制备烧结多孔材料过滤板的等静压成型模具及方法[0002]烧结多孔材料过滤元件一般被制成管状,称烧结多孔材料过滤管。有时,烧结多孔材料过滤元件也做成板状,称烧结多孔材料过滤板。例如,有的真空过滤机所采用的过滤元件就为扇形烧结陶瓷多孔材料过滤板。[0003]目前的烧结多孔材料过滤板大致上有以下三类结构及制备方式:第一类为注浆成型,即通过注浆得到具有中空结构的陶瓷过滤基板,并在空腔内充填支撑颗粒,经烧结而成,然后再在其表面施加过滤表层,如CN1198357A中公开的一种固液分离用陶瓷过滤板及制备方法即属于此类;第二类为分片模压成形后将两片对合粘接获得中空结构的过滤板,即通过模压得到一面带凸起支撑肋、一面为平面的微孔陶瓷单片,而后将两片对合粘结,其工艺流程一般为配料、模压单片、烧成、平面加工、粘接、装配附件,或配料、模压单片、粘接、烧成、平面加工、装配附件,如CN1390623A中所述微孔陶瓷过滤板即属于此类;第三类为CN1486212A所公开的过滤元件及其制造方法,是在模压时在陶瓷混合物中设置至少一个用于所希望凹入区域的芯部材料,压制成坯,然后经高温烧结,使用于凹入区域的芯部材料被燃尽,从而得到基本上连续的过滤表面及所需中空流道,然后通过浸浆、喷射、浇注方式获得过滤工作层,再次经烧结得到烧结多微孔层。[0004]上述第一类的缺点在于:为保证过滤板有足够的机械强度,通常需采用较小粒径的陶瓷微粒,这样所得微孔细小,会造成过滤板滤水阻力增大;其次,注浆方法成型只能得到周壁面基本相等的中空体,由于受抽吸壁厚限止,两侧壁显得相对较薄,转入侧壁抗张强度较低,在使用过程中往往会造成过滤板根部发生开裂甚至折断;再就是,中空支撑是为颗粒堆积支撑,排水阻力较大,影响过滤效率和产能。第二类的缺点在于:生产工艺流程较长,生产效率不高,尤其是对合粘结不仅工效低下,而且还会造成诸多缺陷,如粘接剂用量和粘接压紧力不均匀,会造成基体的开裂;内部多余粘结剂会在凸起支撑肋侧面产生毛糙凸出,占据流道增加排水阻力;再就是,粘结产品在使用过程中,还容易发生粘接力不强而开裂,此类开裂约占5%左右,并且不对称结构,抗抽吸交变应力疲劳强度低,使用寿命短。上述第三类的缺点在于:整体密度存在较大差异,特别是两过滤板面连接部位疏松密度低,严重影响基板整体机械强度,在工作过程中,抽吸及反冲交变应力,易发生疲劳开裂而报废;而且还有可能在烧结过程中,因过滤板各部分密度不同,而发生变形、甚至发生开裂,造成成品率降低。
[0005]本发明首先要解决的技术问题是提供一种结构强度、过滤效率俱佳,且便于制造的烧结多孔材料过滤板及用于制备该过滤板的预制中空板坯。[0006]本发明其次要解决的技术问题是提供一种便于制造上述预制中空板坯的制备烧结多孔材料过滤板的等静压成型模具及利用该模具的制备烧结多孔材料过滤板的方法。[0007]本发明更进一步要解决的技术问题是提供一种用于对包括但不限于上述预制中空板坯进行烧结的制备板状烧结体的专用烧结装置及使用了该装置的方法,提高产品烧结质量。[0008]本发明的烧结多孔材料过滤板包括由烧结金属多孔材料或由烧结陶瓷多孔材料构成的过滤板本体,所述过滤板本体为中空板状结构,该过滤板本体是由粉末料模压成型的预制中空板坯进行烧结制成,该预制中空板坯的一边缘处设有狭长的内模抽芯口,预制中空板坯的内腔中相对该抽芯口设有连该预制中空板坯相对两板面的加强筋,所述抽芯口、加强筋在模压成型该预制中空板坯时一体模压成型于该预制中空板坯上;所述过滤板本体上安装有封闭该抽芯口的密封条,该密封条或过滤板本体上还设有与过滤板本体内腔导通的出口。由于抽芯口、加强筋在模压成型该预制中空板坯时一体模压成型于该预制中空板坯上,模压成型后内模(用于成型预制中空板坯的内腔、加强筋、抽芯口)从抽芯口抽出而脱模,在由预制中空板坯烧结制成的过滤板本体上安装所述密封条后烧结多孔材料过滤板则基本制成。该烧结多孔材料过滤板相比于现有几种过滤板可具有更高的结构强度,易保证过滤效率,且便于制造。
