专利名称:天丝纤维喷气涡流纺制备毛巾的方法半个世纪以来,纺纱技术得到不断的发展,继环锭纺后,先后出现了 转杯纺、自捻纺、摩擦纺、喷气纺、涡流纺、静电纺、包缠纺、包巻纺、 夹心纺又成"三明治"纺、紧密纺、赛罗纺、赛罗菲尔纺、索罗纺、喷气涡 流纺等众多新型纺纱。然而只有转杯纺、喷气纺、紧密纺、喷气涡流纺获 得了较大的商业成功,其余纺纱系统因纱线结构、性能方面的缺陷或纺纱 生产成本过高或产品仅实用于特定产业等因素未获得较大的发展。影响纺织行业生产能力的重要瓶颈之一是纺纱的生产能力,而纺纱生 产能力由纺锭规模及纺纱速度共同决定。据统计资料显示目前世界整个 纺纱规模中,环锭纺和转杯纺占95%以上,环锭纺纱锭约1.7亿,转杯纺 头数占环锭纺锭子数的5%左右,俄国、美国、捷克转杯头数占环锭纺锭 数均高于20%;喷气纺约28万头,主要集中在美国,约占喷气纺总数的 80%;喷气涡流纺约4万头,绝大部分集中在美国、澳大利亚。而我国环 锭纺约7600万锭,转杯纺约175万头,喷气纺约2万头,分布在上海、 天津、重庆、广东、江苏、河南、湖北和山东等地;喷气涡流纺在我国只 有极少量引进,分布在新疆、江苏、福建等地,新型纺纱头数占环锭纺锭 数的比例远低于国际平均水平。就纺纱速度而言,喷气纺的纺纱速度 120 300米/分,转杯纺的纺纱速度100 200米/分,而喷气涡流纺(MVS No.861)的纺纱速度高达450米/分,生产能力相当于每锭环纺的20倍。就纺纱速度上看,应大力发展转杯纺、喷气纺、喷气涡流纺等新型纺 纱。从能耗、节约占地面积、劳动强度上看,新型纺纱占有绝对优势,应加大新型纺纱的投资比例。但环锭纺因纱线具有较高的强力及纱线品种适 应性强,尤其紧密纺、赛络纺、赛罗菲尔纺、索罗纺等对环锭纺家族进行了有效的补充,仍占有较大的市场份额;然而环锭纺的能耗大、效率低、 占地面积大、噪音污染严重及工作环境恶劣等是其致命的缺点,这决定了 传统的环锭纺不是以后纺织产业发展的重点;转杯纺因转杯的速度提高有 限,适纺粗支纱,纱支适应性范围窄,长远发展受限;喷气纺适合宜加工 精细原料如精梳、化纤,适纺中细支纱,但无法生产满足品质需求的100% 纯棉纱线,同时纱线强力仅为同支环锭纱的60%左右,这很大程度制约 了喷气纺纱的发展;喷气涡流纺扩大了喷气纺适纺性,可纺100%的纯棉 纤维,成纱强力较喷气纱大幅提高。喷气涡流纺是利用压縮空气经喷孔形成高速旋转气流,对集聚于空心 锭子顶端的自由端纤维加捻成纱。喷气涡流纺纱线具有如下特点(1) 纱线由芯纤维和包缠纤维两部分组成,纱体柔软,外观具有环 锭纱的真捻特征,断裂强力较喷气纺大幅提高,接近环锭纱强力;(2) 纱线毛羽较少、伸长小,条干均匀;此外纺纱过程中短纤、棉 节被去除,喷气涡流纱被誉为气流精梳纱;(3) 由喷气涡流纱制得的织物耐磨、抗起球、易吸湿、易染、快干。 喷气涡流纺也适用于生产包芯纱等花式纱线。喷气涡流纺因纺纱效率高、环境友好、能耗低、成纱质量好,必将成为21世纪极具前景的新型 纺纱。喷气涡流纺是近几年来出现的新型纺纱技术,该纱线具有毛羽少、刚度 大等显著特点,同时由于其纱线的独特结构,在水以及使用过程中摩擦力的作 用下,面料手感越用越柔软,因此在毛巾类家纺产品的开发中具有较好的市 场潜力。开发绿色纺织品是指开发对环境有利,卫生保健和回归自然的生态纤维 制品,既有利环境又有益人类,同时对纺织企业打造纺织新品牌、增强产品 附加值、打破传统纺织品的各种限制和增强纺织品竞争力起着举足轻重的作 用。