专利名称:高粘度熔体纺丝专用组件的制作方法目前国内涤纶工业丝纺丝组件基本是沿袭使用德国巴马格公司原创技术而设计的SP47-6-3061Z型高压纺丝组件,初始压力12MPa以上,最高能达40MPa,其它正在国内企业使用的工业丝纺丝组件大部分都起源于模仿此结构形成的纺丝组件。 另外,阿克佐公司申请中国发明专利92114129. 7中公开了一种自封式纺丝组件,用于高压力高聚物熔体纺长丝,包括一只喷丝板座,里面装入一块喷丝板, 一套过滤结合件,一只活塞似的可以在喷丝板座里面轴向移动的推力件,该推力件有一中心通道,其顶面与分配板底面紧贴,分配板至少有一通道,位于推力件与分配板之间有一顶部密封,中部密封封住过滤组件与喷丝板座之间的空隙,还有一只底部平面密封圈在底部封住喷丝板座。 但该技术中的纺丝组件还存在下述问题 1、过滤有效面积偏小,过滤精度不够高,纺丝使用周期短; 2、喷丝板上部熔体稳压定量流动存在差别,致使每根纤维的纤度有偏差,给高强 纤维的牵伸同步性留下隐患; 3、更换一次组件的替换零部件费用昂贵。
本发明提供一种使用成本低、组装方便、过滤效果好的熔融纺丝专用组件。
本发明对现有技术的改进有两个基本出发点一是只换喷丝板,不轻易更换组件;
二是保证稳压稳态流动,确保熔体流动无死角,流经每个喷丝孔的熔体流量一致。 本发明是通过下述技术方案来实现的,本发明高粘度熔体纺丝专用组件,包括与
纺丝箱体连接的腔体以及位于腔体出口端的喷丝板,所述的腔体内设有 带熔体流道的压盖,压盖的熔体流道入口与纺丝箱体的熔体出口连通; 靠近喷丝板且与喷丝板之间设有稳压室的分配板,分配板是保证流入每个喷丝板
的熔体流量一致的关键零件;稳压室为喷丝板与分配板之间的圆柱腔体; 位于压盖的熔体流道出口及分配板之间的滤网结合件和组件芯,其中所述的滤网
结合件处于组件芯的外围; 熔体依次流经纺丝箱体的熔体出口、压盖的熔体流道后经滤网结合件过滤流入分 配板,最后通过喷丝板喷出熔体细丝。 所述的压盖为轴线处带有熔体流道的圆台形,熔体流道入口位于圆台形的压盖的 顶面,压盖的熔体流道入口与纺丝箱体的熔体流道出口对应,为了保证密封,在纺丝箱体底 面和压盖的顶面之间设有接口垫圈。 所述的滤网结合件由筒状的多孔骨架,以及沿滤网结合件轴线方向反复折叠后附着在多孔骨架外表面的不锈钢纤维滤网构成。 所述的组件芯表面有连续多达几十个瓦棱形成的圆柱体。 腔体的临近组件芯顶面的部位设有环形台阶,用于支撑压盖的碗形垫圈,碗形垫 圈底部置入环形台阶,碗形垫圈顶部向内翻折形成内翻边,压盖底面架设在碗形垫圈的内 翻边上。 组件芯顶面与压盖底面留有用于作为熔体流道的第一间隙,第一间隙由组件芯顶 面中心部位向组件芯顶面边缘部位逐渐变窄。 腔体的临近滤网结合件部位的内壁由上至下逐渐縮小直至紧贴滤网组件外壁,使 滤网结合件外壁与腔体的内壁之间形成作为熔体流道的第二间隙,第二间隙与第一间隙相 互连通。第二间隙由上至下逐渐变窄,第二间隙与第一间隙在组件芯顶面的外缘部位连通。
滤网结合件顶部通过铝垫圈紧贴组件芯上沿下壁,滤网结合件底部通过铝垫圈紧 贴分配板上表面,随着组件芯直径由上至下逐渐縮小,滤网结合件内壁与组件芯外壁之间 形成作为熔体流道的第三间隙,第二间隙通过滤网结合件与第三间隙相互连通,第三间隙 由上至下逐渐变宽。 组件芯的底面为中心部位略突出的锥面,该锥面顶点在受压后顶紧分配板上表 面,组件芯底面与分配板上表面之间从组件芯底面的中心部位向组件芯底面的外缘形成作 为熔体流道的第四间隙,第四间隙与第三间隙相互连通。第四间隙与第三间隙在组件芯底 面边缘部位相互连通,第四间隙由组件芯底面边缘向组件芯底面中心部位部位逐渐变狭。
