专利名称:喷射式磨机的制作方法作为该种喷射式磨机有一种流动层型的喷射式磨机,如图5所示,所述喷射式磨机具有能够贮存作为被粉碎物的原料粉体(以下简称为“粉体”)的圆筒形容器20,并设置有从其容器的外周壁朝向中心部而彼此对置的多个喷气喷嘴21,使多个粉体乘载着来自喷气喷嘴21的喷出气体而相互冲撞,以进行粉碎。在该构成的喷射式磨机中,能够获得稳定性能,但使粉体滞留于机器内进行粉碎,因此,存在粉碎结束后机器内残留有粉体的问题。另外,作为其他类型的喷射式磨机,如下述的专利文献1、专利文献2例示那样记载有如下的喷射式磨机,即,由设置于圆筒形粉碎室的周壁上的喷气喷嘴,将粉体与气流一起进行绕转粉碎,将粉碎后的粉体输送到粉碎室上方的分级室中进行分级。在专利文献I所记载的喷射式磨机中,多个喷气喷嘴彼此相对于粉碎室的外周壁而倾斜安装,利用来自其喷气喷嘴的喷出气体,使粉体乘载着喷出气体在高速绕转中粉碎。在专利文献2所记载的喷射式磨机中,在喷气喷嘴对置气体喷出口的位置上,以预定的间隔设置有冲撞构件,使粉体乘载着喷出气体与其冲撞构件发生冲撞而进行粉碎。在这些专利文献1、2的喷射式磨机中,在粉碎室上部设置有配置有分级转子的分级室,以将其粉碎并分级为期望粒径的粉体而回收。专利文献1:日本特开平9-206620号公报专利文献2 :日本特开平4-210252号公报
发明所需解决的问题专利文献I的喷射式磨机中,粉碎室和分级室由环状构件区划开,而形成分隔的状态。在粉碎室和分级室不会彼此造成不良影响这一点有效果,但是,经粉碎室粉碎的粉体要送往分级室,如果不粉碎至某一程度以上的粒径时,则粉体会原样不变地滞留在粉碎室中。另一方面,将经分级室内粉碎至预定粒径以下的粉体排出到机体外而回收,但是,未粉碎至预定粒径以下的粉体其一部分返回到粉碎室中,大多原样不变地滞留在分级室内。其结果为,分级室内的压力损失变大,并且,分级室内的粉体浓度也高,因此有可能无法进行正常分级。另外,专利文献2的喷射式磨机附加了冲撞构件,但粉碎室以及分级室的结构与专利文献I大致同样。但是,粉碎室与分级室未被区划开,粉体从粉碎室进入分级室,或者分级室从粉碎室能够自由移动。另一方,未粉碎至预定粒径以下的中间粒径的粉体,易于滞留分级室的周壁部或受绕转气流影响较小的粉碎室中央部附近。另外,在这些喷射式磨机中,仅仅是粉碎室和分级室较为紧凑,而当机器内滞留量增时,正常运转继续无法有可能也生。因此,在本发明中鉴于所述课题,提供一种紧凑且粉碎效率高,并且运转时粉体滞留机器内也少的喷射式磨机。用于解决问题的手段本发明第一特征结构为一种喷射式磨机,具有圆筒形的粉碎室以及与粉碎室相连通的分级室,其中,分级室内设置有与微粉排出口相连通的分级转子,粉碎室内设置有原料供给口以及从外周壁面朝向所述分级转子的旋转方向侧倾斜配置的至少一个喷气喷嘴,分级室形成为以粉碎室内周壁面作为起点沿着分级转子的轴心向分级转子倾斜的圆锥状。这样,使粉碎室形成为圆筒形,并使与该粉碎室相连的分级室形成为圆锥状,由此,经粉碎室粉碎的粉体利用来自喷气喷嘴的喷出气体流,沿着粉碎室的内周面绕转,同时还沿着分级室内周面绕转。此时,粒径大的粉体因绕转速度大,而围绕着外侧的粉碎室和靠近粉碎室的区域旋转。