在这种情况下,具有天丝纤维日益受到人们的重视,有关天丝产品的研 究和开发成为当前纺织品开发的热点之一 。但从目前的现状来看,天丝纤维在传统纺纱过程中仍存在毛羽多及手感 过软等缺陷,同时对于后道产品,尤其是毛巾类产品来说,随着使用时间的 不断增加,面料与皮肤的触感日益发硬,针对这些问题,本发明采用新型纺 纱工艺改善天丝家纺产品的使用性能。发明内容本发明所解决的技术问题,克服天丝纤维在传统纺纱过程中仍存在毛羽 多及手感过软等缺陷,以及使用时间的不断增加,面料与皮肤的触感日益发 硬的缺点。本发明根据天丝纤维的品质特点,通过与棉纤维混纺的方式进行 纺纱,研究不同混纺比与纱线性能之间的关系,同时设计环锭纺、转杯纺、 喷气纺及喷气涡流纺四种纺纱方式,对天丝纱线结构、性能及织物性能进行 较全面的对比分析,最终开发喷气涡流纺系列天丝护肤毛巾产品。喷气涡流纺是在喷气包缠纺的基础上发展起来的一种全新纺纱方法,利 用压縮气流喷射在喷嘴内产生高速旋转气流,使须条的边缘纤维(即,头端自 由纤维)的头端对内层纤维产生相对角位移,使须条获得真捻而成纱,其纺纱 部件及其原理天丝纤维一一喷气涡流机——电子留纱器——筒子纱。经过罗拉牵伸的须条被吸入喷嘴前端的螺旋喷丝口,螺旋曲面和导引针 一起防止捻回向前罗拉钳口的传递,使得纤维须条1是以平行松散的带状纤 维束输送到空心锭子前端,涡流室中的压縮气流由外接的橡皮管,经与喷嘴 内壁相切的四个喷射孔进入喷嘴内部形成涡流2,并沿纺锭3锥形顶端的通道 旋转下移,当纤维的末端脱离喷嘴前端的螺旋曲面和导引针的牵引的控制时, 纤维束的后端受到高速涡流轴向分力的作用,须条的纤维互相分离,产生大量的边缘纤维(头端自由纤维),从而产生自由端,在中空纺锭3入口处呈伞状 倒伏,纤维的另一端根植于纱体内。在中空纺锭3入口的集束和高速回转涡 流的共同作用下,倒伏的纤维(头端自由纤维)沿着纺锭3旋转,当纤维被牵引 到锭子内时,纤维沿着纺锭3的回转而获得一定捻度,完成纤维束的凝聚和 加捻成涡流纱4。本发明所需要解决的技术问题,可以通过以下技术方案来实现天丝纤维喷气涡流纺制备毛巾的方法,其特征在于,用含有天丝纤维的 纺织纤维为原料采用喷气涡流纺纱技术生产天丝纱线,天丝纤维依次经过喷 气涡流机、电子留纱器和筒子纱,加工成天丝纱线,再经纺织、染色加工成 毛巾。所述毛巾包括面巾、方巾。所述喷气涡流机包括螺旋喷丝口、引纱针、空心纺锭纺纱部件。主 喷嘴压力、纺纱速度及前罗拉口到纺锭顶端的距离等工艺参数对喷气涡流 成纱性能具有至关重要的作用。引纱针固定于螺旋喷丝口上,喷丝口螺旋方向通常与涡流的回旋方向 相同,使纤维与涡流场旋转配合输送,在螺旋曲面和引纱针的作用下阻止 纱线捻回向前罗拉处传递,确保自由端的形成。所述引纱针固定于螺旋喷丝口上,喷丝口螺旋方向通常与涡流的回旋 方向相同,使纤维与涡流场旋转配合输送,在螺旋曲面和引纱针的作用下 阻止纱线捻回向前罗拉处传递,确保自由端的形成。所述螺旋喷丝口的螺旋角度为45度。螺旋喷丝口的螺旋角度大小对 纱线外观和强度均产生影响。所述纺锭为中空,前部呈锥形,锥面顶端为孔径,克服了外包纤维巻 绕松散,成纱强度小、毛羽较多的缺点,对成纱的加捻起辅助作用。在轴 向气流的作用下,纤维倒伏在纺锭锥面上,通过切向气流的作用把倒伏的自由纤维包缠在芯纤维上,而纺锭3的中空部分与N2喷嘴配合对涡流纱 4起引导作用,将加捻后的纱线输出。