专利名称:一种超细纤维聚氨酯合成革及其基布,及制备方法和应用的制作方法超细纤维聚氨酯合成革是近年发展起来的一种新型高档的人造皮革,其由超细纤 维和聚氨酯两部分构成。其中,超细纤维三维交联在一起,起到骨架和支撑作用,形成类似 于真皮胶原纤维的结构,分布在纤维四周的是聚氨酯,它使整个合成革基布形成一个整体。超细纤维聚氨酯合成革通常由下述方法制得将超细纤维经机械加工成具有三维 立体网络的非织造布,之后浸渍具有开孔结构的聚氨酯浆料,再经一系列复杂工艺加工成 超细纤维聚氨酯合成革基布,最后经过转移涂层或者后整理方式得到超细纤维聚氨酯合成 革。与其他普通人造合成革相比,超细纤维聚氨酯合成革具有诸多优点。由于超细纤 维比表面积大,含有天然皮革胶原纤维相似的束状超细纤维,因而其具有很强的吸水性。其 透湿性亦与天然皮革相近。而且,超细纤维具有合适的伸长率、拉伸强度高,因此在舒适性 和物理化学性能方面都可以和天然皮革,甚至高级天然皮革相媲美。并且,其在霉变性、保 型性和质量轻便性方面更优于天然皮革,是天然皮革的优良替代品。但目前,关于对超细纤维聚氨酯合成革进行阻燃处理的研究报道很少。已有的阻 燃处理方法获得的产品阻燃性和其他物理化学性能较差,难以满足需要。例如,中国专利 02112718. 2采用喷涂后整理的方法对普通PU人造革进行阻燃处理。但采用该方法对超细 纤维合成革进行阻燃处理,将恶化超细纤维合成革的手感和物理化学性能。再如,中国专利 02801987. 3公开了一种皮革类片状基体,其由0. 5分特以下的超细纤维(A)三维络合形成 的非织造布与填充在其络合空间中的高分子弹性体(B)构成,超细纤维(A)由有机磷成分 共聚聚酯构成,高分子弹性体(B)含有金属氢氧化物或共聚有机磷成分。该专利在树脂中 接枝阻燃成分,并添加金属氢氧化物,但因接枝阻燃成分后,高分子树脂的性能下降较大, 同时金属氢氧化物添加量大,将恶化超细纤维合成革的手感和物理化学性能。该专利还提 到采用背面压层的方式进行阻燃处理,这使得合成革的背面和整个合成革的阻燃性能产生 差异,同时也恶化超细纤维合成革的手感。之所以很难制得阻燃性优异的超细纤维聚氨酯合成革,主要因为由于超细纤维本 身的特性,通常的阻燃剂很难对其进行阻燃处理。并且,超细纤维是由两个完全不同的可燃 性物质超细纤维和聚氨酯组成,大部分阻燃剂只针对某一种可燃性物质,很难兼顾两种完 全不同类型的可燃物质,因此现有的阻燃处理方法很难同时使超细纤维和聚氨酯都具有良 好的阻燃性能。此外,在进行阻燃处理时还需考虑不影响超细纤维革的其他性能。因此,对 超细纤维合成革进行阻燃处理,很难在不影响其他性能的前提下,获得理想的阻燃效果。汽车内饰是皮革和人造革的主要应用领域之一。但汽车内饰用革的测试标准相当 严格,需要所使用的革具有优异的综合性能,因此,汽车内饰用革的开发时间周期长。目前, 世界范围内的汽车内饰用革基本上以天然皮革和普通人造革为主。高档小汽车采用天然皮革作为汽车内饰用革,而中低档的小汽车则采用普通人造革,如普通PU人造革、PVC人造革 等。天然皮革的来源有限,而且随着各种需求的日益增加,用天然皮革作为汽车内饰的来源 必将日趋有限,致使价格节节攀升;而且在其加工过程中需采用特殊的化学助剂,造成环境 污染,且使用过程中具有特殊的气味。而普通人造革在物理化学性能方面和天然皮革具有 很大的差距,诸如撕裂强度、剥离强度、拉伸强度和缝目强度等。特别是PVC人造革,因在加 工过程中需添加增塑剂邻苯二甲酸二辛酯(DOP)、邻苯二甲酸二丁酯(DBP)、邻苯二甲酸二 异丁酯(DIBP)等,在高温高湿的情况下很容易挥发,对人体造成危害。