氮化硅结合碳化硅耐火材料的制备方法【技术领域】。[0002]碳化娃制品属于闻级耐火材料,具有机械强度闻、热导率闻、抗热震性能和耐磨损性好、抗碱侵蚀性优良、抗渣性和抗氧化性优良,以及对部分熔融金属抵抗能力强等特征,已被广泛地应用于钢铁、有色冶金、石油、化学、电力、陶瓷和航空航天等工业领域。碳化硅是强共价键化和物,共价键占88%,其在一般工艺下很难烧结,在烧结时往往需要加入烧结助剂,或者通过第二相结合烧结的方法,才能形成致密的碳化硅烧结体。碳化硅材料的性能也在很大程度上取决于材料中碳化硅颗粒间的结合状况。氮化硅与碳化硅有着相似的化学结构和物理性质,与碳化硅均为强共价键化合物。氮化硅的热膨胀系数小,氧化速度非常慢,高温强度大,体积稳定性好,有良好的导热性,对于多数化学物质都稳定,不被熔融有色金属所侵蚀,是碳化硅理想的结合材料。将氮化硅引入碳化硅内制成氮化硅结合碳化硅材料,在保持了碳化硅固有特性的同时,可以有效地提高碳化硅材料的高温强度、热震稳定性和抗铁水侵蚀能力等性能,而且可以在1200-1450?的较低温度下制备,反应烧结过程为净尺寸烧结,利于制备异形制品,适应大规模工业生产。[0003]反应烧结制备的氮化硅结合碳化硅耐火材料虽然已被广泛应用于钢铁、有色及建材工业,但随着科技的进步,现代工业的工艺技术不断发展,耐火材料所需面对的工作环境越发苛刻,这就对原先使用的耐火的性能提出了更高的要求。氮化硅结合碳化硅耐火材料的生产现在还存在很多问题,如,如何保证硅粉的氮化率、如何控制氮化硅晶相组成、如何防止流硅现象的发生以及如何进一步提高制品强度。[0004]在工业生产中,为了能缩短生产周期,提高氮化率,往往会在原料中加入各种烧结助剂,并在1400°C以上进行烧结。氮化硅结合碳化硅耐火材料制品的强度随氮化硅量增加而提高,但是这种较高的烧结温度限制了原料中硅粉的加入量,如若再原料中添加氮化硅粉则成本会大大提高。在1400°C以上进行烧结,氮化硅会发生α相向β相的晶型转变,烧结助剂也会促进这种转变,而若想制得性能优良的氮化硅结合碳化硅耐火制品,制品中应该含有更多的α相氮化硅。
[0005]为了解决现有技术问题,本发明的目的在于克服已有技术存在的不足,提供一种氮化娃结合碳化娃耐火材料的制备方法,对现有的反应烧结制备氮化娃结合碳化娃耐火制品的方法进行改进和优化,通过调节原料组成和成型密度,在优化过的制度下进行氮化烧结,从而控制金属硅粉和氮气反应的速度以,以实现对材料中氮化硅的含量和晶型的控制及提闻氣化率。[0006] 为达到上述发明创造目的,本发明采用下述技术方案:一种氮化硅结合碳化硅耐火材料的制备方法,包括如下步骤:
①坯料制备:由主要原料和粘结剂充分混合,再经过困料后完成配料,在具体配料时,选用碳化硅和金属硅粉作为主要原料,在主要原料中,碳化硅质量分数为65%~85%,金属硅粉质量分数为15%~35%,碳化硅颗粒与细粉采用特定的级配,选用粒度分别为1.43~
2.5 mm、0.5~1.43 mm、0~0.5 mm和240目的碳化娃粉料,并按照不同粒度由大到小的质量比为2:3:3:2进行配料,金属硅粉的粒度为1000目,粘结剂采用木质素磺酸钙作为主要原料的结合剂,木质素磺酸钙的加入量为主要原料和粘结剂的总质量的3%,木质素磺酸钙与水配成1:1溶液;使用轮碾机进行混料,先将粒度为1.43~2.5 mm、0.5~1.43 mm和O~0.5 mm的碳化硅粉料倒入轮碾机中,混炼5min,然后再向轮碾机中倒入木质素磺酸钙溶液、粒度为240目碳化硅微粉以及粒度为1000目的金属硅粉,混炼40min,而后在接近16°C的条件下经过4~96h困料后,即完成坯料制备;
②素坯成型:将在上述步骤①中完成配料的混合料进行压力成型,得到素胚;在制备素胚时,优选采用干压成型,控制压力可为53~328 MPa,并保压15s ;
③生坯干燥:在40~110°C的温度条件下,对在上述步骤②中制备的素胚进行烘干,得到干燥后的生坯;在制备生坯时,优选的烘干方法是将素坯置于养护箱内依次于40°C、60°C、80°C和 110°C下各保温 6h ;