喷嘴压力对喷气涡流纺纱线质量无疑有着非常重大的影响。同样纺纱 条件下,喷嘴压力小,气流对纱线控制能力下降,纤维包缠松散,无包缠 纤维增多,从而导致纱线质量下降。而喷嘴压力太大,头端自由纤维在强 大气流作用下,可能会使纤维从纱线芯部抽拔出来,且易呈现无规包缠纤 维,这将恶化纱线质量。所述纺纱速度为100-200m/s。纺纱速度的大小极大的影响着纱线的性所述纺锭3到前罗拉口的距离为ll-39mm,前罗拉口到纺锭3的距离 大小极大的决定了包缠纤维的数量。 本发明的有益效果(1) 针对天丝纱线毛羽多、刚度低以及毛巾类产品使用过程中手感发硬等缺 陷,通过新型纺纱技术一喷气涡流纺改善产品性能、提高产品质量。(2) 通过工艺优化设计使成纱综合性能达到最优,确定不同混纺比天丝/棉纱 线的最佳喷气涡流纺纺纱工艺。(3) 对环锭纺、转杯纺、喷气纺、喷气涡流纺四种纱线与织物进行了对比研 究,从纱线结构上分析纱线与毛巾类产品性能之间的相关关系。以下结合附图和来进一步说明本发明。 图1为本发明涡流纺纱的示意图。为了使本发明的技术手段、创作特征、达成目的与功效易于明白了解, 下面结合具体实施例,进一步阐述本发明。 实施例1天丝纤维喷气涡流纺制备毛巾的方法,用含有天丝纤维的纺织纤维为原 料采用喷气涡流纺纱技术生产天丝纱线,天丝纤维依次经过喷气涡流机、电 子留纱器和筒子纱,加工成天丝纱线,再经纺织、染色加工成毛巾。所述毛 巾包括面巾、方巾。在所述喷气涡流纺纱工艺中,使用喷气涡流机,喷气涡流机包括涡流室、 通入到涡流室中的引纱管、与固定支架连接的涡流管以及置于涡流管内的气 流喷射孔,所述喷气涡流机还包括螺旋喷丝口、引纱针、空心的纺锭纺 纱部件。主喷嘴压力、纺纱速度及前罗拉口到纺锭顶端的距离等工艺参数 对喷气涡流成纱性能具有至关重要的作用。 (1)螺旋喷丝口及引纱针引纱针固定于螺旋喷丝口上,喷丝口螺旋方向通常与涡流的回旋方向 相同,使纤维与涡流场旋转配合输送,在螺旋曲面和引纱针的作用下阻止 纱线捻回向前罗拉处传递,确保自由端的形成。螺旋喷丝口的螺旋角度为45度。螺旋喷丝口的螺旋角度大小对纱线 外观和强度均产生影响。螺旋角度大可有效阻止捻度的上传,有利于实捻 纱的形成,提高成纱的强度,但角度过大纤维就不能沿着螺旋曲面进行平 滑输送,使短纤维纱成纱困难;如果螺旋角度偏小,在喷嘴中被涡流加上 埝度就传播到前罗拉处,使得纤维束不能分离而形成假捻。(2) 空心纺锭3喷气涡流纺纺锭为中空,前部呈锥形,锥面顶端为孔径,对成纱的加 捻起辅助作用。在轴向气流的作用下,纤维倒伏在纺锭锥面上,通过切向 气流的作用把倒伏的自由纤维包缠在芯纤维上,而纺锭3的中空部分与 N2喷嘴配合对涡流纱4起引导作用,将加捻后的纱线输出。纺锭3孔径大,使纤维的旋转空间变大,丧失了部分捻度,外包纤维 巻绕松散,成纱强度小、毛羽较多。纺锭孔径小,纤维束伸展的空间小, 纤维之间产生的摩擦大,捻度大,包缠紧密,但孔径过小会导致纺纱过程 的中断。(3) 主喷嘴压力由于喷气涡流纺纺纱体系的基础是用涡流对纤维加捻,纤维受到高速 的喷气涡流及巻取罗拉的作用而形成真捻,因此主喷嘴压力是喷气涡流纺 的关键工艺。从储气室进人喷嘴的高速涡流可分解为切向、轴向和径向三 向气流,喷嘴内部流场速度分布状态决定了喷气涡流纱的结构与特性。