该区域粉碎区域,粉体继续受到粉碎作用。另一方面,粒径小的粉体因绕转速度小,而沿着内侧的分级室的内周面到达分级室内的分级区域。即,在具有随着从粉碎室远离而直径逐渐缩小的倾斜圆锥状内壁面的分级室中,转速越大的粉体粒子在越大的旋转圆周上绕转。另一方面,绕转速度不大的粉体粒子乘载着流入分级转子内且流向上方的搬送气流,在更小的绕转圆周上进行绕转。这样,微粉朝向与粉碎室分离开的分级区域移动,受到利用了分级转子的分级作用。这样一来,能够抑制粉体从粉碎室向分级室的无谓移动,使要粉碎的粗粉留置在粉碎室内,而将已粉碎的粉体迅速送到分级室中进行分级。这样,在分级室内,将微粉向分级转子引导,并经过分级转子内而向机外排出。另一方面,中间粒径的粉体被进入分级室内的分级转子弹出而返回到粉碎室。在粉碎室内,利用来自喷气喷嘴的喷出气体,在粉碎区域中通过与粉碎室内周壁面的冲撞以及各粉体间的碰撞,能够高效地粉碎粉体。另外,能够减少分级室内的粉碎半途粉体(相当于粉体中粒径较大的粗粉),减小了分级转子的负荷,且还能够抑制粗粉混入广品中。本发明的另一特征结构为,在所述粉碎室的中央部,具有从粉碎室的底面部到分级转子的基端侧,沿着轴心向内侧倾斜的圆锥台状接合器(adapter )。通过将圆锥台状接合器设置于粉碎室的中央部,能够将来自分级室的粗粉有效地引导至粉碎室的内周壁面侧。另外,通过将圆锥台状接合器设置于粉碎室中心部,能够减少粉碎室内无用的空间。即,在不存在圆锥台状接合器的情况下,粉碎室的空间容积变大,在粉碎室的中央部出现了旋转流速度小的区域。这也成了该区域滞留有未通过分级室分级的粗粉或中间粒径的粉体的原因。但是,通过设置圆锥状基座,能够消除粉碎室中央部的空间,将粉体送往绕转速度大的粉碎室的内周面侧。由此,粉体不会滞留在中央部,粉碎中途的粉体也被有效地引导到粉碎区域,其结果为,能够提高粉碎效率。此外,在本说明书中,所谓“粉碎效率”是指喷射式磨机单位风量的处理能力。在此,所谓单位风量是指,气体从喷气喷嘴喷出的单位时间体积的。在设置有多个喷气喷嘴的情况下,是指气体从各个喷气喷嘴喷出单位时间体积的合计值的。例如,所谓粉碎效率高的喷射式磨机是指相同风量下处理能力也较大的喷射式磨机,能够获得高粉碎效率的本发明从节能的观点来说也很有利。本发明的另一特征结构为,设置有以预定的间隔与喷气喷嘴前端部对置的冲撞构件。通过在喷气喷嘴的前端部以预定的间隔设置冲撞构件,能够使粉体向其冲撞构件可靠地碰撞,因而能够对粉体施加强冲击力。也就是说,粉体受到来自冲撞构件的冲击力比各粉体间冲撞的情况更大。特别是粉体其粒径越小,则各粉体间的冲撞机会以及冲击力越小。因此,无法对粉体施加充分冲击力。另一方面,在本结构中,通过设置冲撞构件,能够可靠地对粉体施加冲击力,能够有效地进行微粉碎。其结果为,提高了粉碎效率,还减少了机器内的滞留量。另外,通过将冲撞构件配置在粉体绕转的粉碎区域内,还可对绕转中的粉体进行碰撞粉碎,因此,提高了粉碎效率,还减少了机器内滞留量。本发明的再一特征结构为,冲撞构件的冲撞面相对于喷气喷嘴而朝向粉碎室壳体的内壁面侧倾斜。通过使冲撞构件的冲撞面相对于喷气喷嘴而朝向粉碎室壳体的内壁面侧倾斜,与冲撞面发生冲撞的粉体大半部分沿着相对于其倾斜面的冲撞角度而被弹回粉碎室的壳体的内壁面,并冲撞到壳体的内壁面。