高强蒸压粉煤灰砖成型工艺制作方法
- 专利详情
- 全文pdf
- 权力要求
- 说明书
- 法律状态
专利名称:高强蒸压粉煤灰砖成型工艺的制作方法本发明涉及一种粉煤灰砖的加工工艺,尤其涉及高强蒸压粉煤灰砖的成型工艺。这种工艺对坯料的加压采用分阶段方式。分阶段加压方式可以分三个阶段:a.预压阶段;b.压制成型阶段;c.保持阶段。所用坯料的含水量为13~24%。采用本工艺水化反应较为充分,砖的抗压强度可提高至26MPa,是原来的2~3倍;干缩值降至0.4mm/m,只有原来的二分之一。
查看更多专利详情
下载专利文献
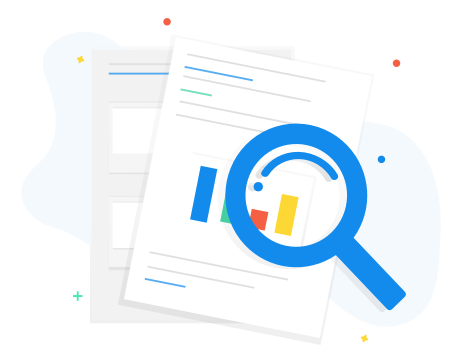
下载专利
同类推荐
-
彭威秦升益秦升益秦升益秦升益王小锋
您可能感兴趣的专利
-
佘志清王卫东胡海军
专利相关信息
-
李欢欢李欢欢迈克尔·R·贝里根迈克尔·R·贝里根孟宪安孟宪安