用于等离子体加工装置的脆性部件的延性模式钻孔方法[0002]在半导体材料加工领域中,例如,使用包括真空加工腔室在内的半导体材料加工装置执行不同的工艺,诸如在衬底上进行蚀刻和使不同的材料沉积在衬底上以及抗蚀剂剥离。随着半导体技术不断发展,晶体管大小不断缩减,这就需要在晶片处理和工艺设备方面有越来越高的准确度、可重复性以及清洁度。存在不同类型的用于半导体加工的设备,所述半导体加工包括牵涉到使用等离子体的应用,诸如等离子体蚀刻、反应性离子蚀刻、等离子体增强化学气相沉积(PECVD)以及抗蚀剂剥离。这些工艺所需类型的设备包括被设置在等离子体腔室内并且必须在该环境中运行的部件。等离子体腔室内部的环境可以包括暴露于等离子体、暴露于蚀刻剂气体以及热循环。用于这些部件的材料必须适合于承受所述腔室内的环境条件,并且也必须适合于对许多晶片进行加工,所述加工可以包括每块晶片的多个工艺步骤。为了有成本效益,这些部件必须经常要承受数百或数千次晶片循环,同时仍保持它们的功能性和清洁度。对于会产生颗粒的部件的容忍度一般极低,即使当这些颗粒很少并且不大于几十纳米时也是如此。还需要被选用于等离子体加工腔室内以通过最有成本效益的方式来满足这些要求的部件。[0003]为了实现这个目的,对形成例如喷头电极的脆性(brittle)部件进行机械加工操作,诸如进行钻孔,以便形成穿过喷头电极的工艺气体输送孔。然而,在脆性部件中进行钻孔可能会在脆性部件的表面中产生小的几乎看不见的微裂纹。这些微裂纹或亚表面损伤会因脆性材料断裂而造成颗粒污染。
[0004]本文公开了一种使用切割工具在等离子体加工装置的部件中进行延性模式钻孔的方法,其中所述部件由非金属的硬而脆性(hard and brittle)材料制成。所述方法包括通过在钻孔同时控制切割深度以在所述部件中钻出每个孔,从而使得一部分脆性材料经历高压相变并在切屑形成期间形成脆性材料的无定形部分。然后,从每个孔去除脆性材料的无定形部分,从而使得在所述部件中形成的每个孔的孔壁具有约0.2 μ m至0.8 μ m的因钻孔所致的表面粗糙度(Ra)。
[0005]图1图示了半导体等离子体加工装置的喷头电极组件的一个实施方式。
[0006]图2图示了半导体等离子体加工装置的一个替代性实施方式。
[0007]图3A、3B图示了可以包括根据本文所公开的延性模式钻孔法所形成的孔的电介质窗和气体喷射器。[0008]图4图示了由非金属的硬而脆性材料制成的部件的亚表面损伤模型。
[0009]图5图示了将切割深度与单晶硅喷头电极中延性模式钻出的孔的孔壁的损伤深度相比较的图表。
[0010]本文公开了一种在等离子体加工装置的部件中进行延性模式钻孔的方法,其中所述部件由非金属的硬而脆性材料制成并且所述部件包括诸如气体喷射孔之类的孔。如本文所用,硬而脆性材料意指适于用作半导体加工腔室中的部件的陶瓷材料、含硅(含单晶硅或多晶硅)材料或石英材料,并且更确切地说,意指包括石英、硅、碳化硅、氮化硅、氧化铝、氮化铝、碳化硼、氧化钇、氧化锆、金刚石等在内的材料。在正常条件下,半导体和陶瓷材料是硬而脆的,并且不容易发生塑性变形。用于等离子体加工装置中的合适部件由诸如硅和碳化硅之类的陶瓷材料和石英材料形成,并且可以包括喷头电极、气体分配构件以及气体喷射器。
[0011]为了实现使这些硬而脆性材料发生塑性变形(即延性模式),优选地使所述部件的一部分表面经历高压相变。延性模式钻孔可以利用通过对切割深度、进刀速率、啄孔距离、钻速以及施加于一部分部件上的压力进行控制而引起的小尺寸范围的延性塑性响应,使得所述部件的一部分硬而脆性材料的一部分经历高压相变,以形成脆性材料的无定形部分,从而可以将脆性材料中发生塑性变形(无定形)的部分去除。将脆性材料中发生塑性变形的部分去除会形成部件中的每个孔,其中所述部件优选地包括用于将工艺气体输送到等离子体加工装置的加工区域中的多个孔。
[0012]优选地,所述部件的每个孔的孔壁因钻孔所致的表面粗糙度具有约0.2μπι至0.8 μ m的粗糙度,并且更优选地,每个孔的孔壁因钻孔所致的表面粗糙度在约0.4 μ m与