[0009]作为上述烧结多孔材料过滤板的一种具体应用实例,所述过滤板本体为梯形或扇形板状结构,其包括呈直线形或呈圆弧形的底边部、与所述底边部相对设置的顶边部以及分别连接底边部与顶边部的左右两侧边部,所述密封条位于该过滤板本体的底边部上并沿该底边部延伸设置,所述出口设置在顶边部上,该出口与抽芯口、加强筋一并在模压成型预制中空板坯时一体模压成型于预制中空板坯上。该应用实例的烧结多孔材料过滤板可用来替换圆盘真空过滤机上使用的扇形烧结陶瓷多孔材料过滤板。其中,作为其加强筋的一种优选结构,所述加强筋包括至少一根条状加强筋,该条状加强筋的一端与所述顶边部的内侧面连为一体,另一端沿内模抽芯方向延伸至靠近底边部的区域内。更进一步的,所述加强筋包括两根相互平行并在过滤板本体的内腔中左右对称设置的所述条状加强筋。
[0010]上述密封条可以由不锈钢或由与过滤板本体相同的材料构成。另外,所述密封条可采用焊接或粘接于过滤板本体的抽芯口处。此外,过滤板本体优选由烧结T1-Al金属间化合物基合金多孔材料或烧结Fe-Al金属间化合物基合金多孔材料构成。
[0011]制备上述烧结多孔材料过滤板的预制中空板坯,由粉末料模压成型,其一边缘处设有狭长的内模抽芯口,其内腔中相对该抽芯口设有连接该预制中空板坯上相对两板面的加强筋,所述抽芯口、加强筋在模压成型预制中空板坯时一体模压成型于该预制中空板坯上。
[0012]该预制中空板坯可以为梯形或扇形板状结构,其包括呈直线形或呈圆弧形的底边部、与所述底边部相对设置的顶边部以及分别连接底边部与顶边部的左右两侧边部,所述抽芯口位于该预制中空板坯的底边部上并沿该底边部延伸设置,所述顶边部上设有与预制中空板坯内腔导通的出口,该出口与抽芯口、加强筋一并在模压成型预制中空板坯时一体模压成型于预制中空板坯上。另外,在该预制中空板坯中,作为其加强筋的一种具体结构,所述加强筋包括两根相互平行并在预制中空板坯的内腔中左右对称设置的条状加强筋,条状加强筋的一端与所述顶边部的内侧面连为一体,另一端沿内模抽芯方向延伸至靠近底边部的区域内。
[0013]本发明制备烧结多孔材料过滤板的等静压成型模具,该模具包括外模单元、内模单元、底部封模单元和顶部封模单元,所述外模单元包括由弹性材料制成的中空板形套,该中空板形套设有顶口和底口,所述顶口和底口分别与顶部封模单元和底部封模单元密封连接;所述内模单元包括与中空板形套的内腔相适配的芯板,芯板、中空板形套、底部封模单元以及顶部封模单元之间形成模具型腔,芯板的底部定位安装在底部封模单元上,芯板顶部靠近外模单元的顶口并设有向芯板内延伸的加强筋成型凹槽,成型后将芯板从中空板形套的底口处向外时抽出时,由所述加强筋成型凹槽所成型的加强筋不妨碍芯板作抽芯运动。通过该模具可对本发明上述烧结多孔材料过滤板进行等静压成型,从而在成型过程中确保粉末料整体受压均匀,密度分布均匀,进一步提高烧结多孔材料过滤板的过滤效果和结构强度。
[0014]使用了上述模具制备烧结多孔材料过滤板的方法,其步骤包括:1)将粉末料填入上述等静压成型模具内,并机械振实,使粉末料充分、均匀填充至模具型腔中,然后将组装好的等静压成型模具放入等静压成型机内压制成型;2)从模具中取出并获得一预制中空板坯,该预制中空板坯的一边缘处通过模压成型形成有狭长的内模抽芯口,其内腔中相对该抽芯口成型有连接该预制中空板坯上相对两板面的加强筋;3)将预制中空板坯放入烧结炉内进行烧结,冷却后得到由烧结金属多孔材料或由烧结陶瓷多孔材料构成的过滤板本体,随后在该过滤板本体上安装用于封闭所述抽芯口的密封条。通过该方法可制造出前述的烧结多孔材料过滤板。
