一种低温烧结制备永磁铁氧体的方法【技术领域】[0001]本发明属于磁性功能材料制备【技术领域】,特别涉及到一种低温烧结制备永磁铁氧体的方法。[0002]近年来随着产品小型化、轻型化、薄型化与环保节能要求的不断提高,使得永磁铁氧体材料的需求量大大的增加。故探索和研发单批次成产更大量的永磁铁氧体材料及其制备技术,对满足工业化使用需求,具有重要的意义,一直以来也都是磁性材料研究领域的重点之一;同时由于国家产业转型战略的实施,对高效能低污染的产业提出了节能环保的基本要求,这对传统成产制备铁氧体材料的企业无疑是提出了变革的迫切要求,因此,如何在最小能耗的基础上生产出性能较高的铁氧体材料,是未来该领域研究的重点。[0003]目前生产铁氧体预烧料的主要工艺是:原料配比一混料球磨一压坯一烧结一制粉。其中烧结过程又分为一次预烧和二次烧结两部分。以国内研发的FB5系列永磁铁氧体材料为例,目前的采用的烧结工艺为:一次烧结温度在1185~1250°C,二次烧结温度在1200~1300°C。可以看到烧结的温度范围需要控制在1200°C以上。根据能耗原理,烧结的温度每提高100°C,所需的燃料比提升为15kg/t,这种能量的过渡消耗,无疑在当今采用煤气发生装置生产燃料混合煤气的产业结构中,燃煤量必然大大增加。[0004]因此,寻求高效率,低能耗的烧结制备工艺,具有节能环保的产业结构升级的重大意义。采用本发明的制备工艺,可以将一次烧结温度降低为1050°C~1100°C,二次烧结温度可以降低为1100~1150°C,对比目前所采用的烧结工艺,平均降低温度为100°C ;采用本发明制备的高性能永磁铁氧体材料剩磁值达到≥380mT,内禀矫顽力Hej值达到≥330.lkA/m,磁能积(BH)max 值达到≥26.7kJ/m3。
[0005]本发明旨在提供一种工艺相对简单、高效节能且利于工业化批量生产的高性能永磁铁氧体材料及其制备方法,通过该方法制备的高性能永磁铁氧体材料具有较高的剩磁、内禀矫顽力和最大磁能积。[0006]为达到上述目的,本发明所采用的技术方案为:
[0007]一种低温烧结制备永磁铁氧体的方法,其特征在于:所述的永磁铁氧体材料是六角晶系,其化学结构式为SivxBax0.nFe(12_y)/nRy/n03,其中O≤χ≤0.95,5.75≤η≤6.15,0〈y < 0.5,R为C u ;其具体的制备方法包括下列步骤:
[0008](I)混料:按化学结构式SivxBax0.nFe(12_y)/nRy/n03的组成要求,将与所含组分的相应氧化物原料Fe2O3或Fe3O4和碳酸盐原料粉末混合后,完成一次配料,随后添加占原料(SivxBaxO -HFeil2^7nRy7nO3组成成分总和)的总重量比分别为0.1~1.0wt%的SiO2,0.1~1.0¥丨%的CaCO3 ;与水,钢球按照料:水:球=1:1.5:15的重量比混合,进行一次球磨I~4小时,得到悬浮颗粒平均粒径为Ι.Ομηι~1.5 μ m的混料;[0009](2)将以上所得的混料烘干,并添加添加剂占混料总重量比为0.1~1.0Wt%的B2O3,0.1~1.0wt%的BaO, 0.1~1.0wt%的CuO,采用球磨干混I小时;
[0010](3)预烧:将步骤⑵中所得混料经过造粒后,在600~820°C之间保温烧结2小时,随后在850~900°C温度之间保温烧结I小时,最后采用1000~1150°C保温预烧I~8小时的,制备出永磁铁氧体预烧料;
[0011](4)制粉:将步骤(2)中所制备的永磁铁氧体预烧料,利用粉碎机破碎,过120目筛,得到永磁铁氧体预烧粉料;
[0012](5) 二次球磨:将步骤(4)中制备的永磁铁氧体预烧粉料和所要加入的二次添加剂 0.1 ~1.8wt % 的 BaCu (B2O5),0.1 ~1.0wt % 的 SrCO3,0.1 ~1.0wt % 的 BaCO3,0.1 ~