0.6μπι之间。如本文所用,术语“约”是指±10%。如本文所用,术语“表面粗糙度”被表示为表面粗糙度测量结果的算术平均值(Ra)。优选地,在等离子体加工装置的部件中进行延性模式钻孔的方法的实施方式将使亚表面损伤减到最低程度,即在钻孔后呈微裂纹形式的亚表面损伤将减少,并且微裂纹向脆性部件中将优选地延伸不到约20 μ m,更优选地不到约10 μ m,并且最优选地不到约5 μ m。理想的是,在钻孔后表面几乎完全没有裂痕。
[0013]图1描绘了平行板电容耦合型等离子体腔室(真空腔室)的喷头组件100的一半,所述喷头组件100包括:顶部电极103,该顶部电极103由非金属的硬而脆性材料形成并且当中包括用于输送工艺气体的气体通过孔104,以及被固定到顶部电极103上的任选的背衬构件102,热控制板101和顶板111。任选的背衬构件102可以由非金属的硬而脆性材料形成,其中任选的背衬构件102具有气体通过孔113,这些气体通过孔113与顶部电极中的用于输送工艺气体穿过该顶部电极的孔104相对准。在热控制板101的上表面上可以提供热扼流器112。顶部电极103被定位于衬底支撑件160上方,该衬底支撑件160对半导体衬底162 (例如半导体衬底)进行支撑。
[0014]顶板111可以形成诸如等离子体蚀刻腔室之类的等离子体加工装置的可移除顶壁。如所示,顶部电极103可以包括内部电极构件105和任选的外部电极构件107。内部电极构件105通常由单晶硅制成。必要时,内部电极105和外部电极107可以由单块的材料制成,该材料诸如CVD碳化硅、单晶硅或其它合适的材料。[0015]单晶硅是用于内部电极构件105和外部电极构件107的等离子体暴露表面的优选材料。高纯度的单晶硅能够使得在等离子体加工期间对于衬底的污染减到最少,这是因为它仅将极少量的不希望有的元素引入到反应腔室中,并且在等离子体加工期间还能够使磨损平缓,从而使颗粒减到最少。
[0016]喷头电极组件100当中包括用于输送工艺气体的孔,并且可以经过大小调整以用于加工大型衬底,诸如直径为300mm的半导体晶片。对于300mm晶片,顶部电极103的直径为至少300_。然而,喷头电极组件可以经过大小调整以加工其它规格晶片或具有非圆形构造的衬底。
[0017]图2是等离子体加工腔室10的一个替代性实施方式的剖视图,其中所述等离子体加工腔室10是电感耦合型。ICP等离子体加工腔室的一个示例是由加利福尼亚州弗里蒙特(Fremont, California)的 Lam Research Corporation 制造的丁CPk 烛刻或沉积系统。ICP等离子体加工腔室还描述于例如共同转让的美国专利N0.6,805,952中,该美国专利以引用的方式整体并入本文。加工腔室10包括具有支撑表面14的衬底支撑件12。支撑表面14被适配成支撑衬底16。真空泵18与排出口 20相连接以将加工腔室10内部维持在低压(例如约I毫托与约50毫托之间)。气体源22经由气体分配构件、喷头装置或气体喷射器中所包括的工艺气体孔向加工腔室10内部供应工艺气体,其中该气体分配构件、该喷头装置或该气体喷射器由非金属的硬而脆性材料形成。举例来说,可以经由气体分配构件24中的孔(未示出)向靠近衬底16的区域中引入工艺气体。
[0018]电介质窗32位于平面天线26下方并且形成等离子体加工腔室10的顶壁。气体分配构件24被放置在电介质窗32下方。在气体分配构件24与衬底16之间的区域中产生高密度的等离子体31,以用于对衬底16进行沉积或蚀刻。优选地,电介质窗32由诸如石英、氧化铝、氮化铝或氮化硅之类的硬而脆性材料形成。在一个替代性实施方式中,电介质窗32具有穿过其延伸的贯穿通道,其中可以插入气体喷射器并且向靠近衬底16的区域中提供工艺气体。