[0015]上述制备烧结多孔材料过滤板的方法中还可以使用以下制备板状烧结体的专用烧结装置,从而对预制中空板坯进行约束烧结,防止预制中空板坯在高温状态下发生变形,提高烧结多孔材料过滤板的产品质量。当然,该专用烧结装置也可以用于对除烧结多孔材料过滤板外的其他板状烧结体进行烧结。该专用烧结装置包括由耐高温材料制成的立式板形槽、槽盖以及槽盖固定装置,所述立式板形槽包括立式板形槽本体、设置于立式板形槽本体内的板形深槽腔以及分别设置于立式板形槽本体相对两板面上的防热变形加强筋,板形深槽腔的周边及底部封闭且开口位于立式板形槽本体的顶部,槽盖与该板形深槽腔的开口配合后通过槽盖固定装置固定于立式板形槽本体上,槽盖上间隔布置有排气孔。
[0016]使用该专用烧结装置制备板状烧结体的具体方法为:步骤包括I)先在专用烧结装置的板形深槽腔的底部铺设一定高度的传热、束缚材料,然后将制备板状烧结体的预制成型板坯装入板形深槽腔内并放置在底部传热、束缚材料上,并使预制成型板坯与板形深槽腔内壁保持设定距离;2)进一步从板形深槽腔的开口向板形深槽腔内倒入传热、束缚材料,使整个预制成型板坯淹没在传热、束缚材料中并由该传热、束缚材料所保持,机械振实使传热、束缚材料充分、均匀填充在预制成型板坯周围;3)安装槽盖并通过槽盖固定装置将槽盖与立式板形槽本体固定,然后再将装好的专用烧结装置放入烧结炉进行烧结,烧结后出炉并从专用烧结装置取出由预制成型板坯烧结形成的板状烧结体。
[0017]下面结合附图和
[0018]图1为本发明烧结多孔材料过滤板【具体实施方式】的结构示意图。
[0019]图2为图1中A — A向剖视图。
[0020]图3为本发明制备烧结多孔材料过滤板的等静压成型模具【具体实施方式】的结构示意图。
[0021]图4为图3中A — A向剖视图。
[0022]图5为通过图3、4所示模具模压成型后的预制中空板坯的结构示意图。
[0023]图6为本发明制备板状烧结体的专用烧结装置(未安装槽盖)的结构示意图。
[0024]图7为图6中A — A向剖视图。
[0025]图8为图6、7所示专用烧结装置的立体结构示意图。
[0026]图9为图8所示专用烧结装置使用过程中的结构示意图。
[0027]图10为图9中A向结构示意图。
【具体实施方式】
[0028]如图1、2和5所示,烧结多孔材料过滤板包括由烧结金属多孔材料或由烧结陶瓷多孔材料构成的过滤板本体100,所述过滤板本体100为中空板状结构,该过滤板本体100由粉末料模压成型的预制中空板坯100Y进行烧结制成,该预制中空板坯100Y的一边缘处设有狭长的内模抽芯口 110,预制中空板坯100Y的内腔中相对该抽芯口 110设有连该预制中空板坯100Y相对两板面的加强筋120,所述抽芯口 110、加强筋120在模压成型该预制中空板坯100Y时一体模压成型于该预制中空板坯100Y上;所述过滤板本体100上安装有封闭该抽芯口 Iio的密封条140,该密封条140 (或过滤板本体100上)上还设有与过滤板本体100内腔导通的出口 190。由于过滤板本体100是由预制中空板坯100Y烧制而成的,因此过滤板本体100的结构附随于预制中空板坯100Y的结构上,即图1所示的过滤板本体100上依然存在抽芯口 110、加强筋120,该加强筋120连接过滤板本体100相对两板面180 (如图2)。由于整个预制中空板坯100Y为粉末模压成型,且预制中空板坯100Y的内腔设有一体模压成型的加强筋120,同时加强筋120对流体运动的阻碍较小,故上述烧结多孔材料过滤板的结构强度和过滤效率较高。
