专利名称:开-关气动致动器的反馈控制的制作方法在后段眼外科手术中使用显微外科切割探针是众所周知的。这些切割探针通常包括中空外切割部件、设置与中空外切割部件共轴且可移动地设置于其中的中空内切割部件,以及在其远端附近径向延伸通过外切割部件的端口。将玻璃体液和/或膜吸入开口端口中,并且致动内部件以闭合端口。一旦闭合端口,内、外切割部件上的切割表面协作以切割玻璃体和/或膜,并且随后通过内切割部件吸走切割组织。在外科手术过程期间,频繁地控制切割速率和工作循环以调节可以在给定时间阶段中切割的组织量。例如,在较不敏感区域(诸如与视网膜分离的区域)切割时,可以以有效率的方式进行切割。当切割更敏感区域中时,诸如靠近视网膜的区域,可以以小心方式进行切割,其中减少了每次切割循环的组织切割量。这可以通过控制端口打开的切割循环中的工作循环或时间百分比而实现。这通过将端口打开的时间量除以单次切割循环的总时间量来确定。提供了较大的工作循环用于进行有效的切割,而提供较小的工作循环进行缓慢且小心的切割。切割部件特性的改变包括来自初始关键部件的公差的改变,可以引起切割机的工作循环的不一致性。为了解决该问题,在生产的时间上校准当前的系统。该工厂校准可能是耗时和昂贵的行为。此外,这是在假设这些相同的关键部件随着时间的改变将不显著地影响性能而进行的。然而,该假设在许多情况下可能是无效的。由于随着时间流逝部件变得磨损,可能不利地影响受控参数的精确性和准确性。这些变化可能潜在地降低系统的性能或者甚至防止系统到达所需的手术目标,潜在地导致切割器未完全打开或关闭。在持续使用的过程中,这些性能下降和故障变得更为明确和更为频繁。尽管具有上述的改进,仍然需要一种改进的玻璃体探针。尤其需要一种玻璃体切除探针,其补偿来自初始公差或者部件随着时间退化的偏差。本公开内容用于解决现有技术中的一个或多个缺陷。
在根据本文原理的一个示例方面,本公开内容涉及具有对于气动致动器的反馈控制的外科手术系统。该系统包括气动压力源和玻璃体切割器,该玻璃体切割器具有切割机构、第一气动输入端口和第二气动输入端口。气动致动器被构造成将气动压力导向第一和第二气动输入端口中之一。第一压力传感器定位和被构造成检测第一气动输入端口处的实际压力,第二压力传感器定位和被构造成检测第二气动输入端口处的实际压力。控制器与第一和第二压力传感器以及气动致动器连通,控制器被构造成基于从第一和第二压力传感器传输的数据而改变气动致动器的致动定时。在另一示例方面,本公开内容涉及一种使用用于气动致动器的反馈控制控制外科手术系统的方法。该方法包括如下步骤将气动压力选择性地引导至玻璃体切割器上的第一和第二气动输入端口中之一,使用第一压力传感器检测第一气动输入端口处的实际压力,以及使用第二压力传感器检测第二气动输入端口处的实际压力。该方法还包括基于第一和第二压力传感器检测得的实际压力而改变气动致动器的动致动定时。在另一示例方面,本公开内容涉及一种具有用于气动致动器的反馈控制的外科手术系统。该外科手术系统包括气动压力源和玻璃体切割器,玻璃体切割器具有切割机构、第一气动输入端口和第二气动输入端口。气动致动器将气动压力导向第一和第二气动输入端口中之一。第一压力传感器定位和被构造成检测第一气动输入端口处的压力,第二压力传感器定位和被构造成检测第二气动输入端口处的压力。控制器与第一和第二压力传感器以及气动致动器通信。控制器被构造成将基于实际测得数据的参数数据与已存储的所需数据比较,并且基于参数数据和已存储的数据计算差值。控制器还被构造成改变用于特定工作循环的已存储工作参数,并且基于用于与气动致动器通信的已改变的工作参数而产生控制信号。在一个不例方面,气动致动器是第一气动致动器和第二气动致动器,该第一气动致动器被构造成将气动压力引导至第一气动端口,而第二气动致动器被构造成将气动压力引导至第二气动端口。应该理解在前的总体描述和如下详细描述仅是示例性和说明性的,并且旨在为要求保护的本发明提供进一步的解释。如下描述以及本发明的实现阐明并建议了本发明的额外优点和目的。