专利名称:烯烃聚合催化剂组分的制备方法本发明涉及一种具有较好活性及形态性质的固体烯烃聚合催化剂组分的制备方法,该组分是采用化学式为〔Mg4(OR)6(R′OH)10〕X的镁化合物来制备的。已经提出了许多通过(ⅰ)一种至少包含有镁、钛及卤素的固体组分同(ⅱ)一种活性有机铝化合物的化合来制备烯烃聚合催化剂的方法。这些烯烃聚合催化剂称为有载体的配位催化剂或催化剂体系。这些催化剂的活性及立体有择性一般能通过下列措施得到改善在固体组分(ⅰ)中加入电子给体(路易斯碱);以及使用一种电子给体作为第三催化剂组分(ⅲ),该电子给体可以同活性有机铝化合物(ⅱ)完全络合或部分络合。为参考方便起见,这里把这种催化剂的含钛固体组分(ⅰ)称为“前催化剂”;把不管是单独使用还是部分地或完全地与一种电子给体络合使用的有机铝化合物(ⅱ)称为“助催化剂”;把不管是单独还是部分或完全同有机铝化合物(ⅱ)络合的电子给体化合物(ⅲ)称为“选择性调节剂”(SCA)。许多专利公开过这种类型的有载体配位催化剂,在现有技术中已公开的这种类型的催化剂体系一般能够高产率地制造烯烃聚合物,同时,供丙烯或高级α-烯烃类聚合的催化剂,对于有规立构的聚合物具有高选择性。尽管如此,对于高有规立构性的聚合物如何进一步改进它们的生产率还正在探索之中。本专业技术人员的目标是要提供一种催化剂体系,该催化剂体系可显示出足够高的活性,使得有可能以高产率生产烯烃聚合物,以致可以排除在脱灰步骤内从聚合物中提取剩余催化剂组分的必要性。在丙烯和高级烯烃的情况下,一个同样重要的目标是对于等规立构的产物或其它有规立构产物提供有足够高的选择性的催化剂体系,以排除从聚合物产物中提取无规聚合物组分的必要性。虽然许多化学组合物可提供活性催化剂体系,但实际上本专业技术人员的考虑已集中在某些较好的组分上。典型的前催化剂包括氯化镁、一般为四价形式的氯化钛,而作为电子给体则包括芳香酯诸如苯甲酸乙酯或对甲苯甲酸乙酯。典型的助催化剂是一种三烷基铝,诸如三乙基铝或三异丁基铝,通常至少部分与选择性调整剂络合使用。典型的选择性调节剂是芳香酯诸如对甲氧基苯甲酸乙酯(茴香酸乙酯)或对甲苯甲酸甲酯。虽然助催化剂和选择性调节剂的选择影响这些催化体系的性能,但看来对体系的活性和生产率的改进有重大影响的组分就是前催化剂。制备这种前催化剂的优选方法见美国专利4,329,253;4,393,182;4,400,302;4,328,328;4,478,952和4,414,132。这种制备前催化剂的典型方法涉及到在卤代烃存在下,镁化合物、四氯化钛、及电子给体的反应。然后使所得的固体颗粒同另外的TiCl4接触,用轻质烃(如异辛烷和异戊烷)将过剩的TiCl4洗去,并将颗粒干燥。如此制备的前催化剂具有卓越的聚合活性(聚合物产率)和立体有择性能(等规立构含量)。尽管如此,对某些应用中,聚合物形态并不理想。已知在烯烃聚合中,聚合物形态同催化剂形态一模一样。再进一步说,前催化剂的形态也依赖于起始镁化合物的形态。因此,如果人们希望得到最佳的催化剂形态(如球体颗粒),使用同样形态的起始镁化合物是令人满意的。在专利文献中已提出许多改进形态的不同方法。一种在GB-A-2,101,610公开的方法涉及到用有机镁化合物同固体颗粒材料反应,用氧气、二氧化碳或羟基化合物处理在载体上的镁组合物,用羰基化合物与该处理过的产物反应,并且同时或相继同过渡金属化合物反应。