一种直流变频电机用永磁铁氧体磁体的制备方法 【技术领域】 [0001]本发明属于磁性材料【技术领域】,尤其涉及一种铁氧体磁体的制备方法。 [0002]随着高新技术的发展和社会对能源效率要求的日益提高,变频技术的应用越来越广泛,尤其是在中国,政府大力提倡节能措施,并着重推荐了变频节能技术。变频电机的特点是:一是运行平稳:变频电机带负载平缓起动,加速及平缓减速刹车,克服了普通洗衣机硬起动的缺点,既减少了起动冲击电波,又避免了冲击载荷对电器的影响,减少振动、噪音,延长了电器使用寿命;二是安全可靠:变频电器采用软件、硬件结合进行安全保护;发生异常情况时及时报警,保证系统安全、可靠运转。高效节能直流变频电机用永磁铁氧体器件作为高性能铁氧体材料的一种应用领域,其性能要求要达到Br ^ 430mT, Hcj ^ 380KA/m,相当于日本TDK公司的FB9性能。目前国内几家超大规模永磁铁氧体生产企业,通过加大La-Co等贵重金属元素的使用量,实现生产FB9系列产品的性能。但是存在两个问题:第一、La-Co加入量大,由于La-Co等贵重金属的价格高,使得生产成本增加;第二、现有的制备工艺在控制物料的颗粒大小和均匀方面达不到要求,以及在成型工序上使用的压制工艺和模具,均会造成生产的产品性能稳定性差,波动大,影响电机正常使用;同时现有的压制工艺生产出来的产品,磨削量大,原料浪费严重,磁器件的磁力线分布发散,表磁降低。
[0003]为了现有技术的缺陷,本发明的目的是提供一种直流变频电机用永磁铁氧体磁体的制备方法,降低生产成本,保证直流变频电机所需永磁铁氧体的高磁性能,满足电机对所需磁体的稳定性的要求。
[0004]一种直流变频电机用用永铁氧体磁体的制备方法,所述磁体为六角晶系,其化学结构式为 AhBx(Fe12ICy)zO19,其中 0.04 ≤ X ≤ 0.70,0.04 ≤ y ≤ 0.40,0.7 ≤ z ≤ 1.2,A 为Ba、Ca、Sr中的至少一种元素,B为La、Pr、Gd中的至少一种元素,且必须含La,C为Co、Zn、Mn、Ni中的至少一种元素,且必须含Co,该制备方法包括以下步骤:
O配料:按化学结构式AhBx(FetyCy)zO19化学计量进行配料,其中使用的各化合物的纯度分别为=Fe2O3 ≤ 98.5% (含 S12 ( 0.05%)、La2O3 ≤ 98%、SrCO3 ≤ 97.5%,Co2O3 ≤ 75%,将各种原料按如下重量比称量=Fe2O3:77~82%,SrCO3:12~14%、A1203:0.2~0.5%,S12:0.2 ~0.5%、La2O3:2 ~5%、Co2O3:2 ~5% ;
2)一次球磨:将原料和辅料加入卧式球磨机加水湿磨,按料、球、水的重量比1:4:2,其中钢球选用合金钢球直径Φ6,置于球磨机中混磨4小时,粒度达到1.0Mm,出料时过150目筛;
3)成型:将磨好的料浆经压滤,用125t压机压制成方块,得到原料料块;
4)预烧:将压制好的原料料块,在轨道电窑中1250~1300°C烧结2小时;
5)破碎:用出口端加装风选装置的滚筒式粉碎球磨机破碎至2~3Mm,制得高性能永磁铁氧体预烧料;
6)退火:将制备的高性能预烧粉料装在耐火盒中,推入轨道电窑在600~900°C下退火2~3小时,退火目的控制颗粒的均匀长大,保证物料颗粒大小一致,确保后序产品性能的稳定性;