[0029]该烧结多孔材料过滤板的外形可以根据具体要求来设计,例如可以是矩形、圆形等。目前在圆盘式真空过滤机中使用了一种扇形过滤板,为了替代该扇形过滤板,可将上述的烧结多孔材料过滤板设计为与该扇形过滤板类似的形状。如图1所示,过滤板本体100设计为梯形或扇形板状结构,其包括呈直线形或呈圆弧形的底边部150 (当底边部150为直线形时,过滤板本体100为梯形;当底边部150为圆弧形时,过滤板本体100为扇形)、与所述底边部150相对设置的顶边部160以及分别连接底边部150与顶边部160的左右两侧边部170 (显然为斜边),所述密封条150位于该过滤板本体100的底边部150上并沿该底边部150延伸设置,所述出口 190设置在顶边部160上;另外,为方便烧结多孔材料过滤板的制造,该出口 190与抽芯口 110、加强筋120 —并在模压成型预制中空板坯100Y时一体模压成型于预制中空板坯100Y上。如图1、2和5所示,上述梯形或扇形板状结构的过滤板本体100中,作为加强筋120的一种易于脱模且支撑强度较高的结构,该加强筋120包括至少一根条状加强筋120,该条状加强筋120的一端与所述顶边部160的内侧面连为一体,另一端沿内模抽芯方向延伸至靠近底边部150的区域内。加强筋120最好包括两根相互平行并在过滤板本体100的内腔中左右对称设置的所述条状加强筋120。
[0030]与上述梯形或扇形板状结构的过滤板本体100相对应,如图5所示,制备该过滤板本体100的预制中空板坯同样也为梯形或扇形板状结构,其包括呈直线形或呈圆弧形的底边部150、与所述底边部150相对设置的顶边部160以及分别连接底边部150与顶边部160的左右两侧边部170 (为斜边),所述抽芯口 110位于该预制中空板坯的底边部150上并沿该底边部150延伸设置,所述顶边部160上设有与预制中空板坯内腔导通的出口 190,该出口 190与抽芯口 110、加强筋120 —并在模压成型预制中空板坯时一体模压成型于预制中空板坯上。其中,所述加强筋120包括了两根相互平行并在预制中空板坯的内腔中左右对称设置的条状加强筋120,条状加强筋120的一端与所述顶边部160的内侧面连为一体,另一端沿内模抽芯方向延伸至靠近底边部150的区域内。
[0031]上述的烧结多孔材料过滤板由以下方法制备:首先,将粉末料填入一等静压成型模具内,并机械振实,使粉末料充分、均匀填充至模具型腔中,然后将组装好的等静压成型模具放入等静压成型机内压制成型;其次,从模具中取出并获得预制中空板坯100Y,该预制中空板坯100Y的一边缘处通过模压成型形成有狭长的内模抽芯口 110,其内腔中相对该抽芯口 110成型有连接该预制中空板坯上相对两板面的加强筋120 ;此后,将预制中空板坯100Y放入烧结炉内进行烧结,冷却后得到过滤板本体100,随后在该过滤板本体100上安装用于封闭所述抽芯口 Iio的密封条140。其中,如图3、4,上述等静压成型模具结构具体包括外模单元210、内模单元220、底部封模单元230和顶部封模单元240,所述外模单元210包括由弹性材料制成的中空板形套211,该中空板形套211设有顶口和底口,所述顶口和底口分别与顶部封模单元240和底部封模单元230密封连接;所述内模单元220包括与中空板形套211的内腔相适配的芯板221,芯板221、中空板形套211、底部封模单元230以及顶部封模单元240之间形成模具型腔,芯板221的底部定位安装在底部封模单元230上,芯板221顶部靠近外模单元210的顶口并设有向芯板221内延伸的加强筋成型凹槽221a,成型后将芯板221从中空板形套211的底口处向外时抽出时,由所述加强筋成型凹槽221a所成型的加强筋不妨碍芯板221作抽芯运动。
[0032]如图3、4所示,由于所要制备的预制中空板坯100Y为前述的梯形或扇形板状结构,因此,该等静压成型模具中,所述芯板221为等腰梯形结构,其底部定位安装在底部封模单元230上,顶边上设有向上凸起的成型定位杆221b,该成型定位杆221b的上端部与顶部封模单元240中对应的定位孔相适配,所述中空板形套211的内侧设有分别与芯板221的左右侧边平行并间隔一定距离的内斜壁211a。上述的成型定位杆221b既起到对芯板221的定位作用,同时也用于成型预制中空板坯100Y上的出口 19。另外,当预制中空板坯100Y中的加强筋120包括至少一根条状加强筋120,该条状加强筋120的一端与所述顶边部160的内侧面连为一体,另一端沿内模抽芯方向延伸至靠近底边部150的区域内时,相应的,力口强筋成型凹槽221a将包括同样数量且与芯板221的抽芯方向相平行的狭长凹槽。