专利名称:单层阵列玻璃基板的切割方法及切割系统的制作方法目前,对于显示装置用玻璃基板的切割领域来说,最常见的是对双层玻璃基板的切割工艺,例如IXD基板;通常对于双层玻璃基板来说主要通过切割机采用悬置切割模式进行切割;由于双层玻璃板可以将其内部安装的各类元件进行有效的保护,因此可以有效避免双轮切割装置切割时所产生的飞溅的玻璃颗粒划伤内部元件;而且在传送台上通过卡盘夹取时,其位于上层的玻璃基板可以有效避免卡盘对内部元件产生物理损害。而如果采用悬置切割模式对单层阵列玻璃基板进行切割,例如TOUCH或OLED基板;显然不适用,会导致成品良率低下;其主要原因是:单层阵列玻璃基板的阵列单元是设于玻璃基板之上的,也就是说当双轮切割装置进行相向对点切割时,很容易导致飞溅的玻璃颗粒划伤阵列单元的·情况发生;而且,如果不对现有双轮切割装置的切割轮之间的轮距进行调整,会很容易导致因双轮加持不利的现象发生,具体的说是,只有上方的切割轮进行切割,而下方的切割轮因距离远而接触不到玻璃基板,这样不能对玻璃基板形成对点的相向切割,这会导致玻璃基板的切口不齐,甚至破损;从而增加单层阵列玻璃基板的坏品率。而且在传送台上通过卡盘夹取时,单层阵列玻璃基板由于对阵列单元进行遮盖保护,因此,显而易见卡盘很容易对其产生物理损害。基于上述原因,现有的对于单层阵列玻璃基板的切割工艺多采用非悬置切割模式,该种模式虽然可通过单切割轮对玻璃基板进行切割,避免了玻璃基板切口破损的问题,但是在单轮切割装置切割时,同样会产生飞溅的玻璃颗粒,从而对阵列单元产生划伤;同时,也无法避免卡盘在夹取时对阵列单元所产生的伤害。针对以上不足,本发明急需提供一种新的单层阵列玻璃基板的切割方法及切割系统。
本发明的目的是提供一种单层阵列玻璃基板的切割方法及切割系统,该方法利用模拟玻璃基材与单层阵列玻璃基材对合安装用以模拟双层玻璃基板切割工艺并以此实现提高单层阵列玻璃基板切割质量的目的。本发明的目的是通过以下技术方案实现的:一种单层阵列玻璃基板的切割方法,该方法包括:将经过阵列工艺后的单层阵列玻璃基材与提供的模拟玻璃基材通过对合工艺组装成双玻璃模拟基材;将双玻璃模拟基材送入切割机进行切割工序,形成双玻璃模拟基板;对双玻璃模拟基板进行分离工序,得到单层阵列玻璃基板。上述的方法,其中,所述通过对合工艺组装成双玻璃模拟基板包括:在所述单层阵列玻璃基材上涂布密封剂;将所述模拟玻璃基材与所述单层阵列玻璃基材对合安装,形成未固化状态的双玻璃模拟基材;将所述未固化状态的双玻璃模拟基材送入UV固化机进行半固化照射,形成所述双玻璃模拟基材。进一步地,上述的方法,在形成双玻璃模拟基板后,还包括对双玻璃模拟基板进行打磨工序的步骤。进一步地,上述的方法,还包括对打磨后的双玻璃模拟基板进行清洗工序的步骤。进一步地,上述的方法,还包括对分离后的单层阵列玻璃基板进行密封剂清除的步骤。进一步地,上述的方法,还包括在所述模拟玻璃基材上预先布设UVmask膜的步骤。 一种实现如上述中任一所述单层阵列玻璃基板的切割方法的切割系统,该系统包括对合机,用于将经过阵列工艺后的单层阵列玻璃基材与提供的模拟玻璃基材组装成双玻璃模拟基材;切割机,用于将双玻璃模拟基材切割成双玻璃模拟基板;基板分离机,用于对双玻璃模拟基板进行分离。