在美国专利-A-4,465,783中公开的另一种方法涉及喷雾干燥过渡金属组合物或悬浮在液体介质中的过渡金属化合物载体。还有在DE-A-2,839,188公开的另一种方法,它是将固体二醇镁颗粒分散在适宜的液相中,随后喷雾干燥。然而,最后的那种方法并不吸引人,因为分散的固体颗粒会引起喷雾干燥设备细孔的堵塞并淤塞泵系统及计量系统。在US-A-4,540,679中,是使用烃基碳酸镁载体,使镁的醇化物与二氧化碳的悬浮液同过渡金属组分起反应,沉淀出“烃基碳酸镁”载体。包括预聚合及使用三乙基铝(TEA)等各种工艺,是用来除去乙醇和改进生产率的。然而这些工艺并不合乎要求,因为例如预聚合是附加的步骤,而加入TEA会使聚合物产品增添灰分。
上述形态控制的方法全部是从大致球形的非晶态的、非化学计量形状开始的,故特别需要一种改进形态的新方法。
业已找到一种新方法,该方法的独特之处是镁起始物是一种严格按照化学计量的、具有一定形状的结晶化合物,该化合物使得有可能制备既具有很高的生产率及选择性、也具有良好的形态的前催化剂颗粒。
本发明提供一种固体卤化镁/卤化钛催化剂组分的制备方法,以用于α-烯烃类的聚合。该方法包括
a).在一电子给体存在下,使四价钛的卤化物同化学式为〔Mg4(OR)6(R′OH)10〕X的镁化合物接触,式中X是至少一种抗衡离子并且总电荷为-2,R和R′可以相同也可以不同,它们是含有1到4个碳原子的烷基;
b).使所得卤化产物同四价钛的卤化物接触;
c).洗涤该所得产物以除去未反应的钛化合物;
d).回收固体催化剂组分。
在一优选实施例中,镁化合物的化学式为〔Mg4(OCH3)6(CH3OH)10〕Cl2。该化合物的结晶形态本质上属于有规则的正交(rhombic)十二面体。这种结构的优点是,它对于球形表面基本上是切向的。如随后实施例所示,按照本发明的催化剂制得的丙烯聚合物具有高堆积密度,每立方厘米达到或超过0.4克。
如实施例所示,本发明的催化剂也具有各种意料不到的卓越催化性能其中包括高活性、对等规立构结构的高选择性、优良的树脂外形(形态)、低催化衰变性、高堆积密度、单位反应器容积的较高生产率、以及颗粒度小、颗粒度分布范围窄。另一优点是在催化剂中的烷氧基类基团似乎是固定在镁上,而不是象先有技术从乙醇镁制得的催化剂那样固定在钛上,这可有助于解释此催化剂的高活性。
本发明有许多重要方面,其一如上所述,它涉及十二面体结构。附图1示出优选镁化合物的二阳离子的分子结构,其中黑圈是Mg,小圈是甲氧基(OCH3),大圈是甲醇(CH3OH)。注意二个氯离子仅是用于平衡在二阳离子上的正电荷,它对分子结构不是必需的。
另一重要方面涉及制备稳定镁晶体的方法,附图2示出一个甲醇镁、氯化镁和甲醇体系的三元相图。本发明之前,只有狭三角形区ABC才被认为是能用以制取稳定的Mg4(OMe)6Cl2·10MeOH结晶的区域。关于制备此结晶的方法将解释如下。
本发明的另一重要方面涉及从起始镁化合物制备卤化产物,这个卤化反应是,在四价钛的卤化物(例如TiCl4)和一种电子给体(例如一种芳香族羧酸的酯)存在下发生的。如实施例所示,该卤化反应最好也在卤代烃(如氯苯)的存在下发生。
本发明的关键方面包括化学式为〔Mg4(OR)6(ROH)10〕X的镁化合物的使用和制备。在优选实施例中,X选自2Cl-、2I-、2Br-、SO2-4和C2O2-4,特别是2Cl-,而R和R′最好是甲基或乙基,特别是甲基。
