专利名称:一种用高岭土脱泥尾砂制备人造石英石的方法人造石英石也称为石英岗石,是一种采用硅质石粒与石粉为原料,并用较少的粘 接剂及颜料,经过集料一搅拌一混料一布料一真空一振动一压缩等工艺过程完成其薄板成 型,再经过热固化一定厚一反面定厚一研磨一分切等加工过程而成为建筑及台面的装饰材 料,它具有极强的耐酸、耐腐蚀、耐磨损、耐高温、抗冲、抗压、抗折、抗渗透、易于清洁和便于 施工等优点,其花纹图案颜色可以人为控制,外观可仿大理石、花岗石等,既具有天然大理 石的优雅和花岗石的坚硬,又具有木材般的细腻和温暖感,还具有陶瓷般的光泽,极具可塑 性,其变形、粘合和转弯等部位的处理有独到之处,能制作任何造型,美观和实用相结合,是 理想的现代建筑装饰材料。发展人造石对合理利用石材资源具有十分重要的意义,特别是国家颁布了《矿产 资源保护法》,矿产资源的利用将受到严格的控制,浪费矿产资源的现象将得到制止,我国 天然石材资源尽管十分丰富,但是目前浪费惊人,成材率仅为30%左右,其余成为大量碎 石,除少量利用外,大部分成为废石处理掉,造成资源的浪费。而这些碎石可以成为树脂基 人造石的主要原料,变废为宝。因此,发展人造石技术和产业符合国家资源综合利用的基本 国策。人造石产品在国外有着宽广的市场和发展前景,号称“石材王国”的意大利,人造石 产品占全国石材总量的10%以上,其中70% 80%的人造石销往德国、法国、日本等国家, 不少高档饭店、超级市场、地铁站等场所选用人造石,装饰效果极佳。因此从近几年的发展 使用趋势看,树脂基人造石有着广阔的发展前景。现在的企业主要采用的方法有两类①浇铸法浇铸法是把树脂、石料、助剂等混合在一起,加入适当的溶剂,配成胶状 或者悬浮态,经过脱泡以后倒入模具成型,其优点是容易混合均勻,产品密实度高,不需要 加压设备,模具要求低,可以任意大小,操作简便。但其产品经常会因气泡脱除不干净而带 有孔洞,干燥固化的时间相对较长,产品的尺寸受树脂的收缩率影响大,比较难控制,且产 品容易发生翘曲。②压铸法压铸法只把树脂、石料和助剂等混合在一起,直接进入模具进行加压 (加热)成型固化,其优点是成型快,只要各粗细石料配比合适就可以达到比较大的密实 度,产品质量均勻可靠。但是由于树脂料相对较少,搅拌相对较困难,需要有加压设备,设备 成本较高,模具大小限制比较大。目前,主要的工艺方法都存在一定的局限性。如中国发明专利申请 200810214635. 6公开的一种人造石英石制备工艺的材料,含有石英石0 90%、石英粉 5% 90%、纤维 25%、偶联剂0. 5%、树脂0. 20%、固化剂0. 5%、 碎玻璃0 70%、碎镜片0 70%、颜料0 5%、贝壳0 5%和金属片0 5%,原料充分混合后,在10 200°C的真空条件进行固化。该专利申请中最佳的石英石粒径为0. 1 20mm,所用的石英粉最佳为300 2000目,其最佳的固化温度为15 30°C,或者是60 90°C,或者是120 150°C。该申请的原料中采用了粒度较大的石英石和颗粒极细小的石英 粉,增加了树脂使用量,降低了人造石英石的强度;而且会造成人造石英石成本提高;石英 粒度相差很大的原料,对人造石英石的强度产生影响。中国发明专利申请200710029148. 8 公开的一种具有大理石花纹和色彩的人造石英石及其制造工艺。该申请公开的原料是 24 120目的石英52% 78%,120 2000目的石英17 % 38 %,不饱和树脂及附料 6% 14%,各色颜料0. 