④生坯排胶:采用高温排胶炉,在200~700°C的温度范围内,对在上述步骤③中制备的生坯在进行排胶;在排胶时,优选控制排胶温度为200~700°C,并优选分别在300°C时和600°C时各保温2h ;
⑤氮化烧结:在1150~1380°C的温度条件下,将在上述步骤④中完成排胶的生坯放入烧结炉中进行36~72h的密封烧结,烧结工艺使用气氛为氮气,氮气纯度> 99.999%,并在烧结炉中维持氮气压力为0.03~0.1MPa,最终得到氮化硅结合碳化硅耐火材料制品;氮化烧结使用的设备优选采用真空电阻炉,即在烧结前,首先将真空电阻炉内抽真空至-0.08~-0.09MPa,然后向真空电阻炉内通入氮气,并维持氮化烧结的氮气气氛;在1150~1380°C的温度条件下,优选地,按照2~:TC /min的升温速度进行升温,氮化烧结采用分段依次烧结,在1150~1200°C范围内保温5~10h,在1200~1300°C范围内保温5~30h,在1300~1380°C范围内保温5~30h ;优选氮化烧结的升温制度为:分段依次进行升温,在O~200°C范围内升温速度为5°C /min,在200~700°C范围内升温速度为3°C /min,在700~1150°C范围内升温速度为5°C /min,在1150~1380°C范围内升温速度为2°C /min。
[0007]本发明与现有技术相比较,具有如下显而易见的突出实质性特点和显著优点:
1.本发明能在各种压力下成型,采用特定粒径的碳化硅作为骨料,通过特定的级配,不仅能在很大的压力范围内干压成型,还能使硅粉得到充分的分散,提高生坯的均匀性;
2.本发明通过控 制成型压力来控制生坯的密度和气孔率,从而控制氮气向材料内扩散的速度,结合调节制品中硅粉的含量来控制反应速度,在避免局部反应放热过多导致硅粉融化的同时,实现对制品中氮化硅的含量和晶型的控制,提高氮化率;
3.本发明在1400°C以下温度进行烧结,减少氮化硅发生α相向β相的晶型转变,制得性能优良的氮化硅结合碳化硅耐火制品,同时降低制备的成本;
4.本发明制备的氮化硅结合碳化硅耐火材料制品在力学性能上有所提高,对原料的要求不高,制备过程简单,成本低廉,烧结温度低,利于实现工业化生产。
[0008]本发明的优选实施例详述如下:
实施例一:
在本实施例中,选用粒度分别为1.43~2.5mm、0.5~1.43mm、O~0.5mm和240目的碳化娃构成级配料,质量比为2:3:3:2,碳化娃质量分数为85%, 1000目娃粉质量分数为15%,各粒度的碳化硅与硅粉纯度≥98%, 240目碳化硅d50为32.718 μ m,1000目硅粉d50为4.694 μ m,木质素磺酸钙不计入总质量,加入量为总质量3%,木质素磺酸钙与水配成1:1溶液。使用轮碾机进行混料,混料时先将1.43~2.5 mm、0.5~1.43 mm和O~0.5 mm的碳化硅倒入轮碾机中,混炼5min,然后倒入木质素磺酸钙溶液、240目碳化硅以及1000目的金属硅粉,混炼40min。混好料后在16°C条件下困料4h,使用四柱液压机干压成型,成型压力53MPa,保压时间15s,制的尺寸为25mmX 25mmX 150mm的样条。样条在恒温恒湿箱中烘干,烘干制度为40°C、60°C、8(rC和110°C各6h。烘干后的式样放入试验炉内,抽真空至-0.08~-0.09MPa,然后通入氮气,氮气纯度≥99.999%,维持氮化烧结的氮气气氛正压0.03~0.1MPa。接通电源加热,O~200°C范围内升温速度为5°C /min ;200~700°C范围内升温速度为2°C /min,其中300°C和600°C下各保温2h进行排胶;700~1150°C范围内升温速度为5°C /min, 1150°〇下保温511 ; 1150~1350°C范围内升温速度为3°C /min, 1200°C下保温5h,1300V下保温20h,1380°C下保温IOh,进行分段氮化烧结。关闭电源,冷却至60V以下,取出样品。烧成后试样无尺寸变化。
[0009]本实施例通过控制成型密度、硅粉掺量和烧结制度来获得具有特定晶型含量和氮化硅含量的氮化硅结合碳化硅耐火材料制品。本实施例方法包括配料、成型、烘干和烧成,具体以碳化硅和硅粉为主要原料,以木质素磺酸钙为结合剂,将原料放入轮碾机中混炼,机压成型,然后在特定制度下烘干,于真空电阻炉中经历排胶和氮化烧结,最终获得力学性能好的特定氮化硅组成和晶型的氮化硅结合碳化硅耐火材料制品。