1.0wt% StJ Fe2O3,0.1~1.0wt%的葡萄糖酸钙,与水、钢球按照料:7jC:球=I:1.5:15的重量比混合,进行二次 球磨,得到悬浮颗粒平均粒径为0.50~1.00 μ m的料浆;所采用钢球的直径分别为3mm、4mm、5mm,重量配比为1:1:1;
[0013](6)压制生坯:根据实际使用要求,控制模具形状的大小,在取向磁场> 385kA/m中进行压制生还,成型压力为6~12MPa,保压10~20s,压制成密度> 3.lg/cm3的中心单孔径圆柱体生坯;
[0014](7)烧结:将步骤(5)中的生坯在850°C保温30分钟,随后在1130~1250°C下,空气氧化性气氛中进行烧结,保温时间为I~6小时,升温速率为5°C /min ;
[0015](8)磨削与测量:将烧结后冷却至室温的磁块进行切割和磨削,按照GB/T3217-92国家标准进行检验、测量。
[0016]如上所述的一种低温烧结制备永磁铁氧体的方法,其特征在于:其中步骤(2)中所述的添加剂还包括工业纯的H3BO3, Ba(OH)2.8H20。
[0017]采用本发明所述的预烧料进行二次辅料添加烧结,在烧结温度为1000°C~IlOO0C时,制备的高性能永磁铁氧体材料剩磁B,值达到> 380mT,内禀矫顽力H。」值达到≥ 323.lkA/m,磁能积(BH)max 值达到≥ 25.9kJ/m3。
[0018]本发明采用一次烧结中添加B203、Ba0、Cu0,并在在600~820°C之间保温烧结2小时,随后在850~900°C温度之间保温烧结I小时,最后采用1000~1150°C保温预烧I~8小时的,制备出永磁铁氧体预烧料。其中B203、BaO, CuO三种物质在850°C以下进行了化学反应。首先由BaO和B2O3生成BaB2O4,随着温度升高至800°C,反应生成的BaB2O4与CuO反应进而生成 BaCu (B2O5)即:Ba0+B203 = BaB2O4 ;BaB204+Cu0 = BaCu (B2O5)。在温度高于 850°C的时候,产生的BaCu(B2O5)溶解,并产生一个低温的液相区,降低了整个铁氧体制备过程中的固相反应温度。其中BaCu(B2O5)溶解后的部分Ba2+再铁氧体晶格中进行了 A位取代,而Cu2+在B位对部分铁离子进行了取代。
[0019]采用本发明的制备工艺,可以将一次烧结温度降低为1050°C~1100°C,二次烧结温度可以降低为1100~1150°C,对比目前所采用的烧结工艺,平均降低温度为100°C ;采用本发明制备的高性能永磁铁氧体材料剩磁Br值达到> 380mT,内禀矫顽力Hej值达到≥ 330.lkA/m,磁能积(BH)max 值达到≥ 26.7kJ/m3。
[0020]为达到上述目的,本发明通过X射线衍射仪(XRD)和扫描电子显微镜(SEM)确定物相组成和形貌,用B— H永磁特性测量仪测量永磁特征参量。
[0021]图1是实施例1中采用本发明专利预烧料制备的SivxBaxO-HFeil2^7nRy7nO3永磁铁氧体材料的XRD衍射图谱;
[0022]图2是SivxBax0.nFe(12_y)/nRy/n03永磁铁氧体材料的SEM形貌图;
[0023]图3是SivxBax0.nFe(12_y)/nRy/n03永磁铁氧体材料的退磁曲线图,其中a为1065°C烧结,b为1085°C烧结。
[0024]下面结合具体实施例,进一步阐述本发明。应理解,这些实施例仅用于说明本发明而不用于对本发明保护范围的限制。本发明可以按
所述的任一方式实施。
[0025]实施例1