超细纤维聚氨酯合成革具有普通人造皮革所不具有的诸多优异性能,且在其生产 加工过程中不使用违禁化学药品,加工过程环保,因而在其使用过程中没有化学药品的挥 发,几乎没有气味。若能将超细纤维聚氨酯合成革用于汽车内饰,具有广阔的应用前景。但 现有技术不能获得阻燃性较佳的超细纤维聚氨酯合成革,并且现有的超细纤维聚氨酯合成 革较难满足汽车内饰用革的其他性能要求。例如,汽车内饰用革的耐黄变级数基本要求在4级以上,而常规的聚氨酯树脂的 耐黄变级数在2级左右,通过添加耐黄变助剂后也一般只能达到3级左右。再例如,汽车内饰用革要求通过强光照射测试,而常规的聚氨酯树脂的软化点在 150°C左右,在强光照射测试过程中,很容易因聚氨酯树脂软化点过低而出现烧焦的现象。再例如,汽车内饰用革对不变色性有较高的要求。汽车内饰用革含有H2S等化学 药品的测试项,因此不能含有能和H2S等化学药品作用后而变色的颜料,如含有铅等金属离 子的颜料在遇到H2S后,会发生化学反应而变色。同时,汽车内饰有耐热80°C X500hr、耐 光110MJX200hr、耐湿热50°C 95% X500hr的测试,其变色必须彡4级。普通的红色和黄 色颜料,在如此苛刻的条件下,很难满足汽车内饰的要求。再例如,汽车内饰革要求圆盘耐磨和学振耐磨> 4级。聚氨酯树脂本身具有高耐 磨,及其他各项物理化学性能优越的特点,但在不添加助剂的情况下,圆盘耐磨CS-10能仅 能达到1 2级,学振耐磨仅能达到1 2级。由于上述尚未解决的技术问题,目前尚未有超细纤维聚氨酯合成革用于汽车内饰 的报道。因此,亟待寻求一种能满足汽车内饰用革要求的超细纤维聚氨酯合成革。
本发明所要解决的技术问题是为了克服现有技术很难获得阻燃性优异的超细纤 维聚氨酯合成革,以及尚没有可满足汽车内饰用革综合性能要求的超细纤维聚氨酯合成革 的缺陷,而提供一种超细纤维聚氨酯合成革基布的制备方法,和一种超细纤维聚氨酯合成 革的制备方法,以及上述方法所制得的产品及其应用。由本发明的方法制得的超细纤维聚 氨酯合成革具有优异的阻燃性能,能满足汽车内饰用革的综合性能要求。本发明的超细纤维聚氨酯合成革基布的制备方法包括如下步骤按常规工艺步骤 制备超细纤维聚氨酯合成革基布,其中,在纺丝步骤中,加入FR-535尼龙阻燃色母粒对超 细纤维丝进行阻燃处理。其中,所述的常规工艺步骤是指本领域现有的制备超细纤维聚氨酯合成革基布的 工艺步骤,具体可根据需要按本领域常识选择,通常包括如下的依次步骤超细纤维的纺 丝,制备非织造布,烫平非织造布,将非织造布浸渍于聚氨酯浆料中,凝固,之后依次进行减量开纤、扩幅干燥上油和鞣皮,即得超细纤维聚氨酯合成革基布。其中,所述的FR-535尼龙阻燃色母粒是日本大油墨化学公司的阻燃尼龙母粒产 品。本发明在超细纤维的纺丝步骤中,特别选择FR-535尼龙阻燃色母粒对超细纤维丝进行 阻燃处理,是因为本发明人在研发过程中发现在纺丝中添加其他类型或型号的阻燃剂进 行阻燃处理时,因超细纤维的纤度小,一般的阻燃剂很难进入超细纤维的“岛”相成分中,有 的会恶化纺丝性能,甚至根本无法得到阻燃性超细纤维复合丝。并且,其他阻燃剂在后续的 浸渍和减量开纤过程中,很容易被水或者溶剂所溶出,从而使超细纤维聚氨酯合成革基布 丧失阻燃性。经大量试验筛选,采用FR-535尼龙阻燃色母粒进行阻燃处理可得到性能优良 的阻燃复合丝,同时在后续加工过程中不因被水和溶剂所溶出而降低其阻燃性,从而保持 较佳的阻燃性能,并且对纺丝过程影响较少,可使纺丝的各项物理性能达到汽车内饰用超 细纤维丝的要求。