组件芯顶部带有环形台阶,滤网结合件顶面紧贴组件芯顶部外台阶的底面,滤网 结合件顶面内缘紧贴组件芯的台阶的根部。 腔体底部设有环形内凸缘,环形内凸缘上置有铝垫片,所述的滤网结合件底面顶 紧铝垫片。 所述的喷丝板通过法兰紧固在腔体出口端,喷丝板顶面与分配板底面之间留有稳 压室,喷丝板顶面覆盖有包边滤网,包边滤网为三层不同目数的滤网。 分配板底面外缘设有环形凸起,包边滤网的边缘被夹紧在喷丝板顶面和分配板底 面的环形凸起之间。 适当容积的稳压室能保证熔体稳压稳态流动,确保流经喷丝板的每个喷丝孔的熔
体流量一致,稳压室的高度为2 4. 5mm,根据泵供量大小,可以人为调整。 熔体流经压盖的熔体流道后,依次流经第一间隙、第二间隙、第三间隙和第四间隙
后进入分配板。熔体流经分配板后进入稳压室,最终经稳压调整后流入喷丝板导孔,并通过
与导孔直连的毛细孔喷出熔体,进行高粘度熔体的喷丝操作。 所述的滤网结合件采用折叠式的滤网,可提高过滤面积4 5倍,滤网展开面积达 800cm2 ;过滤精度为30 40iim时组件的使用周期为45 60天,从而拦截了更多的杂质 和凝胶粒子提高了纺丝质量,大大延长了过滤周期。 本发明高粘度熔体纺丝专用组件中,对过滤组件的结构以及过滤组件附近的熔体 流道做了很大改进,过滤组件附近的熔体流道即第一间隙、第二间隙、第三间隙和第四间隙 的宽度(在通过腔体轴线的纵截面上的宽度)采用了适宜的渐变,使第一间隙、第二间隙、 第三间隙和第四间隙的任何一个断面基本做到熔体流速均匀,流动无死角,熔体经历的热 历史基本一致。
4
本发明高粘度熔体纺丝专用组件使用成本低、组装拆卸方便、过滤效果好,熔体流 道内的流体能保持稳压稳态流动,熔体流动无死角,喷丝时流经喷丝板每个毛细孔的流量
基本一致。
图1是本发明高粘度熔体纺丝专用组件的剖面示意图。
图2是图1中A部放大图。
参看图1、2,本发明高粘度熔体纺丝专用组件包括用于与纺丝箱体12连接的腔体
1以及位于腔体1出口端的喷丝板9。 腔体1带有筒状的壳壁,腔体1内设有 带熔体流道的压盖3,压盖3的熔体流道入口与纺丝箱体的熔体出口连通;
靠近喷丝板9且与喷丝板9之间留有稳压室的分配板14 ; 位于压盖3的熔体流道出口及分配板14之间的滤网结合件和组件芯6,其中滤网 结合件处于组件芯6的外围; 压盖3为轴线处带有熔体流道的圆台形零件,熔体流道入口位于圆台形的压盖3 的顶面,压盖3的熔体流道入口与纺丝箱体12的熔体流道出口对接应,在纺丝箱体12底面 和压盖3的顶面之间设有接口垫圈2。 滤网结合件7由筒状的多孔骨架19,以及沿滤网结合件7轴线方向反复折叠后附 着在多孔骨架19外表面的滤网20构成。 组件芯6侧表面为连续瓦棱形成的圆柱体曲面,腔体1的临近组件芯6顶面的部 位设有四个凸台,该凸台上设有用于支撑压盖3的碗形垫圈4,碗形垫圈4内壁置入四个凸 台上,碗形垫圈4顶部向内翻折形成内翻边,压盖3底面的外缘架设在碗形垫圈4的内翻边 上。 图2中可见,组件芯6顶面与压盖3底面留有用于作为熔体流道的第一间隙15,第
一间隙15由组件芯6顶面中心部位向组件芯6顶面边缘部位逐渐变窄。 腔体1的临近滤网结合件7部位的内壁由上至下逐渐縮小直至紧贴滤网结合件7
外壁,使滤网结合件7外壁与腔体1的内壁之间形成作为熔体流道的第二间隙16,第二间隙
16与第一间隙15相互连通。第二间隙由上至下逐渐变窄,第二间隙16与第一间隙15在组
件芯6顶面的外缘部位连通。 滤网结合件7顶部紧贴组件芯6外壁,滤网结合件7底沿紧贴分配板14上表面, 随着组件芯6直径由上至下逐渐縮小,滤网结合件7内壁与组件芯6外壁之间形成作为熔 体流道的第三间隙17,第二间隙16透过滤网结合件7与第三间隙17相互连通,第三间隙 17由上至下逐渐变宽。 组件芯6的底面为中心部位略突出的锥面,该锥面顶点顶紧分配板14上表面,组 件芯6底面与分配板14上表面之间从组件芯6底面的中心部位向组件芯6底面的外缘形 成作为熔体流道的第四间隙18。第四间隙18与第三间隙17在组件芯6底面边缘部位相互 连通,第四间隙18由组件芯6底面中心部位向组件芯6底面边缘部位逐渐变宽。