有许多制备这样的起始镁化合物的途径。其中之一由Turova等人在Journal of Organomelattic Chemistry,42,9-17页(1972)上发表的文章“烷氧基镁卤化物”中公开。示于附图2中的相图采自Turova文章的图1。
如上所示,在结晶结构中R和R′最好是甲基,而本公开的其余部分见实施例。
Turova等人公开的方法涉及在甲醇中制备MgCl2溶液和在甲醇中制备Mg(OCH3)2,然后,将控制溶液按MgCl2与Mg(OCH3)2的摩尔比为1∶3混合,然后除去甲醇溶剂直至形成结晶。根据需要可加入少量矿脂(“凡士林”油)以改善结晶作用。
这里公开的另一方法涉及使用金属镁MgCl2和甲醇。在此方法中将3当量的Mg溶于MgCl2的甲醇溶液中,以便再一次提供甲醇盐对氯化物为3∶1的摩尔比。
由三相关系图所决定的极为狭窄的稳定范围,将使上述任一方法难于实现商品化。正如Turova等人所讨论的那样,需要极小心控制溶液的浓度和条件来制备稳定结晶结构。这些小心在实验室条件下是可能的,但这样水平的小心在工厂条件下则是很困难的。然而我们已发现可用一种“缓冲”工艺制备这样结构的方法。该工艺优点是运用Si-OCH3键和Si-Cl键具有近乎相等的不稳定性质,可采用SiCl4除去多余的甲醇盐。实际上是在有效氯化物浓度的宽广泛围内缓冲甲醇溶液。此平衡示于下列方程式,其中用一个或多个连续的K1、K2、K3、K4平衡常数(方程式3)来缓冲该溶液
在方程式1中,甲醇镁和甲醇处于溶液内。如条件不合适,则如方程式2所示,发生Mg(OCH3)2、MeOH沉淀。如果浓度极高,此沉淀为〔Mg(OCH3)2〕n。然而,如果将SiCl4(见方程式3)加入此体系,就可能在Turova等人所描述的狭楔形区(ABC))外的宽广浓度范围内进行有效的操作。这可由附图2中D区域表示,D区域是代表以下实施例5和6的有效甲氧基/氯基浓度。此缓冲方法通过AC线向右移动而将楔形区有效地打开。
除了SiCl4外其它物质也可用来缓冲溶液。任何能够提取甲氧基但提供的阴离子不会使晶体形状严重变形的物质均可使用。这些化合物包括四溴化硅、草酸、乙酸和甲酸。
除了Mg(OCH3)2之外,其它起始组分包括含卤素的镁化合物和镁的二醇盐。能作为反应原料的含卤素的镁化合物的例子有烷氧基镁卤化物,诸如异丁氧基氯化镁,乙氧基氯化镁和乙氧基溴化镁。
优选的镁化合物是镁的二醇盐。在这类化合物中,适宜的醇盐基团含有1到4个碳原子。含有这类优选基团的化合物的实例是二异丙醇镁,二乙醇镁、二丁醇镁和乙基异丁醇镁,尤以二甲醇镁为最好。
本发明另一方面包括从结晶中除去一部分(或全部)甲醇。这个操作可在一惰性液体烃,诸如异辛烷中,使结晶沸腾来完成。任何能同甲醇形成共沸物的液体烃都可用。此方法的优点是通过减少微溶的(Cl)(OMe)Ti类化合物的量来降低Ti的含量。
一旦获得镁化合物最佳的均匀颗粒,就需要在复分解反应(消解)中,将该化合物转化为镁的卤化物,诸如在美国专利4,414,132中所公开的那样。
