表面多孔碳化硅材料及其制备方法[0002]碳化硅陶瓷由于具有良好耐酸碱腐蚀性、耐磨擦摩损性、高强度、高硬度、良好的抗氧化性能、较高的抗热震性以及在极高的温度下有良好的尺寸性等物理与化学性能,可用于放射性、腐蚀性、剧毒、易燃、易爆、高温等诸多复杂工况条件。因此,在热机工程及机械密封行业中所显示的良好性能和应用潜力已逐步为人们所认识,已经获得了广泛应用。[0003]由于运行时,作为机械密封的密封环端面间始终处于接触并旋转状态,因此要求密封环材料具有良好的耐磨性,并保持流体膜良好的润滑性能和良好的边界润滑性能,以保证工况下有满意的使用寿命。目前工业部门大量应用的是反应烧结碳化硅、常压固相烧结碳化硅。但在干摩擦及硬面对硬面的特殊工况条件下,密封面之间的摩擦磨损加剧、温升较快,容易产生两工作面的粘合,而造成两端面在工作状态下,摩擦系数的增加,导致密封的失效。反应烧结碳化硅密封材料由于有游离硅的存在,因此其耐磨和耐高温性能较差,不适应上述两种工况条件。常压固相烧结碳化硅是一种近纯相的碳化硅材料,但其在干摩擦条件下,耐磨性能也急剧降低。因此,需要开发新型的碳化硅密封材料使其适应上述特殊的工况条件。[0004]现有表面造孔碳化硅密封件多采用特种加工方法如电火花、激光加工、电解加工、超声波加工,电子束加工等来造孔,制备工艺复杂且成本高昂。CN200810060477.3公布了一种常压烧结微孔碳化硅碳 密封环及其制备方法,常压烧结微孔碳化硅石墨自润滑密封环,其原料组成为碳化硅粉90~96%重量,石墨粉2~8%重量,聚乙烯醇2~5%重量。其制造方法包括以下步骤:将各原料按组成称重,把碳硅微粉和石墨微粉混合均匀;将聚乙烯醇加入去离子水中加温溶化,将混合均匀的粉料加聚乙烯醇水溶液搅拌成浆料,常温球磨;将浆料置于喷雾干燥塔中喷雾造粒,再置于模具内压制成型;将成型的制品放入真空高温炉中烧结,降至室温出炉。该材料中含有碳化硅与聚乙烯醇粘结形成的交联孔隙,改善了碳化硅密封环的自润滑性及耐热冲击性,在硬对硬摩擦组合中,能起缓冲作用,降低动磨擦系数,阻止密封环的失效,产品使用寿命延长。
[0005]本发明旨在进一步扩展现有多孔碳化硅材料的类型和方法,本发明提供了一种表面多孔碳化硅材料及其制备方法。[0006]本发明提供了一种表面多孔碳化硅材料的制备方法,所述方法包括: 1)将碳化硅、烧结助剂混合均匀、干燥、过筛制得第一混合粉体,其中以所述碳化硅的含量为100%计,所述烧结助剂的重量百分比为2~IOwt% ;
2)将碳化硅、烧结助剂、造孔剂混合均匀、干燥、过筛制得第二混合粉体,其中所述第二混合粉体中烧结助剂与第一混合粉体中的相同,且烧结助剂和碳化硅的重量比与第一混合粉体的相同,造孔剂占第二混合粉体的体积百分比为5~22%,优选5~20% ;
3)将所述第一混合粉体和第二混合粉体依次加入模具,干压、等静压成型制得表面多孔碳化硅材料的素坯;
4)将所述素坯在600~900°C下热处理脱粘;以及
5)将经脱粘处理的速配在真空或氩气条件下于1900-220(TC烧成。
[0007]较佳地,所述烧结助剂为碳化硼和碳黑的混合物,其中碳化硼和碳黑的质量比为1: (3 ~10)。
[0008]本发明还提供另外一种表面多孔碳化硅材料的制备方法,所述方法包括:
1)将碳化硅、烧结助剂、粘结剂、溶剂混合均匀制得第一浆料,其中以所述碳化硅的含量为100%计,所述烧结助剂的重量百分比为2~10wt%,所述粘结剂的的重量百分比为