利用该冲撞进行进一步粉碎。本发明的再一特征结构为,冲撞构件由圆锥、角锥以及倾斜切断的圆柱或棱柱任一者构成。通过冲撞构件由圆锥、角锥以及倾斜切断的圆柱或棱柱任一者构成,能够根据粉体的种类或目标粒度,控制经与冲撞构件冲撞后的粉体的弹回方向及前进方向。本发明的又一特征结构为,将粉碎室和分级室一体地横向配置。通过将粉碎室和分级室一体地横向配置,能够在粉碎室中利用重力将粉体集中到位于粉碎室下方的粉碎区域,由此能够可靠地增大同一区域内各粉体间或粉体与冲撞构件间的冲撞机会。由此,能够提高粉碎效率。本发明的另一特征结构为,将喷气喷嘴大致水平朝向地配置于粉碎室的下部位置。并且,通过在集中了粉体的粉碎室下方的粉碎区域中,大致水平朝向设置喷气喷嘴,能够更可靠地对粉体施加加速力,能够有效地进行粉碎。
图1是表示本发明喷射式磨机的实施方式的剖视图。图2是表示本发明喷射式磨机的实施方式的立体图。图3是表示本发明的喷射式磨机的另一实施方式的立体图。图4是本发明喷射式磨机的实施例和比较例的性能的曲线图。图5是本发明一实施例中用作比较例的喷射式磨机的简图。
下部壳体I大体呈杯状,其具有中央具有贯通孔的大致圆板状的底部Ia ;从底部Ia的直径方向外侧的端部沿着大致铅垂方向向上延伸的圆筒状的侧壁部lb。上部壳体2大体呈环状,并在中央部具有用于排出微粉的微粉排出口 4a大致。更具体而言,上部壳体2具有沿着大致水平延伸的上表面2a ;从上表面2a的直径方向外侧的端部沿着大致铅垂方向向下延伸的圆筒状的外周面2b ;从外周面2b下端到上表面2a直径方向内侧的端部即微粉排出口 4a而倾斜向上呈大致直线状延伸的大致圆锥状的内周面2c。微粉排出口 4a其上部连接有共有轴心X的微粉排出管4。另外,在上部壳体2的外周附近部位,设置有上下贯通了上部壳体2的原料供给管5 (原料供给口一个例子),经由该原料供给管5将作为被处理物的粉体供给至下部壳体I。在下部壳体I内的底部Ia的中央安装有圆锥梯形状的底部板14 (圆锥台状接合器一个例子),底部板14具有比微粉排出口 4a稍微大的外形平坦的圆形上表面14a ;从上表面14a的外周部到底部Ia逐渐向外侧变宽大的倾斜侧面14b。将底板14下端部的外径即最大外径设定为比下部壳体I的侧壁部Ib内径充分小,因此,在底部板14的外周与下部壳体I的侧壁部Ib的内表面之间,下部壳体I的底部Ia 一部分(最外周部)成为大致平坦的环状部分而延伸。在喷射式磨机器内部,由上部壳体2的圆锥状内周面2c和底板14的倾斜侧面14b形成大致圆锥台状空间,该圆锥台状空间被适当地区分为特别进行粉碎的下方的粉碎室10和特别进行分级上方的分级室6。如图2例不那样,在粉碎室10设置有喷气喷嘴11。喷气喷嘴11设置在被设为贯通了下部壳体I侧壁部Ib的气体喷出管Ilp的前端,并被配置为从侧壁部Ib的外周壁面向后述分级转子7的旋转方向侧倾斜。气体喷出管Ilp的基端侧利用气体供给软管Ilb与压缩机30相连接。另外,在气体供给软管Ilb的中间介在安装有固定于用于支承喷射式磨机的框体20上的贮气罐T。