[0026]按化学结构式SivxBax0.nFe(12_y)/nRy/n03 (χ = 0.0, η = 6.0, y = 0.2, R 为 Cu 的组成要求,以工业生产的铁红(纯度为99.5% )、碳酸锶(纯度为99.05% )进行一次配料,并同时添加0.2wt% CaC03、0.3wt% SiO2作为一次添加剂,与水,钢球按照料:/Κ:球=I:1.5:15的重量比混合,进行一次球磨2小时,得到悬浮颗粒平均粒径为1.0~1.5 μ m的混料。
[0027]将以上所得的混料烘干,并添加添加剂占混料总重量比为0.3wt %的B2O3,0.5wt%的BaO, 0.6wt%的CuO,采用球磨干混I小时;
[0028]将所得混料经过造粒后,在650°C之间保温烧结2小时,随后在870°C温度之间保温烧结I小时,最后采用1100°c保温预烧6小时的,制备出永磁铁氧体预烧料;随后利用粉碎机破碎,过120目筛,得到永磁铁氧体预烧粉料;随后添加0.5wt %的BaCu (B2O5),0.7wt %的SrCO3,0.9wt5^3BaC03,0.Iwt %的Fe2O3,0.16wt%的葡萄糖酸钙,与水、钢球按照料冰:球=1:1.5:15的重量比混合,进行二次球磨。在取向磁场390kA/m中进行压制生坯,成型压力为12MPa,保压20s,压制成密度3.16g/cm3的中心单孔径圆柱体生坯;将所得生坯在8500C保温30分钟,随后在1080°C下,空气氧化性气氛中进行烧结,保温时间为6小时,升温速率为5°C /min ;
[0029]本实施例所制备的永磁铁氧体产品经检测:剩余磁化强度Br为392.4mT ;磁感应矫顽力Hcb为383.9kA/m ;内禀矫顽力Hcj为323.lkA/m ;最大磁能积(BH)max为26.5kJ/m3。
[0030]实施例2
[0031]按化学结构式SivxBax0.nFe(12_y)/nRy/n03 (χ = 0.0, η = 6.0, y = 0.25, R 为 Cu 的组成要求,以工业生产的铁红(纯度为99.5% )、碳酸锶(纯度为99.05% )进行一次配料,并同时添加0.25wt% CaCO3>0.33wt% SiO2作为一次添加剂,与水,钢球按照料:水:球=I:
1.5:15的重量比混合,进行一次球磨2小时,得到悬浮颗粒平均粒径为1.0~1.5 μ m的混料。
[0032]将以上所得的混料烘干,并添加添加剂占混料总重量比为0.6wt %的B2O3,
0.2wt%的BaO, 0.35wt%的CuO,采用球磨干混I小时;
[0033]将所得混料经过造粒后,在650°C之间保温烧结2小时,随后在880°C温度之间保温烧结I小时,最后采用1120°C保温预烧6小时的,制备出永磁铁氧体预烧料;随后利用粉碎机破碎,过120目筛,得到永磁铁氧体预烧粉料;随后添加0.7wt %的BaCu (B2O5),0.4wt %的SrCO3,0.6wt5^3BaC03,0.4wt%的Fe2O3,0.26wt%的葡萄糖酸钙,与水、钢球按照料冰:球=I:1.5:15的重量比混合,进行二次球磨。在取向磁场396kA/m中进行压制生坯,成型压力为lOMPa,保压15s,压制成密度3.26g/cm3的中心单孔径圆柱体生坯;将所得生坯在8500C保温30分钟,随后在1060°C下,空气氧化性气氛中进行烧结,保温时间为6小时,升温速率为5°C /min ;
[0034]本实施例所制备的永磁铁氧体产品经检测:剩余磁化强度Br为382.4mT ;磁感应矫顽力Hd3为373.6kA/m ;内禀矫顽力H。」为319.lkA/m ;最大磁能积(BH)max为27.8kJ/m3。
[0035]实施例3
[0036]按化学结构式SivxBax0.nFe(12_y)/nRy/n03 (χ = 0.0, η = 6.0, y = 0.3, R 为 Cu 的组成要求,以工业生产的铁红(纯度为99.5% )、碳酸锶(纯度为99.05% )进行一次配料,并同时添加0.35wt% CaCO3>0.36wt% SiO2作为一次添加剂,与水,钢球按照料:水:球=I:
1.5:15的重量比混合,进行一次球磨2小时,得到悬浮颗粒平均粒径为1.0~1.5 μ m的混料。
[0037]将以上所得的混料烘干,并添加添加剂占混料总重量比为0.75wt %的H3BO3,
0.26wt%^ Ba(OH)2.8Η20,0.38wt%^ CuO,采用球磨干混 I 小时;
[0038]将所得混料经过造粒后,在650°C之间保温烧结2小时,随后在890°C温度之间保温烧结I小时,最后采用1160°C保温预烧6小时的,制备出永磁铁氧体预烧料;随后利用粉碎机破碎,过120目筛,得到永磁铁氧体预烧粉料;随后添加0.76被%的BaCu(B2O5),
0.45wt% 的 SrCO3,0.68wt% 的 BaCO3,0.42wt% 的 Fe2O3,0.26wt% 的葡萄糖酸钙,与水、钢球按照料:水:球=1:1.5:15的重量比混合,进行二次球磨。在取向磁场396kA/m中进行压制生坯,成型压力为lOMPa,保压15s,压制成密度3.16g/cm3的中心单孔径圆柱体生坯;将所得生坯在850°C保温30分钟,随后在1070°C下,空气氧化性气氛中进行烧结,保温时间为6小时,升温速率为5°C /min ;
[0039]本实施例所制备的永磁铁氧体产品经检测:剩余磁化强度Br为382.4mT ;磁感应矫顽力Hd3为373.6kA/m ;内禀矫顽力H。」为319.lkA/m ;最大磁能积(BH)max为27.8kJ/m3。
[0040]实施例4
[0041]按化学结构式SivxBax0.nFe(12_y)/nRy/n03 (χ = 0.15,η = 6.0, y = 0.15, R 为 Cu 的组成要求,以工业生产的铁红(纯度为99.5% )、碳酸锶(纯度为99.05% )进行一次配料,并同时添加0.35wt% CaCO3>0.36wt% SiO2作为一次添加剂,与水,钢球按照料:水:球=I:
1.5:15的重量比混合,进行一次球磨2小时,得到悬浮颗粒平均粒径为1.0~1.5 μ m的混料。
[0042]将以上所得的混料烘干,并添加添加剂占混料总重量比为0.65wt %的H3BO3,
0.28wt%^ Ba(OH)2.8Η20,0.68wt%^ CuO,采用球磨干混 I 小时;
[0043]将所得混料经过造粒后,在650°C之间保温烧结2小时,随后在890°C温度之间保温烧结I小时,最后采用1160°C保温预烧6小时的,制备出永磁铁氧体预烧料;随后利用粉碎机破碎,过120目筛,得到永磁铁氧体预烧粉料;随后添加0.86被%的BaCu(B2O5),
0.45wt% 的 SrCO3,0.70wt% 的 BaCO3,0.36wt% 的 Fe2O3,0.48wt% 的葡萄糖酸钙,与水、钢球按照料:水:球=1:1.5:15的重量比混合,进行二次球磨。在取向磁场386kA/m中进行压制生坯,成型压力为llMPa,保压16s,压制成密度3.18g/cm3的中心单孔径圆柱体生坯;将所得生坯在850°C保温30分钟,随后在1075°C下,空气氧化性气氛中进行烧结,保温时间为6小时,升温速率为5°C /min ;
[0044]本实施例所制备的永磁铁氧体产品经检测:剩余磁化强度Br为392.8mT ;磁感应矫顽力Hcb为292.6kA/m ;内禀矫顽力Hcj为373.7kA/m ;最大磁能积(BH)max为30.3kJ/m3。
一种低温烧结制备永磁铁氧体的方法
- 专利详情
- 全文pdf
- 权力要求
- 说明书
- 法律状态
查看更多专利详情
下载专利文献
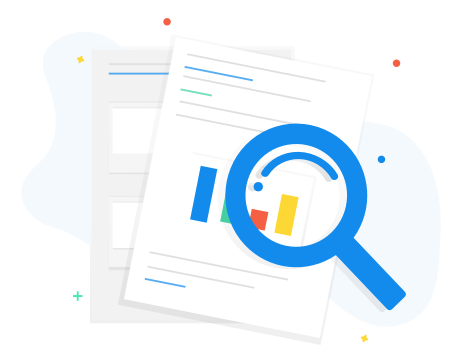
下载专利
同类推荐
-
齐锦刚齐锦刚熊刚
您可能感兴趣的专利
-
刘静, 邓中山刘静, 邓中山
专利相关信息
-
马塞路斯·皮苛特马塞路斯·皮苛特陈凯, 陈树德李小龙