专利名称:一种萃取-酯交换-分离偶联技术制备生物柴油的方法随着全球性能源日益严重的短缺与环境恶化,控制汽车尾气排放,保护人类赖以生存的自然环境成为当前人类急需解决的问题。世界各国的研究人员从环境保护和资源战略的角度出发,积极探索发展替代燃料及可再生能源,生物柴油就是其中一种。生物柴油作为一种新型的环境友好能源,是未来能源发展和利用的重点,生物柴油制备受到了越来越多的关注,生物柴油制备方法的改进将会对生物柴油产业化推进和应用起到更大的作用。生物柴油是指以动植物油脂包括草本植物油、木本植物油、动物油、废弃油脂(如地沟油)藻油为原料和短链醇(如甲醇、乙醇)在催化剂作用下通过酯交换反应生成的长链脂肪酸酯。生物柴油的主要成分是脂肪酸甲酯(FAME),是以可再生资源(如菜籽油、大豆油、玉米油、棉籽油、花生油、棕榈油、回收烹饪油及动物油等)为原料而制成,具备与石油柴油相近的性能。传统的生物柴油制备方法首先要经过复杂的原料油萃取,毛油精制后,再经过化学催化,或生物酶催化等方法进行酯交换反应,然后进行复杂的后续分离,操作流程复杂, 时间较长。生物柴油制备方法的研究主要集中在化学催化法,生物法和新型强化技术如超临界法和超声波法等。固体碱和固体酸催化也越来越受到更多的关注。在产业中规模化应用的酯交换是液体碱催化法和液体酸催化法。其中以氢氧化钾或氢氧化钠为催化剂的液体碱催化法因具有转化率高、反应条件温和、反应速率快等优势成为生物柴油工业生产的主要方法。但在反应的过程中易发生皂化反应,不利于后续分离。(张哲,魏海国.生物柴油生产技术进展.石油规划设计,2009,20 (I) =23-27.)Saka等对菜籽油与超临界甲醇的反应进行了研究。结果发现超临界甲醇法制备生物柴油原料适用性广、无催化剂产物分离简单,从而使该方法成为一种良好的生物柴油制备方法。但该方法反应时间长,温度要求较高,压力大,对设备要求也比较高,能耗量大。 (Chinese Journal Of Applied Chemistry,2006,23(12) 1332-1335)Siegfried Warwel等以乙醇和乙烧或碳酸二乙酯作为萃取剂,同时向其中加入脂肪酶Novozym 435进行萃取-酯交换反应,此种方法时间短,产量高,但不利于酶的回收利用,并且使酶的活性降低。同时有机溶剂萃取后还要处理。(Tjahjono Herawan. Lipase-catalyzed transterification of plant oils with dialkyl carbonates[D]. Aachen Rheinisch-ffestf lische Technische Hochschule Aachen,2004.)DBU、DBN、TBD, MTBD等脒类或胍类物质具有强碱性,但却是弱的亲核试剂,易与质子结合而不易与碳原子结合,因此他们的应用主要是作为强碱性试剂,起到碱或催化剂的作用。其中DBU又称双环脒,化学名是I,8-二氮杂二环-双环(5,4,0)-7-i烯,DBN的化学名是I,5-二氮杂双环[4. 3.0]壬-5-烯,TBD的化学名1,5,7-三氮杂二环[4.4.0] 癸-5-烯,MTBD的化学名1,5,7-三氮杂二环[4.4.0]。DBU —类物质是一种极性可以可逆转化的,向DBU和醇中通入二氧化碳可以使其发生反应转化为重碳酸盐离子态,并且这一过程可以通过向其中通入氮气达到可逆进行。
本发明提供了一种用脒类或胍类强碱性物质作为萃取剂兼催化剂,萃取-酯交换-分离偶联的方法生产生物柴油,解决了目前有机溶剂萃取时产生的大量污染以及生物柴油制备流程复杂等问题,此过程工艺设备简便,操作简单,反应条件温和,利于萃取溶剂兼催化剂的回收利用,适于工业化生产。本发明的技术方案是将原料油料与低碳醇、溶剂脒类或胍类物质混合于一个反应器中,使萃取与酯交换反应同时进行,然后利用脒类或胍类物质的可逆转化的性质,将其与生物柴油相及甘油相分离,最后重新转化回收再利用,其具体过程为萃取-酯交换反应的过程为按一定的比例将原料油料与低碳醇、脒类或胍类物质混合,原料油料低碳醇=I 50-1 350(mOl/mOl),溶剂脒类或胍类物质的量为原料油料质量的5% -85%,温度为20-90°C,搅拌使萃取、酯交换反应同时进行,反应时间 O. 5-6h,反应结束后抽滤将原料与反应后液体分离;分离过程为抽滤后液体分为生物柴油相和甘油相,此时两相中均含有催化剂, 利用脒类或胍类物质的可逆转化特性,向生物柴油相中通入二氧化碳,条件为气体流量为 16-160ml/min,时间为2min_2h,温度为20_80°C,使其与醇反应转化为极性的离子液体,与生物柴油分离;向甘油相加入脂肪酸或脂肪酸酯继续进行酯交换反应,甘油与酸或酯的摩尔比为I : 1-1 6,反应温度为20-80°C,反应时间为O. 