并入本说明书并作为其一部分的附图例示了本方面的若干实施例,并且连同描述一起用于解释本发明的原理。图I是根据实施本文所述的原理和方法的本发明一方面的示例外科手术器械的示意图。图2是根据本发明一方面的在具有反馈控制的外科手术器械上的示例系统的视图。图3是根据本文所述的原理和方法的可工作的示例玻璃体切割器的横截面视图。图4是根据本发明一方面的识别测得的压力特征和包括阈值和峰值的示例压力波形的视图。图5是根据本发明一方面的示出反馈控制步骤的示例模型的视图。图6是根据本发明一方面的示出用于确定对已存储工作参数的调整的示例步骤的流程图的视图。图7是根据本发明另一方面的示出反馈控制步骤的示例模型的视图。
现对本发明的示例性实施例做出详细参考,各实施例的例子在附图中示出。只要可能,相同的附图标记在各附图中被用于指代相同或相似的部件。本公开内容涉及包括用于执行眼外科手术的玻璃体切割器的外科手术系统。外科手术系统被设置和被构造成使用反馈控制来检测和补偿由于各个部件公差和劣化引起的不一致性造成的工作偏差。特别地,反馈控制可以减少系统对各个部件的公差、所需特征的变化和总偏差的总体敏感性。该方法可以潜在地适应较宽范围的关键部件公差,并且可以补偿由于部件老化或者诸如温度的不利环境效应引起的改变或变化。使用反馈控制,该系统被设置和构造成识别工作参数在可接受范围之外的时间,并且使用控制规则以修改工作参数,而将其设置回可接受范围内。这导致了更稳定的切割器工作和由此导致更可预测的手术,同时可能地延长特定部件的寿命,而使得患者的费用更低。图I示出了根据示例实施例的以100总体所示的玻璃体切除外科手术器械。该器械100包括底部外壳102和相关的显示屏104,其示出了在玻璃体切除外科手术期间的系统工作和执行。该器械包括玻璃体切割器系统110,其包括玻璃体切割器112并且被构造成提供反馈控制以补偿由于公差、部件磨损或其它因素引起的机械不一致性造成的工作中的变化。图2是根据一个示例实施例的提供反馈的玻璃体切割器系统110的示意图。在图2中,切割器系统110包括玻璃体切割器112、气动压力源202、方向可调节的开-关气动致动器204、压力传感器206、208、消声器210和控制器216。如图中可见,各个部件沿着表示流动路径或流动线路的路线而彼此流体相通。如图2中所示,玻璃体切割器112是具有第一端口 212和第二端口 214的气动驱动切割器。玻璃体切割器通过接收交替地通过第一和第二端口 212、214的气动压力来工作。图3示出了由附图标记112表示的示例玻璃体切割器的横截面视图。切割器112包括作为其基本部件的外切割管300、内切割管302和往复式气体驱动活塞304,所有部件都部分地装入外壳306中。外壳306具有在切割器近端的端部件308,该端部件具有第一和第二供应空气端口 212、214 (如图2中所示)以及一个抽吸端口 310。示例性切割器112通过移动内切割管302通过外切割管300中的组织接收抽吸端口(未示出)而工作。由于内管往复运动以打开和关闭组织接收端口,内切割管302和外切割管300使用类似于剪刀的剪切作用切割组织。管之间的紧密配合在内切割管302打开组织接收抽吸端口时防止将玻璃体材料牵拉入内、外切割管之间的空间中在工作的一个示例中,如果在第一端口 212处增加空气压力,那么活塞304将向下移动,由此相对于外切割管300移动内切割管302,由此闭合外切割管300的组织接收抽吸端口。这样切割了可能已经吸入组织接收抽吸端口的任何玻璃体材料。排出第一端口 212处的压力并且增加第二端口 214处的压力将向上移动活塞,由此打开组织接收抽吸端口,从而其可以吸取将要切割的新玻璃体材料。在美国专利号No. 5,176,628中更详细地描述一种示例切割器的工作,所述文献在此引入作为参考。其它示例切割器包括代替活塞的弹性隔膜,用于打开和闭合组织接收端口。然而,具有由交替的气动压力驱动的往复动作的任何切割器可以适于与本文所公开的系统一起使用。在一些示例中,玻璃体切割器112被设计以提供每分钟5,000次切割,但是可以预期更高和更低的切割速率。