所述的FR-535尼龙阻燃色母粒的用量较佳的为纺丝步骤中所用成纤高 聚物岛相成分原料的质量百分比5 25%。FR-535尼龙阻燃色母粒的添加可按照常规操 作,使其与超细纤维丝共混即可。较佳的,除在纺丝工艺步骤中对超细纤维进行阻燃处理外,本发明还在将由超细 纤维丝加工而成的非织造布浸渍于聚氨酯浆料的步骤中,加入满足下述条件的添加型阻燃 剂对聚氨酯进行阻燃处理120°C以下不分解,与聚氨酯相容,不溶于水,并且,不溶于碱和 极性有机溶剂或者不溶于有机溶剂。通过上述处理,可达到对超细纤维和聚氨酯都进行阻 燃处理的效果。其中,所述的添加型阻燃剂可选自现有的各种添加型阻燃剂,只要能满足上述性 质要求即可。所述的添加型阻燃剂是指应用方式为直接与材料混配即可的阻燃剂,主要包 括(1)卤素阻燃剂,例如十溴二苯醚、四溴双酚A、八溴醚、十溴二苯乙烷、四溴醚、溴 代聚苯乙烯和六溴环十二烷等,本发明优选十溴二苯醚、十溴二苯乙烷、四溴双酚A中的一 种或多种。(2)磷系阻燃剂,例如红磷、磷酸酯类、聚磷酸铵(APP)、氧化磷类和溴芳烃基磷酸 酯类,其中以红磷应用最为广泛,本发明优选红磷和/或聚合度> 100的APP,以降低在减量 开纤过程中的溶解损失。(3)氮系阻燃剂,例如氰尿酸三聚氰胺盐(MCA)和三聚氰胺等,本发明优选MCA0(4)铝镁系阻燃,例如氢氧化铝和氢氧化镁等。(5)阻燃协同剂,例如三氧化二锑和硼酸锌。通常,阻燃协同剂与其他阻燃剂配合 使用,阻燃剂与协效剂的用量比例较佳的为质量比1 2 1 5。本发明优选下述配比 的阻燃剂组合质量比1 2 1 5的十溴二苯醚和三氧化二锑,质量比1 2 1 5 的十溴二苯乙烷和三氧化二锑,或质量比1 2 1 5的APP和硼酸锌。本发明适用的阻燃剂可选择上述添加型阻燃剂中的一种,或多种的组合,如 1 0. 5 1 0. 5 1的红磷、氢氧化铝和氢氧化镁的阻燃剂组合。本发明对所用的添加型阻燃剂的要求之一为120°C以下不分解,较佳的为140 160°C以下不分解,更佳的为170°C以下不分解。若所用阻燃剂不满足上述耐高温要求,在制 备工艺过程中会分解流失,同时在汽车内饰的测试过程中导致雾化测试不合格。本发明对所用的添加型阻燃剂的要求之二为与聚氨酯相容。根据本领域常识,所述的相容是指与聚氨酯相混具有较好的分散性,不发生分层和絮凝等现象。在浸渍过程中, 若阻燃剂和聚氨酯树脂相容性较差,阻燃剂在聚氨酯树脂中很容易发生分层和絮凝等现 象,同时阻燃剂很容易附着在超细纤维合成革表面,恶化合成革的表观性能,使得阻燃效果 不理想。因此,本发明特别选择与聚氨酯相容的添加型阻燃剂。较佳的,为了进一步促进添 加型阻燃剂与聚氨酯相容,可先将阻燃剂与聚氨酯树脂、溶剂和分散剂混合,经研磨后制得 阻燃浆料。该阻燃剂浆料和聚氨酯的相容性优良,分散均勻,不出现分层和絮凝现象,使得 所制备的超细纤维聚氨酯合成革基布在横向和截面上都分布均勻。本发明对所用的添加型阻燃剂的要求之三为不溶于水,并且,不溶于碱和极性有 机溶剂(针对定岛纤维)或者不溶于有机溶剂(针对不定岛纤维),以避免在制备工艺过程 中阻燃剂被水,以及有机溶剂或碱溶出而丧失阻燃效果。针对采用不定岛纤维,采用有机溶 剂进行减量开纤的制备工艺,本发明特别优选下述阻燃剂中的一种或多种十溴二苯醚、十 溴二苯乙烷、六溴环十二烷、四溴双酚A、红磷、聚合度为100以上的APP、MAC、氢氧化铝和氢 氧化镁、三氧化二锑和硼酸锌。