多晶硅铸锭后熔融石英坩埚碎片再生方法[0002]目如,多晶娃太阳能电池已经占有太阳能电池的主流市场,多晶娃铸淀是多晶娃太阳能电池生产中主要的环节之一。多晶硅铸锭的过程中熔融石英坩埚为一次性使用的消耗品,加大了多晶硅铸锭的成本。随着高品位石英矿的日渐枯竭,石英原料成本逐渐增加。[0003]现阶段铸锭用熔融石英坩埚的制作主要是采用注浆法。熔融石英坩埚原料采用铸锭后熔融石英坩埚碎片,由于石英坩埚碎片存在微量的污染,一般情况下经过常规粉碎后用于作为绝热材料的填充物使用,产生了极大的浪费。如果能够对铸锭后熔融石英坩埚碎片的回收利用再生熔融石英坩埚,则既可以避免熔融石英材料的浪费,又可以降低熔融石英坩埚的制造成本。但是,目前还没有能够有效回收利用再生坩埚的办法,若采用常规的浆料制作方法及注浆法成型,再生熔融石英坩埚将达不到多晶硅铸锭的使用要求,不能实现真正的再生。[0004]由上可见,对再生熔融石英坩埚已变的十分的迫切。一种绝对行之有效的的再生技术将极大地降低多晶硅铸锭的成本,对多晶硅太阳能电池的发展将起到极大的推动作用。因此,有必要提供一套全新的包括制浆及成型的利用熔融石英坩埚碎片再生石英坩埚的方法。
[0005]本发明所要解决的技术问题是提供一种多晶硅铸锭后熔融石英坩埚碎片再生方法,再生坩埚具有成型强度高、致密度大、密度均匀、成品率高的特点,且制作周期短、耗费成本低。[0006]本发明为解决上述技术问题而采用的技术方案是提供一种多晶硅铸锭后熔融石英坩埚碎片再生方法,依次包括如下步骤:a)对多晶硅铸锭后熔融石英坩埚碎片进行清洗分拣山)对所述石英坩埚碎片进行非晶化处理;c)对所述石英坩埚碎片进行湿式粉碎;d)对粉碎后的石英坩埚碎片进行制浆,采用等静压方式成型;e)进行晾干及烧结处理。[0007]上述的多晶硅铸锭后熔融石英坩埚碎片再生方法,其中,所述步骤a)中采用超声波并且使用弱酸溶液进行清洗,所述弱酸溶液按盐酸和水1:100的体积比稀释,所述弱酸溶液温度为60°C,清洗时间为4~6小时。
[0008]上述的多晶硅铸锭后熔融石英坩埚碎片再生方法,其中,所述步骤a)中采用超声波并且使用弱酸溶液进行清洗,所述弱酸溶液按盐酸和氢氟酸按照1:1.5的体积比配置,所述清洗时间为I~10小时。
[0009]上述的多晶硅铸锭后熔融石英坩埚碎片再生方法,其中,所述步骤b)中非晶化处理过程如下:对于析晶量较少的坩埚碎片粗碎后,在1700~1800°C下熔融2~4小时后进行快速冷却;对于析晶量较多的坩埚碎片细碎至粒度100μπι以内后采用过筛的方式除去部分方石英晶体。
[0010] 上述的多晶硅铸锭后熔融石英坩埚碎片再生方法,其中,所述步骤c)中在进行湿式粉碎时按重量百分比加入0.5~1%的去离子水,并将石英坩埚碎片粉碎至I~50um。
[0011]上述的多晶硅铸锭后熔融石英坩埚碎片再生方法,其中,所述步骤c)采用管式粉碎机进行湿式粉碎,粉碎后浆料颗粒按重量百分比组成如下:粒度为I~IOym占20%,粒度为10~30 μ m占60%,剩余粒度为30~50 μ m占20%。
[0012]上述的多晶硅铸锭后熔融石英坩埚碎片再生方法,其中,所述步骤d)中在制浆过程中按重量百分比加入:0.2%丙烯酰胺作为有机单体,0.1%双丙烯酰胺作交联剂,0.5%亚硫酸铵作为催化剂,0.5%过硫酸铵作为引发剂。