参考图2,在所示的实施例中,玻璃体切割器系统的开-关气动致动器204是标准的四路开-关阀。正如公知的,气动致动器具有螺线管,其工作以将致动器移动至图2的示例中所示的两个开-关位置中之一。本文中,气动致动器204处于一位置用于将气动压力提供至第一端口 212,以及从第二端口 214排出气动压力。在该位置处,气动压力可以从压力源202传递通过开-关气动致动器204到达第一端口 212,其中气动压力向玻璃体切割器提供气动动力。同时,第二端口 214处的气动压力可以通过开-关气动致动器204到达消声器210,在那里将气动压力排出至大气。在另一位置,开-关气动致动器204允许将气动压力从压力源202传递至第二端口 214,在那里气动压力将气动动力提供至玻璃体切割器112。同时,第一端口 212处的气动压力可以通过开-关气动致动器204而排出至消音器210,在那里将其排出至大气。开-关气动致动器被构造成如下进一步所述地从控制器216接收工作信号。在工作中,将气动压力从源202而交替地引导至第一和第二端口 212、214以使得玻璃体切割器112工作。开-关气动致动器204在其两个位置之间非常快速地交替,以将气动压力交替地提供至第一和第二端口 212、214。尽管示出具有单个气动致动器204,但是其它实施例包括两个气动致动器,其中一个与两个端口 212、214的一个相连。这些实施例以类似于所述方式工作,其中致动器被构造成从控制器216独立地接收工作信号。压力传感器206、208工作以检测第一和第二端口 212、214处的气动压力水平。这些压力传感器206、208可以是标准的压力传感器,其能够检测压缩气动压力水平并且传送表示检测得的压力水平的数据至控制器216。 在不同的实施例中,控制器216例如是PID控制器、被构造成执行逻辑功能的集成电路或者执行逻辑功能的微处理器。它可以包括存储器和可以执行存储在存储器中的程序的处理器。在一些实施例中,存储器存储用于玻璃体切割器112的特定工作循环或切割速率的最小阈值压力、特定所需的时间长度和所需的峰值压力,以及其它参数。在一些实施例中,控制器216被构造成提供定时功能,其追踪测得的压力高于存储的阈值压力的时间量。控制器216与开-关气动致动器204以及压力传感器206、208通信。如下文所述,控制器216被构造成基于从压力传感器206、208接收得的反馈来控制气动致动器204的工作。图4是表示在特定工作循环上的压力波的示例波形400。中线以上的压力表示由第一压力传感器206检测到在第一端口 212处的压力,而中线以下的压力表示由第二压力传感器208检测到在第二端口 214处的压力。波形400包括输入和存储在控制器216中的最小压力阈值(PO,Pl)。这些最小压力阈值是必须达到或超过的阈值压力值,以便使得玻璃体切割器工作以完全打开或关闭组织接收端口。为了玻璃体切割器以所需切割速率或工作循环工作,在气动端口 212、214的实际压力(PO,pi)超过最小压力阈值(PO,Pl)持续所需时间长度(T0,Tl),该所需时间长度对应于所需的切割速率或工作循环。下文将参考图3中的示例玻璃体切割器112进行描述。
在工作中,压力传感器206测量第一端口 212处的实际压力(pi)。为了在一个方向上致动图3中的气动活塞314以闭合组织接收端口,实际压力(pi)必须达到或超过图4中所示的最小阈值压力(P1)。如果未达到或没有超过最小阈值压力(Pl),气动活塞304可能不会移动足够远以完全闭合图3的切割器中的外切割管300中的组织接收端口。此外,通过控制实际压力(Pl)处于或超过最小阈值压力(Pl)的时间长度,系统控制工作循环。随着处于或超过阈值压力(Pl)的时间变化,所以切割速率或工作循环也改变。类似地,压力传感器208测量第二端口 214处的实际压力(PO)。为了在图3中以相反的方向上致动气动活塞304以打开组织接收端口,实际压力(PO)必须达到或超过最小阈值压力(PO)。