所述的添加型阻燃剂的用量可根据需要选择,较佳的为聚氨酯树脂质量的10 50%。所述的聚氨酯浆料中的除阻燃剂外各成分的配比可按本领域常识选择,较佳的质 量份数配比为100份聚氨酯树脂,10 50份阻燃剂、20 80份极性有机溶剂(如DMF)、 0. 2 2份有机硅表面活性剂(如道康宁化学的施10)、0. 1 1. 5份勻泡剂(如上海多森 化工有限公司的DS-Si),以及根据所需颜色选择用量的色浆。其中,所述的聚氨酯树脂可 采用现有的制备超细纤维合成革所用的聚氨酯树脂,优选上海华峰超纤材料股份有限公司 的JF-W-TL4100、JF-W-TL4085和JF-W-TL4030。为了获得较佳的手感和综合性能的超细纤 维聚氨酯合成革基布,本发明优选高弹性模量(12 15MPa)的聚氨酯树脂和低弹性模量 (3 8MPa)的聚氨酯树脂搭配的组合,更优选质量比为1 1 1 2的JF-W-TL4100 (约 12MPa)禾口 JF-W-TL4085(约 8MPa),1 0. 5 1 3 的 JF-W_TL4100(约 12MPa)和 JF-W-TL4030 (约3MPa)。所述的弹性模量为100%弹性模量,即伸长100%时应力与应变的 比例系数。其他试剂可选择本领域常规试剂。在浸渍的工艺步骤中,采用上述添加型阻燃剂对聚氨酯进行阻燃处理的具体操作 为将添加有上述添加型阻燃剂的聚氨酯浆料混合均勻后,将烫平的非织造布浸入其中。其 他工艺操作条件可采用本领域常规条件。除了上述在纺丝,或纺丝和浸渍的工艺步骤分别对超细纤维和聚氨酯进行阻燃处 理外,较佳的,本发明还通过后整理的方式,采用水溶性阻燃剂进行进一步的阻燃处理,以 获得更佳的阻燃效果。较佳的操作为采用含水溶性阻燃剂的水溶液对超细纤维合成革基布 进行浸轧(较佳的为二浸二轧),之后烘干即可。所述的含水溶性阻燃剂的水溶液中,水溶 性阻燃剂与水的质量比较佳的为1 1 1 6。水溶性阻燃剂的水溶液的PH较佳的为 6 8。所述的浸轧较佳的控制带液率为80 90% ;百分比为含浸后基布的增重与原始重 量的百分比值。所述的烘干的温度较佳的为80 150°C。通常,不含有活性基团的阻燃剂, 如通用织物阻燃剂FR-6004(长兴达化工有限公司),在80 150°C下烘干后,即可获得良 好的阻燃性,但通常具有不耐洗刷的缺点。含有活性基团的阻燃剂,如ATP(北京洁尔爽高 科技有限公司)和DOher-6503(东莞东莞市道尔化工有限公司有限公司),在80 150°C下烘干后,再经170 200°C高温烘燥处理,即可获得永久阻燃效果。因为在高温处理的过 程中,阻燃剂与纤维、阻燃剂相互之间可以进行交联反应,而固着在基布之中。本发明的一较佳实例中,采用水溶性阻燃剂与水的质量比为1 2 1 6的水 溶液,其中水溶性阻燃剂为ATP (北京洁尔爽高科技有限公司)和/或Doher-6503(东莞东 莞市道尔化工有限公司有限公司),采用NaOH或者氨水调该含水溶性阻燃剂的水溶液的pH 为6 8,将超细纤维合成革基布二浸二轧后控制带液率为80 90%,在80 130°C进行 预烘干,然后在170 200°C高温烘燥1 5分钟,即可获得具有永久阻燃效果的超细纤维 聚氨酯合成革基布。本发明另一较佳实例中,采用水溶性阻燃剂与水的质量比为1 1 1 2的水 溶液,其中水溶性阻燃剂为FR-6004(长兴达化工有限公司),将超细纤维合成革基布二浸 二轧,控制带液率为80 90%,在80 150°C烘干后得到非永久性阻燃超细纤维合成革基布。