[0013]上述的多晶硅铸锭后熔融石英坩埚碎片再生方法,其中,所述步骤d)按重量百分比加入0.5~2%的硼酸、磷酸或氮化硅抑制方石英晶粒的生长,控制方石英的重量百分含量至2%以下。
[0014]上述的多晶硅铸锭后熔融石英坩埚碎片再生方法,其中,所述步骤d)采用冷等静压机进行快速加压成型,最高压力为llOMPa,成型温度为40°C,采用缓慢泄压的方式进行脱模,泄压时长为20小时。
[0015]上述的多晶硅铸锭后熔融石英坩埚碎片再生方法,其中,所述步骤e)中晾干过程如下:在温度60°C,湿度50%的室内自然晾干I~2小时;所述步骤e)中烧结为常压烧结,最高烧结温度为1200°C,在900°C以下升温速率较缓,在高温900~1200°C之间采用快速升温烧结的办法,烧结时采用氮气或者氩气进行保护。
[0016]本发明对比现有技术有如下的有益效果:本发明提供的多晶硅铸锭后熔融石英坩埚碎片再生方法,通过对多晶硅铸锭后熔融石英坩埚碎片进行清洗分拣,非晶化处理,湿式粉碎以及等静压方式成型,能够避免石英材料的浪费,大大降低添加剂的加入量,避免引入杂质来源,从而使得再生坩埚具有成型强度高、致密度大、密度均匀、成品率高的特点,且制作周期短、耗费成本低。
[0017]图1为本发明多晶硅铸锭后熔融石英坩埚碎片再生流程示意图。
[0018]下面结合附图和实施例对本发明作进一步的描述。
[0019]图1为本发明多晶硅铸锭后熔融石英坩埚碎片再生流程示意图。
[0020]请参见图1,本发明提供的多晶硅铸锭后熔融石英坩埚碎片再生方法,依次包括如下步骤:
[0021]步骤S1:对多晶硅铸锭后熔融石英坩埚碎片进行清洗分拣;
[0022]步骤S2:对所述石英坩埚碎片进行非晶化处理;对于坩埚不同的析晶程度采取不同的非晶化处理方式,对于析晶量较少的坩埚碎片粗碎后,采用高温1700~1800°C熔融2~4小时后强制快速冷却的方法;对于析晶量较多的坩埚碎片细碎至粒度100 μ m左右后采用过筛的方式,除去部分方石英晶体,并且在制浆过程中加入方石英抑制剂进行坩埚烧结;
[0023]步骤S3:对所述石英坩埚碎片进行湿式粉碎作为制浆原料,其浆料具有流动性及悬浮性均较好的特点;在细碎过程中采用湿式粉碎的方法,加入去离子水量约为0.5~1?七%,相对注浆法成型,浆料含水量较低;制浆过程中只需加入相对注浆法成型很少量的有机单体、催化剂、交联剂及引发剂等,即可实现很理想的成型及烧结效果,烧结后坩埚密度高,气孔率低;
[0024]步骤S4:对粉碎后的石英坩埚碎片进行制浆,采用等静压方式成型;成型速率较快,注浆后成型过程中加压采用快速施压,缓慢泄压的方式,成型温度为40°C左右;
[0025]步骤S5:进行晾干及烧结处理;采用等静压成型后,胚体含水量较少,在60°C,湿度50%的环境中,晾干时间仅为I~2小时,或无需晾干,即可进行烧结。
[0026]本发明提供的多晶硅铸锭后熔融石英坩埚碎片再生方法,用多晶硅铸锭后坩埚碎片经过特殊处理后作为原料且采用等静压成型的方法成型后常压烧结。等静压成型方法的采用使的对含水量的要求及有机单体、交联剂及引发剂的使用量大大减小,减少了杂质来源。本发明具有以下特点:等静压成型速率快,减少成型时间;由于采用的等静压成型胚体含水量较少,只需自然晾干I~2小时即可立即烧结,缩短生产周期;坩埚碎片作为原料可极大的减少石英原料成本和加工时间。
[0027]下面给出一个具体实施例对本发明进行的进一步的详细描述,具体过程如下:
[0028]将铸锭后的熔融石英坩埚碎片进行拣选,除去表面涂层碎屑,舍弃部分粘硅及渗透很严重的坩埚。