上述的系统,其中,所述对合机包括涂胶装置,用于在单层阵列玻璃基材上涂布密封剂;翻转对合装置,用于将模拟玻璃基材与单层阵列玻璃基材对合安装;uv固化机,用于对未固化状态的双玻璃模拟基材进行半固化照射。进一步地,上述的系统中,还包括打磨抛光机,用于对双玻璃模拟基板进行打磨工序。进一步地,上述的系统中,还包括基板清洗机,用于对打磨后的双玻璃模拟基板进行清洗。本发明与现有技术相比具有以下的优点:1、本发明采用在单层阵列玻璃基材上安装所述模拟玻璃基材的方法,以模拟双层玻璃基板的切割工艺;通过模拟玻璃基材对阵列单元进行保护,既可有效避免在悬置切割模式或非悬置切割模式中因玻璃飞溅对阵列单元所产生的划伤,又可解决在悬置切割模式时双轮间距与单层阵列玻璃基材厚度之间的适应性的问题,节省了调整轮距的工序;而且还可以有效避免卡盘夹取时对阵列单元产生物理损害;提高了切割质量,保证了成品质量,降低了坏品率。2、本实施例中采用点状喷涂密封剂的技术,可为分离工序提供有力保障,由于模拟玻璃基板和单层阵列玻璃基板之间通过密封胶呈多点连接,因此可轻易地将模拟玻璃基板和单层阵列玻璃基板分离;同时减小了分离后对密封剂进行清除的难度。3、本发明采用通过UV固化机对双玻璃模拟基材进行半固化照射的方法,可使封框胶的胶体固化到半凝结状态,此时的双玻璃模拟基材其上端的模拟玻璃基材与下端的单层阵列玻璃基材之间的连接相对稳固,但使两者不完全固定,两者之间的连接稳固度可使双玻璃模拟基材能够承受切割力的程度;以便为双玻璃模拟基材的分离工序提供相对便利的条件,使双玻璃模拟基材的模拟玻璃基材与单层阵列玻璃基材的分离相对更加容易,不会因粘连过牢无法分离而影响单层阵列玻璃基板的成产进度;加快了分离工序的进度。4、本发明中采用打磨抛光机对双玻璃模拟基板进行抛光打磨的步骤,利用软毛刷件对双玻璃模拟基板特别是其边沿切口处进行抛光打磨作业,使其更加光滑,采用经抛光打磨后的双玻璃模拟基板有效提高了基板切割工艺质量,提高了产品品质。5、本发明中所述UVmask膜按阵列单元的设计位置进行分布;采用预先安装UVmask膜的步骤,可简化切割工艺,使未固化的双玻璃模拟基材可快速直接的送入UV固化机进行密封剂的半固化工序;加快了进度,提高了生产效率。以下结合附图和实施例对本发明作进一步说明。
图1是本发明的切割方法的流程框图。;图2是本发明中双玻璃模拟基板的结构示意图(剖视图)。
通过基板清洗机对打磨后的双玻璃模拟基板进行清洗工序。本实施例中所述的基板清洗机可采用常规的LCD玻璃基板清洗机,属于现有技术故对其具体结果此处不再进行介绍。4、通过基板分离机对双玻璃模拟基板进行分离工序,得到单层阵列玻璃基板。参见图2所示,本实施例中所述双玻璃模拟基板包括上层的模拟玻璃基板101、下层的单层阵列玻璃基板102,在该单层阵列玻璃基上设有阵列单元103,所述模拟玻璃基板与单层阵列玻璃基板通过涂布在两者之间的密封剂104连接;从而将阵列单元很好地保护在双玻璃模拟基板内。采用基板分离机进行分离,由于此时的密封剂处于半固化状态,因此很轻易的就能将模拟玻璃基板摘下,以得到单层阵列玻璃基板。对分离后的单层阵列玻璃基板进行密封剂清除。