本发明还涉及由上述方法制得的超细纤维聚氨酯合成革基布。本发明进一步涉及一种超细纤维聚氨酯合成革的制备方法,其包括如下步骤采 用上述方法制备超细纤维聚氨酯合成革基布,之后对其进行干法造面,即可。其中,所述的干法造面可采用本领域常规工艺和试剂。通过干法造面可以赋予合 成革各种花纹和颜色,大大提高合成革的档次,但合成革的圆盘耐磨、学振耐磨、耐光照牢 度、湿热老化变色、雾化性能、可清洗性、耐寒冷性以及冷热循环等,都与合成革表面所用的 聚氨酯树脂、颜料、助剂以及加工工艺有着直接的联系。因此,为了使超细纤维聚氨酯合成 革具有优异的综合性能,本发明对干法造面时所用的革用表面聚氨酯树脂、颜料和助剂进 行了优化选择。较佳的,本发明选择脂肪族不黄变聚氨酯树脂作为革用表面(包括面层和中层) 聚氨酯树脂,其耐温性高,软化点达190°C,可以承受高温、强光照和强辐射的作用而不被破 坏,同时还需具有优良的成膜性能和耐化学品性,耐磨性好、玻璃化温度低等特性,提高超 细纤维聚氨酯合成革的耐黄变性。本发明优选Bayer的XP2610和ELH等。较佳的,本发明优选用汽巴的黄色B-KP和红色B-RF,ZSD化工的红色JL-MR和黄 色几-MY,上海晶联化工物资实业有限公司白色浆8001A和上海晶联化工物资实业有限公 司黑色色浆8907D中的一种或多种,以提高超细纤维聚氨酯合成革的颜色不变性,尤其是 在较高温度,较高光强,湿热等苛刻条件下的色不变性。由于采用上述优选颜料,本发明制 得的超细纤维聚氨酯合成革已通过本田、马自达、三菱和福特等汽车厂商的变色测试要求。较佳的,本发明优选道康宁的DC-51和DC-55有机硅耐磨助剂,以使超细纤维合成 革能达到汽车内饰用革的耐磨性能要求,且有利于提高色牢度,其用量较佳的为革用表面 聚氨酯树脂质量的0.1 3%。较佳的,本发明优选迪比喜化学贸易上海有限公司的UV-328和1260,以使超细纤 维合成革能达到汽车内饰用革的耐光性能要求,其用量较佳的为革用表面聚氨酯树脂质量 的 0. 2 1. 5%。本发明进一步涉及由上述方法制得的超细纤维聚氨酯合成革。本发明的超细纤维聚氨酯合成革除具有优异的阻燃性,还可具有优异的综合性 能,可适用于广泛的应用领域,尤其适用于要求严格的汽车内饰用革。因此,本发明再进一步涉及本发明的超细纤维聚氨酯合成革在制备汽车内饰用革中的应用。本发明中,上述各优选条件,可任意组合,即可得本发明各较佳实例。本发明所用试剂和用料均市售可得。本发明的积极进步效果本发明的方法可使得超细纤维合成革基布及合成革具有 优异的阻燃性能,绝大部分产品可达到水平燃烧速度<81mm/min,并且,本发明的超细纤维 合成革具有优异的综合性能,如耐光、坚牢度优良、高耐磨、色泽柔和、可以和天然牛皮革相 媲美的物性等,绝大部分产品可满足汽车内饰用革的要求。说明书附1为效果实施例2实验台的示意图,图中数字单位为mm。 实施例4操作工艺同实施例1,但浸渍步骤中按表4的配方配制聚氨酯浆料,即得超细纤维 聚氨酯合成革基布样品4。表 4 实施例5依次按照如下步骤制备超细纤维聚氨酯合成革基布纺丝、制备非织造布,烫平非 织造布(密度为0. 28g/cm3),将非织造布浸渍于聚氨酯浆料中,经质量百分比浓度为40% 的DMF水溶液凝固槽凝固,之后依次进行甲苯减量开纤、扩幅干燥上油和鞣皮,即得超细纤 维聚氨酯合成革基布。其中,纺丝过程中各原料的质量份数比为尼龙6 低密度聚乙烯FR-535阻燃色 母粒(日本大油墨化学公司)=50 50 12. 5。