气体喷出管Ilp和喷气喷嘴11相对于下部壳体I的直径方向而横向倾斜配置,因此,通过将来自压缩机30的高压缩气体从喷气喷嘴11中喷出,使粉碎室10内产生气体的高速绕转流。例如,在下部壳体I的内径为大约400mm的情况下,优选为分别将气体喷出管Ilp和喷气喷嘴11相对于直径方向的倾斜角度大约40度从设定在大约70度的范围内的,但只要是使粉碎室10内产生旋转流的所需角度即可。进而,在粉碎室10设置有作为粉碎机构的冲撞构件12。冲撞构件12配置在从下部壳体I的侧壁部Ib或底部Ia向内侧分离开预定距离的位置上,其具有圆柱状基体部12b ;设置于与基体部12b的棒状构件12c相反一侧的圆锥形状冲撞面12a。如图2例示那样,冲撞构件12配置在与气体喷出管Ilp平行设置的棒状构件12c一端,棒状构件12c被支承在沿着被设置为沿着大致径向贯通了下部壳体I侧壁部Ib的支承构件13的前端。此外,支承构件13支承着棒状构件12c,以使冲撞构件12且还包含棒状构件12c另一端在内的整体从下部壳体I底部Ia以及侧壁部Ib内表面分离开。将冲撞面12a配置为与由喷气喷嘴11生成的旋转流以及喷气喷嘴11的喷出口Ila自身相对置。将冲撞面12a和喷气喷嘴11的喷出口 Ila设定为以预定的间隔对置。
在此,本发明中所谓预定间隔是指,设定为经喷气喷嘴11加速的粉体为了冲撞粉碎而维持充分速度所需的距离。所述预定间隔随着下部壳体I的内径、喷出口 Ila的口径及喷出风量而不同,但优选设定为大约30mm到260mm。例如,下部壳体I的内径大约400mm、喷出口 Ila的口径(直径)大约8. 6mm、风量大约5m3/min的情况下,优选将所述预定的间隔设定为大约70mm到130mm。这样,通过使从原料供给管5供给至粉碎室10内的粉体利用来自喷气喷嘴11的喷出气体(喷射气流)与冲撞面12a发生碰撞,能够将粉体微粉碎。特别是在圆锥形状冲撞面12a的至少一部分、即接近下部壳体I侧壁部Ib的部位由相对于与轴心X对应的径向向下部壳体I的侧壁部Ib倾斜的特定面构成,因此,通过使经该特定面反射出的粉体大多继续冲撞到下部壳体I的侧壁部Ib上,以进行进一步粉碎。在分级室6的直径方向中心部、更具体说在底板14的平坦上表面与上部壳体2的微粉排出口 4a之间,设置有绕轴心X驱动旋转的分级转子7。分级转子7大致圆筒状呈,其外周面与圆锥台状分级室6连通连接,分级转子7的上端与微粉排出口 4a连通连接。分级转子7安装在旋转轴8的上端,所述旋转轴8从比下部壳体I更靠下侧的空间经由分别形成于底部板14和下部壳体I的各中心部处的贯通孔,上下延伸到比底部板14上表面14a更靠上侧的空间中。在旋转轴8的下端安装有滑轮9,由省略图示的马达使分级转子7向图2所示的箭头方向旋转。此外,分级转子7的旋转方向与喷气喷嘴11喷出的喷射气流流向一致。分级转子7具有与旋转轴8上端连结的下方环构件7a ;与形成有微粉排出口 4a的上部壳体2的贯通孔周边下表面对置配置的上方环构件7b ;将下方环构件7a与上方环构件7b连结起来而上下延伸的多个分级叶片7c。各个分级叶片7c形成为上下细长地延伸的矩形板状,上方环构件7b的内径与微粉排出管4的内径大致一致。