体积百分比,称取粒径为10nm-300nm的陶瓷纳米颗粒3%-10%,陶瓷前驱体3%-20%,可纺高聚物5%-30%,溶剂40%-89%,总体积为100%;步骤2将可纺高聚物加入到溶剂中,在水浴中加热并磁力搅拌;步骤3将陶瓷前驱体加入到步骤2中得到的可纺高聚物溶液中,在水浴中加热并磁力搅拌陈化;步骤4再将陶瓷纳米颗粒加入到步骤3中得到的陶瓷前驱体可纺溶液中,在水浴中保持恒温,进行超声波分散和恒温溶胀,形成纺丝液;步骤5将丝液按照静电纺丝技术制备成复合纳米纤维;步骤6将复合纳米纤维经烧结,得到陶瓷纳米复合纤维。本发明方法,对于原料选择条件宽,可选范围大。
陶瓷纳米复合纤维的静电纺丝制备方法
- 专利详情
- 全文pdf
- 权力要求
- 说明书
- 法律状态
查看更多专利详情
下载专利文献
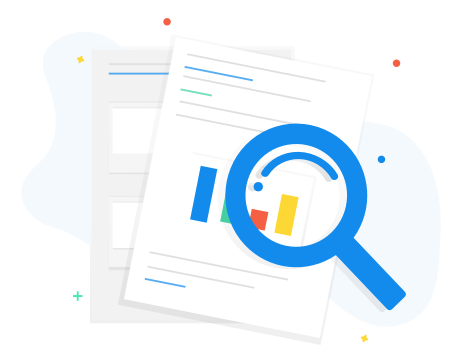
下载专利
同类推荐
-
徐雷宋云昌任转龙
您可能感兴趣的专利
-
沈晓芳代淑梅, 李秋园代淑梅, 李秋园代淑梅, 李秋园
专利相关信息
-
代淑梅, 李秋园代淑梅, 李秋园张欣P·莫拉佐尼P·莫拉佐尼白佳海, 唐钰栋