其中,浸渍步骤中按表5的配方配制聚氨酯浆料。表 5 实施例6依次按照如下步骤制备超细纤维聚氨酯合成革基布纺丝、制备非织造布,烫平非 织造布(密度为0. 28g/cm3),将非织造布浸渍于聚氨酯浆料中,经质量百分比浓度为40% 的DMF的水溶液凝固槽凝固,之后依次进行碱减量开纤、扩幅干燥上油和鞣皮,即得超细纤 维聚氨酯合成革基布。其中,纺丝过程中各原料的质量份数比为尼龙6 改性聚酯FR-535阻燃色母粒 (日本大油墨化学公司)=50 50 2. 5。其中,浸渍步骤中按表6的配方配制聚氨酯浆料。表 6 实施例7采用实施例1 4所制备的基布样品1 4,然后按照ATP 水=1 2的比例配 制溶液,搅拌均勻后,用氢氧化钠中和,使PH = 6 8,然后选用手感丰满,性能指标合格的 超细纤维合成革基布二浸二轧,控制带液率为85 %左右,然后在温度梯度为80°C、100°C、 110°C、12(TC、13(rC烘干,然后在195°C的高温下交联固化150秒,得到永久性阻燃超细纤 维聚氨酯合成革基布样品5 8。实施例8采用实施例1 4制备的基布样品1 4,FR-6004 水=1 1的比例配制溶液, 二浸二轧,控制带液率为85%左右,在130°C下烘干,得到超细纤维聚氨酯合成革基布样品 9 12。实施例9采用实施例1所制备的基布样品1,然后按照ATP Doher-6503 水=1 3 3 的比例配制溶液,搅拌均勻后,用氢氧化钠中和,使PH = 7,然后选用手感丰满,性能指标 合格的超细纤维合成革基布二浸二轧,控制带液率为80%左右,然后在温度梯度为80°C、 100°C、110°C、120°C、130°C烘干,然后在170°C的高温下交联固化5分钟,得到永久性阻燃 超细纤维聚氨酯合成革基布。实施例10采用实施例2制备的基布样品2,FR-6004 水=1 2的比例配制溶液,二浸二 轧,控制带液率为90%左右,在150°C下烘干,得到超细纤维聚氨酯合成革基布。实施例11采用实施例1制备的基布样品1,FR-6004 水=1 2的比例配制溶液,二浸二 轧,控制带液率为80%左右,在80°C下烘干,得到超细纤维聚氨酯合成革基布。实施例12采用实施例1 4制得的超细纤维合成革基布样品1 4,面层采用表7的原料 配比进行干法表面修饰,面层涂敷量为140g/m2,中层为200g/m2,粘结层(配比如表8)为 110g/m2,烘干温度梯度为60°C、80°C、10(rC、12(rC、135°C,车速为6m/min,干燥好后,采用 即剥离,得到超细纤维合成革样品1 4。为了获得各种性能和手感,然后经后整理,如水揉寸。表7干法表面修饰面层和中层配比表 表8干法粘结层原料配比表 实施例13采用实施例7制得的超细纤维基布样品5 8,面层采用表9的原料配比进行干法 表面修饰,面层涂敷量为140g/m2,中层为200g/m2,粘结层(配比如表8)为110g/m2,烘干温 度梯度为60 °C、80 V、100°C、120 V、135 V,车速为6m/min,干燥好后,采用即剥离,得到超 细纤维合成革样品5 8。表9 实施例14采用实施例8制得的超细纤维基布样品9 12,面层采用表10的原料配比进行干 法表面修饰,面层涂敷量为140g/m2,中层为200g/m2,粘结层(配比如表8)为110g/m2,烘干 温度梯度为60°C、80°C、100°C、120°C、135°C,车速为6m/min,干燥好后,采用即剥离,得到 超细纤维合成革样品9 12。