下方环构件7c具有与旋转轴8上端连结的圆锥台状基端部;从所述基端部的下端向径向外侧延伸的圆板状部;并从该圆板状部的上表面向上方立着设置分级叶片7c。圆板状部的外径与底部板14的上表面14a大致同径,圆板状部与底部板14的上表面14a对置配置。如图1所示,分级转子7相对于旋转轴8借助下方环构件7a呈悬臂状受到支承。分级叶片7c的形状以及片数并不仅限于图1以及图2所例示的情形,还能够任意选择。分级叶片7c的形状能够选自平板状、外周侧厚而内侧薄的楔形状、其外周侧为曲面水滴形状、平板弯曲的形状、平板前端部折曲的形状、分级转子7的上方外径大于下方的形状等中。分级叶片7c沿着分级转子7的外周面从中心呈放射状配置,但也能够相对于中心向反旋转方向侧倾斜配置。另外,构成为在安装有上部壳体2的状态下,形成有与上部壳体2的贯通孔周边下表面和分级转子7的上方环构件7b上端面之间不接触的左右微小间隙。另外,在与分级转子7的上方环构件7b对置的上部壳体2的内表面,设置有彼此沿径向分离开的两个环状槽。由此,将上部壳体2与分级转子7之间的隙间迷宫式密封起来,防止了粗粉从分级室6向微粉排出管4脱落的现象发生。进而,通过将压缩气体供给所述间隙内以使所述间隙内的压力设于分级室6内,能够更有效地防止粗粉脱落现象的发生。同样,构成为形成有与下方环构件7a和底部板14的上表面14a之间也不接触的左右微小隙间。自原料供给管5供给的粉体利用从喷气喷嘴11喷出的气体进行加速,再通过与冲撞构件12或下部壳体I的内周壁面发生冲撞,或者各粉体间发生冲撞而被粉碎。构成为,粉体沿着上部壳体2的圆锥形状内周面高速绕转,同时重复施加与冲撞构件12发生冲撞以及各粉体间发生冲撞,由此进行粉体的粉碎。经粉碎过程微粉化的微粉在沿着内壁面高速旋转中,从粉碎室10被移送向分级室6。在分级室6内,经充分微粉化的微粉由分级转子7分级,经过分级转子7内部从微粉排出管4向机器外排出,再由旋流器或集尘机等公知的捕集机构回收。另一方面,大于预定粒径的粗粉未通过分级转子7,而被输送到分级转子7的下侧方,返回粉碎室10而再次被粉碎。底板14下端的大小、倾斜角度等能够任意设定。例如,在下部壳体I内径大约400mm、内壁面高度大约75mm的情况下,能够使底板14的上端外径大约为170mm,下端的外径大约为300mm,倾斜角大约为50度,高度大约为75mm。只要构成为使底板14的下端外径大于上端外径的方式形成倾斜面即可,但在进一步减少粉体滞留量这一点上,优选为底板14的下端外径为下部壳体I内径的1/2以上。此外,虽未作图示,但也能够将微粉排出口 4a设置在底板14的上表面上,使微粉排出管4贯通于底部板14中并向下部壳体I的下方伸出。在该情况下,分级转子7、旋转轴8以及皮带轮9被支承在上部壳体2的上侧部。在本实施方式中,安装于下部壳体I的喷气喷嘴11个数不仅限于一个,也能够是多个。另外,喷出口 Ila的口径也能够根据粉体的种类、性状、粒度或目标粒度而适当变更。另外,当根据粉体的种类无需设置有冲撞构件12时,通过在粉碎室10内进行高速绕转使各粉体间发生冲撞或粉体与下部壳体I的内周壁面发生冲撞,以进行微粉碎。另外,冲撞构件12的冲撞面12a的形状并不仅限于圆锥形状,也能够是角锥或球面。