在用四价钛的卤素化合物卤化时,最好使镁化合物反应生成一种卤化镁,其中卤素对镁的原子比至少为1.2∶1。卤化进行得越完全,得到的结果越好,即生产出卤素对镁的原子比至少为1.5∶1的镁的卤化物。最优选的反应是那些能产生完全卤化的反应产物即镁的二卤化物的反应。这样的卤化反应最好在镁化合物对钛化合物摩尔比为0.005∶1至2∶1,最适宜为0.01∶1至1∶1的条件下进行。这些卤化反应是在电子给体存在下,最好也有卤代烃存在下进行,惰性烃烯释剂或溶剂也可存在。当使用一种惰性稀释剂或溶剂时,当然不可用它来完全代替卤代烃,因为如实施例所述,卤化反应最好在一种卤代烃存在下进行。
适宜的四价钛的卤素化合物包括芳氧基卤化物或烷氧基二卤化物和三卤化物,诸如二己氧基-二氯化钛、二乙氧基二溴化钛、异丙氧基三碘化钛和苯氧基三氯化钛;较好的是钛的四卤化物;最好是四氯化钛。
适宜的卤代烃是仅含有一个卤素的化合物,诸如丁基氯和戊基氯,而优选的卤代烃是脂肪族卤代烃,其每分子中含有1到12个碳原子,特别是小于9个碳原子,并含有至少二个卤素原子,诸如二溴甲烷、三氯甲烷、1.2-二氯乙烷、二氯丁烷、1,1,3-三氯乙烷、三氯环己烷、二氯氟代乙烷、三氯丙烷、三氯氟辛烷、二溴二氟癸烷、六氯乙烷和四氯异辛烷。四氯化碳和1,1,3-三氯乙烷是优选的脂肪族卤代烃。芳香族卤代烃也可用,例如氯苯、溴苯、二氯苯、二氯二溴苯、萘基氯、氯甲苯和二氯甲苯,氯苯和二氯苯是优选的芳香族卤代烃。
用于制备固体催化剂组分的适宜电子给体是醚、酯、酮、酚、胺、酰胺、亚胺、腈、膦类、亚磷酸盐、
、胂、磷酰胺和醇化物。适宜的给体涉及例如U.S-A-4,136,243或其等效专利GB-A-1,486,194以及GB-A-1,554,340或其等效专利DE-A-2,729,126的给体。优选的给体是酯、二酯和二胺,特别是芳香族羧酸酯和芳族羧酸二酯,诸如苯甲酸乙酯、苯甲酸甲酯、苯甲酸对甲氧基乙酯、苯甲酸对乙氧基甲酯或苯甲酸对乙氧基乙酯、丙烯酸乙酯、异丁烯酸甲酯、乙酸乙酯、碳酸二甲酯、己二酸二甲酯、邻苯二甲酸异丁酯、富马酸二己酯、马来酸二丁酯、草酸乙基异丙酯、苯甲酸对氯代乙酯、苯甲酸对氨基己酯、环烷酸异丙酯、甲苯甲酸正戊酯、环己酸乙酯、新戊酸丙酯、N,N,N′,N′-四甲基乙烯二胺、1,2,4-三甲基哌嗪和2,2,5,5-四甲基哌啶。电子给体可单独用或混合用。用于制备钛组分的优选电子给体是苯甲酸乙酯和邻苯二甲酸异丁酯。
卤化反应通常会形成一种固体反应产物,该产物可从液体反应介质中通过过滤、倾析或其它适宜方法分离出来,并随后可用一种惰性烃稀释剂诸如正己烷、异辛烷或甲苯洗涤,以便除去任何未反应的物质,其中包括由物理方式吸收的卤代烃。
随后进行卤化,使产物同四价钛的卤素化合物接触、诸如二烷氧基二卤化钛、烷氧基三卤化钛、苯氧基三卤化钛或苯氧基四卤化钛。最好的钛化合物是四卤化钛、特别是四氯化钛。这样处理可增加四价钛在固体催化剂组分中的含量。在固体催化剂的组分中,所增加的四价钛含量最好应足够满足最后的四价钛对镁的原子比从0.005∶1到3.0∶1,特别是从0.02∶1到1∶1。为此目的同四价钛的卤素化合物进行反应最适宜的温度为60°至136℃,接触时间为0.1至6小时,也可选择在有惰性烃或卤代烃稀释剂存在下进行接触。特别好的接触温度是70°至120℃,而最好的接触时间是0.5至3.5小时。进行此处理的方式可为使固体同几份的TiCl4连续接触,TiCl4中应包含有从上述列举中所选出的合适的电子给体。
优选的卤原子,可能是由被卤化的镁化合物所含的卤原子,可能是作卤化剂的钛化合物所含的卤原子,以及与卤化产物接触的四价钛的卤化物中所含的卤原子,是氯。
