专利名称:制造成型二氧化硅玻璃坯体的方法 由无定形的、多孔的成型SiO2坯体,可利用烧结和/或熔融来制造高纯度的、局部或完全致密化的成型SiO2坯体;例如,该SiO2坯体可用作拉制硅单晶的坩埚,或当作玻璃纤维或光纤的预成型品。而且任何类型的石英物品都可以用此方法制成。而且高孔隙度无定形的成型SiO2坯体已在许多技术领域广泛利用。可提及的实例为过滤材料、隔热材料或防热罩。无沦成型坯体的使用目的为何,此类成型坯体的制造方法必须有三个基本要件。一方面是成型坯体的成品应尽可能具有正确的最终尺寸及轮廓;而另一方面未烧结的成型坯体最好具有最高密度及优异的均匀性。如此便可将烧结温度降低,其效果为一方面使加工成本显著下降,而另一方面在烧结成型SiO2坯体时使结晶感受性显著降低。最后,成型坯体必须有足够的强度以容许工业应用或作进一步加工。制造SiO2成型坯体的方法分成干式及湿式化学方法。以干式或压制法而言,通常需要加入粘合剂以达成足够的高密度并确保成型后生坯体有合格的强度。然而之后这些又必须以高难度技术及更昂贵的步骤除去。将杂质引入成型坯体的危险性会使成型坯体无法使用于例如拉制硅单晶体、制造光纤或其他光学方面的应用。因此,湿式化学法为制备多孔性成型SiO2坯体的优选方法。文献中已公开的一个方法是溶胶-凝胶法。这通常以将含硅单体溶解在溶剂(溶胶)开始,经由水解及缩聚形成纳米多孔的立体SiO2网络(凝胶)。接着通过干燥得到多孔成型坯体。该方法的一项缺点是起始物质昂贵。另外,此方法只能获得含有10至20重量%固体含量的凝胶。这样的成型坯体强度很低并在后续烧结期间明显收缩。如此成型便无法达成正确的最终尺寸及轮廓。EP 318100中说明了取得低孔隙度成型SiO2坯体的方法。在此例中,制备在水中高度分散(热解)二氧化硅的分散液。此处物质的触变性应用在成型上。所得的固体含量达60重量%。产生的40体积%收缩率使得成型成正确的最终尺寸及轮廓极为困难。EP 0220774透露一个制造旋转对称的成型SiO2坯体的方法利用高度分散性二氧化硅分散液的离心力达成旋转铸造的方法。该方法仅限应用在旋转对称的成型坯体。EP 653381及DE-A 2218766公开了一个滑铸方法将粒度为0.45至70微米的粒子在水中制成石英玻璃分散液。该分散液可达成的固体含量在78与79重量%之间。接着该分散液通过萃取水在多孔的铸模中凝固,并从铸模取出后干燥。虽然可用此方法制造出固体含量高、接近正确最终尺寸的成型坯体成品,但该方法因有依赖分散作用的水萃取而非常耗时,而且只能应用于薄壁成型部件。EP 0196717 B1透露了一个压力铸造方法在多孔的铸模中通过高压,从高度分散性二氧化硅的水性分散液制造出成型SiO2坯体。为了控制流变特性及在成型后使成型坯体达成足够的强度,必须在其中混入离子型添加剂。生坯体的伴随纯化排除了以下的应用例如拉制硅单晶的坩埚、光纤或光学元件。成型坯体可达成的密度,约50%,因太低而无法成型成接近正确的最终尺寸。如DE 19943 103 A1中所述,具有极高填充系数的分散液的成型已有建议,以便达成非常高的生坯密度。但这在实施时会造成更大的问题,因分散的SiO2粒子会导致显著的触变效应,使加工更加困难。
电泳沉积是湿化学成型法,即使由填充系数低的悬浮液也可达成非常高的密度。术语“电泳沉积”是指对应于施加的静电DC电场,表面带电荷的电介质粒子在分散液中的运动及凝聚作用。由于该粒子表面电荷与周围介质媒体的互动,使其与施加的电位差相反方向在分散液中运动。这些粒子可沉积在带与粒子表面电荷相反电荷的导电电极上(阳极或阴极),从而获得稳定的成型坯体。
这优选使用有机分散液,虽然这需要复杂的保护措施以去除成型及后续热处理中会产生的毒性副产品。另外,丢弃有机分散液也会造成生态问题。
