专利名称:一种预氧化炉的制作方法预氧化炉是用于对原丝进行氧化热处理制备氧化纤维的热处理炉。预氧化炉 外设置有若干为原丝导向的导向辊。原丝的基本氧化过程如下用制备碳纤维用 的氧化纤维原丝,例如,聚丙烯腈(PAN)基连续纤维,使其在很多导向辊导向作用下,沿z字型路径运行通过热处理腔。原丝在通过热处理腔时会被逐步预氧化处理。由于原丝的预氧化过程是逐步进行的,因此,如果原丝在热处理前期就 在高温下进行,那么丝束会因氧化不充分而燃烧。所以,预氧化炉具有以下三个主要的性能指标l.炉膛内的气流温度均匀性;2.炉膛氧含量的充分性3.预氧 化过程中预防自燃现象。针对以上性能指标,目前普遍使用的预氧化炉就存在下列问题。 首先,针对炉膛内的气流温度均匀性。现在较为先进的处理方式是每个热 处理腔都是一端为丝的入口端,另一端为丝的出口端,在每个热处理腔的末端部 分都有一个热气导入腔,而另一端是热气导出腔。热气流最开始是在每个热气导 入腔中形成,其方向是指向热处理腔的内部,热气的流动方向是沿着丝的运行方 向;在每个热气导出腔开始形成抽出的热气,相对于热气流开始的位置形成一 循环通道。为了提高温度的均匀性,炉膛内会采用调节板、进风汇总器、出风汇 集器。进风汇总器结构是有一个长方体形状的空腔组成,这个长方体空腔的前部 和后部是敞开的。这样的设计结构使气流平行于丝束运行方向流动,防止了热处 理腔内部由热气流动引起大的紊乱区。从而有效防止紊乱区的产生而发生的断丝 和丝束起毛。出风汇集器结构是有一个长方体形状的空腔和锥型腔组成,前部锥 型腔分布很多汇集孔,后部长方体空腔是汇集腔。这样的设计结构防止断丝进入 热气汇集腔,使得丝束运行时断丝很容易回到丝束中去。但是,如果进风汇总器 和出风汇总器都安装在炉膛内,这就大大縮小了炉膛的有效尺寸,这样产能也就 降低。而且一旦安装好,可调性能也很差。其次,因为设备本身就是用来对原丝进行氧化热处理制备氧化纤维的热处 理炉,可见炉腔内的氧含量充分,适合是非常重要的。而传统的氧含量控制系统 采用的是开环控制系统,当氧含量不足或过量时需要手动调节阀门,增加了使用 者的麻烦,这在当今强调效率,追求高自动化的工作环境是不适合的。再者,考虑到原丝在预氧化过程中在高温下的自燃现象。首先,原丝的氧化 是需要逐步进行,直到丝束的氧化进行到一定的程度都应该保持在一个较低的热 处理温度。但是如果低温一直持续到热处理的后期,那么就需要很长的热处理时 间。为了保证长的热处理时间就需要增加炉子的长度或增加炉子的通道(也就是 说,原丝在炉子中的路径增长了)。因此,会因炉子的尺寸变大而提高预氧化炉 的生产成本。
本发明提供一种预氧化炉,它在保证符合原丝预氧化要求的前提下,采用 微分化调节装置使温度均匀性显著提高,也更方便操作。 本发明是通过以下技术方案实现的
一种预氧化炉,包括有炉架,炉架上固定有炉体,所述炉体内固定有横置的 隔板,所述隔板将炉体内的炉室分成若干层相互独立的炉腔;每层炉腔对应的前、 后端面上分别设置有进丝口和出丝口,其特征在于每层炉腔对应的侧壁上均设 置有进风口和出风口;包括有风机,所述风机的出风口通过进风系统与与各层炉 腔上的进风口相连通,风机的进风口通过出风系统与各层炉腔上的出风口相连 通;所述进风系统包括有与风机出风口连通的加热室,所述加热室内安装有若干 加热管,加热室的出风口通过管道依次连接有过滤室、上层管路风道调节室,所 述过滤室内设置有过滤网,所述上层管路风道调节室的出风口外通过分叉管道分 别连通有若干入腔纵向风道调节室,每个入腔纵向风道调节室的出风口均通过管 道连通有腔体进风调节室,腔体进风调节室的出风口分别与炉体上对应的进风口 相连通;所述出风系统包括有与炉体上各出风口连通的腔体出风调节室,每个腔 体出风调节室的出风口均通过管道连通有出腔纵向风道调节室,出腔纵向风道调 节室的出风口通过汇集管道连通有下层管路风道调节器,所述下层管路风道调节 室的出风口与风机的进风口相连通;所述上层管路风道调节室、入腔纵向风道调
4节室、出腔纵向风道调节室、下层管路风道调节室均是在一腔室内固定有相互并
列的并与风向平行的竖直隔板;所述腔体进风调节室、腔体出风调节室是在一腔
室内设置有相互并列的且与风向垂直的竖直隔板。
