一种湿法-干法刻蚀结合提升熔石英元件阈值的表面处理方法【技术领域】[0001]本发明属于光学材料与光学元件【技术领域】,具体涉及一种提升熔石英元件激光损伤阈值的表面处理方法。[0002]熔石英是高功率固体激光装置中应用最普遍、用量最大的光学材料之一,广泛用于制备透镜、光栅、窗口和屏蔽片等光学元件。由于传统加工的熔石英元件表面含有划痕、抛光沉积层等表面和亚表面缺陷,这些缺陷将导致入射激光在此处产生很强的调制,元件表面及缺陷内部残留的抛光粉对入射激光尤其是紫外激光有很强的吸收,这些因素导致熔石英元件的表面损伤阈值远远低于体损伤阈值。[0003]为去除表面残留抛光沉积层并钝化缺陷,以减小对紫外激光的吸收和调制作用,目前常用的表面处理方法是湿化学刻蚀,如:利用氢氟酸与二氧化硅之间的强化学反应,以一定浓度的氢氟酸作为腐蚀液对熔石英元件进行一定时间刻蚀。该方法能有效、快速去除元件表面残留抛光粉并钝化缺陷,但此方法有两个不足:第一,元件表面形貌不受控,刻蚀后划痕等缺陷尺寸在纵向和横向均会有所增长,若刻蚀时间过短,沉积层和杂质去除不彻底,刻蚀时间过长又将导致元件表面粗糙度增大且可能影响面形,这两种情况都会影响元件的光传输特性,降低元件的抗激光损伤能力,如“熔石英亚表面缺陷原位表征及损伤阈值研究”(参见《光电子.激光》2010,21 (10),1519,蒋勇,袁晓东,向霞等);第二,化学反应产物SiF62—容易沉积在刻蚀表面,反而降低元件的激光损伤阈值。虽然美国采用了兆声波动态酸刻蚀克服了 SiF62—沉积问题,如“HF-Based Etching Processes for Improving LaserDamage Resistance of Fused Silica Optical Surfaces,,(参见Journal of the AmericanCeramic Society2011,94:416, TI Suratwala, PE Miller, JD Bude 等),但表面粗糖度仍然不受控,并且对环境污染大,对设备要求也很高。干法刻蚀如离子束铣是通过含能离子轰击材料表面产生级联碰撞,从而将表面原子溅射出去,这种原子级去除方法对形貌可控,容易获得超光滑表面,平均粗糖度小于0.2nm,如“Morphology evolution of fused silicasurface during ion beam figuring of high-slope optical components,,(参见Applied0ptics2013,52:3719, WL Liao7YF Dai,XH Xie等),但正因为是原子级去除,所以刻蚀效率比较低,加工周期太长。[0004]因此,需要找到一种既能去除熔石英元件表面残留抛光粉并钝化缺陷,同时又能获得良好的表面粗糙度的有效、快速、环保的表面处理方法,从而有效提升熔石英元件的激光损伤阈值。
[0005]本发明提出了一种湿法-干法刻蚀结合提升熔石英元件阈值的表面处理方法。该方法针对传统的研磨抛光工艺加工的熔石英元件的不足,首先采用湿化学刻蚀去除表面残留抛光粉并钝化缺陷,然后采用干刻蚀方法去除湿化学反应产物SiF62—,同时对元件表面粗糙度进行改善,从而获得洁净光滑的表面,即达到了有效并快速提升熔石英元件的激光损伤阈值的目的。[0006]本发明技术方案包括以下步骤:
[0007]步骤1:采用去离子水清洗传统加工的熔石英元件表面;
[0008]步骤2:采用无水乙醇进行超声清洗;
[0009]步骤3:对经步骤2处理后的熔石英元件采用氢氟酸溶液进行刻蚀处理,以去除划痕等亚表面缺陷内部残留的抛光粉并同时对轮廓尖锐的划痕进行钝化处理;