3~IOwt % ;
2)将碳化硅、烧结助剂、粘结剂、造孔剂、溶剂混合均匀制得第二浆料,其中所述第二浆料中的烧结助剂、粘结剂分别与第一混合粉体中的相同,且烧结助剂、粘结剂和碳化硅的重量比与第一浆料中的相同,造孔剂占碳化硅、烧结助剂、粘结剂和造孔剂的总体积为5~22%,优选5~20% ;
3)将所述第一浆料和第二浆料依次加入模具注模成型、干燥制得表面多孔碳化硅材料的素还;
4)将所述素坯在600~900°C下热处理脱粘;以及
5)将经脱粘处理的速配在真空或氩气条件下于1900-220(TC烧成。
[0009]较佳地,所述粘结剂包括四甲基氢氧化铵、聚乙烯醇和/或甲基纤维素。
[0010]较佳地,所述溶剂为水或乙醇,所述第一浆料的固含量为50~80wt%,所述第二浆料的固含量为50~80wt%。
[0011]较佳地,所述烧结助剂为氧化铝和氧化钇的混合物,其中氧化铝和氧化钇的质量比为 I:(0.67 ~1.33)。
[0012]较佳地,步骤4)中,热处理的时间为0.5~3小时。
[0013]较佳地,步骤5)中,烧结时间为I~2小时。
[0014]此外,本发明还提供一种根据上述的制备方法制备的表面多孔碳化硅材料,所述多孔碳化硅材料包括致密层、以及与致密层紧密结合的多孔层,所述多孔层中的气孔率为5-22vol %,优选 5 ~20vol %。
[0015]本发明的有益效果:
本发明采用叠层制备工艺制备出表面多孔的碳化硅多孔材料,材料的致密层采用添加烧结助剂的碳化硅原料,多孔层采用添加造孔剂与烧结助剂的碳化硅原料,通过干压或注浆工艺成型,通过脱粘在高温下烧成。本发明的显著特征在于采用添加造孔剂的方式表层造孔,造孔的形貌与体积均可通过添加造孔剂的形貌与添加量控制。且和传统的电火花、激光加工等加工工艺相比具有简单易操作、成本低廉的特点;本发明的另一个显著特征在于制备的材料表层多孔内层致密,且多孔层与致密层之间结合紧密无明显的分界线,制备的材料具有优良的力学性能。
[0017]以下结合附图和下述实施方式进一步说明本发明,应理解,附图及下述实施方式仅用于说明本发明,而非限制本发明。
[0018]表面多孔碳化硅材料具有良好耐酸碱腐蚀性、耐磨擦摩损性、良好的抗氧化性能、优良的耐热水腐蚀性能自润滑性能在化学、冶金、机械密封等领域具有广泛的应用前景。本发明采用叠层制备工艺制备出表面多孔的碳化硅多孔材料,材料的致密层采用添加烧结助剂的碳化硅原料,多孔层采用添加造孔剂与烧结助剂的碳化硅原料,通过干压或注浆工艺成型,通过脱粘在高温下烧成。本发明的显著特征在于采用添加造孔剂的方式表层造孔,造孔的形貌与体积均可通过添加造孔剂的形貌与添加量控制。且和传统的电火花、激光加工等加工工艺相比具有简单易操作、成本低廉的特点;本发明的另一个显著特征在于制备的材料表层多孔内层致密,且致密层、多孔层之间结合紧密无明显的分界线,制备的材料具有优良的力学性能。
[0019]本发明提供了一种单表面多孔的碳化硅材料及其制备方法,制备的材料上层表面为多孔层,下层为致密层,且上下层之间结合紧密无明显的分界线,制备的材料具有优良的力学性能。 [0020]所述的表面多孔的碳化硅材料,多孔材料可以是以碳化硼-碳为烧结助剂的固相烧结碳化硅,也可以是添加氧化铝-氧化钇为烧结助剂的液相烧结碳化硅材料。
[0021]所述的表面多孔的碳化硅材料,多孔层厚度可以通过制备工艺调解,气孔率在5-15νο1% ο