一种较优的设计是:成型定位杆221b位于芯板221的中心线上,加强筋成型凹槽221a包括两条对称设置在成型定位杆221b左右两侧的所述狭长凹槽,这样,成型的预制中空板坯100Y中即形成两根相互平行并在预制中空板坯100Y的内腔中左右对称设置的所述条状加强筋120,且出口 19刚好位于两根条状加强筋120之间。[0033]进一步如图3、4所示,上述模具中,所述底部封模单元230的具体结构包括设有芯板定位槽的刚性底座231以及设置在刚性底座231上方并位于芯板221与中空板形套211之间的底部橡胶密封塞232。同时,所述顶部封模单元240的具体结构包括刚性盖板241以及设置在刚性盖板241下方的顶部橡胶密封塞242,刚性盖板241与顶部橡胶密封塞242形成一个填塞于中空板形套211的顶口内并与其适配的封模体。底部封模单元230与顶部封模单元240中均使用了刚性构件(如钢制构件)加橡胶密封塞的结构,既保证了密封可靠性,同时也保证了模具的整体刚性和强度。当所述成型定位杆221b的上端部与顶部封模单元240中对应的定位孔相适配的情况下,顶部封模单元240中与成型定位杆221b上端适配的定位孔最好仅设于顶部橡胶密封塞242上。另外,外模单元210还可包括安装在中空板形套211外表面的刚性夹板212,进一步提高模具的整体刚性,确保成型质量。图3、4中模具的上下两端外还分别紧套有橡胶密封套213,进一步防止等静压成型时压力油渗入模具创造产品污染。
[0034]上述制备烧结多孔材料过滤板方法中,还可使用一种制备板状烧结体的专用烧结装置。如图6至10所示,该装置包括由耐高温材料制成的立式板形槽310 (例如立式板形槽310整体由耐高温不锈钢制成)、槽盖320以及槽盖固定装置330,所述立式板形槽310包括立式板形槽本体311、设置于立式板形槽本体311内的板形深槽腔312以及分别设置于立式板形槽本体311相对两板面311a上的防热变形加强筋313,板形深槽腔312的周边及底部封闭且开口位于立式板形槽本体311的顶部,槽盖320与该板形深槽腔312的开口配合后通过槽盖固定装置330固定于立式板形槽本体311上,槽盖320上间隔布置有排气孔321。槽盖320最好与立式板形槽310采用相同材料制成,以防槽盖320与立式板形槽310之间因热膨胀系数不同造成损坏。烧结前,先在该专用烧结装置的板形深槽腔312的底部铺设一定高度的传热、束缚材料(例如三氧化二铝粉),然后将制备板状烧结体的预制成型板坯(上述预制中空板坯100Y)装入板形深槽腔312内并放置在底部传热、束缚材料上,并使预制成型板坯与板形深槽腔312内壁保持设定距离;然后,进一步从板形深槽腔312的开口向板形深槽腔312内倒入传热、束缚材料,使整个预制成型板坯淹没在传热、束缚材料中并由该传热、束缚材料所保持,机械振实使传热、束缚材料充分、均匀填充在预制成型板坯周围;此后,安装槽盖320并通过槽盖固定装置330将槽盖320与立式板形槽本体311固定,再将装好的专用烧结装置放入烧结炉进行烧结,烧结后出炉并从专用烧结装置取出过滤板本体100 ;安装槽盖320前,最好在板形深槽腔312的顶部开口处由耐高温网丝覆盖后再安装槽盖320,以防传热、束缚材料从槽盖320上间隔布置的排气孔321泄露。