基体部12b除了圆柱以外,也能够形成为棱柱或球体。在基体部12b采用圆柱或棱柱形状的情况下,为了使粉体冲撞到冲撞面12a后弹回到下部壳体I的内壁面,优选为其冲撞面12a由相对于与轴心X对应的径向而向下部壳体I的侧壁部Ib倾斜的面构成。冲撞构件12的冲撞面12a的材质从防止磨损损伤的观点出发,优选由超硬合金或陶瓷制作,但其取决于粉体的种类而并不会局限这些材质。作为最佳的超硬合金或陶瓷,能够使用氧化铝、氧化锆、碳化钨、碳化硅、碳化钛、氮化硅以及氮化钛等,但并不受限于此。在粉碎耐热弱的原料的情况下,也可冷却冲撞构件12。作为冷却方法,考虑在冲撞构件中设置致冷剂用流路以通流致冷剂的方法。另外,通过将喷气喷嘴11与冲撞构件12之间的间隔适当变更,还能够调节粉碎力。即,这些结构能够根据粉体的种类、性状、粒度或目标粒度来适当变更。其目的在于,构成为用于连结支承构件13与棒状构件12c间的连结机构能够调节冲撞面12a与喷出口 Ila之间的间隔。对下部壳体1、上部壳体2、微粉排出管4、分级转子7、喷气喷嘴11、底板14等的材质未作特别限定,也能够由不锈钢等普通的材料制成。但是,在磨损作用强的粉体的场合,除了喷气喷嘴11和冲撞构件12以外,优选至少粉体相接的部分由超硬合金或陶瓷制作。作为最佳的超硬合金陶瓷,能够使用氧化铝、氧化锆、碳化钨、碳化硅、碳化钛、氮化硅、氮化钛等,但不受限于此。[第二实施方式]以下,基于图3来说明本发明的第二实施方式。在第二实施方式中,基本上,将使用图1、2作为说明的实施方式的喷射式磨机中的粉碎室10以及分级室6横向配置,并且,作为附带于其中的构成构件的喷气喷嘴11、分级转子7等也一并安装。所谓“横向配置”是指,将分级转子7的旋转轴向与重力轴向配置为大致正交。S卩,基本的结构与图1以及图2所示的第一实施方式相同,但横向配置的情况下,优选为原料供给管5设置在构成粉碎室10的下部壳体I的外周壁面,且使原料供给管5从下部壳体I的中心向侧方偏移,并被配置为沿着分级转子7的旋转方向与粉碎室10相连通。 在第二实施方式中,通过将粉碎室10、分级室6横向配置,粉体容易因重力而滞留于下部壳体I内的下方部。为此,将喷气喷嘴11和冲撞构件12呈大致水平朝向配置于下部壳体I的铅垂方向下部而设置。由此,在有限空间中粉体浓度高的状态下,能够利用喷气喷嘴11和冲撞构件12对粉体施加粉碎作用,因此,能够有效地进行粉体的粉碎。实施例作为实施例,使用图3所示的第二实施方式的横向喷射式磨机进行了粉碎试验。另外,作为比较例,使用图5所示的流动层型喷射式磨机(计数喷射式磨机200AFG(Hosokawa Micron株式会社制))进行了粉碎试验。图4示出了这些的粉碎试验的结果。在这些粉碎试验中,作为被处理物,全使用了平均粒径235 μ m的重质碳酸钙。为了使经粉碎获得的产品的平均粒径同等,分别调节两个分级转子7、27的转速进行运转,比较此时的粉碎效率。另外,在运转结束后,再测定并比较残存于机器内的粉体的质量。图4是将经粉碎获得的粉体的平均粒径(μm)作为横轴、将单位风量的处理能力、即粉碎效率[(kg/h) / (m3/min)]作为纵轴的曲线图。