专利名称:无瓷化泡沫玻璃烧结填充料及其工艺方法现有泡沫玻璃烧结技术配合料采用低氧化温度的碳黑作为发泡剂,此种碳黑氧化温度约为450℃,配合玻璃粉料入模后,为了使配合料在发泡前不因碳黑被氧化而瓷化,(瓷化——泡沫玻璃制品四周表面产生一层釉状玻璃态物质,厚度可达40mm,使制品不能发足,达不到预定加工尺寸和容量其形成原因是配合料中的发泡剂碳黑在烧结前过早氧化,配合料失去发泡功能,在烧结完成后形成白瓷质硬化实心玻块。)在料粉上盖上耐热钢板,目的是使配合料在预热和烧结过程中与空气隔绝。但由于料模可拆结构,在模具进高温炉后,会因受热而严重变形,模具边板与底板之间会出现很明显的空隙,模底四周的配合料会由于模具变形而暴露在高温空气中,使发泡剂碳黑被氧化,配合因而瓷化板结,直到产品发泡结束,产品四周便留下厚度20-30mm,宽度达到产品毛坯高度的近1/2,瓷化体重量约占单块毛坯用粉量的15%,产品质量因瓷化质块的存在而成品率下降30%左右,成品加工时因先要敲掉瓷化的棱角,制品的棱角因而也被打掉很多,产品质量受损严重。为此采取加大模具的尺寸,以此来保证制品有足够的加工余量,这样必然又导致能耗增加,成本增加,企业效益因此受到严重影响。综上所述原有的泡沫玻璃生产技术由于不能彻底地消除瓷化问题,存在着粉料损耗大,产品成品率低,能耗大,加工成本高,原料利用率低。
本发明的目的在于克服现有泡沫玻璃烧结技术的不足之外,旨在提供一种无瓷化泡沫玻璃烧结填充料。本发明的另一目的在于提供泡沫玻璃无瓷化烧结工艺方法。本发明的目的可以通过如下技术方案来实现一种用于制作泡沫玻璃模具上的填充料,填充料为干燥的固体可燃物料。所谓的可燃物料至少为无烟煤粉、硅石粉、木槺、刨花其中的一种。其重量百分比为无烟煤粉50-80%、硅石粉5-20%、木槺15-20%、刨花5-10%,并将其粉碎,其粒径为2-3mm。上述的填充料也可为干燥固体有机可燃物料。本发明的目的还可以通过以下技术措施来实现先将玻璃粉碎均匀地铺入模盒内,并盖上模盖后,压紧。然后再将已粉碎的可燃物料填充到模盒四周的所有间隙及盖板四周的间隙,并在盖板上投放可燃物料;将充分封闭的玻璃配合料模进入炉内,可燃物料燃烧放出的热能,加速了玻璃配合料的烧结溶化,表面自动形成保护膜,同时CO2深度增加,使炉内缺氧,玻璃配合料不被氧化,使玻璃粉料无瓷化。
本发明的优点与产生的有益效益是1、明显地提高产品的质量,经济效益十分显著。由于可燃物在炉内产生上升循环气流使得炉膛四周温度更为一致,使产品泡孔均匀,从而使制品备部位强度一至,导热系数一致,容重一致,光泽一致,从而更具有市场竞争力,制品附加值提高,每立方米产品市场价可比原来增加50-80元,年可增创效益23万元。由于采用无瓷化发泡技术后,制品毛坯无瓷化附着物存在,脱模及加工时不必再对毛坯进行击打,清除瓷化物,使制品边角完好率由原来的不足30%提高到80%,生产效益明显提高,产成本可降下12%。每立方米产品成本由900元下降到800元,年增效益约30万元;2、减少单块毛坯的用料量,节省了原料费。采用无瓷化发泡技术后,单块毛坯用料量由原来的9.5kg下降到8.2kg,单块毛坯用料减少1.3kg,按本厂年产15万块毛坯计年可减少玻璃用量195吨,按每吨料粉1200元计,年可节省23万元原料费,而每烧结一吨配合料要耗费683元,从而可节省电费13.3万元,减少产生瓷类垃圾195吨,在一定程度上减少了环境污染;3、节省人工修补费。无瓷化技术使制品修补工作大大减少,使制品修补价由原来每块0.25元减少到0.20元/块,年可节约用于修补人工费3万元;4、模具的使用周期延长。无资化发泡技术的采用使生产模具及相关轨道等氧化速度大大减慢,每套模具的使用周期由原来的40天提高到60天,年节省模具费8万多元;5、降低了能耗。无瓷化发泡技术其关键是将可燃物随同料模送入炉内,可燃物在炉内燃烧时放出热能,供粉料发泡使用,根据比较,采用无瓷化发泡技术后生产耗电费由原来188元/m3泡沫玻璃下降到173元/m3,按全年产出4500m3计,年可节约电费6.75万元;6、本发明所采用的可燃物来源广、成本低,操作简单,而且使用过程中全部转化成热能用于产品发泡。可燃物可由木材加工产生时交出的锯末、刨花及价格为每吨200元左右的煤粉经粉碎加工后待用。其综合成本为每吨220元,以每块毛坯使用用0.5kg计,全年共计消耗75吨可燃物,计价为16500元。
