一种钢骨混凝土梁及其施工方法[0002]近年来钢骨混凝土结构有了广泛的应用,施工工艺也日益成熟,但施工中通常会出现单肢箍筋(也称拉筋或勾筋)需要穿过钢骨腹板的情况,对于单肢箍筋穿过钢骨腹板,常采用以下两种设置方式:(I)在钢骨腹板上预留孔洞,单肢箍筋从预留的孔洞中穿过,如附图1-2所示;(2)单肢箍筋焊接在钢骨腹板或搭筋板上。对于上述设置方式一,由于单肢箍筋在与纵筋连接时,单肢箍筋两端通常需要弯曲180°以便勾住纵筋,若事先将单肢箍筋一端弯成180°勾住一侧纵筋、另一端穿过腹板预留孔洞后再现场手工弯曲180°勾住另一侧纵筋,存在弯曲速度慢、尺寸不宜到位等问题;若在安装之前,事先将单肢箍两头均弯曲180°,则决定了预留在钢骨腹板上的孔径必然较大,削弱了钢骨截面尺寸,对结构受力必然会产生不良影响,设计不允许。对于上述设置方式二,单肢箍筋与钢骨腹板或与搭筋板焊接,焊接量会急剧增加,也必然会造成施工缓慢、影响工期、同时也不利于节约成本,且因施工空间狭窄,无法保证焊接质量。
[0003]为克服现有技术中存在的上述缺点,本发明的目的之一是提供一种新型的钢骨混凝土梁,该钢骨混凝土梁内的单肢箍筋设置方便;本发明的目的之二是提供一种钢骨混凝土梁的施工方法。 [0004]为达到上述目的一,本发明采用了以下技术方案: 一种钢骨混凝土梁,包括钢骨、纵向钢筋,闭合箍筋、混凝土以及拉结钢骨两侧纵向钢筋的单肢箍筋,其特征在于:在所述钢骨的腹板两侧对称焊接有若干块钢板,所述钢板水平布置并与钢骨的腹板垂直,钢板上设置有孔洞,单肢箍筋一端与纵向钢筋连接,另一端直接勾住钢板上的孔洞。[0005]所述单肢箍筋与纵向钢筋连接的一端弯曲180°勾住纵向钢筋,单肢箍筋与钢板连接的一端弯曲90°,弯曲段插入所述孔洞中。[0006]所述孔洞的直径与所述单肢箍筋的直径相适应,所述孔洞直径比所述单肢箍筋的直径大2mm~4 mm。[0007]所述单肢箍筋呈梅花型布置,竖向间距为135mm~150mm,水平间距为400mm,相邻钢板之间的竖向间距与单肢箍筋的竖向间距一致。[0008]为达到上述目的二,本发明采用了以下技术方案:
一种钢骨混凝土梁的施工方法,其特征在于包括以下步骤:
(1)按设计尺寸加工钢骨;
(2)按设计尺寸加工钢板,并在钢板上设置孔洞;
(3)按设计位置,将钢板对称焊接于钢骨腹板的两侧,钢板水平布置并与钢骨腹板垂 直;
(4)钢骨吊装就位;
(5)绑扎纵向钢筋及闭合箍筋;
(6)安装单肢箍筋,所述单肢箍筋的一端弯曲180°勾住纵向钢筋,另一端弯曲90°插入孔洞中;
(7)浇筑混凝土并养护。
[0009]所述孔洞的直径与所述单肢箍筋的直径相适应,所述孔洞直径比所述单肢箍筋的直径大2mm?4 mm。
[0010]所述单肢箍筋呈梅花型布置,竖向间距为135mm?150mm,水平间距为400mm,相邻钢板之间的竖向间距与单肢箍筋的竖向间距一致。
[0011 ] 所述步骤(1)-(3)在工厂进行。
[0012]所述步骤(6)中的单肢箍筋事先已加工弯曲完毕。