如图4所示,可知在实施例与比较例之间,所获得的粉体的平均粒径不存在大的差异,但实施例的粉碎效率相比于比较例更加良好。换言之,在获得相同平均粒径产品的情况下,可知实施例与比较例相比可获得节能效果。另外,运转结束后残留于机器内的粉体的滞留量相对于比较例中的17k9,而在实施例中大幅减少至2k9,能够减少了原料的浪费。产业上的可利用性本发明是能够高效地微粉碎以碳酸锂、氢氧化锂、镍酸锂、钴酸锂、锰酸锂等锂化合物;硝酸钠(芒硝)、氢氧化钠、碳酸钠、重碳酸钠、亚硫酸钠、亚硝酸钠、硫化钠、硅酸钠、硝酸钠、重硫酸钠、硫代硫酸钠、食盐等钠化合物;硫酸镁、氯化镁、氢氧化镁、氧化镁、碳酸镁、乙酸镁、硝酸镁、氧化镁、氢氧化镁等镁化合物;氢氧化铝、硫酸铝、氢氧化铝、聚氯化铝、氧化铝、明矾、氯化铝、氮化铝等铝化合物;氧化硅、氮化硅、碳化硅、硅酸钙、硅酸镁、硅酸钠、硅酸铝等硅化合物;氯化钾、氢氧化钾、硫酸钾、硝酸钾、碳酸钾等钾化合物;碳酸钙、氯化钙、硫酸钙、硝酸钙、氢氧化钙等钙化合物;氧化钛、钛酸钡、钛酸锶、碳化钛、氮化钛等钛化合物;硫酸锰、碳酸锰、氧化锰等锰化合物;氧化铁等铁化合物;氯化钴、碳酸钴、氧化钴等钴化合物;氢氧化镍、氧化镍等镍化合物;氧化钇、钇铁石榴石等钇化合物;氢氧化锆、氧化锆、氧化锆硅酸、锆英砂等锆化合物;氯化锑、氧化锑、硫酸锑等锑化合物;氯化钡、氧化钡、硝酸钡、氢氧化钡、碳酸钡、硫酸钡、钛酸钡等钡化合物;氧化铋、次碳酸铋、氢氧化铋等铋化合物;各无机化合物;招镇钻系、铁络钻系、铁猛系、锁系、银系^钻系、钦铁砸系、猛招碳系、镨系、钼金系等磁铁材料;以及颜料、玻璃、金属氧化物、碳、活性碳、焦炭、矿物、滑石粉、电池材料、储氢合金、有机化合物、树脂、色剂、粉体涂料等为首的广泛领域中的各种材料的装置,而且,还能够减少机器内的滞留量以及装置停止后的残留量,从而能够减少原料的无
谓浪费。
附图标记说明
I下部壳体
2上部壳体
3紧固件
4微粉排出管
4a微粉排出口
5原料供给管(原料供给口 )
6分级室
7分级转子
7c分级叶片
8旋转轴
9滑轮
10粉碎室
11喷气喷嘴
Ila喷出口
12冲撞构件
12a冲撞面
12b基体部
12c棒状构件
13支承构件
14底板(圆锥台状接合器)
20容器
21喷气喷嘴
27分级转子
X轴心
T贮气罐
本发明涉及一种喷射式磨机,其具有圆柱形的粉碎室(10)和与该粉碎室(10)相连通的分级室(6),所述的分级室(6)中设置有微粉排出口(4a)和分级转子(7),所述的粉碎室(10)中设置有原料供给管(5)和至少一个喷气喷嘴(11),所述的分级室(6)的形状为起始于所述的粉碎室(10)的内壁面并斜朝向所述的分级转子(7)的圆锥形,这种构造使得该喷射式磨机具有很高的粉碎效率,而且当该喷射式磨机运转结束后能够减少腔室内的粉末残留。
喷射式磨机制作方法
- 专利详情
- 全文pdf
- 权力要求
- 说明书
- 法律状态
查看更多专利详情
下载专利文献
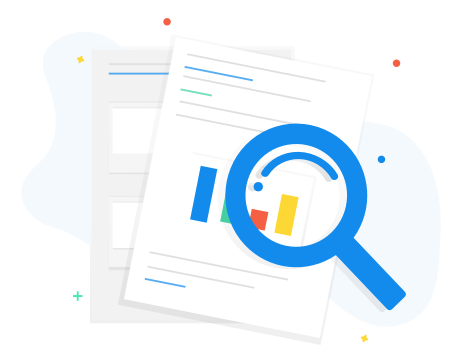
下载专利
同类推荐
-
吉川雅浩吉川雅浩吉川雅浩吉川雅浩王凤云
您可能感兴趣的专利
-
孙梓顺孙梓顺许松柏许松柏
专利相关信息
-
许松柏许松柏许松柏许松柏谢建国谢建国