因此没有达到最小阈值压力(PO)可能导致图3中切割器中的仅局部打开的组织接收端口。此外,如上所述,实际压力(PO)应当达到或超过最小阈值压力(PO)持续所需时间长度(TO ),所需时间长度对应于所需的切割速率或工作循环。在常规系统中,致动器特征由于初始公差或劣化以及随着时间磨损而引起的改变可能潜在地降低致动器的性能或者甚至防止致动器完全打开或完全闭合。然而,在本系统中,控制器216被构造成通过测量和追踪测得的实际压力(PO,pi)高于各最小压力阈值(P0,P1)的实际时间(to,ti)来补偿部件公差和变化。通过比较实际时间(to,tl)和所需时间(T0,Tl),控制器216可以计算可使用的差别或差值,以修改发送至开-关气动致动器204的控制信号以调节切割器的工作循环。这可以基于确定是否应当对发送至开-关气动致动器204的信号进行调整的控制规则而进行。参考下文的产生和使用用于气动式开-关气动致动器204的反馈控制的示例方法,这将变得更为清楚。图5示出了用于产生和使用反馈控制以减少由于部件变化引起的错误的示例控制回路500,所述部件变化诸如可以例如随着公差增大或磨损而发生。将参考控制回路500描述反馈控制的示例方法。在使用中,系统110从设置特定的切割速率和/或工作循环的健康护理提供者接受输入。这可以使用器械100上的输入装置而进行,可以通过控制玻璃体切割器112而输入。输入示例可以包括挤压切割器手柄以调节工作循环,经由使用键盘、鼠标、旋钮或其它已知输入装置在屏幕上选择而输入。在一些示例中,使用缺省或预先编程的值而将设置预先存储在系统中。随后系统初始化并且以该特定设置工作,并且控制开-关气动致动器204以气动地致动切割器112。基于输入或预先存储的数据,控制器216存储表示必须在每个端口达到或被超过的最小压力阈值(PO,PD的数据,以完全打开或闭合玻璃体切割器上的组织接收端口。反馈控制在压差传感器502处开始。参考上述示例,压差传感器502代表第一和第二压力传感器206、208。然而,在其它实施例中,使用其它压力传感器结构,其在一些实施例中仅包括单个压力传感器。回到本文所公开的示例,当压差传感器502在第一和第二端口 212、214处检测得实际气动压力(PO、pi)时,反馈控制开始。压差传感器502可以与器械100上的气动流动线路物理相连,可以位于切割器112自身上或者位于其它位置,只要其能够检测代表或指示第一和第二端口 212、214处的压力。压差传感器502输出指示第一和第二端口 212、214中的实际压力(p0、pl)的数据作为模拟信号。在该示例中,模数转换器(ADC)504将模拟信号转换为数字形式。虽然在图5中示为独立的元件,ADC504可以与压差传感器502物理相连,可以是控制器216的一部
8分,或者可以设置在两者之间。在一些实施例中,ADC504还以下列方式被构造成追踪测得的压力(p0,pi)到达或超过预先存储的最小压力阈值(PO,PI)的实际时间长度(to,11)。这些最小压力阈值(PO, Pl)表示完全打开或完全闭合切割器上的组织接收端口所需的压力。因而,实际时间长度(to, tl)指示组织接收端口完全打开或完全闭合的实际时间长度。实际时间长度(to,tl)可以用于单个切割循环,或者可以在多个切割循环上被平均。随后,ADC504输出实际时间长度(t0,tl)。在一些实施例中,控制器216代替ADC504来追踪时间。在图5中,然后数字信号由数字过滤器506以本技术领域公知的方式过滤,以提供由求和模块508处理的且在控制器206中可执行的有意义数据。求和模块508被构造成探测关于组织接收端口被完全打开的时间或组织接收端口完全关闭的时间的时间长度误差或差值(eO,el)。这是基于对于所选切割速率和/或工作循环而与所需时间长度(T0,Tl)相比的实际时间长度(t0,tl)。这些可以在多个循环上进行平均。下文示出了用于确定差值(e0,el)的一个示例方法。在一个示例中,求和模块使用简单的求和计算来确定差值(e0,el)。如下提供了这些的示例e0=t0-T0=实际时间-所需时间;以及el=tl-Tl=实际时间-所需时间。