01% 10%。该发明工艺所公开的树脂量不够,需使用较大数量的 极细的石英粉,会提高成本。这些技术中由于原料中采用了粒度较大的石英石颗粒和极细 小的石英粉,一方面会使树脂使用量增加,这将降低成品材料的强度;另一方面由于需要使 用极细的石英粉,会使成品制造成本提高;而且原料中两类粒度相差很大会在制造过程中 产生偏聚,对成品材料的强度产生更为负面的影响;由于其制造中需要加热压制,其制备过 程中能耗较高,同时压制成型产品的成品率不高,限制了人造石英石的大规模生产。
本发明的目的在于提供一种用高岭土脱泥尾砂制备人造石英石的方法。本发明包括以下步骤1)将不饱和树脂与色料搅拌均勻,再按顺序加入高岭土脱泥尾砂、天然河沙和二 氧化硅粉末,搅拌均勻后,再依次加入促进剂、偶联剂和固化剂,搅拌均勻后,将混合物注入 模具中,所述不饱和树脂、色料、高岭土脱泥尾砂、天然河沙、二氧化硅粉末、促进剂、偶联剂 和固化剂,按质量百分比,10 120目的天然河沙12% 65%,大于120 1500目的天然 河沙15% 35%;二氧化硅粉末5% 15%;不饱和树脂0. 19%;促进剂0. 5% ;偶联剂0. 3% ;固化剂0. 5% ;色料0 5% ;2)将模具送入真空箱抽真空,压制成型,固化加热;3)冷却脱模除去模具,打磨抛光,最后切割成人造石英石规格板。在步骤1)中,按质量百分比,最好10 120目的天然河沙60%,大于120 1500 目的天然河沙20% ;二氧化硅粉末9% ;不饱和树脂10% ;促进剂0. 5% ;偶联剂0. ; 固化剂0. 4%;所述不饱和树脂可采用环氧树脂等;所述促进剂可采用过氧化甲乙酮(工业 品牌号为PT-24,中文俗称为蓝水)等;所述偶联剂可采用有机硅烷偶联剂等,优选丙基三 甲氧基硅烷;所述固化剂可采用二乙烯三胺等。在步骤2)中,所述抽真空的真空度可为10 IOOPa的条件下保持5 20min ;所 述真空度最好为10 60Pa,优选为10 20Pa ;所述固化加热的温度可为25 200°C,固 化加热的时间可为8 17min,固化加热的温度最好为50 175°C,固化加热的时间最好为 10 15min,固化加热的温度优选为80 125°C,固化加热的时间优选为10 15min。对制备后的人造石英石可进行抽样检查,根据《轻工建材行业标准》和《无机材料 力学性能测试标准》分别测试其力学性能和物理性能。其力学性能主要包括抗压强度和抗 折强度;物理性能包括吸水率、密度和热膨胀系数。本发明可根据用户和市场对人造石英石颜色的不同要求,选择不同色料的种类和 比例,以改变其外观颜色和颜色的深浅程度。4与现有的技术相比,本发明采用高岭土脱泥尾砂、天然河沙、二氧化硅粉、不饱和 树脂、促进剂、粘合剂、固化剂以及适量的色料等原料,通过一定的工艺制备出高强度、耐腐 蚀、耐磨损、质地美观的优质人造石英石。本发明的初期投入少,操作方便,上马快,工艺简 单合理,制造出来的人造石英石不仅具有大理石的天然花纹、条纹和丰富的色彩,而且具有 石英石的硬度。本发明中将颗粒尺寸不同的高岭土脱泥尾砂、天然河沙、二氧化硅粉末和不饱和 树脂等混合物置于真空箱在适当的真空中保持适当时间,对板材来说,减小了树脂分布的 不均勻,可以减小板材固化时收缩不均勻导致的变形,从而提高制品的成品率。