总之,无瓷化发泡技术年综合效益十分可观,年效益约为100万元,就本行业而言,本发明解决制品瓷化多年来一直迫切需要解决的技术难题。
图1为本发明模盒填充料示意图
实施例1,矩形模盒是用3mm耐热不锈钢板制作。底板(1)700×540mm,四边卷起20mm高的围条,边板(2)高150mm,边板(2)在底板(1)内组装后容积为680×500×150mm。将玻璃配合料称量后入模整平,然后盖上670×490mm的盖板压在玻璃配合料上压紧。将已粉碎含量为80%无烟煤和含量为20%的硅石粉混合物填充到内盖板四周所有的间隙和底板(1)四周的间隙,盖板上投放无烟煤粉和硅石粉混合物,其粒径为2mm,硅石粉为85目。以自然疏松填充为好,使可燃物料细粉对模内玻璃粉料起到封闭作用(参见图1)。
将已充分封闭的配合料模进入炉内预热,此时可燃物料经加热将接近燃点,配合料仍保持在封闭状态中,当模盒进入发泡炉位时,无烟煤粉和硅石粉开始由外向内燃烧。燃烧时须由氧气助燃。由于炉膛常处于封闭状态,炉膛很快进入贫氧状态,CO2浓度增加,炉膛内烟气又一直在吸收着炉内稀少的氧气,同时放出大量的热能,加上无烟煤粉和硅石粉仍在缓慢燃烧放出的热量,加速了模盒内玻璃配合料的烧结熔化。玻璃配合料一经熔化,其表面亦自动形成保护膜,配合料中的碳黑亦无法被空气中的氧气所捕足消耗,与此同时,由于炉膛内无烟煤粉和硅石粉在连续不断地缓慢燃烧,其燃烧产生的上升气流加速了炉膛内高温气体的循环,使玻璃制品整体受热均匀,制品泡孔更为一致。烧结完毕后,从炉膛轨道取出模盒,打开模盒,剔除灰烬,制品四周表面无瓷化现象。
实施例2,玻璃配合料称量后入模整平,然后压上盖板。将已粉碎含量为70%无烟煤粉、15%木槺、10%的硅粉、5%刨花混合物填充到内盖板所有的间隙和底板(1)四周的间隙,并在盖板上铺上一层无烟煤粉、木槺、硅石粉、刨花混合物,其粒径为3mm,硅石粉为90目。
当模盒进入发泡炉位时,可燃混合物由外向内燃烧,玻璃配合料在预热阶段与炉膛内480-700℃的高温含氧空气隔离,配合料进入烧结发泡工区后,在炉内受原有发热元件的帮助,可燃混合物燃烧,模盒上的可燃混合物失去封闭效果时,玻璃配合料开始熔化并在表面形成膜形成自我封闭,同时炉膛封闭燃烧处于贫氧状态,配合料中的碳黑在全发泡过程中都得到了充分可靠的保护、直到最后在880℃左右的温度中与玻璃液中的活性氧化物反应,最终实现玻璃配合料全部发泡形成泡沫玻璃。
实施例3,用80%无烟煤粉、10%木槺、10%刨花颗粒状可燃性混合物对模盒进行封闭,盖板上投放可燃物料。当模盒进入炉膛后,可燃性混合物燃烧,加快炉温的提升,同时使炉内缺氧,进一步保证玻璃配合料不被氧化,同样也可以实现泡沫玻璃粉料烧结无瓷化。同时耐热模具及钢架在无氧化环境下损耗大大降低,可延长其使用寿命。
本发明公开一种无瓷化泡沫玻璃烧结填充料及其工艺方法。所谓的填充料为干燥固体可燃物料。将可燃物料对模盒内玻璃配合料进行全封闭,并在盖板上投放可燃物料。当配合料模进入炉内,可燃物料燃烧,加快炉温的提升,同时使炉内缺氧,保证了配合料不被氧化,实现了玻璃无瓷化。本发明致力于解决了多年来玻璃制品瓷化这一迫切需要解决的技术难题,其结果是明显地提高玻璃制品的质量和产品成品率,节省了原材料,延长了模具及钢架的有效使用周期,经济效益十分显著。
无瓷化泡沫玻璃烧结填充料及其工艺方法
- 专利详情
- 全文pdf
- 权力要求
- 说明书
- 法律状态
查看更多专利详情
下载专利文献
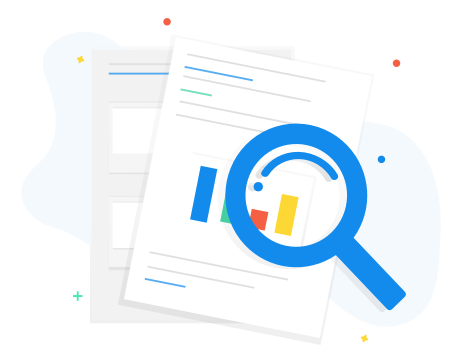
下载专利
同类推荐
-
岸本正一高伯菘, 王坤池王坤池, 王清华王坤池, 王清华方晨航
您可能感兴趣的专利
-
苅谷浩幸, 前田伸广苅谷浩幸, 前田伸广苅谷浩幸, 前田伸广苅谷浩幸, 前田伸广吕文慧, 尹计深熊刚
专利相关信息
-
肖湘东佘志清张艺龄丁体英李延祚顾春生