如EP 0104903中的实施例所述,电泳沉积发生的其他问题来自水中分散液。例如,水在DC电压约1.5V以上时会电分解。由于阳极(+)与阴极(-)之间的电位差,氢(H+)及羟基离子(OH-)会朝向带有相反电荷的电极迁移。离子在电极重新结合并分别形成氢气或氧气,有时会导致成型坯体中作为气体包裹体的大的不规则瑕疵。因此,此种成型坯体不可能应用于工业规模上。
US 2002/0152768 A1公开了一种制造坯体、特别是杯型坯体的方法利用电泳沉积法以高纯度SiO2玻璃制造。在此情况下,带负电的SiO2粒子会从至少有80重量%固体含量的水性悬浮液,沉积至导电的带正电电极(阳极)上。因羟基离子在沉积的成型坯体中的阳极重新结合,目前尚未有防范内含气泡的可行措施。另外,悬浮液中的SiO2粒子表面必须带负电,才能在阳极端引起沉积。由由添加剂将pH调整在6与9之间达成。该添加剂以及沉积的成型坯体与石墨阳极之间的直接接触,导致成型坯体内污染,使成型坯体无法当作光纤及其他光学元件的预成型品、或抽拉硅单晶的坩埚使用。
US 5194129中公开了处理气泡形成问题的方法。沉积在能保留并储存氢的钯电极上发生。这可防范气泡与瑕疵。但此方法受限于钯的有限氢保留容量,因而只能制造薄壁成型坯体。另外,成型坯体与钯电极之间的接触也造成污染。
US 3882010公开了一个利用电泳沉积由含有耐火陶瓷粒子的悬浮液制造铸造坩埚的方法。该发明尝试解决离子在沉积电极重新结合而形成气泡的问题;首先将耐火粒子的导电层及石墨(10∶1的比例)涂在蜡模上,接着在其上实施电泳沉积。该文献未透露要预防气泡在成型坯体中形成所根据的机理。另外,该方法非常复杂且限于特定系统。因此以此方法无法制造出高纯度的SiO2成型坯体。
EP 0200242及EP 0446999 B1公开了利用电泳沉积在多孔膜上制造玻璃成型坯体、以及后续纯化与烧结的方法。此方法中由于添加物的污染而必须将多孔玻璃成型坯体纯化,形成一个额外耗时且高成本的加工步骤。所使用膜的特征在于其孔隙尺寸小于要沉积的粒子的平均孔隙大小。当使用纳米级粒子作为起始材料时,所使用膜的孔隙同样必须也是微小的孔隙;这明显限制了膜材料的选择。例如,不可能使用在压力铸造、滑铸或毛细铸造时使用的本领域技术人员已知的多孔塑料模,因其平均孔隙大小是约为几百纳米至100微米。由于日前尚未出现已知构型上稳定的膜材料,其一方面孔隙大小小于50纳米,另一方面不会将污染引进SiO2玻璃成型坯体(例如石膏或粘土模),使用此方法无法生产以高纯度SiO2玻璃制造的立体成型坯体。
本发明的目标是提供一种可以制造均匀的成型SiO2坯体的方法。
此目标可由以下方法达成包括相对大的无定形SiO2粒子及相对小的无定形SiO2粒子的无定形SiO2粒子,从水性分散液中经电泳沉积在绝缘的膜上,其形状与构型符合要制造的SiO2成型坯体,其中膜的平均孔隙大小大于较小的无定形SiO2粒子的平均粒度。
依据本发明的方法便能制造具有开孔、接近正确的最终尺寸与轮廓的成型坯体。
在实施电泳沉积的装置中,不导电的膜固定在两个导电的电极、即阳极(正极)与阴极(负极)中,该膜的平均孔隙大小大于较小的无定形SiO2粒子的平均粒度,且该膜的形状与构型符合要制造的SiO2成型坯体。在此情况下,电极与膜之间无电接触。阳极与膜之间的空间充满了由水及无定形SiO2粒子组成的分散液。膜与阴极之间的空间则充满了匹配流体(matching fluid)。通过在阳极(正极)与阴极(负极)之间施加电位差(DC电压),使得分散液中的SiO2粒子与分散剂分离,并随电泳的驱动力从阳极移向不导电的膜。SiO2粒子沉积并压紧在膜上,从而首先形成具有开孔的湿SiO2成型坯体。此成型坯体随后与膜分离并干燥。在特定实施方案中,成型坯体首先在膜上干燥然后再与膜分离。