组件芯6顶部带有四个凸台,滤网结合件7顶面紧贴组件芯6顶部凸台的底面,滤 网结合件7顶面内缘紧贴组件芯6的凸台的根部。 腔体1底部设有环形内凸缘,环形内凸缘上置有铝垫片5,滤网结合件7底面顶紧 铝垫片5的顶面。 喷丝板9利用螺栓10通过法兰8紧固在腔体1出口端,喷丝板9顶面与分配板14 底面之间留有稳压室,喷丝板9顶面覆盖有包边滤网ll,包边滤网11为三层的滤网。分配 板14底面外缘设有环形凸起,包边滤网11的边缘被夹紧在喷丝板9顶面和分配板14底面 的环形凸起之间,稳压室的高度可以通过调整包边滤网11的厚度来改变。
分配板14的外缘顶部顶靠在腔体1底部,分配板14的外缘底部通过焊接固定在 腔体1底部,焊口部位21再磨削加工至平面,分配板14上面孔的分布和直径可以通过现有 技术计算,以确保熔体流量均匀。 本发明高粘度熔体纺丝专用组件安装方式是将每个已清洗过的零部件备好,先 用法兰8,螺栓10将表面附着好包边滤网11的喷丝板9紧固在腔体1底部。
再向腔体1内部放入铝垫片5、滤网结合件7再放入铝垫片,放入组件芯6、碗形垫 圈4、压盖3、接口垫片2。本发明高粘度熔体纺丝组件组装完毕。 将预热过的纺丝组件放置到机械手上,通过腔体1内T形螺纹连接到纺丝组件12 里,随着腔体1的旋紧,纺丝箱体对压盖3产生向下的压力,碗形垫圈4受压,在压力的作用 下碗形垫圈4与压盖3及腔体组件1贴紧,因为碗形垫圈4为自紧式密封垫圈, 一旦组件充 满熔体产生压力后,可实现自紧式密封。 在正常工作时,在熔体压力的作用下组件芯6会逐渐下移,铝垫片5与组件芯6、滤 网结合件7及腔体1贴紧,实现工作密封。 如1图所示,本发明高粘度熔体纺丝专用组件工作时熔体沿箭头a所示方向经进 纺丝箱体12底部出口进入压盖3的熔体流道,熔体流经压盖3的熔体流道后,依次流经第 一间隙15、第二间隙16、再经过滤网结合件7的精密过滤后进入第三间隙17和第四间隙18 再进入分配板14。 熔体通过分配板14的分配孔后进入稳压室,在经过包边滤网11的过滤稳压进入 喷丝板9,并通过喷丝板9上的毛细孔沿箭头b方向喷出熔体(图中采用省略画法,省略了 喷丝板9上的喷丝孔),进行高粘度熔体的纺丝运行。 设定某一工业丝规格后,若按每分钟333. 3克熔体流量计,在组件内的停留时间 不超过1. 8分钟,组件内部压力上升缓慢,为高压自封式,组装方便,拆卸简单,本发明可独 立更换喷丝板9,大大减少组件更换成本,即使更换整体组件,其成本也仅原先的一半。
本发明公开了一种高粘度熔体纺丝专用组件,包括与纺丝箱体连接的腔体以及位于腔体出口端的喷丝板,所述的腔体内设有带熔体流道的压盖,压盖的熔体流道入口与纺丝箱体的熔体出口连通;靠近喷丝板且与喷丝板之间设有稳压室的分配板;位于压盖的熔体流道出口及分配板之间的滤网结合件和组件芯,其中所述的滤网结合件处于组件芯的外围;熔体依次流经纺丝箱体的熔体出口、压盖的熔体流道后经滤网结合件过滤流入分配板,最后通过喷丝板喷出熔体细丝。本发明高粘度熔体纺丝专用组件加工费省、改换成本低、组装拆卸方便、过滤效果好,熔体流道内的流体稳压稳态流动,熔体流道无死角,喷丝均匀。
高粘度熔体纺丝专用组件制作方法
- 专利详情
- 全文pdf
- 权力要求
- 说明书
- 法律状态
查看更多专利详情
下载专利文献
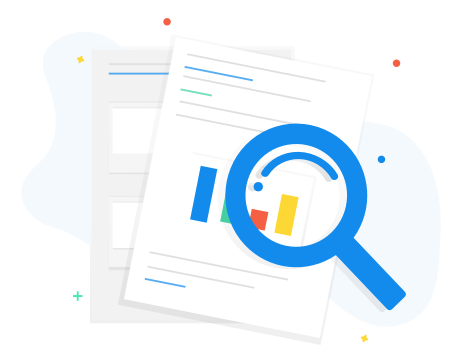
下载专利
同类推荐
-
宋云昌刘让同刘让同张晨, 张森林J.D.克罗斯
您可能感兴趣的专利
-
J.D.克罗斯刘为民J·伊罗拉J·伊罗拉李琦
专利相关信息
-
孙军伟孙军伟孙军伟朱志华, 谢国强卢秀强