当用四价钛的卤素化合物处理后,将催化剂组分从液体反应介质中适当地分离出来,洗去未曾反应的钛化合物。最后洗涤过的催化剂组分的钛含量宜为1.5到3.6%(重量),但也可多达4.5%(重量)。
用来洗涤催化剂组分的物质最好是惰性的,轻质液体烃。优选的轻质液体烃是脂族烃、脂环烃和芳香烃。这样的液体例子包括异戊烷、正己烷、异辛烷和甲苯,用异戊烷最好。
在2-6次洗涤中,每次洗涤时轻质烃的用量为每克前催化剂5到100毫升,最好为约25毫升。
所得固体组分是前催化剂,它在聚合过程中同助催化剂和选择调节剂一起使用。
与作为选择调节剂的有机铝化合物一起使用的或与其反应的合适电子给体,是上述那些与制备固体催化剂组分有关的电子给体和硅烷。优选的给体是酯和有机硅化合物。优选的酯是芳香族羧酸酯或芳香族羧酸二酯,诸如上述同制备固体催化剂组分有关的酯。可用的有机硅化合物的例子包括化学通式为R1nSi(OR2)4-n的烷氧基硅烷和酰氧基硅烷,其中n从0到3,R1是一个烃基或一个卤素原子,R2是一个烃基。具体的例子包括三甲基甲氧基硅烷、三苯基乙氧基硅烷、二甲基二甲氧基硅烷和苯基三甲氧基硅烷。在催化剂中作为选择调节剂用的给体可与在制备含钛的催化剂组分中所用的给体相同或不相同。用作选择调节剂的电子给体最好是苯甲酸对乙氧基乙酯、苯乙基三甲氧基硅烷和二苯基二甲氧基硅烷。
用作助催化剂的有机铝化合物可选自烯烃聚合催化剂体系内的任何已知的活化剂,该体系包含卤化钛但最好不含卤素,虽然可采用三烷基铝化合物、二烷基铝卤化物和二烷基铝醇盐,但最好用三烷基铝化合物,特别是那些每一烷基中有2到6个碳原子的三烷基铝化合物,例如,三乙基铝、三正丙基铝、三异丁基铝、三异丙基铝和二丁基正戊基铝。
单独使用、与有机铝化合物联合使用或与有机铝化合物反应时,选择调节剂的比例,按每摩尔铝化合物的摩尔数计算,最好为0.005到1.5,特别是0.1到0.5。按每摩尔Ti的摩尔数计算,选择调节剂的比例最好为0.1到50,特别是0.5到20。
按每摩尔镁的摩尔数计算,含于固体催化剂组分内电子给体的比例宜为0.01到10,最好为0.05到5.0,特别是0.05到0.5。
为了制备最终聚合催化剂组合物,前催化剂、助催化剂和选择调节剂如果单独应用的话,可将其简单地混合,它们的比例最好为使最终催化剂中铝对钛的原子比为1∶1到150∶1,并且以10∶1到150∶1为更好。最好各种组分分别注入反应器内。本发明的催化剂在较低Al∶Ti比例下,例如低于80∶1,甚至低于50∶1时,与同等类型的现有技术催化剂相比,显示出很好的活性。然而,在一些条件下,在较高Al∶Ti比例下使用也可能是有利的。增加Al∶Ti的比例,会增加催化剂的活性,但要以增加未提取的产物中的催化剂残余物为代价。对任何给定方法和所需产物选择Al∶Ti比例时要考虑这些因素,也要考虑所需的全同规整度水平。一般,Al∶Ti比为30∶1到100∶1,特别50∶1到80∶1是有利的。
本发明也涉及一种使用新型催化剂组分和组合物使α-单烯烃诸如乙烯或丁烯、特别是丙烯聚合的方法。聚合可用任何惯用技术进行,诸如气相聚合或使用液体单体或用惰性烃稀释剂作为液体介质的浆状聚合。氢可用来控制聚合物的分子量,而不损害催化剂组合物的立体有择(定向)性能。进行聚合时,可以分批地或连续地向聚合反应器中以恒定或间歇方式加入催化剂组合物或者加入一种或多种催化剂组分。催化剂组合物的活性和立体定向性非常显著,因此不需任何清除催化剂的操作或提取聚合物的技术。在聚合物中的金属残留物的总量诸如化合的铝、镁和钛的总含量可以低到150ppm,甚至低于75ppm。