所述连接在下层管路风道调节器与风机间的管道上安装有调节阀。所述上层管路风道调节室上连通有进气管,所述进气管外连通有消防风室,
所述消防风室内填充有氮气;所述进气管上安装有调节阔。
本发明炉腔不锈钢内外壁开有V型槽,使得炉体在实际工作温度范围内不会
出现变形、膨胀的现象。
本发明由炉体结构系统、热风循环系统、温度控制系统、气氛检测系统(氧
含量)四大部分组成。
本发明中用到的热风为循环使用的。开始时,打开风机开关,风从风机出风口进入加热室,经加热管加热后,热风进入到过滤室中,热风经过滤网过滤后进入上层管路风道调节室。由于上层管路风道调节室内有并列的竖直隔板,所以热风在通过上层管道调节室时会经历一级调整。热风经上层管路风道调节室出来后分成若干路,分别进入与其对应的入腔纵向风道调节室中。热风在入腔纵向风道调节室内竖直隔板的作用下经历二级调整。热风从入腔纵向风道调节室流出后进入腔体进风调节室,在腔体进风调节室经历三级调整后分别进入到各层炉腔内。由于热风与走丝方向垂直,并且经过风道进出口长度和宽度方向上"微分法"分级调节风速,确保了进入炉膛内的热风温度均匀性。
热风流经炉腔后,从炉腔的出风口流出,依次流经腔体出风调节室、出腔纵向风道调节室、下层管路风道调节室,最后流入风机内。
由上可知,炉膛内氧含量釆用闭环控制系统,如此可以实现氧含量在线检测和氧含量自动控制功能。
本发明中使用有消防风室。本发明在温度过高时,可报警并自动调节温度。同时,消防风室内的阀门自动打开,往炉腔通入大量保护性气体,减少氧气含量,阻止自燃现象发生。
本发明的每个热处理腔有独立的进出风系统,同一热处理腔同一温度,同一风量,同一氧势。单层炉膛长度5400mm,热处理腔有效区长度5000mra,炉口宽度150mm,炉口高度20mm,丝层间距150mm。通过这些热处理腔丝束在运行过程
5中能够形成连续的丝,每个热处理腔都是一端为丝的入口端,另一端为丝的出口端。
本发明炉体底部框架采用碳钢表面防锈处理,所有腔体均采用321不锈钢材料焊接而成,其中包含风道,风道调节装置等与热循环风接触部均采用321不锈钢材料焊接。所述预氧化炉的表面全部采用不锈钢表面拉丝板。
所述预氧化炉热工材料全部选用陶瓷纤维材料,其极低的导热系数和容重,减小了设备能耗,降低表面温度。同时无任何有害气体挥发。
在每个热处理腔的侧壁部分都有一个热风循环系统。图4中循环风经过风机送入加热腔加热后,通过过滤器过滤,由"管路风道调节器"分三路送进"入腔纵向风道调节器"后,再由"腔体进风调节器"分三路进入炉体,要求风行方向与丝束运行方向垂直,循环风出腔后按对应各调节器回到风机入口。其中根据工艺要求循环风在循环中通过管道上的"调节阀"有新风补充和排放过程。新风风源来自厂房内(洁净度10000级),废气排放前进行热交换。调节阀的动作由氧含量控制系统决定,阔门动作基础点能够保证20% (作为参考)新风补充。该套热风循环系统在解决温度均匀性方面具有灵活的调节功能,其独特的风道设计原理在大型腔体的应用已十分成熟。因此,热处理炉减少了丝束热处理过程中可能发生的毛丝或丝断裂,氧化处理会更均匀。
炉体中的独立温度调节方式,使三个热处理腔中温度值彼此不相同。第一路热气循环通道包含热气循环管、热处理腔、热气循环风机、热交换器。第二路热气循环通道至第三热气循环通道和第一热气循环通道原理一样。
本发明的优点
本发明结构简单,解决现有预氧化设备在温度均匀性、氧含量控制系统以及
原丝自燃现象方面的所遇到的问题,充分利用炉膛有效空间,从而节约了设备和
生产成本,使碳纤维的经济生产变得可行。
图l为炉体结构示意图。
图2为本炉体截面图。
图3为热风循环系统图。
图4为本发明结构示意图。图5为A向截面示意图。
一种预氧化炉,包括有炉架l,炉架1上固定有炉体2,所述炉体2内固定有横置的隔板3,所述隔板3将炉室内的炉腔分成三层相互独立的炉腔4;每层炉腔4对应的前、后端面上分别设置有进丝口 5和出丝口,每层炉腔对应的侧壁上均设置有进风口 6和出风口 7;包括有风机8,所述风机8的出风口通过进风系统与与各层炉腔4上的进风口 6相连通,风机8的进风口通过出风系统与各层炉腔4上的出风口 7相连通.