7)二次球磨:将粗粉加入辅料,添加少量Si02、CaC03、Al2O3、复合分散剂等,其中0.lwt% ( S12 ( 1.0wt%, 0.5wt% ( CaCO3 ( 2wt%, 0.lwt% ( Al2O3 ( 2wt%, 0.05wt% ≥复合分散剂< 1.2wt%,球磨时间10小时,可以制备满足性能要求的原料使用;按料、球、水的重量比1:5:2,其中钢球选用合金钢球直径Φ6与Φ4按1:1配比使用,粒度达到0.70~0.75μιτι ;
8)成型:将脱水后的料浆使用模具压制产品,含水量控制在25%~45%,然后在磁场中进行压制生坯,压制的压力为700~750kg/cm3,成型磁场≥10000e (I 0e=79.6A/m);
9)烧结:压制生坯在电窑1210±10°C保温2小时烧结;
10)磨加工:按照产品图纸要求尺寸进行加工,经过清洗、检测工序得到最终的永磁铁氧体磁体;
11)性能测试:产品磁性能测。
[0005]本发明进一步改进,在步骤7)中复合分散剂为葡萄糖酸钙、山梨醇、碳酸氢铵的混合物,其中0.05wt% <葡萄糖酸|丐< 0.6wt%, 0.05wt% <山梨醇< 0.8wt%, 0.05wt% <碳酸氢铵< 0.5wt%,抑制晶粒长大,助溶促进固相反应,提高颗粒的成型取向度,保证获得高性能铁氧体产品。
[0006]本发明进一步改进,在步骤8)中成型工艺采用反压工艺,成型模具的冲头和吸水板均与磁体的形状一致,在成型模具的冲头和上模吸水板上均镶嵌不锈钢不导磁材料,使磁力线均匀分布,并利用上述反压工艺,磁体的外弧表面磁感应强度高,内弧表面磁感应强度低,使得磁体工作面具有高表面磁感应强度。
与现有技术相比,优点是(I)减少了 Co2O3用量,Co2O3的实际用量仍在1.2%以下,与此相比其他企业生产同类性能的产品,使用量都在1.5%以上,降低了生产成本;(2)预烧料退火工艺,保证颗粒大小的一致性,产品性能的稳定性好;(3)对成型模具使用不锈钢镶嵌,在成型时磁力线聚集在磁体工作面,有效提高磁体工作面的表面磁感应强度,使电机性能得到提高;(4)反压工艺的使用,可降低加工磨削量,磨削量为可降低至28%,与此相比其他企业生产同类型的产品其磨削量为40~45%,有效减少原料的使用,减少浪费;(5)产品的磁性能高,扩大了变频电机的工作温度。
[0007]下面结合几个实施例对本发明进一步说明。
[0008]实施例1
一种直流变频电机用用永铁氧体磁体的制备方法,所述磁体为六角晶系,其化学结构式为 A1-A (Fe12_yCy) z019,其中 0.04 ≤ X ≤ 0.70,0.04 ≤ y ≤0.40,0.7 ≤ Z ≤1.2,A 为 Ba、Ca,Sr中的至少一种元素,B为La、Pr、Gd中的至少一种元素,且必须含La,C为Co、Zn、Mn、Ni中的至少一种元素,且必须含Co,该制备方法包括以下步骤:
O配料:按化学结构式AhBx(FetyCy)zO19化学计量进行配料,其中使用的各化合物的纯度分别为=Fe2O3 ≥ 98.5% (含 S12 ( 0.05%)、La2O3 ≥ 98%、SrCO3 ≥ 97.5%,Co2O3 ≥ 75%,将各种原料按如下重量比称量=Fe2O3:81.98%、SrCO3:12.11%、Al2O3:0.21%、S12:0.21%、La2O3:2.36%、Co2O3:3.13% ;