众所周知,这里所用这种类型的有载体配位前催化剂和催化剂体系,对于催化剂毒物诸如潮气、氧、碳的氧化物、炔属化合物和硫化合物高度敏感并且敏感程度不同。应当了解,在本发明实践中以及在下面实施例中,装置和反应试剂及稀释剂要求全都小心地干燥并清除潜在的催化剂毒物。
前催化剂的生产率是按在一小时或二小时标准的间歇式反应中,以千克聚合物/克前催化剂来确定的;它也可表示为千克聚合物/克钛。催化剂活性有时表示为千克聚合物/克前催化剂/小时。如果按一小时的标准试验确定,则催化剂活性在数字上与生产率相同。
按照美国食品和药品管理局(FDA)的规则,通过测量二甲苯可溶性聚合物(XS)的量来测出全同立构聚丙烯的选择性,XS试验按下列手续进行在一搅拌的烧瓶中,将试样完全溶于含有氧化抑制剂的二甲苯中,在120℃回流下加热,然后将烧瓶不加搅拌浸于25℃的水浴中1小时,在此期间不溶解部分沉淀下来。滤去沉淀物,通过对每10毫升等分滤液的蒸发,真空干燥残渣并称量残渣来测定存在于滤液中的可溶部分。二甲苯可溶部分由带有一些低分子量结晶物质的非晶态物质组成。(FDA规则121.2501和1.1.2510,1971)。
就丙烯均聚物来说,XS的数值典型地比在回流正庚烷中可提取的聚合物量约小2%。因此,聚丙烯的全同立构指数(在回流正庚烷中的不溶解量)大约为100-(XS+2)。
催化剂生产率在标准条件下显示与立体选择性成反比关系。对于任何给定的前催化剂,这种关系是特征性的。通过改变选择调节剂(SCA)的比例,通常有可能将这些变量控制在一些界限之内。在一小时的标准试验中,当增加SCA量时,则会增加对于全同立构聚合物或有规立构聚合物的选择性,但会降低活性,从而降低生产率。
下列实施例用来解释本发明实施例1到6含镁起始物的制备A.使用精确化学计量法制备(即OCH3/Cl=3.0/1)实施例1.(停留在亚稳态的楔形区内)将无水氯化镁溶解于甲醇中并蒸馏出约1/6的溶剂。缓慢加入3.0当量的金属镁,将其保持在温和回流状态,然后使反应继续保持回流直到镁全部消耗掉。静置后,得到南瓜形结晶体和一些灰色粉末的混合物。将该产物在甲醇和异丙醇的混合物中形成淤浆,并倾析出灰色粉末。再用丙醇和异丙醇溶液洗涤后,在流动氮气下干燥该结晶体,得到按总镁量计的回收率为65%(分析结果Mg=15.5%、Cl=12.2%、Mg/Cl=1.85摩尔/摩尔)。母液的大致成分为8.5%Mg(OCH3)2+3.0%MgCl2,是符合三元相图的稳定溶液。
实施例2.(对照例)(由于稀释,离开亚稳态的楔形区)制备手续如实施例1,只是在回流完毕时,将带有足够异丙醇的与甲醇溶液等体积的异辛烷加入热甲醇溶液中,以得到均匀溶液。冷却后,结晶产物的产量根据总镁量计算基本上是定量的(分析结果Mg=14.1%、Cl=10.4%、Mg/Cl=2.0摩尔/摩尔)。与实施例1对照,产物似乎是结晶体形式的混合物。
