一种新型转炉自动挡渣滑动水口用滑板砖及其制备方法[0002]随着钢铁行业的迅速发展,用户对钢材质量的要求日益提高。因此,生产高质量、高技术含量、高附加值的优钢产品成为钢铁企业的必然选择。钢水质量直接影响钢材的性能。减少转炉出钢过程中的下渣量是提高钢水质量的一个重要环节。转炉出钢过程中如何降低下渣量是长期困扰钢铁行业的技术难题,已经成为转炉冶炼特钢、优钢的制约因素。转炉炼钢生产中,炉内冶炼时产生大量熔融状态的炉渣。这些炉渣会随着转炉的出钢流入钢包内,造成不利影响:影响钢包耐火材料的寿命;造成钢水回硫、回磷,影响钢水质量;增加炉后铁合金的消耗;增加后续工序合成渣的用量;延长精炼工序处理时间。[0003]早在2000年,卢森堡、德国、日本等国家钢铁企业就在转炉上采用在大型钢包滑动水口技术。鉴于该滑动水口挡渣技术在减少钢水回磷、提高合金收得率、减少钢中夹杂物、提高钢水清洁度、减少钢包粘渣、延长钢包使用寿命等方面的突出优点。国内福建三钢、上海宝钢、莱钢型钢、安阳钢厂等钢企先后采用该技术,取得了较好的使用效果。国民经济的发展带动了钢材消费结构的变化。目前,越来越多的企业采用转炉生产特殊钢,这对低成本生产高洁净度钢水提出了越来越高的要求。就转炉炼钢生产企业而言,为生产IF钢、石油管线钢、硅钢、轴承钢、弹簧钢等高附加值钢材,减少转炉出钢时的下渣量是提高钢水洁净度,从而提高转炉钢产品的质量和档次,降低其生产成本最有效的途径,在此背景下转炉滑动水口挡渣新技术应运而生。[0004]1970年新日铁发明了挡渣球,利用其比重介于钢渣之间,在出钢将完时堵住出钢口以阻断渣流入钢包 内。在此基础上,各国钢铁企业在不断探索新的挡渣技术,先后开发了十几种挡渣方法,包括挡渣塞、气动挡渣和闸阀挡渣等。德国Salzg-1tte钢厂210吨转炉使用一种在出钢口末端用液压闸门的挡渣装置,其挡渣效果与挡渣球相比,钢包下渣量减少了 70%。国内使用闸阀式挡渣技术的钢厂极少。宝山钢铁股份公司第一炼钢厂3座转炉投产时使用挡渣球挡渣,第二炼钢厂2座转炉投产时采取气动挡渣。2006年宝钢在5座转炉上全部改用挡渣塞挡渣。2008年11月份,宝钢向国内某公司购买了转炉滑板闸阀式挡渣技术,在一炼钢3号300吨转炉进行了试验,取得了良好的挡渣效果。宝山钢铁股份公司第一炼钢厂3座转炉投产时使用挡渣球挡渣,第二炼钢厂2座转炉投产时采取气动挡渣。2006年宝钢在5座转炉上全部改用挡渣塞挡渣。2008年11月份,宝钢向国内某公司购买了转炉滑板闸阀式挡渣技术,在一炼钢3号300吨转炉进行了试验,取得了良好的挡渣效果。[0005]常用挡渣的工作原理和使用效果如下:挡渣帽的工作原理为出钢开始时炉渣先经过出钢口,利用挡渣帽封闭出钢口,使用时挡渣帽对前渣有一定的挡渣效果,对中、后期下渣控制无效;软质挡渣塞的工作原理为利用软质挡渣塞封闭出钢口,特殊材料的软质挡渣塞在炉渣先通过出钢口后爆裂,使用时软质挡渣塞能够有效地防止出钢前期下渣,对中后期下渣控制无效;挡渣球的工作原理为利用挡渣球密度介于渣钢之间(一般为4.2~4.5g/cm3),在出钢结束时堵住出钢口,以阻断转炉渣进入钢包内,使用时挡渣球对前、中期下渣控制无效,操作简单、成本低廉、挡渣命中率高(50%~70%),挡渣球在转炉内是以随波逐流的方式运动到出钢口,挡渣不可靠;挡渣镖的工作原理为利用导向杆将半球形挡渣塞准确定位到出钢口,基本原理与挡渣球相似,使用时挡渣镖对前期下渣控制无效,与挡渣球相t匕,可灵活调节比重,能自动准确到达预定位置,具有一定的抑制中期涡流卷渣效果,对后期下渣挡渣成功率可达90%以上;电磁法的工作原理为通过产生的磁场使钢水变细,使出钢口上方钢液产生的吸入涡流高度降低,可有效防止炉渣流出出钢口,使用时