专利名称::2.5维编织回转体复合材料成型方法技术领域:。:随着复合材料在航空、航天等领域的广泛运用,对于回转体结构件的需求不断增力口,例如火箭喷管、喷气发动机的喉管、火箭头与排气管等重要机件。对于圆管状、圆锥状和圆台状的回转体织物可以采用三维机织和三维编织的纺织方法实现。目前,采用三维机织方法织造回转体立体织物的技术主要是法国布罗彻于1972年发明的“全自动织造机”设备,并于1986年完成BR900型和BR2000型全自动设备的设计和安装。其织造原理是采用酚醛泡沫塑料芯,保证其外形和圆管织物的内孔形状一致。径向棒由酚醛和碳纤维复合制成的刚性棒,用它插入塑料芯的半径方向,并在塑料芯圆柱面上排成单头等螺距的螺旋线。周向纱喂入径向棒形成的螺旋形通道中。几根周向纱同时喂入通道,形成螺旋形卷绕。径向棒的周向间距相等,把塑料芯的圆周分成若干等分,相邻两排径向棒形成一个梯形通道。轴向纱喂入梯形通道内,每次同时喂入几根周向纱,随着梯形通道的宽度增加,喂入的周向纱根数也增加。轴向纱和周向纱交替喂入梯形通道和螺旋形通道内,形成圆管形织物。采用该技术已生产了上百只三维碳纤维织物产品,大量运用于法国和美国的火箭发动机上的整体型进气喉管和排气锥形管。由于该织造技术是由法国原子能委员会资助,主要用于航天和原子能设备中,所以该设备造价昂贵,维护困难,应用领域单一,不能满足当前复合材料工业生产高性能、低成本复合材料的要求。采用三维编织的方法也可以形成回转体形状的立体织物,其中四步法和两步法使用较多。四步法圆形编织其原理为主体携纱器按周向和径向排成的主体纱阵,其中半径方向的携纱器数称为层数,圆周方向的携纱器数称为列数。附加携纱器间隔排列在主体纱的外围。每一携纱器上携带一根编织纱线。编织过程由行和列的四步间歇运动实现第一步,相邻列的携纱器以相反的方向在径向移动一个携纱器的位置;第二步,相邻层的携纱器以相反的方向在周向移动一个携纱器的位置;第三步,各列携纱器的运动方向与第一步的相反;第四步,各层携纱器的运动方向与第二步的相反。经过四步运动,完成一个机器循环。在一个机器循环中获得的预成型件长度定义为花节长度,重复上述编织步骤,纱线将相互交织而形成一定长度的圆管形预成型件。两步法是将所有纱线分成固定不动的纱线和编织纱线两组。其中固定不动的纱线以立体织物的轴向,在编织物内基本成为一条直线,并按编织物的横截面分布。编织纱线以一定式样在固定纱线之间运动束紧固定纱线,形成圆管形预制件。该方法的具体步骤为第一步,一根编织纱线从最里层运动到最外层,左右相邻两根编织纱线从最外层运动到最里层;第二步,在第一步从最里层运动到最外层的纱线在第二步中从最外层运动到最里层,在第一步中从最外层运动到最里层的纱线在第二步中从最里层运动到最外层,完成一个编织循环。三维编织技术在工艺上的突出特点是能够按照零件的形状和尺寸大小直接编织出回转体复合材料预制件,但由于其织造受到编织机尺寸的限制,目前大多数工业编织机仅能生产小截面(宽度小于100mm)的预制件,而且配套设备占地面积大,成本较高。2.5D(维)编织织物具有成型速度快,可设计性强,织物整体性好,仿形精度高等特点。使用2.5D(维)编织织物作为增强体的复合材料具有质轻、高强度、高模量以及优异的抗破损等优点,被广泛地应用于航天、航空领域,特别是军工武器领域方面。采用2.5D(维)编织技术织造回转体织物能够有效地弥补三维机织和三维编织技术在织造异形结构织物中的不足,并且织造出的预制件其具有较好的综合性能和较高的性价比,较好的满足了当前国际复材料领域对高性能复合材料制造低成本化的需求,受到了普遍关注。目前,回转体复合材料的主要成型方法有RTM和RFI两种方法。RTM(ResinTransferMolding)即树脂传递膜塑工艺,其主要原理是采用注射设备将专用注射树脂(按一定比例配方的不饱和聚脂、催化剂、促进剂的混合物)注入闭合模腔,在模具的型腔里预先放置增强材料预制件,模具周边被紧固和密封,并事先设计又注射及排气系统以保证树脂通畅流动和模腔内气体的顺利排出,使树脂能充分得浸润纤维。模具还需要又加热系统以进行加热固化,最后脱模经抛光、打磨得到复合材料成品。其工艺原理详见文献《树脂传递模塑(RTM)工艺的发展及应用》航天工艺曹运红1998,(3):48_51。RTM工艺具有污染小、成型效率高、成品孔隙率低等优点,已广泛使用于建筑、交通、电讯、卫生、航空、航天等领域。