[0010]实施例二:
本实施例与实施例一基本相同,特别之处在于:
在本实施例中,选用粒度分别为1.43~2.5mm、0.5~1.43mm、O~0.5mm和240目的碳化娃构成级配料,质量比为2:3:3:2,碳化娃质量分数为80%, 1000目娃粉质量分数为20%,各粒度的碳化硅与硅粉纯度≥98%,240目碳化硅d50为32.718 μ m,1000目硅粉d50为4.694 μ m,木质素磺酸钙不计入总质量,加入量为总质量3%,木质素磺酸钙与水配成1:1溶液。使用轮碾机进行混料,混料时先将1.43~2.5 mm、0.5~1.43 mm和O~0.5 mm的碳化硅倒入轮碾机中,混炼5min,然后倒入木质素磺酸钙溶液、240目碳化硅以及1000目的金属硅粉,混炼40min。混好料后在16°C条件下困料10h,使用四柱液压机干压成型,成型压力73MPa,保压时间15s,制的尺寸为25mmX 25mmX 150mm的样条。样条在恒温恒湿箱中烘干,烘干制度为40°C、60°C、8(rC和110°C各6h。烘干后的式样放入试验炉内,抽真空至-0.08~-0.09MPa,然后通入氮气,氮气纯度≥99.999%,维持氮化烧结的氮气气氛正压0.03~0.1MPa。接通电源加热,O~200°C范围内升温速度为5°C /min ;200~700°C范围内升温速度为2V /min,其中300°C和600°C下各保温2h进行排胶;700~1150°C范围内升温速度为5°C /min, 1150°〇下保温511 ; 1150~1350°C范围内升温速度为3°C /min, 1200°C下保温5h,1250°C下保温10h,1300°C下保温20h,1380°C下保温10h,进行分段氮化烧结。关闭电源,冷却至60°C以下,取出样品。烧成后试样无尺寸变化。
[0011]实施例三:
本实施例与前述实施例基本相同,特别之处在于:
在本实施例中,选用粒度分别为1.43~2.5mm、0.5~1.43mm、O~0.5mm和240目的碳化娃构成级配料,质量比为2:3:3:2,碳化娃质量分数为75%, 1000目娃粉质量分数为25%,各粒度的碳化硅与硅粉纯度≥98%,240目碳化硅d50为32.718 μ m,1000目硅粉d50为4.694 μ m,木质素磺酸钙不计入总质量,加入量为总质量3%,木质素磺酸钙与水配成1:1溶液。使用轮碾机进行混料,混料时先将1.43~2.5 mm、0.5~1.43 mm和O~0.5 mm的碳化硅倒入轮碾机中,混炼5min,然后倒入木质素磺酸钙溶液、240目碳化硅以及1000目的金属硅粉,混炼40min。混好料后在16°C条件下困料15h,使用四柱液压机干压成型,成型压力113MPa,保压时间15s,制的尺寸为25mmX 25mmX 150mm的样条。样条在恒温恒湿箱中烘干,烘干制度为40°C、60°C、8(rC和110°C各6h。烘干后的式样放入试验炉内,抽真空至-0.08~-0.09MPa,然后通入氮气,氮气纯度≥99.999%,维持氮化烧结的氮气气氛正压
0.03~0.1MPa。接通电源加热,O~200°C范围内升温速度为5°C /min ;200~700°C范围内升温速度为2°C /min,其中300°C和600°C下各保温2h进行排胶;700~1150°C范围内升温速度为5°C /min,1150°C下保温5h ;1150~1350°C范围内升温速度为3°C /min, 1200°C下保温10h,1250°C下保温10h,1300°C下保温20h,1380°C下保温10h,进行分段氮化烧结。关闭电源,冷却至60°C以下,取出样品。烧成后试样无尺寸变化。
[0012]实施例四:
本实施例与前述实施例基本相同,特别之处在于:
在本实施例中,选用粒度分别为1.43~2.5mm、0.5~1.43mm、O~0.5mm和240目的碳化娃构成级配料,质量比为2:3:3:2,碳化娃质量分数为75%, 1000目娃粉质量分数为25%,各粒度的碳化硅与硅粉纯度≥98%,240目碳化硅d50为32.718 μ m,1000目硅粉d50为4.694 μ m,木质素磺酸钙不计入总质量,加入量为总质量3%,木质素磺酸钙与水配成1:1溶液。使用轮碾机进行混料,混料时先将1.43~2.5 mm、0.5~1.43 mm和O~0.5 mm的碳化硅倒入轮碾机中,混炼5min,然后倒入木质素磺酸钙溶液、240目碳化硅以及1000目的金属硅粉,混炼40min。混好料后在16°C条件下困料15h,使用四柱液压机干压成型,成型压力127MPa,保压时间15s,制的尺寸为25mmX 25mmX 150mm的样条。样条在恒温恒湿箱中烘干,烘干制度为40°C、60°C、8(rC和110°C各6h。烘干后的式样放入试验炉内,抽真空至-0.08~-0.09MPa,然后通入氮气,氮气纯度≥99.999%,维持氮化烧结的氮气气氛正压
0.03~0.1MPa。接通电源加热,O~200°C范围内升温速度为5°C /min ;200~700°C范围内升温速度为2°C /min,其中300°C和600°C下各保温2h进行排胶;700~1150°C范围内升温速度为5°C /min, 1150°C下保温IOh ;1150~1350°C范围内升温速度为3°C /min, 1200°C下保温10h,1300°C下保温15h,1380°C下保温10h,进行分段氮化烧结。关闭电源,冷却至60°C以下,取出样品。烧成后试样无尺寸变化。
[0013]实施例五:
本实施例与前述实施例基本相同,特别之处在于:在本实施例中,选用粒度分别为1.43~2.5mm、0.5~1.43mm、O~0.5mm和240目的碳化娃构成级配料,质量比为2:3:3:2,碳化娃质量分数为75%, 1000目娃粉质量分数为25%,各粒度的碳化硅与硅粉纯度≥98%,240目碳化硅d50为32.718 μ m,1000目硅粉d50为4.694 μ m,木质素磺酸钙不计入总质量,加入量为总质量3%,木质素磺酸钙与水配成1:1溶液。使用轮碾机进行混料,混料时先将1.43~2.5 mm、0.5~1.43 mm和O~0.5 mm的碳化硅倒入轮碾机中,混炼5min,然后倒入木质素磺酸钙溶液、240目碳化硅以及1000目的金属硅粉,混炼40min。混好料后在16°C条件下困料15h,使用四柱液压机干压成型,成型压力177MPa,保压时间15s,制的尺寸为25mmX25mmX 150mm的样条。样条在恒温恒湿箱中烘干,烘干制度为40°C、6(TC、8(rC和110°C各6h。烘干后的式样放入试验炉内,抽真空至-0.08~-0.09MPa,然后通入氮气,氮气纯度≥99.999%,维持氮化烧结的氮气气氛正压
0.03~0.1MPa。接通电源加热,O~200°C范围内升温速度为5°C /min ;200~700°C范围内升温速度为2°C /min,其中300°C和600°C下各保温2h进行排胶;700~1150°C范围内升温速度为5°C /min, 1150°C下保温IOh ;1150~1350°C范围内升温速度为3°C /min, 1200°C下保温10h,1300°C下保温20h,1380°C下保温10h,进行分段氮化烧结。关闭电源,冷却至60°C以下,取出样品。烧成后试样无尺寸变化。
[0014]上面对本发明实施例进行了说明,但本发明不限于上述实施例,还可以根据本发明的发明创造的目的做出多种变化,凡依据本发明技术方案的精神实质和原理下做的改变、修饰、替代、组合、简化,均应为等效的置换方式,只要符合本发明的发明目的,只要不背离本发明氮化硅结合碳化硅耐火材料的制备方法的技术原理和发明构思,都属于本发明的保护范围。
氮化硅结合碳化硅耐火材料的制备方法
- 专利详情
- 全文pdf
- 权力要求
- 说明书
- 法律状态
查看更多专利详情
下载专利文献
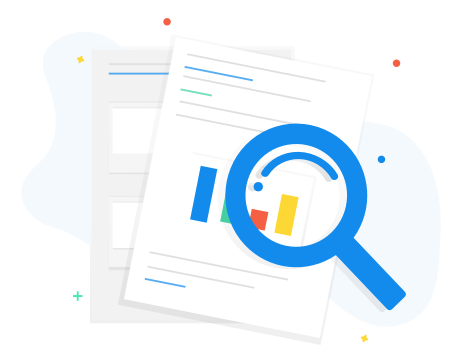
下载专利
同类推荐
您可能感兴趣的专利
专利相关信息
-
邓树军邓树军C·J·黄, A·J·皮兹克陈凯, 陈树德付伟峰, 窦涛付伟峰, 窦涛