电磁法出钢时间长,大型转炉出钢时间需15分钟以上,劳动生产率大大降低;滑动水口法的工作原理为以机械或液压方式开启或关闭出钢口,以达到挡渣目的,使用时滑动水口法可以最有效地控制前期和后期下渣,挡渣成功率可以达到100%,挡渣效果良好,但其装置设备复杂,成本较高,安装拆卸均不方便;气动法的工作原理为采用了炉渣流出检测装置,由发送和接收信号的元件及信号处理器件构成,通过二次线圈产生的电压变化,即可测出钢水流过出钢口流量的变化,能准确地控制挡渣时间,使用时气动法对前期下渣控制无效,在迅速性、可靠性和费用等方面有明显优势。但出钢时发生吸入涡流引起钢渣混出时,挡渣时机不好掌握,且工作环境恶劣,部件更换频繁;红外线下渣检测的工作原理为利用不同物质在不同温度下发出的红外波长不同,分辨钢水和炉渣,使用时红外线下渣检测在迅速性、可靠性和费用等方面有明显优势,但不能阻止转炉下渣。[0006]转炉出钢口用滑动水口,包括出钢口内水口,出钢口上下滑板和出钢口外水口。其工作原理类似于钢包滑动水口控流系统,安装在转炉出钢口本体外部,通过液压驱动系统和自动下渣检测系统控制滑板自动开启和关闭,实现少渣、无渣出钢的目的。转炉出钢口滑板在出钢过程中,要经历高温钢水、钢渣的强力冲刷,频繁挡渣操作过程中滑板铸孔和滑道要承受高温钢水、钢渣的磨蚀和熔损,冶炼过程中铸孔处于全开状态,受到高温烈焰的直接冲击氧化,不连续放钢导致滑板经受1600°C高温强热震冲击;所以转炉出钢口滑板的损毁方式为钢水、钢渣的冲刷侵蚀扩径、高温烈焰的冲击氧化,滑动面的拉毛磨损、频繁高低温转换导致的热震裂纹等 。故转炉滑板要求材质必须具备较好的高温抗折强度、优良的热震稳定性、较好的抗渣侵蚀性和较好的高温抗氧化性能。
[0007]本发明的目的是针对现有技术存在的问题,提供一种具备较好的高温抗折强度、优良的热震稳定性、较好的抗渣侵蚀性和较好的高温抗氧化性能的新型转炉自动挡渣滑动水口用滑板砖及其制备方法。
[0008]本发明的目的是通过以下技术方案解决的:
一种新型转炉自动挡渣滑动水口用滑板砖,其特征在于:该滑板砖中各组分的重量百分含量为:58%~68%的板状刚玉、6%~8%的98镁砂、8%~11%的电熔尖晶石、3%~5%的石墨、4%~7%的a-氧化铝微粉、1%~2%的烧结剂、4%~7%的铝硅合金粉和4%~5%的树脂。
[0009]所述的各组分的颗粒级配:板状刚玉颗粒直径为(2~1、I~0)mm、98镁砂直径为I~0_、电熔尖晶石为325目、石墨为180目、a-氧化招微粉为I μ m。
[0010]所述板状刚玉的颗粒级配按重量百分含量为:2~1mm,30% ~35% ;
I ~0mm,28% ~33%。
[0011]一种新型转炉自动挡渣滑动水口用滑板砖的制备方法,其特征在于:该滑板砖中各组分的重量百分含量为:58%~68%的板状刚玉、6%~8%的98镁砂、8%~11%的电熔尖晶石、3%~5%的石墨、4%~7%的a-氧化铝微粉、1%~2%的烧结剂、4%~7%的铝硅合金粉和4%~5%的树脂;该制备方法的步骤如下:
a、混练:将各组分按上述配比混合后进行均匀搅拌获得泥料;
b、成型:把称量好的泥料加入模具内,由摩擦压机机压成型并自然干燥获得砖坯;
C、干燥:将砖坯放入窑中缓慢升温干燥30~40小时,干燥温度不超过200°C ;
d、烧成:将窑温自干燥温度匀速升温至970~1030°C并保温12~15小时;
e、油浸:将烧成后的砖坯在温度为200~240°C、压力为1.2~1.3Mpa的环境下油浸6~8小时;
f、焙烧:将油浸后的砖坯放入窑中,将窑温缓慢升温至680~720°C,保温12~15小时后自然冷却至室温;
g、机加工:将焙烧后的砖坯进行打箍、套壳、磨床、包装后即制得所需的新型转炉自动挡渣滑动水口用滑板砖。