[0035]为使立式板形槽310的传热效果更适于板状烧结体的烧结,如图6至10,所述立式板形槽本体311及其板形深槽腔312均为矩形结构,立式板形槽本体311 —侧板面的外壁至对应板形深槽腔312内壁之间形成的壁厚与立式板形槽本体311另一侧板面的外壁至对应板形深槽腔312内壁之间形成的壁厚大致上相等。另外,立式板形槽本体311两板面311a的顶部还进一步的分别设置了向板面外侧凸起并沿着该立式板形槽本体311的长度方向延伸的顶部横向加强筋313a,所述槽盖固定装置330包括数个沿着立式板形槽本体311的长度方向间隔设置的卡箍331,所述卡箍331从外向内抱卡住立式板形槽本体311的顶部及其两侧的顶部横向加强筋313a从而将槽盖320压紧在板形深槽腔312的开口上,这样不仅能够对槽盖320进行非常有效的固定,同时在顶部横向加强筋313a和卡箍331的共同作用下可有效防止立式板形槽310开口部位在高温下变形,避免烧结后产品不易取出的窘境。
[0036]另外,如图6至10,所述防热变形加强筋313的优选结构为:防热变形加强筋313包括多根向板面311a外侧凸起并沿立式板形槽本体311的长度方向延伸的横向加强筋313b,同一侧板面311a上的横向加强筋313b在立式板形槽本体311的高度方向上间隔排列。这种结构能够既能够有效防止立式板形槽本体311上两板面311a的热变形,同时有利于板面311a上的温度分布的均匀性,从而更好的保证产品烧结质量。同一侧板面311a上还可设置至少一个横向加强筋313b上连接有把手340,以便工人操作。
[0037]实施例
[0038]如图1、2和5,用于圆盘式真空过滤机的烧结多孔材料过滤板,包括由烧结T1-Al金属间化合物基合金多孔材料构成的过滤板本体100,过滤板本体100为扇形板状结构,其由粉末料等静压模压成型的预制中空板坯100Y进行烧结制成,该预制中空板坯100Y的一边缘处设有狭长的内模抽芯口 110,预制中空板坯100Y的内腔中相对该抽芯口 110设有连该预制中空板坯100Y相对两板面的加强筋120,加强筋120包括两根相互平行并在预制中空板坯的内腔中左右对称设置的条状加强筋120,条状加强筋120的一端与所述顶边部160的内侧面连为一体,另一端沿内模抽芯方向延伸至靠近底边部150的区域内,所述抽芯口110、加强筋120在等静压模压成型该预制中空板坯100Y时一体模压成型于该预制中空板坯100Y上;所述过滤板本体100上粘接安装有封闭该抽芯口 110的密封条140,该密封条140由不锈钢制成,过滤板本体100上顶边部160的中心处设有出口 190,该出口 190与抽芯口 110、加强筋120 —并在模压成型预制中空板坯100Y时一体模压成型于预制中空板坯100Y上;过滤板上方圆孤的半径R为490毫米,过滤板高度A设为266毫米,宽度B为250毫米,底部两个安装孔中心距离C为98毫米,厚度设为24毫米,扇形左右两侧边部170的倾角设为30°。具体安装时,将上述多块烧结多孔材料过滤板拼装成360°的带状圆盘,这些圆盘都垂直均布且安装在主机水平转轴上。工作时圆盘在转动中不断经过下方的料槽,使浆料在过滤板上不断地形成滤饼,并由刮刀刮下,滤出的水进入过滤板内腔,并通过出口190不断地排出。
[0039]上述烧结多孔材料过滤板的制造方法为:将粉末料填入上述的等静压成型模具内,并机械振实,使粉末料充分、均匀填充至模具型腔中,然后将组装好的等静压成型模具放入等静压成型机内压制成型;从模具中取出并获得一预制中空板坯100Y;将预制中空板坯100Y放入上述专用烧结装置,然后将专用烧结装置放入烧结炉内进行烧结,冷却后得到过滤板本体100,然后在过滤板本体100上机械加工出安装孔(两个安装孔中心距离C为98毫米),随后在该过滤板本体100上粘接安装用于封闭抽芯口 110的密封条140。
制备烧结多孔材料过滤板的等静压成型模具及方法
- 专利详情
- 全文pdf
- 权力要求
- 说明书
- 法律状态
查看更多专利详情
下载专利文献
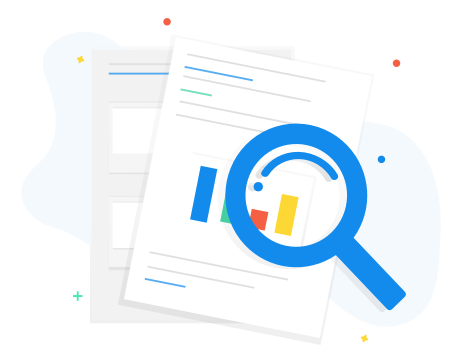
下载专利
同类推荐
-
孙守旗孙守旗孙棠丽陈海标, 潘锋
您可能感兴趣的专利
-
陈海标, 潘锋熊刚P·卢瑟陈海标, 潘锋
专利相关信息
-
杨志峰刘建龙J·D·赫尔芬斯蒂尼, W·R·鲍威尔J·D·赫尔芬斯蒂尼, W·R·鲍威尔