不导电的膜优选可透过离子,使得阳离子与阴离子可在电泳沉积时,各自通过膜向阴极或阳极移动。
由于膜上的沉积物与两个电极之间的空间隔离,因此能避免引进气泡;气泡是由H+与H-离子在电极重新组合而形成的。
对于沉积,优选使用具有在5至60体积%之间开孔的不导电的膜,更优选在10至30体积%之间。该膜的孔隙大小大于使用的较小SiO2粒子的平均粒度。所使用的膜孔隙大小在100纳米与100微米之间,优选介于100纳米与50微米之间,更优选介于100纳米与30微米之间。
膜不导电,也无半导体特性。优选其电阻率大于108欧姆·米,特别优选大于1010欧姆·米。
该膜可用水润湿。膜与水之间的接触角相应小于90°,优选小于80°。该膜用水完全润湿,以便实施电泳沉积时通过膜取得阴极与阳极间电场的恒定轮廓(constant profile)。
本领域技术人员已知的塑料适合当作膜的材料,其是化学性稳定的且不含自由残渣,特别无金属残渣。工业压滑铸造所使用的塑料也优选合适。最优选聚甲基丙烯酸酯与聚甲基丙烯酸甲酯。
膜厚度是由要制造的成型物的形状来决定的。优选膜厚度,使得可由膜准确地制造出指定的形状,并且在实施本发明的方法时该形状是构型稳定的。膜厚度优选不要超过必要的厚度,以便满足先前提及的条件;若非如此,实施本发明的电泳时,电场会发生不必要的衰减,而损坏电泳沉积。
导电且化学性稳定的材料可当电极使用。还可使用涂覆导电的、化学性稳定的材料。电极的使用方式为整批形式或网状形式。
导电的塑料、石墨、钨、钽或贵金属皆为优选的电极材料。特别优选钨、钽或铂。然而,电极也可由合金组成和/或用前述材料涂覆。如此选择电极材料可防止沉积的成型坯体被原子杂质、尤其电极的金属原子污染。
优选使用水作为分散剂。特别优选使用电阻率大于或等于18兆欧姆·厘米的高纯水。
优选使用具有最圆及最紧密结构的SiO2粒子作为无定形SiO2粒子。SiO2粒子的比密度应优选介于1.0与2.2克/立方厘米之间。更优选粒子的比密度介于1.8与2.2克/立方厘米之间。尤其优选粒子的比密度介于2.0与2.2克/立方厘米之间。优选SiO2粒子外表面具有小于或等于3OH基/平方纳米,更优选小于或等于2OH基/平方纳米尤其优选小于或等于1OH基/平方纳米。
优选无定形SiO2粒子的晶体部分最多为1%。其还应优选与分散剂之间展现最少的相互作用。
存在的无定形SiO2粒子总是至少有两种不同的平均粒度。较大的无定形SiO2粒子粒度分布的D50值应介于1与200微米之间;优选1与100微米之间;更优选10与50微米之间,特别优选10与30微米之间。
粒子分布尽可能窄是更有利的。无定形SiO2粒子的BET表面积为0.001平方米/克至50平方米/克;更优选0.001平方米/克至5平方米/克较佳;特别优选0.01平方米/克至0.5平方米/克。
不同来源的无定形SiO2粒子具有这些特性,例如熔凝(重新烧结)二氧化硅及任何类型的无定形烧结的或压紧的SiO2。因此这些优选适合于依照本发明制造分散液。
相应的材料可以目前已知的方式在氢氧焰中制造。也可例如由Tokoyama,Japan以Exelica?商标购得。
若前述条件都已符合,则也可使用其他来源的粒子,例如天然石英、石英玻璃砂、透明石英、研磨石英玻璃或研磨石英玻璃废料、以及化工制造的二氧化硅玻璃,例如沉淀的二氧化硅、高度分散(煅制)二氧化硅(以火焰热解方式制造)、干凝胶或气凝胶。
无定形SiO2粒子优选是沉淀二氧化硅、高度分散的二氧化硅、熔凝二氧化硅或压紧的SiO2粒子;更优选高度分散的SiO2或熔凝SiO2;特别优选熔凝SiO2。也可同样使用前述各种SiO2粒子的混合物。
小的SiO2粒子优选是煅制或熔凝二氧化硅,其粒度为1至100纳米,优选10至50纳米。