[0012]所述步骤a中的混练过程为:混练机开机后首先投入颗粒料板状刚玉和98镁砂,3~5分钟后加入树脂,经过8~10分钟混匀后投入细粉料电熔尖晶石、石墨、a-氧化铝微粉、烧结剂和铝硅合金粉,再搅拌8~10分钟后开始加压15~25分钟,加压完成后提升碾轮出料。
[0013]所述步骤a中的混练过程中混练机的温度要保持在20~35°C。
[0014]所述步骤c中的缓慢升温干燥过程为:20~25小时内将窑温均匀升温到180~200°C后保温10~15小时。
[0015]所述步骤d中的烧成过程为:20~25小时内将窑温自干燥温度匀速升温至970~1030°C并保温12~15小时。
[0016]所述步骤f中的焙烧过程为:20~25小时内将窑温匀速升温至680~720°C后保温12~15小时。
[0017]所述的各组分的颗粒级配:板状刚玉颗粒直径为(2~1、1~0)mm、98镁砂直径为I~0_、电熔尖晶石为325目、石墨为180目、a-氧化招微粉为I μ m。
[0018]本发明相比现有技术有如下优点:
本发明通过调整滑板砖的配方、简化滑板砖的生产工艺,进一步提高了滑板砖的综合性能,使其具备较好的高温抗折强度、优良的热震稳定性、较好的抗渣侵蚀性和较好的高温抗氧化性能。
[0019]本发明的滑板砖有效地减少了转炉出钢下 渣量,使顶渣的改质石灰和合成渣的用量必然降低,其中炉后石灰耗由3 kg/t降低1.6kg/t ;出钢口、钢包寿命得到进一步提高,出钢口寿命高达150炉,使用该滑板砖后,降低成本8.51元/吨钢,但设备增加成本3.89元/吨钢、耐材增加在本2.19元/吨钢,故采用该滑板砖的无渣出钢直接效益为2.43元/吨钢,按按年产500万吨钢计算,可创直接经济效益1215万元。
[0020]本发明的滑板砖为优质钢种开发提供了有利条件,减少废品,提高质量,避免下渣回磷造成的钢水回炉,废品,并大幅度减少钢中的夹杂物,提高钢水的质量;实现钢水的窄成份和窄温度控制,生产优质品种钢的质量合格率高而稳定;提高出钢口、钢包耐材寿命;减轻炉下清渣劳动强度;出钢时间稳定,便于生产周期和出钢温度的控制。
[0021]本发明的滑板砖使用时降低了合金、石灰及耐材等原材料的消耗,符合国家节能减排的产业政策;且钢产量达到饱和而出现竞争格局时,各钢铁企业将会逐步转向重视质量和成本的轨道,必将选择利润比较稳定的优质钢生产;该滑板砖满足优质钢材料高质量、低成本的要求,为转炉流程生产优质钢提供保证,同时实现了出钢过程自动化,因此该滑板砖具有十分广阔的推广应用前景,具有显著的经济社会效益。
[0022]下面通过实施例对本发明作进一步的说明。
[0023]一种新型转炉自动挡渣滑动水口用滑板砖,该滑板砖中各组分的重量百分含量为:58%~68%的板状刚玉、6%~8%的98镁砂、8%~11%的电熔尖晶石、3%~5%的石墨、4%~7%的a-氧化铝微粉、1%~2%的烧结剂、4%~7%的铝硅合金粉和4%~5%的树脂;上述各组分的颗粒级配:板状刚玉颗粒直径为(2~1、1~O) mm、98镁砂直径为I~0mm、电熔尖晶石为325目、石墨为180目、a-氧化招微粉为1 μM;其中板状刚玉的颗粒级配按重量百分含量为:2~1mm的板状刚玉30%~35%,I~Omm的板状刚玉28%~33%。烧结剂可选用新乡熔鑫耐材有限公司生产的产品。