而且本发明 的尾砂、河沙粒度的配合适当,既可以克服现有技术中因不同粒度的石英产生偏聚而使成 品品质变劣的不足,而且可以使用较少的树脂和固化剂,使产品既能在较短时间内固化脱 模,提高生产效率,同时又不至于产生气泡,影响产品质量,而且可以回收利用高岭土尾砂, 环境友好,进一步减少生产成本,适合于产业化。实施例4工艺过程同实施例1。采用的龙岩高岭土尾砂粒度10 120目40%,天然河沙 120 1500目30%,1000 2000目以上二氧化硅粉末15%,不饱和树脂14%,偶联剂 0.3%,促进剂0. 1%,固化剂:0.5%,色料0. 1%0真空度为50Pa的条件下保持20min,固 化过程温度在180°C。冷却脱模除去模具,打磨抛光,最后切割成人造石英石规格板。经试 验,抗压强度为217. IMPa,抗折强度为40. IMPa,吸水率为0. 018%,密度为2. 41g/cm2,热膨 胀系数为 2. 77 X 10_5°C ―1。实施例5工艺过程同实施例1。采用的龙岩高岭土尾砂粒度10 120目60%,天然河沙 120 1500目20%,1000 2000目以上二氧化硅粉末9 %,不饱和树脂10 %,偶联剂 0. 1%,促进剂0. 5%,固化剂0. 4%。真空度为IOPa的条件下保持lOmin,固化过程温度 在90°C。冷却脱模除去模具,打磨抛光,最后切割成人造石英石规格板。经试验,抗压强 度为230. 2MPa,抗折强度为43. 2MPa,吸水率为0. 017%,密度为2. 45g/cm2,热膨胀系数为 2. 70 X IO-5oC Λ实施例6工艺过程同实施例1。采用的龙岩高岭土尾砂粒度10 120目48%,天然河沙 120 1500目30%,1000 2000目以上二氧化硅粉末12%,不饱和树脂9%,偶联剂 0. 1%,促进剂0.4%,固化剂:0.3%,色料0. 2%0真空度为IOMPa的条件下保持8min,固 化过程温度在70°C。冷却脱模除去模具,打磨抛光,最后切割成人造石英石规格板。经试 验,抗压强度为224. 2MPa,抗折强度为41. 9MPa,吸水率为0. 019%,密度为2. 43g/cm2,热膨 胀系数为 2. 76 X 10_5°C ―1。实施例7工艺过程同实施例1。采用的龙岩高岭土尾砂粒度10 120目50%,天然河沙 120 1500目25%,1000 2000目以上二氧化硅粉末12%,不饱和树脂11 %,偶联剂 1 %,促进剂0. 5%,固化剂0. 4%,色料0. 1 %。真空度为30Pa的条件下保持8min,固化 过程温度在120°C。冷却脱模除去模具,打磨抛光,最后切割成人造石英石规格板。经试验, 抗压强度为220. 6MPa,抗折强度为41. 7MPa,吸水率为0. 020%,密度为2. 39g/cm2,热膨胀 系数为2. 75 X10_5°C人实施例8工艺过程同实施例1。采用的龙岩高岭土尾砂粒度10 120目50%,天然河沙 120 1500目30%,1000 2000目以上二氧化硅粉末11 %,不饱和树脂8 %,偶联剂 0. 2%,促进剂0. 3%,固化剂0. 5%。真空度为20Pa的条件下保持8min,固化过程温度 在130°C。冷却脱模除去模具,打磨抛光,最后切割成人造石英石规格板。经试验,抗压强 度为221. 8MPa,抗折强度为41. 5MPa,吸水率为0. 021 %,密度为2. 33g/cm2,热膨胀系数为 2. 73 X IO-5oC Λ实施例9工艺过程同实施例1。