表 10 实施例15依次按照如下步骤制备超细纤维聚氨酯合成革基布纺丝、制备非织造布,烫平非 织造布(密度为0. 28g/cm3),将非织造布浸渍于聚氨酯浆料中,经质量百分比浓度为40% 的DMF水溶液凝固槽凝固,之后依次进行甲苯减量开纤、扩幅干燥上油和鞣皮,即得超细纤 维聚氨酯合成革基布样品1。其中,纺丝步骤的操作为将质量份数比为=50 50 10的尼龙6 低密度聚 乙烯(LDPE) FR-535阻燃色母粒(日本大油墨化学公司),混合充分后,送入到单螺杆挤 出机中熔融纺丝,并经一牵和二牵定型后,在温度为50°C的烘箱中将水分烘干至汗水率为 2.0%,然后再切成53mm长度的短纤维,打包备用。其中,浸渍步骤中所用聚氨酯浆料为。 效果实施例1阻燃性能测试测试样品超细纤维合成革基布样品1 12 (实施例1 4、7和8);超细纤维合成革样品1 12 (实施例12 14)测试方法IS03795/SAE J369测试结果如表11所示表11阻燃性能测试数据 由以上数据可见,本发明的方法制得的超细纤维聚氨酯合成革基布,以及超细 纤维合成革具有优良的阻燃性能,其中超细纤维合成革基布样品1、3 12,超细纤维聚 氨酯合成革样品1、3 12均可达到汽车内饰用革的阻燃性要求(ISO 3795/SAE J369) (81mm/min0超细纤维合成革基布样品2虽然达不到< 81mm/min的水平,但经过后整理的 方式采用水溶性阻燃剂进行处理后(超细纤维聚氨酯基布样品5 12)达到< Slmm/min 的水平。由实施例15所制备的样品具有一定的阻燃性,其燃烧速度为95mm/min,按照实施 例8进行后处理后,其燃烧速度为34mm/min,能满足汽车内饰的阻燃要求。效果实施例2手感——僵直度测试测试样品超细纤维合成革基布样品1 12 (实施例1 4、7和8);超细纤维合成革样品1 12 (实施例12 14)测试方法在经向和纬向各剪三块试样,试样的尺寸为25mmX200mm。把试样放置 在如图1的实验台上,试样的右边紧贴着刻度线A,再在试样上放置一块相同尺寸的压板。 以约10mm/S的速度向斜面方向缓慢推动压板,当试样接触斜面时记录此时右边的位置,以 刻度线B作为记号。如果试样始终没有和斜面接触,重新剪切长350mm的试样试验。计算 每块试样在右边正面、右边反面和左边正面、左边反面四种状态测试结果的平均值,然后计 算经向和纬向三块试样的平均值。测试结果如表12所示表12僵直度测试数据 由以上数据可见,本发明的方法制得的超细纤维聚氨酯合成革基布,以及超细纤 维合成革具有优良的手感度和丰满度,其中超细纤维合成革基布样品2、4和9 12,以及超 细纤维合成革样品2、4和9 12均可达到汽车内饰用革的僵直度要求75mm。效果实施例3物理性能——撕裂强度测试测试样品超细纤维合成革基布样品1 12 (实施例1 4、7和8);超细纤维合成革样品1 12 (实施例12 14)测试方法ASTMD1004测试结果如表13所示表13撕裂强度测试数据 由以上数据可见,本发明的方法制得的超细纤维聚氨酯合成革基布,以及超细 纤维合成革具有优良的撕裂强度,所有的样品均可达到汽车内饰用革的撕裂强度要求: 彡150N。其中样品5 8,因采用了高温处理,撕裂强度有一定程度地下降但仍可以满足汽 车内饰革的撕裂强度要求》150N。效果实施例4物理性能——拉伸强度测试测试样品超细纤维合成革基布样品1 12 (实施例1 4、7和8);超细纤维合成革样品1 12 (实施例12 14)测试方法=ISO37 1994测试结果如表14所示表14拉伸强度测试数据 因超细纤维聚氨酯合成革的拉伸强度在径向和纬向有很大差异,且都是纬向比径 向低,因此上述数据采用纬向数据。