[0022]所述的表面多孔的碳化硅材料,致密层必须与多孔层材料材料体系一致。
[0023]一种单表面多孔的碳化硅材料制备方法,包括以下步骤:
A、采用叠层制备工艺制备出表面含造孔剂、下层不含造孔剂的碳化硅材料素坯;
B、素坯材料在真空或氩气条件下脱粘;
C、脱粘后的坯体在真空或氩气条件下烧成。
[0024]所述的一种单表面多孔的碳化硅材料制备方法,所添加的造孔剂为PMMA等。
[0025]所述的一种单表面多孔的碳化硅材料制备方法,用水或无水乙醇为溶剂,将碳化硅、烧结助剂原料粉体或其与造孔剂的混合粉体充分混合。
[0026]所述的一种单表面多孔的碳化硅材料制备方法,上述原料经过充分混合后,采用干压、直接等静压或直接注模工艺先成型出致密碳化硅,再在其上层制备含造孔剂的复合材料素还。
[0027]所述的一种单表面多孔的碳化硅材料制备方法,复合材料的素坯在真空或气氛条件下,经600-1000°C脱粘。
[0028]所述的一种单表面多孔的碳化硅材料制备方法,脱粘后的坯体在真空或氩气条件下,经1900-2200°C条件下烧成。[0029]表面造孔的无压烧结碳化硅密封件,通过在表面引入微孔作为流体或润滑剂的存储体,帮助促进在滑动元件表面的界面处保持流体膜,从而改善了普通无压烧结SiC的抗摩擦性能,为石油加工工业中经常遇到的有限润滑工况提供了理想解决方案,也可用于硬对硬磨面组合的苛刻应用环境。本发明在新型表面造孔的无压烧结碳化硅密封件的研制过程中,采用一种全新的造孔方法,通过对表面造孔方式、表面含孔的密封材料的烧成工艺研究,实现新型表面造孔的无压烧结碳化硅密封件的制备。
[0030]所述具体制备步骤如下:
1)将碳化硅粉体、造孔剂、烧结助剂原料粉体、和/或分散剂、粘结剂在无水乙醇或去离子水中通过球磨机充分混合均匀,制备出浆料I;
2)将碳化硅粉体、烧结助剂原料粉体、和/或分散剂、粘结剂在无水乙醇或去离子水中通过球磨机充分混合均匀,制备出衆料2 ;
3)将浆料I和2在风箱中干燥或通过喷雾造粒干燥,将烘干的浆料2粉体加入到模具中轻轻预压平整,再加入烘干的浆料I粉体,在20-60MPa下干压成型制备出多孔材料素坯。两种浆料粉体的添加比例可根据实际需要进行调整;
4)或将浆料2倒入石膏模具中吸浆干燥5-60min,再倒入浆料I充分干燥后脱模,制备出多孔材料素还;
5)将制备的多孔材料素坯在真空条件下,600-900°C热处理;
6)脱粘后的坯体 在氩气条件下,经1900-2200°C条件下烧成。
[0031]图1为本发明的一个实施例中采用PMMA为造孔剂制备的表面多孔固相烧结SiC材料形貌,其中,图1中(a)为制得材料的表面形貌,图1中(b)为制得材料的断口形貌;
图2为本发明的一个实施例中采用PMMA为造孔剂制备的表面多孔液相烧结SiC材料形貌,其中图2中(a)为制得材料的断口形貌,图2中(b)为制得材料的表面形貌。
[0032]以下结合附图和下述实施方式进一步说明本发明,应理解,以下实施例只用于对本发明进行进一步说明,不能理解为对本发明保护范围的限制,本领域的技术人员根据本发明的上述内容做出的一些非本质的改进和调整均属于本发明的保护范围。下述示例具体的温度、时间等也仅是合适范围中的一个示例,即、本领域技术人员可以通过本文的说明做合适的范围内选择,而并非要限定于下文示例的具体数值。
[0033]实施例1