这些SiO2粒子的BET表面积优选为10平方米/克至400平方米/克;更优选50平方米/克至400平方米/克。高度分散的(煅制)SiO2(以火焰热解方式制造)优选具有这些特性。它们可以商品名HDK(Wacker-Chemie)、Cabo-Sil(Cabot Corp.)或Aerosil(Degussa)购得。这些纳米级SiO2粒子的功能是充当基本上较大SiO2粒子之间的无机粘合剂,但不是用作达成更高填充因数的填充材料。这样的SiO2粒子在分散剂中优选具有双峰式粒度分布。
针对无定形SiO2粒子总量,较小无定形SiO2粒子的存在量优选是0.1至50重量%;更优选1至30重量%;特别优选1至10重量%;100重量%中剩余部分由较大的无定形SiO2粒子形成。
在一个特别实施方案中,无定形SiO2粒子以高纯度形式存在,即含有一定比例的原子杂质(特别是金属)≤300ppmw(百万分之重量份);该比率最好是≤100ppmw;更优选≤10ppmw且最优选≤1ppmw。
因为以电泳为驱动力量时,表面电荷粒子的移动速度不受粒度的影响,水及单峰式粒度分布的SiO2粒子的分散液,也可均匀的沉积,形成有开孔的均匀成型坯体,而不会使粒子依其大小分离。但在其他湿的化学方法中则观察到分离现象。
SiO2粒子以目前已知的方式在水中分散。本领域技术人员已知的任何方法都可应用于此。分散液的填充因数介于10与80重量%之间;优选在30与70重量%之间;特别优选在50与70重量%之间。因其比较低的填充因数,无定形SiO2粒子分散良好,而触变性仅为次要因素,并且该分散液可容易地加工。流变性能可进一步调整并重复控制。
该分散液的粘度有利地介于1与1000mPa·s之间;优选介于1与100mPa·s之间。
该分散液的pH值介于3与9之间;优选在3与7之间;特别优选3与5之间。导电性介于0.1与10000μS/cm之间;优选介于1与100μS/cm之间。优选ζ电位介于-10与-80mV之间。
在特定实施方案中,在分散液中加入无机碱,优选不污染金属成分的挥发性物质较好;特别是铵化合物,如四甲基氢氧化铵(TMAH)或氨,或它们的混合物。
经此方式调整pH值介于9与13之间,优选在10与12之间。同样调整Z电位则在-10与-70mV之间,优选在-30与-70mV之间。
水当作膜与阳极之间的匹配流体。优选使用电阻率大于或等于18兆欧姆/厘米的高纯度水。
在特殊实施方案中,在匹配流体中加入了无机或有机酸,如HCl、H2SO4、硅酸、醋酸或甲酸,或碱,尤其是铵化合物如四甲基氢氧化铵(TMAH)或NH3,或它们的混合物。再者也可在其中加入离子源添加物。特别优选分解时不形成任何金属离子的挥发性物质。因此匹配流体的电导率优选介于0.1与100,000μS/cm之间;更优选介于0.1与10,000μS/厘米之间。
阳极(正电荷)与阴极(负电荷)之间施加的DC电压介于5与500V之间;优选介于30与300V之间。电场强度介于1与100伏特/厘米之间;优选介于5与50伏特/厘米之间。
沉积的持续时间基本上视选择的坯体厚度而定。原则上可制备任何坯体厚度。沉积的体厚度介于1与50毫米之间;优选5与30毫米之间;更优选5与20毫米之间。沉积速度介于0.1与2毫米/分钟之间;优选0.5与2毫米/分钟之间。
以此方式沉积的具有开孔的成型坯体,可用本领域技术人员已知的方法从膜分离。沉积的成型坯体优选使用压缩空气与膜分离;空气经由膜孔隙从膜的对侧吹入成型坯体。成型坯体也可用水以类似方式进行分离。
在特定实施方案中,成型坯体与膜的分离方式如下将沉积成型坯体的膜放置在电极之间,并将电极与成型坯体或膜之间的空间用水填充,优选使用高纯度水;并在电极之间施加DC电压,该DC电压的信号与电泳沉积施加的电压的信号相反。通过电渗透流量,成型坯体与膜之间的界面会形成水层,使成型坯体从膜上脱离。