由以上数据可见,本发明的方法制得的超细纤维聚氨酯合成革基布,以及超细 纤维合成革具有优良的拉伸强度,所有的样品均可达到汽车内饰用革的拉伸强度要求:彡225N。其中样品5 8因采用高温处理后,拉伸强度有所下降,但仍然可以满足汽车内饰 用革的测试要求。效果实施例5耐磨性能测试测试样品超细纤维合成革样品1 8(实施例12 13),对比样品1 4(超细 纤维合成革样品1 4的制备方法中耐磨助剂DC-51替换为汽巴耐磨助剂IRGASURF SR 100)。测试方法将样品在圆盘耐磨CS-10砂轮上8000回,测试其耐磨性。评判标注 SAE J948测试结果如表15所示表15耐磨性测试数据 由以上数据可见,本发明的方法制得的超细纤维聚氨酯合成革基布,以及超细纤 维合成革具有优良的耐磨性,其中超细纤维合成革样品1 8均可达到汽车内饰用革的耐 磨性要求4级。效果实施例6耐光性能测试测试样品超细纤维合成革样品1 12 (实施例12 14)测试方法SAEJ1885/J2212测试结果如表16所示表16耐光性测试数据 由以上数据可见,本发明的方法制得的超细纤维聚氨酯合成革基布,以及超细纤 维合成革具有优良的耐光性,其中超细纤维合成革样品1 12均可达到汽车内饰用革的耐 光性要求4级。效果实施例7色牢度测试
测试样品超细纤维合成革样品1 12 (实施例12 14)测试方法FLTM-BN103-01测试结果如表17所示表17色牢度测试数据 由以上数据可见,本发明的方法制得的超细纤维聚氨酯合成革基布,以及超细纤 维合成革具有优良的耐光性,其中超细纤维合成革基布样品1 12均可达到汽车内饰用革 的色牢度要求4级。效果实施例8耐寒性测试测试样品超细纤维合成革样品1 12(实施例12 14)测试方法FLTM-BN128-01测试结果所有样品-30°C下冲击无裂痕。效果实施例9耐H2S变色测试测试样品超细纤维合成革样品1 12 (实施例12 14)测试方法TLFM-AN102-01测试结果所有样品耐H2S测试变色等级> 4级,能满足汽车内饰用革要求。
本发明公开了一种超细纤维聚氨酯合成革基布的制备方法按常规工艺步骤制备超细纤维聚氨酯合成革基布,其中在纺丝步骤中,加入FR-535尼龙阻燃色母粒对超细纤维丝进行阻燃处理。本发明还公开了由该方法制得的超细纤维聚氨酯合成革基布,一种超细纤维聚氨酯合成革的制备方法,以及由该方法制得的超细纤维聚氨酯合成革及其在制备汽车内饰用革中的应用。本发明的方法可使得超细纤维合成革基布及合成革具有优异的阻燃性能,可达到水平燃烧3分钟,烧毁长度≤81mm,并且,本发明的超细纤维合成革具有优异的综合性能,如耐光、坚牢度优良、高耐磨、色泽柔和、可以和天然牛皮革相媲美的物性等,可满足汽车内饰用革的要求。
一种超细纤维聚氨酯合成革及其基布,及制备方法和应用制作方法
- 专利详情
- 全文pdf
- 权力要求
- 说明书
- 法律状态
查看更多专利详情
下载专利文献
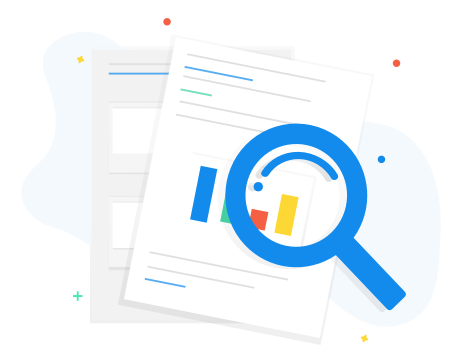
下载专利
同类推荐
-
D·阿迪森代淑梅, 李秋园代淑梅, 李秋园周耀恩, 罗庆周耀恩, 罗庆
您可能感兴趣的专利
-
周耀恩, 罗庆马延和马延和马延和F-J·明特, J·博斯曼
专利相关信息
-
F-J·明特, J·博斯曼迈克尔·H·埃利, 迈克尔 H 埃利吕伟民吕伟民D·索默, U·斯图茨