但RTM工艺也有以下几点不足1、传统的RTM成型工艺需要一系列的配套设备予以支持,这些设备包括注射系统、电热式加热器、钢模具、液压机、温度控制系统、真空泵、压力容器等,整套RTM设备配套成本高、占地面积大、维护保养困难;2、由于树脂混合物在泵内经混合后产生化学反应,注射完成后胶液固化使得混合头报废,经常更换成本很高;3、模具密封困难(详见文献《谈RTM技术推广的局限性》玻璃钢/复合材料翟继业等1997,(4)38);4、制品纤维体积含量低,大面积结构复杂的模腔内树脂流动不均衡,气泡缺陷不易排除等(详见文献《RTM工艺国内外研究现状》玻璃钢/复合材料段华军等2000,(5)46)。传统的RTM工艺是针对板块状层合复合材料研制的,随着立体织物的出现,由于其微观结构较板块状层合复合材料复杂,采用传统的RTM工艺已不能满足立体织物的成型要求,尤其对于回转体等复杂形状的复合材料构件。传统RTM工艺在制备板块状层合复合材料时树脂的注射方式是水平方向,即沿着板块的长度或者宽度方向,由于层合复合材料预制件是采用叠加铺放的方式组成的,胶液可以在每层之间顺畅流动,所以水平方向的注胶方式可以满足预制件充分浸润的要求。但对于回转体立体织物,回转体预制件复杂的空间结构以及内部各部分不同的渗透率使得水平注射方式不能充分浸润预制件,复合成型的试验件常出现有气泡和干斑的现象。RFI(ResinFlimInfusion)即树脂膜熔渗工艺,该工艺主要针对高粘度树脂和固体粉末树脂,将预先制备好的树脂膜铺放在涂有脱模剂的低模上,将树脂的厚度由完全渗透和浸湿预制件所需的树脂数量所决定;将干的预制件铺放在树脂膜上,然后依次放置多孔隔板、吸胶材料和透气材料等;按照真空成型工艺的特点将模腔封装,与热环境下采用真空技术将树脂沿着预制件厚度方向抽吸,树脂膜受热后黏度降低,逐渐填满整个预制件空间,随即按照固化工艺制成复合材料成品。其工艺原理详见文献《树脂膜熔渗(RFI)工艺及其发展现状》中国胶粘剂曹魏等2008,17(3):41-46。RFI工艺免去了RTM工艺所需的树脂混合注射设备以及双面模具的加工,无需制备预浸料,具有成型压力低、树脂传递行程短和劳动强度低等特点。RFI工艺适用的树脂需满足一下要求1、树脂基体能在室温条件下成膜,中低温固化;2、所制成的模具有良好的韧性,易弯曲而不破碎且不粘手;3、在工作温度下持续一段时间的低黏度,然后黏度随着文帝的俄升高而增长较快;4、固化温度高于熔融温度,是树脂能够充分浸润预制件;5、熔融时对纤维语之间具有良好的浸润性、浸渗能力、匹配性和粘附性,制件在受力条件下不易发生纤维和树脂间的脱落。RFI工艺的缺点有以下几个1、由于RFI工艺对树脂体系要求过于严格导致满足RFI工艺用的树脂数量极少,从而限制了RFI工艺的发展(详见文献《树脂膜熔渗工艺(RFI)的研究现状》纤维复合材料王东,梁国正2000,35(3):11_14;《树脂膜熔渗工艺及其数值分析方法》玻璃钢/复合材料晏石林,杨梅,谭华2004(2)33-35);2,RFI工艺不适合成型形状复杂的小型制件,如回转体结构。因为回转体织物在织造过程中就附着在回转体模具的芯模之上,树脂膜无法嵌入在模具和预制件之间,从而不能保证树脂在加热融化后沿着回转体的厚度方向浸润织物;3、RFI工艺的树脂用量不能精确,需采用吸胶布等材料吸除多余的树脂,存在一定的浪费现象,工艺流程复杂。
技术领域:。包括以下过程(1)利用由至少4台简易编织方机采用放射性加纱法进行编织;(2)对横截面变化的织物由小端向大端编织;根据模具直径的不同变化,在纬纱圆周方向均匀挂上经纱;(3)将回转体织物竖直放置于模具中;(4)进行从下而上多通道注胶;并实时监测注胶压力,保证注胶加载稳定;(5)通过出胶口兼观察口判断注胶完成;(6)封闭最后一个出胶口,进行模腔保压;(7)固化后处理。该方法及相应的成型设备成本低廉,操作简便,复合快捷,胶液注射均匀,压力可调,树脂体系多样,成品质量良好。文档编号D04C1/00GK101811365SQ20091002511公开日2010年8月25日申请日期2009年2月20日优先权日2009年2月20日发明者刘佳,周光明,张建钟,张立泉,郭洪伟申请人:南京航空航天大学;中材科技股份有限公司
2.5维编织回转体复合材料成型方法
- 专利详情
- 全文pdf
- 权力要求
- 说明书
- 法律状态
查看更多专利详情
下载专利文献
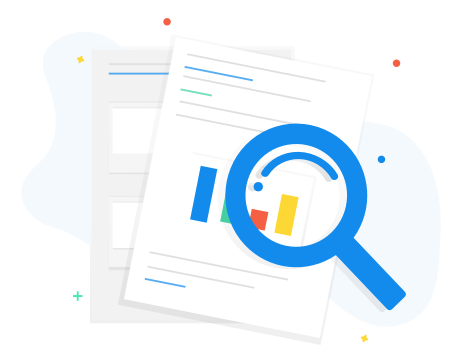
下载专利
同类推荐
-
张春阳, 王国磊张春阳, 王国磊张春阳, 王国磊
您可能感兴趣的专利
-
张春阳, 王国磊张春阳, 王国磊张春阳, 王国磊N·赫费特N·赫费特大内和征
专利相关信息
-
大内和征大内和征黄忠, 刘庆伟黄忠, 刘庆伟黄忠, 刘庆伟黄忠, 刘庆伟