其 中强度最大而且起加捻作用的是切向气流,切向速度沿喷嘴轴向存在差 异,就单根边缘自由尾端纤维而言在不同位置加捻程度不同,这是造成喷 气涡流纱沿轴向捻度不匀的重要原因;纤维束进人喷嘴加捻区后,在径向 气流的作用下,部分纤维的一端从纱体中分离出来形成倒伏在纺锭锥面上 的自由端纤维,径向气流速度较小,波动较大,这有利于进入喷嘴中边缘 自由尾端纤维在气流作用在膨胀,从而在切向气流作用下获得更多的包缠 纤维;而轴向气流引导加捻后的纱线输出。喷嘴压力对喷气涡流纺纱线质量无疑有着非常重大的影响。同样纺纱 条件下,喷嘴压力小,气流对纱线控制能力下降,纤维包缠松散,无包缠 纤维增多,从而导致纱线质量下降。而喷嘴压力太大,头端自由纤维在强 大气流作用下,可能会使纤维从纱线芯部抽拔出来,且易呈现无规包缠纤 维,这将恶化纱线质量。(4) 纺纱速度在追求纺纱高速度、高质量的今天,喷气涡流纺纱机械的推出显然满 足了市场的需求,村田公司最新一代喷气MVS861纺纱机速度高达 450m/min,使得纺纱速度成为喷气涡流纺系统最为瞩目的优点。纺纱速度为100-200m/s。纺纱速度的大小极大的影响着纱线的性能。 旋转的涡流对纱的加捻要比机械式加捻效率高的多,引纱速度低,纤维在 涡流场的时间长,纤维间转移更加充分,捻度大,包缠更加紧密,可以预 测纱线有更高的强度,而引纱速度高,纤维受涡流加捻的时间比较短,包 缠不充分且易形成不规则包缠,纱线强度降低。(5) 前罗拉口到纺锭3的距离前罗拉口到纺锭3的距离为11-39mm^前罗拉口到纺锭3的距离大小 极大的影响喷气涡流纺纱线性能,它决定了包缠纤维的数量,是喷气涡流 纺纱系统非常关键的工艺,通常纺纱条件下,要求它比纤维平均长度稍小。该距离越大,自由纤维越多,纱线性能越接近于真捻纱,但距离过大, 纤维损失率高,同时对纤维的控制能力下降,也会恶化纱线性能。该距离 过小,纤维两端均被握持,自由纤维少,芯纤维多,与包缠纤维少的喷气 纺纱相似。本发明制备的毛巾的主要技术性能指标 纺织成品尺寸变化率经向《3.0%,纬向《3.0%,漂白产品白度》90;纺织成品色牢度耐洗(变色、沾色)》3-4级,耐汗渍(变色、沾色)》3-4级, 耐干摩擦》3-4级,耐湿摩擦》3级; 纺织成品甲醛含量《75mg/kg。以上显示和描述了本发明的基本原理、主要特征和本发明的优点。本行 业的技术人员应该了解,本发明不受上述实施例的限制,上述实施例和说明 书中描述的只是说明本发明的原理,在不脱离本发明精神和范围的前提下本 发明还会有各种变化和改进,这些变化和改进都落入要求保护的本发明范围 内。本发明要求保护范围由所附的权利要求书及其等同物界定。
本发明公开了一种天丝纤维喷气涡流纺制备毛巾的方法,用含有天丝纤维的纺织纤维为原料采用喷气涡流纺纱工艺生产天丝纱线,再经纺织、染色加工成毛巾,在所述喷气涡流纺纱工艺中,螺旋喷丝口的螺旋角度为45度,纺纱速度为100-200m/s。克服天丝纤维在传统纺纱过程中仍存在毛羽多及手感过软等缺陷,解决了毛巾使用久了日益发硬的缺点。
天丝纤维喷气涡流纺制备毛巾的方法
- 专利详情
- 全文pdf
- 权力要求
- 说明书
- 法律状态
查看更多专利详情
下载专利文献
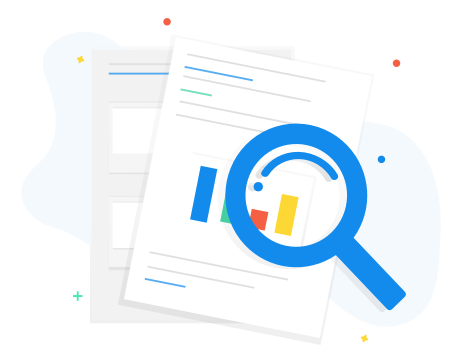
下载专利
同类推荐
-
施移锋, 林孝建代淑梅, 李秋园代淑梅, 李秋园代淑梅, 李秋园李鹏程
您可能感兴趣的专利
-
马延和马延和马延和F-J·明特, J·博斯曼
专利相关信息
-
孙妙囡迈克尔·H·埃利, 迈克尔 H 埃利吕伟民