差值e0表示一个致动器位置处的差值。例如,致动器位置可以是提供气动压力以打开玻璃体切割器112上的组织接收端口的位置。差值el表示相对的致动器位置处的差值。例如,相对的致动器位置是提供气动压力以闭合玻璃体切割器112上的组织接收端口的位置。在一些实施例上,差值基于在多个循环上得到的平均值。在一些实施例中,求和模块508计算E,表示两个位置处的两个差值之间的不对称性。可以使用下列公式进行。E=el-e0。基于计算得的差值(e0,el),控制器216使用控制规则510,以确定是否应当对用于控制气动致动器204的工作循环数据进行改变。参考图6解释了本文由附图标记600所示的一个示例性控制规则。图6中的控制规则600在步骤602处开始。在步骤604,控制规则询问差值e0和差值el是否均等于或大于零。如果是,那么系统正确地运作,因为实际压力(PO,Pl)处于或高于最小压力阈值(PO,Pl)的实际时间长度(to,tl)等于或大于所需时间长度(T0,Tl)。因此,工作循环和切割速率无需改变,而询问在步骤606处结束。作为选择地,在一些实施例中,如果需要,系统可以仍然使用不对称性E作为回路误差,以使用控制器216增加或减少工作循环以提供更精确工作。如果在步骤604处答案为否,那么在步骤608处,控制规则询问e0是否大于或等于零以及el是否小于零。如果答案为是,那么在步骤610处系统使用E作为回路误差以通过控制气动致动器204增加将气动压力引导至端口 214的时间量来校正工作循环。校正工作循环可以包括调节或更新产生用于特定工作循环的定时信号所使用的已存储工作数据。随后在步骤606控制规则结束。如果在步骤608处答案为否,那么系统在步骤612处询问e0是否小于零以及el是否等于或大于零。如果为是,那么在步骤614处,系统使用E作为回路误差以通过控制气CN 102917653 A
书
明
说
7/8页
动致动器204增加将气动压力引导至端口 212的时间量来校正工作循环。随后在步骤606处,控制规则结束。步骤608和610确定致动器打开的时间量是否应当增加或减少。在一些实施例中,不对称性E表示增加量或减少量。在一些实施例中,计算得的差值(eO, el)表示增加量或减少量。如果在步骤612答案为否,那么eO和el均小于零,如步骤616中所示。因而,系统进入故障状态,因为工作循环校正不足以校正该故障状态。在步骤616处的这种状态的潜在原因是低的源压力,由此导致了幅值不足以达到最小阈值压力以完全打开或完全闭合切割器112中的组织接收端口。这种状态的另一潜在原因是切割速率高于系统在当前工作参数下可以维持的切割速率。当进入故障状态时,系统可以使用听觉、视觉或触觉信号提醒健康护理提供者系统未处于工作状态。在一个不例实施例中,在激活故障状态之前,系统Iio可以控制气动压力源202以增加源压力。在该实施例中,如果源压力足够地增加,那么系统可以返回至控制规则的起始处。如果不可能增加源压力,那么可以触发故障状态。在另一示例实施例中,如果压力不能足够地增加,那么系统可以提醒用户,指出可能需要降低切割速率以达到所需的工作循环。可以根据用户指令手动地或者自动地改变切割速率。控制规则在步骤606处结束。返回图5,在使用控制规则510确定是否需要校正工作循环之后,如果需要,系统输出为校正值(u0,ul)。随后,使用该校正值(u0,ul)以更新已存储的工作循环控制数据512以将所需时间(T0,Tl)更接近地调整至实际压力(p0,pi)大于最小阈值压力(PO,Pl)的实际时间(t0,tl)。在一些示例中,这是通过更新存储在控制器存储器中的表而实现的,该表追踪所需时间并且将所需时间与所需切割速率或工作循环相关联。使用已更新的工作循环数据,系统产生控制信号用于控制气动致动器204。本文中,由于气动致动器可以改变类型和所使用的数量,气动致动器由气动歧管516。随后,该方法可以重复以连续地检测和校正可能发生的与所需值的偏差。