所获得的具有开孔的成型坯体接着干燥。干燥采用本领域技术人员已知的方法实施例如真空干燥、通过热气如氮气或空气的干燥、接触干燥或微波干燥。同时也可将单独的干燥方法组合使用。优选通过微波干燥。
进行干燥时成型坯体内的温度优选介于25℃与成型坯体孔隙中分散剂(水)的沸点之间。干燥时间则视待干燥的成型坯体体积、最大层厚度及成型坯体的孔隙结构而定。
成型坯体干燥时发生微小收缩。收缩程度视湿成型坯体的填充系数而定。填充系数为80重量%时,体积收缩等于或小于2.5%且线性收缩等于或小于0.8%。填充系数越高则收缩得越少。
在特定实施方案中,所有步骤皆使用高纯度材料进行,成型坯体原子杂质、尤其是金属的比例小于或等于300ppmw;优选小于或等于100ppmw;更优选小于或等于10ppmw最优选小于或等于1ppmw。
可以此方式获得的成型坯体为无定形SiO2成型坯体;其具有开孔,以及接近正确的最终轮廓与任何所需大小及构型。
成型坯体的SiO2粒子含量至少为64体积%;优选至少有70体积%;其孔隙体积(以汞孔隙计测定)范围由1毫升/克至0.01毫升/克;优选由0.8毫升/克至0.1毫升/克;更优选由0.4毫升/克至0.1毫升/克;在烧结至1000℃时保持稳定的孔隙直径范围物1至10微米,优选3至6微米直径,或者孔隙具有双峰式直径分布第一孔隙最大直径范围是0.01微米至0.05微米;优选0.018微米至0.0022微米。第二孔隙最大直径范围是1微米至5微米;优选1.8微米至2.2微米。
本发明的成型坯体可具有单峰式孔隙直径分布,孔隙直径范围是2.2微米至5.5微米;优选3.5微米至4.5微米,并且成型坯体的内表面积为100平方米/克至0.1平方米/克,优选50平方米/克至0.1平方米/克。将具有上述双峰式孔隙直径分布的成型坯体加热至1000℃时,便可获得这样的成型坯体。
将本发明成型坯体烧结至1000℃时,其体积优选是稳定的。
依据本发明,使用少量(约1至4重量%)纳米级粒子制造分散液时,本发明的成型坯体制造方法可用于由分散液制造成型坯体,其单峰式孔隙分布的大小范围是1微米至10微米;优选3微米至6微米。在分散液中使用较大的粒子会使成型坯体具有较大的孔隙;而分散液中窄小的粒度分布则使成型坯体有窄小的孔隙大小分布。
将较大量的(约5至50重量%)纳米级粒子加入时,会使成型坯体有双峰式孔隙大小分布;除了所说的孔隙外,成型坯体也包含次纳米级孔隙。
在所有的情况中,成型坯体的整体填充系数保持不变。
本发明成型坯体的密度介于1.4克/立方厘米与1.8克/立方厘米之间。
所描述的单峰式孔隙分布的成型坯体在烧结温度达1000℃时会维持稳定至少达24小时。另外,他们具有热稳定性,而且有非常低的热膨胀系数。
由于上述的成型坯体具有特性,因此具广泛不同的用途;例如当作过滤材料、隔热材料、防热罩、催化剂载体材料,以及充当玻璃纤维、光纤、光学玻璃或任何类型的石英物件的“预成型品”。
在另一具体实施方案中,可将广泛不同的分子、材料及物质完全或部分加入具有开孔的成型坯体。优选具有催化活性的分子、材料及物质。如同US 5655046中所述,本领域技术人员已知的所有方法皆可用于此处。
在另一具体实施方案中,可将提供额外性质给各成型坯体的分子、材料及物质加入分散液和/或具有开孔的成型坯体。
在特定实施方案中,可将促进或促使方英石形成的化合物完全或部分加入分散液和/或成型坯体。如同DE 10156137中所描述,本领域技术人员已知的促进和/或引起方英石形成的化合物皆可用于此处。在此情况下,优选使用BaoH和/或铝化合物。
此类成型坯体烧结完成后,便能获得拉Si单晶的坩埚,其在内部和/或外部具有方英石层,或者完全由方英石构成。这些坩埚特别适合拉晶,因为他们具有热稳定性,并且例如其污染硅熔体的程度较低。由此可在拉晶时可达到较高的产量。