5-6h,生成甘二酯和单甘酯,再向其中通入二氧化碳使催化剂与醇反应转化为离子液体而与酯相分离;催化剂回收过程向分离后的离子态催化剂中通入氮气置换出二氧化碳,时间为 2min-2h ;流量为16ml/min-160ml/min,使其极性减弱转化为非离子态,回收重复利用萃取溶剂兼催化剂。萃取-酯交换-分离偶联技术中的原料可以是藻粉,动物脂肪,文冠果,麻风树籽, 棉籽,大豆,花生,菜籽,玉米胚芽等植物油籽。萃取-酯交换-分离偶联技术中的低碳醇通常是指碳原子数在1-10的直链或支链醇。萃取-酯交换-分离偶联制备生物柴油过程中,既作为萃取溶剂又作为催化剂的物质主要包括DBU(1,8- 二氮杂二环-双环(5,4,0)-7- i^一烯)、DBN(1,5_ 二氮杂双环 [4. 3. O]壬-5-烯)、TBD(1,5,7-三氮杂二环[4.4.0]癸-5-烯)、MTBD (I,5,7-三氮杂二环[4.4.0])等脒类或胍类物质。与现有技术相比,本发明的效果和益处是脒类或胍类物质在整个过程中既作为萃取剂又作为催化剂,而将原料油萃取和酯交换反应以及分离偶联在一个体系中,工艺设备简便,避免了有机试剂萃取产生大量污染, 简化流程,操作简单,反应条件温和,利于催化剂回收利用,适于工业化生产。(4)向甘油相中加入与其摩尔比为I : 3的甘三酯,在40°C下反应2h,使其继续反应生成甘二酯或单甘酯,40°C下再向其中通入15min流量为40ml/min的二氧化碳,使DBN转化为极性较强的离子液体,而与酯相分离。(5)然后向转化为离子态的催化剂中通入15min氮气,流量为40ml/min,温度为40°C,置换出二氧化碳使其极性减弱转化为非离子态,回收重复利用DBN。实施例四(1)将2. OOg的大豆粉碎,与8. 41g的异丙醇混合,向其中加入O. 40g的 DBU,在50°C条件下加热搅拌反应2h,经抽滤将粉末与液体分离,液体取样分析其生物柴油转化率达98. 7%。(2)将抽滤后粉末用70ml正己烷索氏萃取,经分析计算得DBU的萃取率达98. 1%。(3)将生物柴油相与甘油相分离后,向生物柴油相中通入20min 二氧化碳,流量为45ml/min,温度为50°C,使DBU转化为极性较强的离子液体,自动与生物柴油分离。(4) 向甘油相中加入与其摩尔比为I : 2. 5的月桂酸,在50°C下反应3h,使其继续反应生成甘二酯或单甘酯,50°C下再向其中通入20min流量为45ml/min的二氧化碳,使DBU转化为极性较强的离子液体,而与酯相分离。(5)然后向转化为离子态的催化剂中通入20min氮气, 流量为45ml/min,温度为50°C,置换出二氧化碳使其极性减弱转化为非离子态,回收重复利用DBU。实施例五(I)将3. OOg的文冠果籽仁粉碎,与12. 33g的辛醇混合,向其中加入 O. 75g的DBU,在60°C条件下回流加热搅拌反应2. 5h,经抽滤将粉末与液体分离,液体取样分析其生物柴油转化率达98. 9%。(2)将抽滤后粉末用70ml正己烷索氏萃取,经分析计算得DBU的萃取率达98. 7%。(3)将生物柴油相与甘油相分离后,向生物柴油相中通入二氧化碳lh,流量为80ml/min,温度为60°C,使DBU转化为极性较强的离子液体,自动与生物柴油分离,然后再回收重复利用DBU。(4)向甘油相中加入与其摩尔比为I : 4的棕榈酸,在 50°C下反应4h,使其继续反应生成甘二酯或单甘酯,60°C下再向其中通入Ih流量为80ml/ min的二氧化碳,使DBU转化为极性离子液体,而与酯相分离。(5)然后向转化为离子态的催化剂中通入Ih氮气,流量为80ml/min,温度为60°C,置换出二氧化碳使其极性减弱转化为非离子态,回收重复利用DBU。