B.使用过量氯化物制备(即OCH3/Cl<3/1)实施例3.(对照例)(借助于高Cl浓度,使亚稳态的楔形区向外移动)将市售氯化镁溶于市售8%的甲醇镁的甲醇溶液〔每0.95升(美国的夸脱)溶液70克MgCl2中〕,静置过夜后,从溶液中滤去絮凝状的镁,将1.5升澄清溶液与1.5升异辛烷混合,并加入0.8升异丙醇以保证混合均匀。用一聚四氟乙烯浆式搅拌器在230转/分转速下搅拌该溶液。一天以后,收集沉淀物,用异辛烷洗涤并在流动氮气下干燥。按总镁量计,收率为42%(分析结果Mg=15.9%、Cl=22.8%、Mg/Cl=1.0摩尔/摩尔)。产物看起来是在5~30微米范围的完整成形结晶的混合物。
实施例4.(对照例)将无水氯化镁溶于甲醇内,加入1.0当量的镁旋屑以保持温和的回流。继续回流过夜,然后将带有足够异丙醇的与甲醇溶液等体积的异辛烷加入热溶液中,以使溶液均匀。在剧烈搅拌下使溶液冷却,以便得到尺寸范围为20-80微米的球形非晶态产物。按总镁量计收率为81.5%。
C.在SiClx(OCH3)y缓冲剂存在下用过量氯化物制备实施例5.向一个盛1200毫升甲醇溶液的2升锥形烧瓶(Erlenmeyer flask)中,加入每份为5-8克的镁(43克,1.77摩尔)。将溶剂缓慢加热使镁开始溶解,此后,反应热足以维持温和的回流。当所有的镁溶解后,缓慢加入四氯化硅(45克、264毫摩尔;按总氯量计,过量20%)(由于发生颇为放热的酸/碱反应)。将两份这样制备的溶液合
并蒸馏出足够的甲醇,使总体积成为1.6到1.7升。将热溶液‘A’倒入装备有大叶片浆式搅拌器和不锈钢档板的2升反应壶中,在高速度下搅拌,直到溶液冷却,并得到大量小晶体。将晶体收集于粗多孔漏斗中,用500克异辛烷/150克异丙醇混合物洗涤二次,用异辛烷洗涤二次,在流动氮气下干燥20分钟。产量为420克(71%)。用可见和扫描电子显微镜检验,显示该产物的形状为正交十二面体的均匀结晶型。
实施例6.将上述例5中的105克热溶液A同6克甲苯混合,得到一清澈溶液。搅拌过夜后得到8.1克形状为正交十二面体、完整成形的透明结晶。
以上在实施例1中所制备的结晶说明了本发明的制备法,并得到良好的催化剂。实施例2的操作是在楔形区ABC之外,并未制得良好的催化剂,同样实施例3和4也在本发明之外。实施例5和6是按照本发明所描述的缓冲体系。
实施例7到17前催化剂的制备前催化剂的制备法如下将电子给体(类型和数量见表1)同150毫升体积比为1∶1(V/V)的四氯化钛和氯苯的混合物一起加入到50毫摩尔的适宜镁起始物(表1)中,在室温下搅拌15分钟,然后将该溶液于110℃下搅拌一小时并趁热过滤。将残留物固体在150毫升的四氯化钛/氯苯为1∶1溶液中制成淤浆,加入0.2到0.4毫升的邻苯二甲酰氯(US-A-4,535,068),在110℃下将该淤浆搅拌30-60分钟。趁热过滤后,将固体在150毫升的四氯化钛/氯苯为1∶1溶液中制成淤浆,在110℃下搅拌30分钟并趁热过滤。使反应容器冷至40℃以下,此固体用每份为150毫升的异戊烷洗涤6次,然后在40℃和流动氮气下干燥100分钟。各种前催化剂的钛含量见表1。实施例11到13是对照例。
(表1见下页)
表1前催化剂 镁起始物 电子给体 钛实施例 实施例 (毫摩尔) (%重量) 註释7 1 iBP(9.7) 3.44 将镁起始8 1 iBP(6.0) 4.63 物在异辛9 1 iBP(7.5) 4.06 烷中加热10 1 MpT(16.7) 5.30 沸腾1小11 2 iBP(7.6) 4.10 时,以除12 3 iBP(17.3) 4.98 去92%的13 4 iBP(11.1) 4.81 结合甲醇。