本实施例中可利用化学试剂(例如酒精)对密封剂进行清除,以使单层阵列玻璃基板更加清晰,保证了产品质量。同时,对分离后的模拟玻璃基板进行密封剂清除。可利用化学试剂对密封剂进行清除,以使单层阵列玻璃基板更加清晰,为再循环使用提供了保障。在所述模拟玻璃基材上预先布设UVmask膜。本实施例中所述UVmask膜按阵列单元的设计位置进行分布;采用预先安装UVmask膜的步骤,可简化切割工艺,使未固化的双玻璃模拟基材可快速直接的送入UV固化机进行密封剂的半固化工序;加快了进度,提高了
生产效率。为实现上述中所述单层阵列玻璃基板的切割方法;本发明特提供了一种单层阵列玻璃基板的切割系统,该系统包括对合机,用于将经过阵列工艺后的单层阵列玻璃基材与一块模拟玻璃基材组装成双玻璃模拟基材;切割机,用于将双玻璃模拟基材切割成双玻璃模拟基板;基板分离机,用于对双玻璃模拟基板进行分离;所述对合机通过传送带、切割机和基板分离机之间分别通过传送带连接。本实施例中所述的切割机可采用悬置式切割机或非悬置式切割机,用于对双玻璃模拟基材进行悬置切割或非悬置切割。本实施例中所述 对合机包括涂胶装置,用于在单层阵列玻璃基材上涂布密封剂;翻转对合装置,用于将模拟玻璃基材与单层阵列玻璃基材对合安装;uv固化机,用于对未固化状态的双玻璃模拟基材进行半固化照射;所述涂胶装置、翻转对合装置和UV固化机之间分别通过传送带连接。本实施例中的切割系统还包括打磨抛光机,用于对双玻璃模拟基板进行打磨工序;所述打磨抛光机通过传送带与所述UV固化机连接。本实施例中的切割系统还包括基板清洗机,用于对打磨后的双玻璃模拟基板进行清洗;所述基板清洗机两端分别通过传送带与所述打磨抛光机和基板分离机连接。本发明中所述的对合机、切割机、UV固化机、打磨抛光机、基板清洗机和基板分离机的结构均属于现有技术,此处不再过多赘述。
本发明涉及显示技术领域,尤其涉及一种利用模拟玻璃基材与单层阵列玻璃基材对合安装实现模拟双层玻璃基板切割工艺的单层阵列玻璃基板切割方法及切割系统;该方法包括将经过阵列工艺后的单层阵列玻璃基材与提供的模拟玻璃基材通过对合工艺组装成双玻璃模拟基材;将双玻璃模拟基材送入切割机进行切割工序,形成双玻璃模拟基板;对双玻璃模拟基板进行分离工序,得到单层阵列玻璃基板。本发明采用在单层阵列玻璃基材上安装所述模拟玻璃基材的方法,通过模拟玻璃基材对阵列单元进行保护,避免在悬置切割模式或非悬置切割模式中因玻璃飞溅对阵列单元所产生的划伤,解决在悬置切割模式时双轮间距与单层阵列玻璃基材厚度之间适应性问题。
单层阵列玻璃基板的切割方法及切割系统制作方法
- 专利详情
- 全文pdf
- 权力要求
- 说明书
- 法律状态
查看更多专利详情
下载专利文献
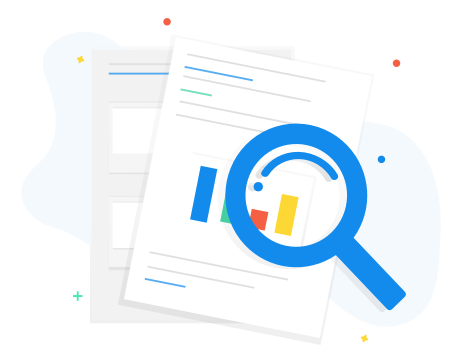
下载专利
同类推荐
-
岸本正一高伯菘, 王坤池王坤池, 王清华龙峰孟凡强
您可能感兴趣的专利
-
孟凡强中西正直, 金子静则方晨航苅谷浩幸, 前田伸广苅谷浩幸, 前田伸广苅谷浩幸, 前田伸广吕文慧, 尹计深
专利相关信息
-
吕文慧, 尹计深吕文慧, 尹计深芳谷光明芳谷光明德本诚治万文, 万黎明肖湘东