在具体实施方案中,所获得的成型坯体可经再次烧结。本领域技术人员已知的所有方法都可应用于此,例如真空烧结、区域烧结、电弧放电烧结、等离子体或激光烧结、感应烧结或在大气或气流中烧结。
优选EP-A-1210294中所述的在真空或气流中烧结。
成型坯体可进一步在特殊气氛如He、SiF4中烧结,以便达到再纯化和/或富集烧结物中特定原子及分子。如US 4979971中所述,本领域技术人员已知的所有方法都可应用于此。如EP 199787中所述,所有方法更可进一步用于再纯化。
如同一申请人在申请DE 10158521 A及DE 10260320 A中的详细说明,优选以CO2激光烧结。如此便可能制造出100%无定形(无方英石)烧结的成型SiO2玻璃坯体,其是100%无定形、透明、不透气且有至少2.15克/立方厘米、优选2.2克/立方厘米的密度。
在特定实施方案中,烧结的成型SiO2玻璃坯体内无气体包裹体,并且优选其OH基浓度为小于或等于1ppm。
在特定实施方案中,所有步骤皆使用高纯度材料实施时,烧结的成型坯体的原子杂质、特别是金属比例≤300ppmw;优选≤100ppmw;特别优选≤10ppmw;更优选≤1ppmw。
以此方法制造的烧结成型SiO2玻璃坯体特别适合于使用二氧化硅玻璃的所有用途。优选的应用场合为任何类型的石英物件、玻璃纤雏、光纤及光学玻璃。
拉硅单晶的高纯度SiO2玻璃坩埚是特别优选的应用场合。
图1所示为实施例1中所述的本发明制造坩埚的方法。
图2所示为实施例2中所述的本发明制造坩埚的方法。
以下的实施例将进一步说明本发明。
实施例1一个14英寸的坩埚经电泳方法沉积在塑料膜的内部。
由铝(表面涂敷铂)制成的阳极(1)与电压电源(7)的阳极连接。塑料膜(3)由具有40微米大孔隙半径及20体积%的开孔度的聚甲基丙烯酸甲酯所组成。SiO2分散液(5)由5重量%的煅制二氧化硅、70重量%的熔凝二氧化硅及25重量%的高纯度水组成。该分散液位于阳极(1)与膜(3)之间。匹配流体(4)的电导率已使用TMAH电解液调整至7000μS/cm,并且位于膜与阴极(2)之间。由铝(表面涂敷铂)制成的阴极(2)与电压电源(7)的阴极连接。
电场密度为15伏特/厘米时,坯体厚度为10毫米的坩埚在5分钟时间内从分散液沉积在面对膜阳极(内侧)的一侧上。
已经沉积坩埚后,除去分散液并由匹配流体取代。接着使电场反向20秒后,坩埚与膜脱离。
实施例2一个14英寸的坩埚经电泳法沉积在塑料膜的外侧。
以铝(表面涂数铂)制成的阴极(1)与电压电源(7)的阴极连接。塑料膜(3)由40微米大孔隙半径及20体积%开孔度的聚甲基丙烯酸甲酯组成。SiO2分散液(5)由5重量%的煅制二氧化硅、70重量%的熔凝二氧化硅及25重量%的高纯度水组成。该分散液位于阳极(2)与膜(3)之间。
匹配流体(4)的电导率已使用TMAH电解液调整至7000μS/cm,并且位于膜与阴极(1)之间。以铝(表面涂敷铂)制成的阳极(2)与电压电源(7)的阳极连接。
电场密度为15伏特/厘米,坯体厚度为10毫米的坩埚在5分钟时间内从分散液沉积在膜的外侧上。坩埚已经沉积后,除去分散液并由匹配流体取代。接着使电场反向20秒后,坩埚与膜脱离。
一种制造具有接近正确的最终尺寸及轮廓的均匀成型SiO
制造成型二氧化硅玻璃坯体的方法
- 专利详情
- 全文pdf
- 权力要求
- 说明书
- 法律状态
查看更多专利详情
下载专利文献
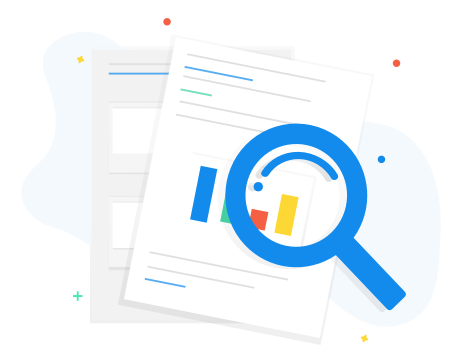
下载专利
同类推荐
-
岸本正一高伯菘, 王坤池王坤池, 王清华王坤池, 王清华彭威方晨航
您可能感兴趣的专利
-
苅谷浩幸, 前田伸广苅谷浩幸, 前田伸广秦升益秦升益秦升益秦升益吕文慧, 尹计深
专利相关信息
-
吕文慧, 尹计深吕文慧, 尹计深肖湘东王小锋张艺龄丁体英丁体英