14 5 iBP(9.9) 4.6715 5 iBP(8.7) 2.0016 5 iBP(8.7) 4.4917 6 iBP(8.7) 4.04iBP=邻苯二甲酸异丁酯MpT=对甲苯甲酸甲酯实施例18到33液体沉淀(LlPP)和气相丙烯聚合使用2.7升丙烯、132毫摩尔氢气和能提供8微摩尔钛的足量催化剂,在一只3.8升(1美国加仑)高压釜中,于67℃下进行LlPP聚合2小时。使三乙基铝(70摩尔/摩尔Ti)同17.5毫摩尔的SCA(实施例23用对乙氧基苯甲酸乙酯,其它实施例用二苯基二甲氧基硅烷)混合,或者在注入前同前催化剂预混合5到30分钟;或者在前催化剂注入之前直接注入高压釜中去。
在一只15升(4美加仑)配备有螺条搅拌器的高压釜中,将丙烯以10克/分钟流速,压力为300磅/平方英寸(表压),温度为67℃,进行气相聚合2小时。在高压釜中充满气流后,将SCA(17.5摩尔/摩尔钛)注入釜中,随后注入三乙基铝(70摩尔/摩尔钛),最后注入前催化剂(足够提供8微摩尔的钛)。
结果见表2。注意实施例24到26是对照实施例,所用催化剂是从不纯的Mg4(OMe)6(MeOH)10Cl2的氯代甲醇镁制备的,这就是为什么它们的生产率比其它用以说明液相聚合的实施例低得多的原因。
表2聚合 催化剂 生产率 X.S. 相实施例 实施例 (公斤聚丙烯/克 (%重量) (g/l) 形态细节催化剂)18 7 44.7 6.8 l19 7 24.0 4.5 g 0.37b.d.,84.5%的聚合物为0.25-2.0毫米20 8 40.6 9.1 l 0.32b.d.,85.6%的聚合物为0.50-2.0毫米21 8 20.4 13.8 g 0.35b.d.,88.6%的聚合物为0.50-2.0毫米22 9 40.9 6.1 l 0.39b.d.,87.1%的聚合物为0.25-2.0毫米23 10 18.8(1小时) 7.9 l24 11 24.9 6.5 l25 12 6.0 8.5 l26 13 10.5 9.7 l27 14 66.1 7.2 l 0.43b.d28 14 15.8 5.4 g
表2(续)聚合 催化剂 生产率 X.S. 相实施例 实施例 (公斤聚丙烯/克 (%重量) (g/l) 形态细节催化剂)29 15 34.3 3.4 l 0.37b.d.,84.3%的聚合物为0.25-2.0毫米30 15 10.2 2.0 g31 16 46.1 6.2 l 0.39b.d.,80.7%的聚合物为0.5-2.0毫米32 17 63.9 7.5 l 0.36b.d.
33 17 20.9 5.4 g注“g”是气相聚合“l”是液相聚合“b.d”是堆积密度
通过化学式为[Mg
烯烃聚合催化剂组分的制备方法
- 专利详情
- 全文pdf
- 权力要求
- 说明书
- 法律状态
查看更多专利详情
下载专利文献
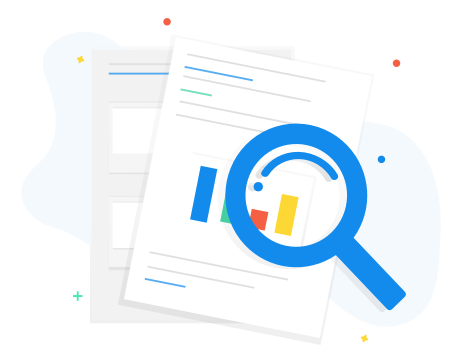
下载专利
同类推荐
-
丁建松J·洛伊克尔施惠栋, 谢宗传施惠栋, 谢宗传J·J·里昂哈德, W·穆勒J·J·里昂哈德, W·穆勒
您可能感兴趣的专利
-
S·V·波罗达伊夫S·V·波罗达伊夫刘世勇, 刘固寰住田宽人詹姆斯·E·西利二世
专利相关信息
-
詹姆斯·E·西利二世杜建忠, 刘秋明杜建忠, 刘秋明A·查特基D·瓦诺潘