[0024]一种新型转炉自动挡渣滑动水口用滑板砖的制备方法,该滑板砖中各组分的重量百分含量为:58%~68%的板状刚玉、6%~8%的98镁砂、8%~11%的电熔尖晶石、3%~5%的石墨、4%~7%的a-氧化铝微粉、1%~2%的烧结剂、4%~7%的铝硅合金粉和4%~5%的树脂,各组分的颗粒级配:板状刚玉颗粒直径为(2~1、1~0)mm、98镁砂直径为1~0mm、电熔尖晶石为325目、石墨为180目、a-氧化铝微粉为I μ m,其中板状刚玉的颗粒级配按重量百分含量为:2~Imm的板状刚玉30%~35%,1~Omm的板状刚玉28%~33% ;该制备方法的步骤如下:a、混练:将各组分按上述配比混合后进行均匀搅拌获得泥料,混练的具体过程为:混练机开机后首先投入颗粒料板状刚玉和98镁砂,3~5分钟后加入树脂,经过8~10分钟混匀后投入细粉料电熔尖晶石、石墨、a-氧化铝微粉、烧结剂和铝硅合金粉,再搅拌8~10分钟后开始加压15~25分钟,加压完成后提升碾轮出料,另外混练机的温度要保持在20~35°C;b、成型:根据砖形图纸把模具安装好,成型前,按预先计算理论体积密度称取相应的泥料重量,确定砖坯成型加压强度,打击次数和成型压力,检测有无裂纹、缺棱、缺角、熔洞、夹层等不合格产品,然后把称量好的泥料加入模具内,由摩擦压机机压成型并自然干燥获得砖坯;c、干燥:将砖坯放入窑中缓慢升温干燥30~40小时,干燥温度不超过200°C,具体缓慢升温干燥过程为:20~25小时内将窑温均匀升温到180~200°C后保温10~15小时;d、烧成:将窑温自干燥温度匀速升温至970~1030°C并保温12~15小时,具体过程为:20~25小时内将窑温自干燥温度匀速升温至970~1030°C并保温12~15小时;e、油浸:将烧成后的砖坯在温度为200~240°C、压力为1.2~1.3Mpa的环境下油浸6~8小时;f、焙烧:将油浸后的砖坯放入窑中,将窑温缓慢升温至680~720°C,保温12~15小时后自然冷却至室温,具体焙烧过程为:20~25小时内将窑温匀速升温至680~720°C后保温12~15小时;g、机加工:将焙烧后的砖坯进行打箍、套壳、磨床、包装后即制得所需的新型转炉自动挡渣滑动水口用滑板砖。
[0025]实施例一
一种新型转炉自动挡渣滑动水口用滑板砖的制备方法,选取重量百分含量为:颗粒直径为2~Imm的板状刚玉30%、颗粒直径为I~Omm的板状刚玉33%、颗粒直径为I~Omm的98镁砂6%、325目的电熔尖晶石8%、180目的石墨4%、I μ m的a_氧化铝微粉4%、烧结剂1%、铝硅合金粉5%和4%的树脂,按照每机500公斤的搅拌量进行配料,首先打开自动化调压升降式混练机,接着投入颗粒料板状刚玉和98镁砂,3分钟后加入树脂,经过8~10分钟混匀后投入细粉料电熔尖晶石、石墨、a-氧化铝微粉、烧结剂和铝硅合金粉,再搅拌8~10分钟后开始加压25分钟,加压完成后提升碾轮出料即获得泥料,另外混练机的温度要保持在28°C ;根据砖形图纸把模具安装好,成型前,按预先计算理论体积密度称取相应的泥料重量,确定砖坯成型加压强度,打击次数和成型压力,检测有无裂纹、缺棱、缺角、熔洞、夹层等不合格产品,然后把称量好的泥料加入模具内,采用高吨位自动化摩擦压机成型以确保砖坯的稳定性并自然干燥获得砖坯;将砖坯放入窑中,在20小时内将窑温均匀升温到180°C后保温15小时进行干燥;在25小时内将窑温自干燥温度匀速升温至100(TC并保温14小时进行烧结;将烧成后的砖坯在温度为200~240°C、压力为1.2~1.3Mpa的环境下油浸6~8小时;将油浸后的砖坯放入窑中,在20小时内将窑温缓慢升温至720°C,保温13小时后进行焙烧,焙烧完成后自然冷却至室温;将焙烧后的砖坯进行打箍、套壳、磨床、包装等机加工过程,即制得所需的新型转炉自动挡渣滑动水口用滑板砖。
[0026]实施例二