[0019]图3A示出了示例性电介质窗32,其包括平行平面表面42、侧面44以及被配置成支撑气体喷射器50的贯穿通道46。电介质窗可以由石英制成,其中可以对石英进行精加工处理。用于电介质窗的示例性精加工处理可以见于共同转让的美国专利N0.7,250,114中,该美国专利特此以引用的方式整体并入本文。替代地,电介质窗可以由陶瓷材料形成。优选地,气体喷射器50延伸贯穿整个贯穿通道46。如图3B的剖视图中所示,气体喷射器50包括在上端具有凸缘43的圆柱体40、延伸穿过上部轴向端的中心孔45、在该孔与下部轴向端的外表面之间延伸的多个气体孔47、以及O型环形槽48、51。气体喷射器可以由诸如陶瓷或石英材料之类的电介质材料制成,其中气体喷射器50包括用于穿过它输送工艺气体的孔47。气体喷射器的示例公开于以引用的方式并入本文的美国专利N0.8,025,731和7,785,417 中。
[0020]等离子体加工装置中的诸如喷头组件100中的碳化硅背衬构件102和硅顶部电极103 (参见图1)、被放置在电介质窗32下方的气体分配构件24 (参见图2)以及电介质窗32的气体喷射器50 (参见图3A和图3B)等硬而脆性部件当中优选地包括气体通过孔。顶部电极103中的气体通过孔104、碳化硅背衬构件102中的气体通过孔113以及气体喷射器50中的气体通过孔47可以根据本文所公开的延性模式钻孔方法来形成。另外,气体分配构件24 (参见图2)中的气体通过孔(未示出)可以根据本文所公开的延性模式钻孔方法而形成。优选地,该部件中的孔具有约0.2mm至15mm的直径,并且更优选地,约0.2mm至0.7mm的直径,诸如约0.64mm、约0.5mm或约0.43mm的直径。
[0021]本文所公开的延性模式钻孔方法可以用于在等离子体加工装置的任何部件上形成孔或洞,其中该部件由非金属的硬而脆性材料制成。所述方法包括通过控制切割深度以在所述部件中进行钻孔,从而使得一部分脆性材料经历高压相变而在切屑形成期间形成脆性材料的无定形部分。该方法还包括将脆性材料中发生塑性变形的部分去除以在该部件中形成孔。优选地,每个孔的孔壁因钻孔所致的表面粗糙度具有约0.2 μ m至0.8 μ m的表面粗糙度,并且更优选地,每个孔的孔壁因钻孔所致的表面粗糙度在约0.4 μ m与0.6 μ m之间。优选地,由非金属的硬而脆性材料制成的部件中延性模式钻出的孔在形成时将具有向该部件的表面中延伸不到约20 μ m,并且更优选地延伸不到约10 μ m,并且最优选地延伸不到约5 μ m的亚表面损伤。
[0022]优选地,在延性模式钻孔处理期间,使非金属的硬而脆性材料在钻孔期间经历高压相变以便减少该材料在钻孔期间的脆性断裂。在极高的压力下,诸如在钻头与部件材料之间的接触界面处存在的极高的压力下,半导体、石英以及陶瓷材料会从共价键和/或离子键键合的结构转变成经过高压相变的金属结构。举例来说,已发现,与在常压或低压条件下硅的结构相比较,在本文所公开的延性模式钻孔法中所存在的高压相变会使硅转化成β-Sn晶体结构。所提供的能够形成经过高压相变的材料的压力应当足够大以克服该材料的硬度。优选地,使用诸如金刚石钻头之类的切割工具来进行延性模式钻孔。
[0023]图4图示了由非金属的硬而脆性材料(诸如硅)制成的部件200的亚表面损伤模型。如所示,部件200已经历高压相变,其中在主体层201上方形成弹性变形层202。在弹性变形层202上方是该部件中包含亚表面损伤的部分。亚表面损伤可以包括可能在所述部件200中形成结晶缺陷或不规则性的位错203以及会干扰结晶材料的堆垛层错序列的堆垛层错204。微裂纹205可能形成并且可能从部件200的上表面206延伸到弹性变形层202并且有可能穿过变形层202。优选地,在弹性变形层202上方亚表面损伤延伸不到约10 μ m并且更优选地不到约5 μ m。
[0024]优选地,进行延性模式钻孔以使得在非金属的硬而脆性材料中形成直径为约
0.2mm至15mm,诸如约0.64mm、约0.5mm或约0.43mm的孔。举例来说,为了减少直径为约
0.4mm至0.8mm的孔的亚表面损伤的深度,延性模式钻孔优选地以约20,000至60,000转/分钟的钻速进行,更优选地以约35,000至55,000转/分钟进行,并且最优选地以约40,000至50,000转/分钟进行。延性模式钻孔优选地具有约0.5至1.5英寸/分钟的进刀速率以及约0.001至0.004英寸的啄孔深度,其中切割深度小于约450纳米/转。切割深度大于450纳米/转可能会导致在脆性模式下进行钻孔,其中很可能出现亚表面损伤。更优选地,切割深度是约200至400纳米/转。另外,在延性模式钻孔期间,可以向钻孔位点供给去离子水以便减少污染。