[0013]本发明的有益效果:通过在钢骨腹板上焊接设有预留孔洞的钢板,单肢箍筋安装时能够直接勾在钢板上的预留孔洞之中,包括单肢箍筋的弯曲在内的大部分工作能够在工厂事先完成,现场手工操作任务大大减少,既能保证施工质量也能缩短工期;且在钢骨腹板上焊接钢板,一方面避免了在腹板上开孔对钢骨截面造成削弱,另一方面还能增加钢骨与混凝土的锚固性能。
[0014]图1是现有技术钢骨混凝土梁中的单肢箍筋设置方式。
[0015]图2是图1中钢骨的侧视图。
[0016]图3是本发明的钢骨混凝土梁断面图。
[0017]图4是图3中a-a断面中的钢骨视图。
[0018]图5是图3中局部A的大样图。
[0019]图中,1、钢骨;2、纵向钢筋;3、闭合箍筋;4、混凝土 ;5、单肢箍筋;6、钢板;7、孔洞;11、翼板;12、腹板。
[0020]下面对本实施例结合附图加以详细描述,但本发明的保护范围不受实施例所限。
[0021]如图3-5所示,本发明的钢骨混凝土梁,包括钢骨1、纵向钢筋2,闭合箍筋3、混凝土 4以及拉结钢骨I两侧纵向钢筋2的单肢箍筋5,其特征在于:在所述钢骨I的腹板两侧对称焊接有若干块钢板6,所述钢板6水平布置并与钢骨I的腹板垂直,钢板6上设置有孔洞7,单肢箍筋5 —端与纵向钢筋2连接,另一端直接勾住钢板6上的孔洞7。
[0022]所述单肢箍筋5与纵向钢筋2连接的一端弯曲180°勾住纵向钢筋2并绑扎,单肢箍筋5与钢板6连接的一端弯曲90°,弯曲段插入所述孔洞7中。
[0023]所述孔洞7的直径与所述单肢箍筋5的直径相适应,所述孔洞7的直径比所述单肢箍筋5的直径大4mm。
[0024]所述单肢箍筋5呈梅花型布置,竖向间距为135mm?150mm,水平间距为400mm,相邻钢板6之间的竖向间距与单肢箍筋5的竖向间距一致。[0025]所述纵向钢筋2直径为28mm、闭合3箍筋直径为16mm钢,闭合箍筋3间距IOOmm每道由内而外设置三层,单肢箍筋5直径8_。
[0026]所述钢板6宽度为40mm、厚度为10mm。
[0027]本发明钢骨混凝土梁的施工方法,包括以下步骤:
(1)按设计尺寸加工钢骨I;
(2)按设计尺寸加工钢板6,并在钢板6上设置孔洞7;
(3)按设计位置,将钢板6对称焊接于钢骨I腹板12的两侧,钢板6水平布置并与钢骨I腹板垂直;
(4)钢骨吊装就位;
(5)绑扎纵向钢筋2及闭合箍筋3;
(6)安装单肢箍筋5,所述单肢箍筋5的一端弯曲180°勾住纵向钢筋2并绑扎,另一端弯曲90°插入孔洞7中;
(7)浇筑混凝土4并养护。
[0028]所述孔洞7的直径与所述单肢箍筋5的直径相适应,所述孔洞7的直径比所述单肢箍筋5的直径大4mm。
[0029]所述单肢箍筋呈梅花型布置,竖向间距为135mm?150mm,水平间距为400mm,相邻钢板6之间的竖向间距与单肢箍筋5的竖向间距一致。
[0030]所述步骤(1)-(3)在工厂进行。
[0031]所述步骤(6)中的单肢箍筋5事先已加工弯曲完毕。
一种钢骨混凝土梁及其施工方法
- 专利详情
- 全文pdf
- 权力要求
- 说明书
- 法律状态
查看更多专利详情
下载专利文献
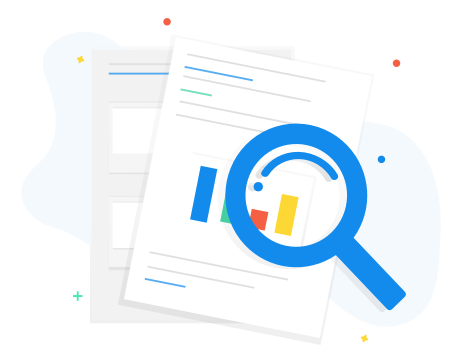
下载专利
同类推荐
-
于吉涛朱绍杰, 吕丛丛张鹏飞
您可能感兴趣的专利
-
朱绍杰, 吕丛丛
专利相关信息
-
肖燎宋运来杨海涛