实施例六⑴将4. OOg的菜籽仁粉碎,与15. 50g的甲醇混合,向其中加入I. 20g 的TBD,在70°C条件下回流加热搅拌反应3h,经抽滤将粉末与液体分离,液体取样分析其生物柴油转化率达99. 6%。(2)将抽滤后粉末用70ml正己烷索氏萃取,经分析计算得DBU的萃取率达99. 0%。(3)将生物柴油相与甘油相分离后,向生物柴油相中通入I. 5h二氧化碳, 流量为100ml/min,温度为60°C,使TBD转化为极性较强的离子液体,自动与生物柴油分离。(4)向甘油相中加入与其摩尔比为I : 5的油酸,在60°C下反应5h,使其继续反应生成甘二酯或单甘酯,65°C下再向其中通入I. 5h流量为120ml/min的二氧化碳,使TBD转化为极性较强的离子液体,而与酯相分离。(5)然后向转化为离子态的催化剂中通入I. 5h氮气,流量为100ml/min,温度为60°C,置换出二氧化碳使其极性减弱转化为非离子态,回收重复利用 TBD。实施例七(I)将5. OOg的棉籽仁粉碎,与15. 50g 丁醇混合,向其中加入I. 5g的 MTBD,在60°C条件下回流加热搅拌反应4h,经抽滤将粉末与液体分离,液体取样分析其生物柴油转化率达99. 8%。(2)将抽滤后粉末用70ml正己烷索氏萃取,经分析计算得MTBD 的萃取率达99. 3%。(3)将生物柴油相与甘油相分离后,向生物柴油相中通入2h 二氧化碳,流量为150ml/min,温度为70°C,使MTBD转化为极性较强的离子液体,自动与生物柴油分离。(4)向甘油相中加入与其摩尔比为I : 3的亚油酸,在70°C下反应lh,使其继续反应生成甘二酯或单甘酯,70°C下再向其中通入2h流量为150ml/min的二氧化碳,使MTBD转化为极性较强的离子液体,而与酯相分离。(5)然后向转化为离子态的催化剂中通入2h氮气, 流量为150ml/min,温度为70°C,置换出二氧化碳使其极性减弱转化为非离子态,回收重复利用MTBD。实施例八⑴将2. OOg文冠果籽仁粉碎,与4. 66g甲醇混合,向其中加入O. IOg的 DBN,在60°C条件下加热搅拌反应5h,经抽滤将粉末与液体分离,液体取样分析其生物柴油转化率达96. 3%。(2)将抽滤后粉末用70ml正己烷索氏萃取,经分析计算得DBN的萃取率达95. 1%。(3)将生物柴油相与甘油相分离后,向生物柴油相中通入I. 5h 二氧化碳,流量为160ml/min,温度为80°C,使DBN转化为极性较强的离子液体,自动与生物柴油分离。(4)向甘油相中加入与其摩尔比为I : 6的甘三酯,在80°C下反应2h,使其继续反应生成甘二酯或单甘酯,80°C下再向其中通入2h流量为160ml/min的二氧化碳,使DBN转化为极性较强的离子液体,而与酯相分离。(5)然后向转化为离子态的催化剂中通入I. 5h氮气,流量为160ml/min,温度为80°C,置换出二氧化碳使极性减弱其转化为非离子态,回收重复利用 DBN。
一种萃取-酯交换-分离偶联技术制备生物柴油的方法,属于新能源生产技术领域。采用碱性脒类物质或胍类物质作为萃取溶剂兼催化剂,将萃取、酯交换反应和分离偶联起来制备生物柴油。将含油原料与低碳醇、脒类或胍类催化剂混合,搅拌加热,使萃取、酯交换反应同时进行;液固分离,通过沉降分离将液相中甘油和生物柴油分离,再利用脒类或胍类物质与醇在通入二氧化碳的条件下反应转化为极性的离子液体而使其分别与生物柴油、甘油分离;然后向离子液体中通入氮气使其可逆转化为非离子态而回收重复利用。本发明将原料油的萃取和酯交换反应以及产物分离偶联在一个体系中进行,设备简单,清洁环保,制备流程少,反应温和,利于回收利用,工业化前景好。
一种萃取-酯交换-分离偶联技术制备生物柴油的方法
- 专利详情
- 全文pdf
- 权力要求
- 说明书
- 法律状态
查看更多专利详情
下载专利文献
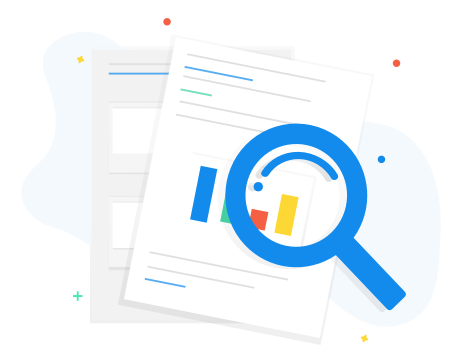
下载专利
同类推荐
-
杨天奎杨天奎王红胜
您可能感兴趣的专利
-
A·O·宗韩成美K-C·林, R·威德曼刘顺兴C.D.齐尔巴
专利相关信息
-
C.D.齐尔巴C.D.齐尔巴C.D.齐尔巴C.D.齐尔巴D. 齐尔巴 C.D. 齐尔巴 C.杨顺才, 蔡军