[0010]步骤4:刻蚀完毕后采用去离子水清洗熔石英元件,然后采用无水乙醇对元件脱水;
[0011]步骤5:对经步骤4处理后的熔石英元件采用含能惰性离子束进行表面抛光,去除湿化学反应产物SiF62—,同时获得良好的表面粗糙度。
[0012]其中步骤3中采用的氢氟酸溶液浓度为1%~40%,刻蚀处理时间为I~20分钟。
[0013]其中步骤5中所采用的惰性离子为氩、氪或氙;离子束能量为400~1000eV ;离子束流密度为2~20mA/cm2 ;离子束入射角度为30~70° ;抛光方式为大束斑定点抛光或扫描抛光;抛光时间为5~60分钟。
[0014]本发明提供的湿法-干法刻蚀结合提升熔石英元件阈值的表面处理方法可去除传统的研磨抛光工艺加工的熔石英元件表面残留抛光粉并钝化缺陷,同时又能获得良好的表面粗糙度,克服了湿化学刻蚀增大表面粗糙度的问题和干法离子束刻蚀效率低的缺点。与单一方法相比,本发明能有效快速获得洁净光滑的熔石英表面。因此,本发明可有效、快速的提升熔石英元件的激光损伤阈值,提升熔石英元件的抗激光损伤能力。
[0015]图1为本发明流程示意图。
[0016]图2为实施例1中熔石英元件表面划痕经1%氢氟酸刻蚀10分钟、离子束抛光5分钟和10分钟的光学显微照片。
[0017]实施例1
[0018]传统光学抛光的熔石英元件尺寸为60mmX 60mm,厚度为5mm。首先采用去离子水清洗传统的研磨抛光工艺加工的熔石英元件表面,然后采用无水乙醇进行超声清洗,在1%氢氟酸溶液中刻蚀10分钟、然后再依次用去离子水清洗和无水乙醇脱水后,采用能量为600eV的氩离子束进行表面抛光,抛光方式为大束斑定点抛光,离子束流密度为3mA/cm2,离子入射角度为60°,抛光时间为10分钟。对传统抛光、氢氟酸刻蚀以及离子束抛光三种状态的样品进行表面粗糙度和355nm的紫外激光损伤阈值测试(R-on_l方法),结果如下:粗糙度峰-谷值依次为:21nm、32nm、9nm ;粗糙度均方根值依次为:0.7nm、0.9nm、0.5nm ;损伤阈值依次为:5.3mA/cm2,6.8mA/cm2,8.1mA/cm2。结果表明,湿法-干法刻蚀结合提升熔石英元件阈值的表面处理方法能快速、有效改善熔石英元件表面质量,提升激光损伤阈值。
[0019] 实施例2[0020] 传统光学抛光的熔石英元件尺寸为30mmX30mm,厚度为4mm,首先采用去离子水清洗传统的研磨抛光工艺加工的熔石英元件表面,然后采用无水乙醇进行超声清洗,在5%氢氟酸溶液中刻蚀5分钟、然后再次用去离子水清洗和无水乙醇脱水后,采用能量为400eV的氩离子束进行表面抛光,抛光方式为扫描抛光,扫描速度为200mm/min,离子束流密度为15mA/cm2,离子入射角度为45° ,抛光时间为50分钟。对传统抛光、氢氟酸刻蚀以及离子束抛光三种状态的样品进行表面粗糙度和355nm的紫外激光损伤阈值测试(R-on_l方法),结果如下:粗糙度峰-谷值依次为:18nm、41nm、llnm ;粗糙度均方根值依次为:0.7nm、l.lnm、0.4nm ;损伤阈值依次为:5.1mA/cm2,6.5mA/cm2,8.7mA/cm2。结果表明,湿法_干法刻蚀结合提升熔石英元件阈值的表面处理方法能快速、有效改善熔石英元件表面质量,提升激光损伤阈值。
一种湿法-干法刻蚀结合提升熔石英元件阈值的表面处理方法
- 专利详情
- 全文pdf
- 权力要求
- 说明书
- 法律状态
查看更多专利详情
下载专利文献
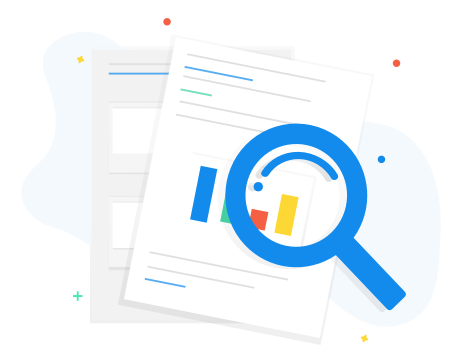
下载专利
同类推荐
-
金凤山曹广斌刘付亚福高惠民
您可能感兴趣的专利
-
邵胜荣邵胜荣罗尔夫·马丁计培春
专利相关信息
-
计培春候清霞候清霞张志健朱克军赫拉巴努什·哈克