采用的龙岩高岭土尾砂粒度10 120目40%,天然河沙 120 1500目25%,1000 2000目以上二氧化硅粉末15%,不饱和树脂10%,偶联剂 1%,促进剂3%,固化剂2%,色料4%。真空度为20Pa的条件下保持llmin,固化过程温度在130°C。冷却脱模除去模具,打磨抛光,最后切割成人造石英石规格板。经试验,抗压强 度为216. IMPa,抗折强度为38. 7MPa,吸水率为0. 027%,密度为2. 20g/cm2,热膨胀系数为 2. 80 X IO-5oC Λ实施例10工艺过程同实施例1。采用的龙岩高岭土尾砂粒度10 120目40%,天然河沙 120 1500目占29%,1000 2000目以上二氧化硅粉末10%,不饱和树脂:9%,偶联剂 2%,促进剂5%,固化剂4%,色料1 %。真空度为20Pa的条件下保持13min,固化过程温 度在130°C。冷却脱模除去模具,打磨抛光,最后切割成人造石英石规格板。经试验,抗压强 度为217. 8MPa,抗折强度为39. IMPa,吸水率为0. 028%,密度为2. llg/cm2,热膨胀系数为 2. 82 X IO-5oC Λ实施例11工艺过程同实施例1。采用的龙岩高岭土尾砂粒度10 120目35%,天然河 沙120 1500目30%,1000 2000目以上二氧化硅粉末15 %,不饱和树脂8 %,偶联 剂3%,促进剂4%,固化剂5%。真空度为20Pa的条件下保持12min,固化过程温度在 130°C。冷却脱模除去模具,打磨抛光,最后切割成人造石英石规格板。经试验,抗压强度 为218. 8MPa,抗折强度为39. 5MPa,吸水率为0. 029%,密度为2. 13g/cm2,热膨胀系数为 2. 88 X IO-5oC Λ实施例12工艺过程同实施例1。采用的龙岩高岭土尾砂粒度10 120目40%,天然河 沙120 1500目35%,1000 2000目以上二氧化硅粉末10 %,不饱和树脂10 %,偶 联剂1%,促进剂2%,固化剂2%。真空度为20Pa的条件下保持8min,固化过程温度 在130°C。冷却脱模除去模具,打磨抛光,最后切割成人造石英石规格板。经试验,抗压强 度为220. IMPa,抗折强度为39. 9MPa,吸水率为0. 026 %,密度为2. 23g/cm2,热膨胀系数为 2. 79 X IO-5oC Λ
一种用高岭土脱泥尾砂制备人造石英石的方法,涉及一种建筑装饰材料。将不饱和树脂与色料搅拌,加入高岭土脱泥尾砂、天然河沙和二氧化硅粉末,搅拌后,加入促进剂、偶联剂和固化剂,搅拌后注入模具中,所述不饱和树脂、色料、高岭土脱泥尾砂、天然河沙、二氧化硅粉末、促进剂、偶联剂和固化剂。将模具送入真空箱抽真空,压制成型,固化加热;冷却脱模除去模具,打磨抛光,最后切割成人造石英石规格板。初期投入少,操作方便,上马快,工艺简单合理,产品不仅具有大理石的天然花纹、条纹和丰富的色彩,而且具有石英石的硬度,适合于产业化。
一种用高岭土脱泥尾砂制备人造石英石的方法
- 专利详情
- 全文pdf
- 权力要求
- 说明书
- 法律状态
查看更多专利详情
下载专利文献
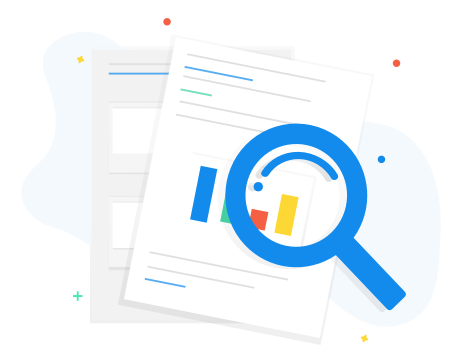
下载专利
同类推荐
-
裵正洙, 李震皓
您可能感兴趣的专利
-
金凤山陈凯, 陈树德陈凯, 陈树德葛怀友李明照
专利相关信息
-
埃胡德·马罗姆, 迈克尔·米治里特斯基I·基拉伊I·基拉伊何经锁, 江超何经锁, 江超