在另一实施例中,系统110仅基于检测得的压力而提供反馈,而无需监视高于最小压力阈值所花费的实际时间。图7示出了该备选控制回路的工作的示例。在许多方面,图7中的备选实施例类似于如上在图5中所述的。仅详细描述了区别。控制回路700以类似于上述的方式工作,其中系统从设定特定切割速率和/或工作循环的健康护理提供者接收输入。基于输入或预先存储的数据,控制器216存储表示在每个端口必须达到的峰值压力(ΡΚ0,PKl)的数据,以完全打开和闭合玻璃体切割器上的组织接收端口达到对应于所需工作循环或切割速率的时间长度。峰值压力表示在波形尖端处所示的最大压力。本文中,反馈控制在压差传感器702处开始。压差传感器702将指示第一和第二端口 212、214中实际压力(pkO,pkl)的数据作为模拟信号输出。ADC704将模拟信号转换成数字形式。在该实施例中,ADC识别实际检测得的峰值压力(pk0,pkl)。这些是由压力传感器206、208对于各个端口 212、214识别的最大压力。随后,由数字滤波器706以本领域已知的方式对数字信号进行滤波,以提供有意义的数据,以由求和模块708可在控制器216中处理。求和模块708被构造成检测所需峰·
10值压力(PK0,PK1)和实际峰值压力(pk0,pkl)之间的误差或者差值(e0,el)。在该示例中,求和模块使用简单的求和计算确定差值(e0,el)。这些如下所提供e0=pk0-PK0=(实际峰值压力)_ (所需峰值压力);以及el=pkl-PKl=(实际峰值压力)_ (所需峰值压力)。此外,差值eO、el各代表不同致动器位置的差值。这些致动器位置可以是提供气动压力以完全打开或完全闭合玻璃体切割器112上的组织接收端口的那些位置。求和模块708使用上述相同等式计算在两个位置的两个差值之间的不对称性E。E=el_eO。基于计算得的差值(e0,el),控制器216使用控制规则710确定是否应当对用于控制致动致动器204的工作循环数据进行改变。在该实施例中,控制规则与参考图6所述的控制规则相同。在使用控制规则710以确定工作循环是否需要校正之后,如果需要,系统输出校正(u0,ul)。随后,使用该校正(u0,ul)以更新工作循环712以将所需峰值压力(PKO,PKl)更接近地调整至实际压力(pkO,pkl)。使用已更新的工作循环数据,系统产生了控制信号用于控制具有开-关气动致动器204的气动歧管716。随后,该方法可以重复以连续地探测和校正可能发生的所需值的偏差。可以使用该反馈控制以减少系统对各个部件公差、改变和与所需特征的总偏差的总敏感性。该方法不需要工厂校正,可以接受较宽范围的关键部件公差,并且继续补偿由于部件老化或者不利环境效应诸如温度而产生的改变。本发明的其它实施例对于考虑了说明书并实现了本发明公开的本领域技术人员而言是显而易见的。说明书和示例仅旨在被理解为示例性的,并且本发明的真正范围和精神由所附权利要求指示。
1
一种外科手术系统,其具有用于气动致动器的反馈控制,其包括气动压力源和玻璃体切割器,其具有切割机构、第一气动输入端口和第二气动输入端口。被构造成气动致动器以将气动压力导向第一和第二气动输入端口中之一处。定位和被构造成第一压力传感器以检测第一气动输入端口处的实际压力,而定位和被构造成第二压力传感器以检测第二气动输入端口处的实际压力。控制器与第一和第二压力传感器以及气动致动器通信。其基于从第一和第二压力传感器通信而得到的数据,而最终改变致动致动器的致动定时。
开-关气动致动器的反馈控制制作方法
- 专利详情
- 全文pdf
- 权力要求
- 说明书
- 法律状态
查看更多专利详情
下载专利文献
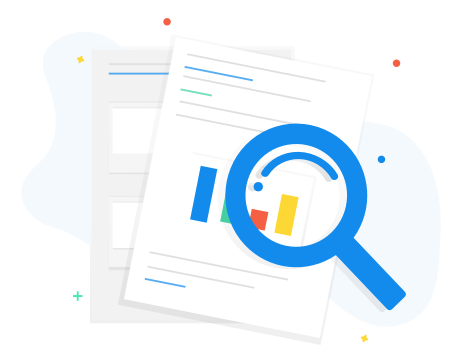
下载专利
同类推荐
-
贺磊盈埃米利奥·鲁伊斯莫拉莱斯埃米利奥·鲁伊斯莫拉莱斯埃米利奥·鲁伊斯莫拉莱斯埃米利奥·鲁伊斯莫拉莱斯李章雨
您可能感兴趣的专利
-
田皓日周益, 张喜平周益, 张喜平曲光辉, 汪义钧曲光辉, 汪义钧
专利相关信息
-
曲光辉, 汪义钧曲光辉, 汪义钧曲光辉, 汪义钧