2)一次球磨:将原料和辅料加入卧式球磨机加水湿磨,按料、球、水的重量比1:4:2,其中钢球选用合金钢球直径Φ6,置于球磨机中混磨4小时,粒度达到1.0Mm,出料时过150目筛;
3)成型:将磨好的料浆经压滤,用125t压机压制成方块,得到原料料块;
4)预烧:将压制好的原料料块,在轨道电窑中1250°C烧结2小时;
5)破碎:用出口端加装风选装置的滚筒式粉碎球磨机破碎至2~3Mm,制得高性能永磁铁氧体预烧料;
6)退火:将制备的高性能预烧粉料装在耐火盒中,推入轨道电窑在750°C下退火2.5小时,退火目的控制颗粒的均匀长大,保证物料颗粒大小一致,确保后序产品性能的稳定性;
7)二次球磨:将粗粉加入辅料,添加少量Si02、CaCO3> Al2O3、复合分散剂等,其中S12:0.8wt%, CaCO3::1.2wt%, Al2O3:0.2wt%,复合分散剂:1.0wt%,球磨时间10小时,可以制备满足性能要求的原料使用;按料、球、水的重量比1:5:2,其中钢球选用合金钢球直径Φ6与Φ4按1:1配比使用,粒度达到0.70~0.75Mm,其中复合分散剂为葡萄糖酸钙、山梨醇、碳酸氢铵的混合物,其中葡萄糖酸钙:0.6wt%,山梨醇:0.2wt%,碳酸氢铵:0.2wt%,抑制晶粒长大,助溶促进固相反应,提高颗粒的成型取向度,保证获得高性能铁氧体产品;
8)成型:将脱水后的料浆使用模具压制产品,含水量控制在25%,然后在磁场中进行压制生还,压制的压力为700kg/cm3,成型磁场10000e (I 0e=79.6A/m),成型工艺采用反压工艺,成型模具的冲头和吸水板均与磁体的形状一致,在成型模具的冲头和上模吸水板上均镶嵌不锈钢不导磁材料,使磁力线均匀分布,并利用上述反压工艺,磁体的外弧表面磁感应强度高,内弧表面磁感应强度低,使得磁体工作面具有高表面磁感应强度。
9)烧结:压制生坯在电窑1210±10°C保温2小时烧结;
10)磨加工:按照产品图纸要求尺寸进行加工,经过清洗、检测工序得到最终的永磁铁氧体磁体;
11)性能测试:产品磁性能测。
[0009]相关数据列于表1、2、3、4中;检测烧结得到的永磁铁氧体磁体,性能数据如表5中所示。
[0010]实施例2同实施例1的方法,相关数据列于表1、2、3、4中;检测烧结得到的永磁铁氧体磁体,性能数据如表5中所示。
[0011]实施例3同实施例1的方法,相关数据列于表1、2、3、4中;检测烧结得到的永磁铁氧体磁体,性能数据如表5中所示。
[0012]实施例4同实施例1的方法,相关数据列于表1、2、3、4中;检测烧结得到的永磁铁氧体磁体,性能数据如表5中所示。
[0013]表1原料重量比
一种直流变频电机用永磁铁氧体磁体的制备方法
- 专利详情
- 全文pdf
- 权力要求
- 说明书
- 法律状态
查看更多专利详情
下载专利文献
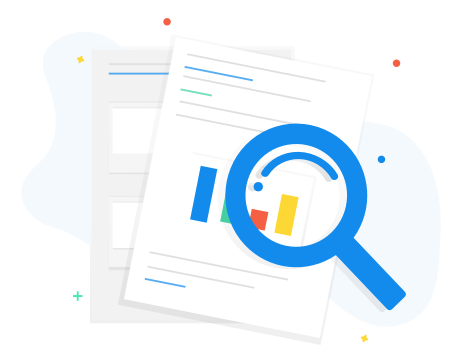
下载专利
同类推荐
-
齐锦刚齐锦刚李小龙许建益, 郑杰李前军
您可能感兴趣的专利
-
建方方建方方须佐昌司田且承, 闵丙旭田且承, 闵丙旭
专利相关信息
-
田且承, 闵丙旭牛晓飞李增光, 王美凤吴云飞林其平