一种新型转炉自动挡渣滑动水口用滑板砖的制备方法,选取重量百分含量为:颗粒直径为2~Imm的板状刚玉32%、颗粒直径为I~Omm的板状刚玉28%、颗粒直径为I~Omm的98镁砂7%、325目的电熔尖晶石10%、180目的石墨5%、I μ m的a_氧化铝微粉6%、烧结剂2%、铝硅合金粉6%和5%的树脂,按照每机500公斤的搅拌量进行配料,首先打开自动化调压升降式混练机,接着投入颗粒料板状刚玉和98镁砂,4分钟后加入树脂,经过8~10分钟混匀后投入细粉料电熔尖晶石、石墨、a-氧化铝微粉、烧结剂和铝硅合金粉,再搅拌8~10分钟后开始加压20分钟,加压完成后提升碾轮出料即获得泥料,另外混练机的温度要保持在25°C ;根据砖形图纸把模具安装好,成型前,按预先计算理论体积密度称取相应的泥料重量,确定砖坯成型加压强度,打击次数和成型压力,检测有无裂纹、缺棱、缺角、熔洞、夹层等不合格产品,然后把称量好的泥料加入模具内,采用高吨位自动化摩擦压机成型以确保砖坯的稳定性并自然干燥获得砖坯;将砖坯放入窑中,在22小时内将窑温均匀升温到190°C后保温12小时进行干燥;在24小时内将窑温自干燥温度匀速升温至1030°C并保温12小时进行烧结;将烧成后的砖坯在温度为200~240°C、压力为1.2~1.3Mpa的环境下油浸6~8小时;将油浸后的砖坯放入窑中,在25小时内将窑温缓慢升温至700°C,保温15小时后进行焙烧,焙烧完成后自然冷却至室温;将焙烧后的砖坯进行打箍、套壳、磨床、包装等机加工过程,即制得所需的新型转炉自动挡渣滑动水口用滑板砖。
[0027]实施例三
一种新型转炉自动挡渣滑动水口用滑板砖的制备方法,选取重量百分含量为:颗粒直径为2~Imm的板状刚玉35%、颗粒直径为I~Omm的板状刚玉30%、颗粒直径为I~Omm的98镁砂8%、325目的电熔尖晶石11%、180目的石墨5%、I μ m的a_氧化铝微粉5%、烧结剂1.5%、铝硅合金粉7%和4%的树脂,按照每机500公斤的搅拌量进行配料,首先打开自动化调压升降式混练机,接着投入颗粒料板状刚玉和98镁砂,5分钟后加入树脂,经过8~10分钟混匀后投入细粉料电熔尖晶石、石墨、a-氧化铝微粉、烧结剂和铝硅合金粉,再搅拌8~10分钟后开始加压15分钟,加压完成后提升碾轮出料即获得泥料,另外混练机的温度要保持在30°C ;根据砖形图纸把模具安装好,成型前,按预先计算理论体积密度称取相应的泥料重量,确定砖坯成型加压强度,打击次数和成型压力,检测有无裂纹、缺棱、缺角、熔洞、夹层等不合格产品,然后把称量好的泥料加入模具内,采用高吨位自动化摩擦压机成型以确保砖坯的稳定性并自然干燥获得砖坯;将砖坯放入窑中,在25小时内将窑温均匀升温到200°C后保温10小时进行干燥;在20小时内将窑温自干燥温度匀速升温至970°C并保温15小时进行烧结;将烧成后的砖坯在温度为200~240°C、压力为1.2~1.3Mpa的环境下油浸6~8小时;将油浸后的砖坯放入窑中,在23小时内将窑温缓慢升温至680°C,保温12小时后进行焙烧,焙烧完成后自然冷却至室温;将焙烧后的砖坯进行打箍、套壳、磨床、包装等机加工过程,即制得所需的新型转炉自动挡渣滑动水口用滑板砖。
[0028]根据上述三个实施例制得的产品为碱性铝镁碳尖晶石质滑板砖,上述三个实施例制得的滑板砖的平均理化指标如下表所示:
一种新型转炉自动挡渣滑动水口用滑板砖及其制备方法
- 专利详情
- 全文pdf
- 权力要求
- 说明书
- 法律状态
查看更多专利详情
下载专利文献
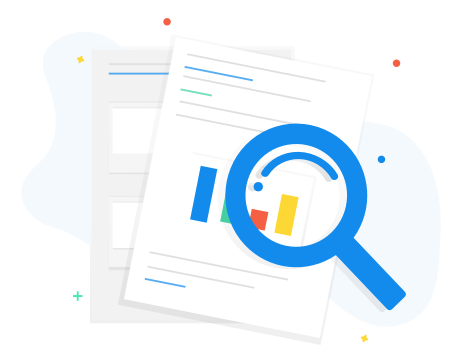
下载专利
同类推荐
-
杭文明, 王远林顾华志顾华志顾华志顾华志于海滨, 蔡海宁张军
您可能感兴趣的专利
-
张军张军张军张军张军张军
专利相关信息
-
张军孙颖莹, 申 谢孙颖莹, 申 谢孙颖莹, 申 谢孙颖莹, 申 谢孙颖莹, 申 谢关爽, 卢静