所述进风系统包括有与风机8出风口连通的加热室9,所述加热室9内安装有若干加热管,加热室9的出风口通过管道依次连接有过滤室10、上层管路风道调节室11,所述过滤室10内设置有过滤网,所述上层管路风道调节室11的出风口外通过分叉管道分别连通有若干入腔纵向风道调节室12,每个入腔纵向风道调节室12的出风口均通过管道连通有腔体进风调节室13,腔体进风调节室13的出风口分别与炉体2上对应的进风口相连通;所述出风系统包括有与炉体2上各出风口连通的腔体出风调节室14,每个腔体出风调节室14的出风口均通过管道连通有出腔纵向风道调节室15,出腔纵向风道调节室15的出风口通过汇集管道连通有下层管路风道调节器16,所述下层管路风道调节室16的出风口与风机8的进风口相连通;所述上层管路风道调节室11、入腔纵向风道调节室12、出腔纵向风道调节室15、下层管路风道调节室16均是在一腔室内固定有相互并列的并与风向平行的竖直隔板;所述腔体进风调节室B、腔体出风调节室14是在一腔室内设置有相互并列的且与风向垂直的竖直隔板。
连接在下层管路风道调节器16与风机8间的管道上安装有调节阀17。
上层管路风道调节室11上连通有进气管,所述进气管外连通有消防风室18,所述消防风室18内填充有保护性气体;所述进气管上安装有调节阀。
风机8和加热室9分别安装在风机支撑架19和加热箱支撑架20上。新风由风机8进入加热室9加热后,再经管道进入上层管路风道调节室稳流,此时在上层管路风道调节室一端开有消防风道(及时通入保护性气体,防止预氧化过程中自燃现象发生),然后经过稳压的热风再依次经过入腔纵向风道调节室12、腔体进风调节室13,最后进入各层炉腔4,对经过各层炉腔4内的"Z"型走势的原丝进行充分预氧化后,废气再经由管道进入热交换器21进行热交换, 一部分热能进入加热室被重新循环利用,而交换后的废气经废气排出口排出,至此一个完整的预氧化过程完成!
本发明公开了一种预氧化炉,包括有炉架,炉架上固定有炉体,所述炉体内固定有横置的隔板,所述隔板将炉体内的炉室分成若干层相互独立的炉腔;每层炉腔对应的前、后端面上分别设置有进丝口和出丝口,每层炉腔对应的侧壁上均设置有进风口和出风口;包括有风机,所述风机的出风口通过进风系统与各层炉腔上的进风口相连通,风机的进风口通过出风系统与各层炉腔上的出风口相连通。本发明结构简单,解决现有预氧化设备在温度均匀性、氧含量控制系统以及原丝自燃现象方面的所遇到的问题,充分利用炉膛有效空间,从而节约了设备和生产成本,使碳纤维的经济生产变得可行。
一种预氧化炉制作方法
- 专利详情
- 全文pdf
- 权力要求
- 说明书
- 法律状态
查看更多专利详情
下载专利文献
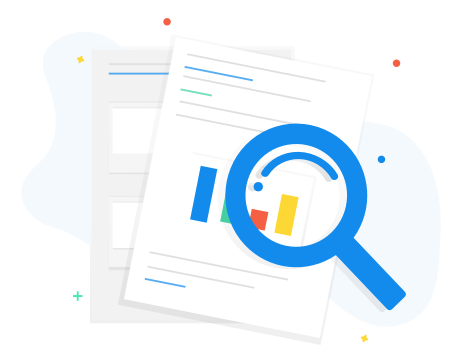
下载专利
同类推荐
-
莫雪魁
您可能感兴趣的专利
-
孟春艳孟春艳
专利相关信息
-
李建强, 马晓光毛裕民, 谢毅徐时清