将碳化娃、10vol% PMMA、3wt%炭黑和0.6wt%碳化硼等原料在无水乙醇中通过行星球磨机充分混合均匀,制备出浆料,在烘箱中60°C干燥12h,经研磨后过100目筛制得混合粉体I ;将碳化娃、3wt%炭黑和0.6wt%碳化硼等原料在无水乙醇中通过行星球磨机充分混合均匀,制备出浆料,在烘箱中60°C干燥12h,经研磨后过100目筛制得混合粉体2 ;将粉体2与粉体I按重量比1:1先后加入模具中,40MPa下干压成型,后经200MPa等静压成型备出多孔材料素坯。制备的多孔材料素坯在真空条件下,以0.50C /min的升温速率至800°C脱粘,脱粘后的坯体在氩气条件下,经2100°C条件下烧成,制备的材料形貌见图1。从图1的(a)中可以看出,制备的材料一个表面具有气孔,为多孔层所在的表面;从图1的(b)中可以看出,制备的材料,在多孔层上具有气孔。经测量,制备的材料具有非常优良的机械性能,抗折强度为 345.6±61.4MPa,密度为 2.92±0.01g/cm3,气孔率为 10.41±0.05%。
[0034]实施例2将碳化硅、10vol% PMMA、7wt%氧化钇和氧化铝等原料在无水乙醇中通过行星球磨机充分混合均匀,制备出浆料,在烘箱中60°C干燥12h,经研磨后过100目筛制得混合粉体I ;将碳化硅、7wt%氧化钇和氧化铝等原料在无水乙醇中通过行星球磨机充分混合均匀,制备出浆料,在烘箱中60°C干燥12h,经研磨后过100目筛制得混合粉体2 ;将粉体2与粉体I按重量比1:1先后加入模具中,40MPa下干压成型,后经200MPa等静压成型备出多孔材料素坯。制备的多孔材料素坯在真空条件下,以0.5°C /min的升温速率至800°C脱粘,脱粘后的坯体在氩气条件下,经1900°C条件下烧成。制备的具有非常优良的机械性能,抗折强度为547.6±75.3MPa,密度为 2.99±0.07g/cm3,气孔率为 10.00±0.04%。
[0035] 实 施例3
将碳化硅粉体、15vol % PMMA、7wt %氧化钇和氧化铝粉体、1.0wt %四甲基氢氧化铵、
3.0wt %聚乙烯醇等在去离子水中,通过行星球磨机充分混合3h,制备出浆料1,浆料I的固含量为75wt% ;将碳化硅粉体、7wt%氧化钇和氧化铝粉体、l.0wt %四甲基氢氧化铵、
3.0wt %聚乙烯醇等在去离子水中,通过行星球磨机充分混合3h,制备出浆料2,浆料2的固含量为75wt%。将制备的浆料2倒入石膏模中,吸浆20min再倒入浆料1,自然干燥24h取出,放入60°C恒温恒湿烘箱中干燥12h取出,在真空条件下以0.5°C /min的升温速率至800°C脱粘,脱粘后的坯体在氩气条件下,经1900°C条件下烧成,制备的材料形貌见图2。从图2的(b)中可以看出,制备的材料一个表面具有气孔,为多孔层所在的表面;从图2的(a)中可以看出,制备的材料,在多孔层上具有气孔,在致密层上没有气孔。制备的材料抗折强度为 330.6±27.2MPa,气孔率为 21.5±0.03%。
表面多孔碳化硅材料及其制备方法
- 专利详情
- 全文pdf
- 权力要求
- 说明书
- 法律状态
查看更多专利详情
下载专利文献
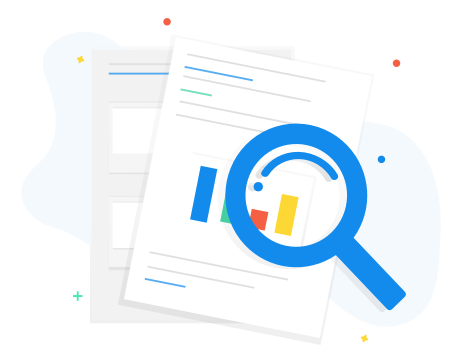
下载专利
同类推荐
-
陈海标, 潘锋陈海标, 潘锋陈海标, 潘锋
您可能感兴趣的专利
-
杨志峰刘建龙邓树军L·T·坎哈姆, C·P·巴雷特何玉明郭兴忠
专利相关信息
-
方宁象姚秀敏陈顺潮, 王铠莎陈顺潮, 王铠莎王亚洲, 王伯初