[0029]碎片清洗,将碎片放入温度为60°C带有清洗溶液的清洗池中,使用超声波频率为40KHZ,溶液为按照盐酸和水重量百分比1:100的配比得到的弱酸溶液,清洗时间为4~6小时,可有效清除表面残留涂层粉末、石墨等杂质,然后使用去离子水浸泡并清洗碎片至检测PH为中性,烘干。
[0030]纯度及析晶量检测,除去部分污染较为严重的坩埚碎片,试验证明在不发生硅粘附坩埚的情况下,坩埚纯度均符合使用要求,按照析晶量多少将坩埚碎片分级。
[0031]粗碎酸洗,使用颚式粉碎机将坩埚碎片粉碎至5_左右的石英颗粒,使用盐酸与氢氟酸按照重量百分比1:1.5比例配置成二元混合弱酸溶液,将石英颗粒在弱酸溶液中浸泡I~10小时,可有效去除Al、Fe等金属杂质。酸洗后使用去离子水浸泡清洗至检测pH为中性。
[0032]非晶化处理方式1:对于析晶量不大的原料,粉碎至粒度约100 μ m,使用过筛的办法,将大于IOOym约10%的颗粒去除。此法可有效去除部分石英晶体。
[0033]非晶化处理方式2:对于析晶量较大的原料,将原料高温1750°C熔融,保温2~4小时,然后采用风冷的方式强制快速冷却。
[0034]进一步细碎,加入去离子水,将坩埚碎片采用管式粉碎机湿式粉碎,颗粒度分布为I~50 μ m,加入去离子水量约0.5~lwt%。本发明可采用管式粉碎机对浆料粒度进行较为格严的控制格,粉碎后浆料颗粒按重量百分比组成如下:浆料粒度为I~ΙΟμπι约20%,浆料粒度为10~30 μ m约60%,剩余约20%粒度为30~50 μ m。
[0035]磁选除铁,使用磁选除铁设备对浆料进行除铁处理。
[0036] 制浆,加入有机单体丙烯酰胺,加入量约为0.2wt%,交联剂为亚甲基双丙烯酰胺,加入量约为0.lwt%,催化剂为亚硫酸铵加入量约为0.5wt%,引发剂为过硫酸铵,加入量约为 0.5wt%0
[0037]加入硼酸,加入量为0.5~2wt%,具体加入量视原料的析晶情况定。
[0038]加入柠檬酸,调节浆料的pH,pH在3~5范围较佳。
[0039]真空除气,搅拌。气温(例25°C)下真空压力0.02MPa,搅拌约5小时,真空条件下陈腐2~5小时。
[0040]振动加料,振动频率20Hz,振动时间120秒。
[0041]等静压成型,加料后静置两小时,采用冷等静压机在室温40°C条件下进行等静压成型,采取快速加压的方式压制,并以缓慢泄压的方式进行脱模,最高压力为llOMPa,总时长约20小时。
[0042]晾干,成型胚体在室温60 V,湿度50%的环境下,自然晾干约2小时。
[0043]烧结,在氮气保护气氛下,进行常压烧结。烧结最高温度为1200?,900~1200°C高温段快速烧结。
[0044]虽然本发明已以 较佳实施例揭示如上,然其并非用以限定本发明,任何本领域技术人员,在不脱离本发明的精神和范围内,当可作些许的修改和完善,因此本发明的保护范围当以权利要求书所界定的为准。
多晶硅铸锭后熔融石英坩埚碎片再生方法
- 专利详情
- 全文pdf
- 权力要求
- 说明书
- 法律状态
查看更多专利详情
下载专利文献
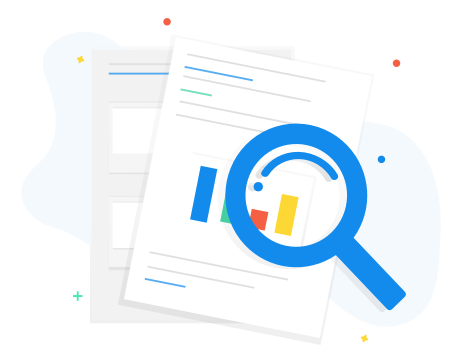
下载专利
同类推荐
-
金凤山金凤山
您可能感兴趣的专利
-
高惠民张龑吴立龙李宗辉
专利相关信息
-
罗尔夫·马丁廖寄乔郭瑞, 熊胜全陈红荣周学刚周学刚