[0025]优选地,在已钻出该部件的孔之后,可以使用诸如混合酸蚀刻溶液(MAE)之类的酸性溶液对该部件进行清洁。举例来说,用于对硅进行蚀刻的酸混合物可以由经过乙酸(CH3COOH或HC2H3O2X水或其它添加剂稀释的氢氟酸(HF)和硝酸(HNO3)构成。如从B.Schwartz 和 H.Robbins,的论文 Chemical Etching of Silicon, J.Electrochem.Soc.(“硅的化学蚀刻”,《电化学学会志》),第123卷,第12期(1976年12月),第1903-1909页(参见其中的图8和9)中所知,酸混合物的组成决定了蚀刻速率并且还决定了蚀刻表面的拓扑结构或在使用掩模进行蚀刻的情况下所产生的轮廓的图案。另外,用于清洁诸如喷头电极之类的硅电极的酸性溶液和方法的示例性实施方式还可以见于共同转让的美国专利N0.7,507, 670中,该美国专利特此以引用的方式整体并入本文。
[0026]图5图示了切割深度的影响,该切割深度是控制硅喷头电极中延性模式钻出的气体通过孔的损伤深度的另外一个因素。优选地,切割深度是约200纳米至450纳米/转以使亚表面损伤减到最少。切割深度大于450纳米/转可能会导致在脆性模式下进行钻孔,从而很可能出现亚表面损伤。更优选地,切割深度是约200纳米至400纳米/转以使亚表面损伤减到最少。切割深度小于约200纳米/转可能会导致偶然出现的亚表面损伤,从而会使得结果的可重复性较低。
[0027]在由非金属的硬而脆性材料制成的部件中进行延性模式钻孔期间,碎片可能会堆积于切割工具(钻头)上,从而导致扭矩更大,工具寿命缩短以及工艺的均一性降低。因此,在使用钻头钻出多于一个孔时,可能需要通过在钻孔操作之间间歇地将工具浸于超声波液中来对切割工具进行定期的超声波清洁。优选地,在钻出一定数目的孔之后,对切割工具进行超声波清洁,并且更优选地,在钻出每个孔之后对切割工具进行超声波清洁。虽然不希望受理论所束缚,但是在切割工具接触到超声波清洁液时,可以去除切割工具上所堆积的多达99%的碎片。此外,可以在对预定数目的部件进行延性模式钻孔之后对切割工具进行全面清洁。优选地,在对每个部件进行延性模式钻孔之后,对切割工具进行全面清洁。全面清洁过程包括取下钻头,使用苛性碱肥皂清洁钻头,以及将钻头复位。
[0028]本文还公开了一种更换等离子体加工装置包含的部件的方法。该方法包括在已用的部件受到腐蚀时从等离子体加工装置中取出已用的部件(诸如喷头电极);以及使用根据本文所公开的方法所形成的部件替换已用的部件。
[0029]另外,本文公开了一种在等离子体加工装置中对半导体衬底进行蚀刻的方法。该方法包括将根据本文所公开的方法的实施方式所形成的部件安装于等离子体加工装置的等离子体腔室中,以及在该等离子体腔室中对至少一个半导体衬底进行等离子体蚀刻。
[0030]本领域普通技术人员应了解,本发明可以在不脱离其精神或实质特征的情况下以其它具体形式来实施。本发明所公开的实施方式因此应在所有方面被认为具有说明性而不具限制性。本发明的范围是由所附权利要求书而不是上述描述指示的,并且属于权利要求书的等同方案的含义和范围内的所有变化意图被涵盖于本发明的范围中。
用于等离子体加工装置的脆性部件的延性模式钻孔方法
- 专利详情
- 全文pdf
- 权力要求
- 说明书
- 法律状态
查看更多专利详情
下载专利文献
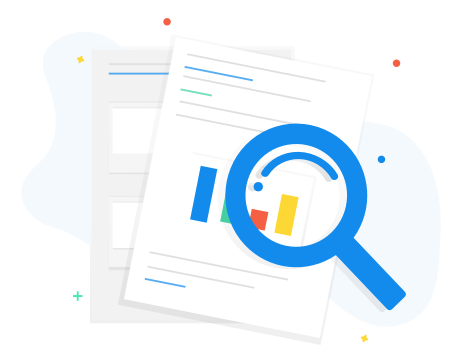
下载专利
同类推荐
-
利华·李·黄利华·李·黄吉田雅也徐红萍, 邓建清K-J·胡贝尔-哈格, I·比罗-弗朗斯
您可能感兴趣的专利
-
A·弗罗里普A·弗罗里普杉田守男陶武刚, 陈健杉田守男杉田守男
专利相关信息
-
刘晓强吴艳华吴艳华, 王旭宁吴艳华, 王旭宁朴淳五李小成, 周超李小成, 周超