专利名称:一种丹参酚酸类成分提取除杂方法丹参具有活血化瘀、养血安神等功效。在临床上以丹参为君药的(单、复方)注射液或滴注液用于心血管疾病的疗效确切,而毒副作用较小,故需求量较大。据统计,目前SFDA颁布的丹参类注射液生产批文已多达近100余张,所采用的提取除杂工艺几乎均是传统的三水提二醇沉一水沉,如现有的丹参滴注液国家标准工艺简易流程是丹参水提3次(8 10倍水量/次)一浓缩一75%醇沉I次一浓缩一碱水解I次一85%醇沉I次一浓缩一酸水沉I次一配制。除杂效果肯定,但因醇沉前各类机械颗粒、异物、大分子的蛋白、纤维、果胶、鞣 质、淀粉、微生物等杂质未经处理,在醇沉特别是在第一次醇沉时,这些杂质较快沉淀析出并将“高浓度料液”包裹,故使有效成分损失较大。且生产周期长、能耗大、乙醇用量大,故生产成本较高。丹参中的酚酸类活性成分的分子量小的不足100,大的不超I 000,而需要除去的淀粉、蛋白质等非活性成分的分子量则大多在50 000以上(参见文献孙福东,王淑玲,王英姿.膜分离技术在中药提取与制剂研究中的应用[J].齐鲁药事,2008. 27(4):226-228)。因此选用3 000 10 000截留分子量的超滤膜进行超滤,即能够滤除水煎液中的大分子杂质而保留小分子量的活性成分,所以可以取代醇沉工艺,提取的丹参素钠可达9mg/g生药、原儿茶醛可达2 mg/g生药以上,且酒精物耗和浓缩能耗降低、生产周期减少,提取收率增加,故单耗成本大大降低。离心处理主要是中药水煎液有较多悬浮的难以过滤的固体微粒和胶体粒子,是造成膜污染和膜通量低下的最主要因素,而离心则是将这些微粒沉降除去的最有效操作。
本发明的目的即为提供一种简单、有效并能最大限度减少有效组分群损失的除杂方法。本发明的目的可以通过以下技术方案来实现 一种丹参酚酸类成分提取除杂方法,其步骤包括 I丹参原药材或饮片,用纯化水提取3次。2提取液减压浓缩至相对密度I. 10 I. 15 (60 70°C),冷藏12 24小时。3用每分钟4500转以上的碟式沉降分离机进行离心,取清液。4用每分钟8000转以上的管式高速离心机进行离心,取清液。5用不大于O. 22微米的无机陶瓷膜进行超滤,取透过液。6用40% (g/ml)盐酸溶液调节pH至9,煮沸I小时,再用4mol/L盐酸溶液调节pH至6,冷藏12 24小时。7用每分钟8000转以上的管式高速离心机进行离心,取清液。8用4mol/L盐酸溶液调节pH至4,煮沸,加O. 1% O. 3% (g/ml)针用活性炭,保温搅拌20 30分钟,滤过,冷藏12 24小时。9用每分钟8000转以上的管式高速离心机进行离心,取清液。10加注射用水至相对密度I. 01 I. 05(60 70°C),用4mol/L盐酸溶液调节pH至2 3,冷藏24 36小时。11用每分钟8000转以上的管式高速离心机进行离心,取清液。12用3000 10000截留分子量的超滤膜进行超滤,透过液即为丹参精制液——用于制备丹参注射液或滴注液的配制原料。·
实施例I
步骤I.取300kg净制丹参原药材,用8、8、6倍量纯化水煎煮提取3次。每次2小时,滤过,三次提取液合并。步骤2.提取液减压浓缩至相对密度I. 10 (60°C),冷藏12小时。步骤3.用每分钟4500转碟式沉降分离机进行离心,取清液。步骤4.用每分钟10 000转管式高速离心机进行离心,取清液。步骤5.用O. 22微米的无机陶瓷膜进行超滤,取透过液。步骤6.用40% (g/ml)盐酸溶液调节pH至9,煮沸I小时,再用4mol/L盐酸溶液调节pH至6,冷藏12小时。步骤7.用每分钟10 000转的管式高速离心机进行离心,取清液。步骤8.用4mol/L盐酸溶液调节pH至4,煮沸,加O. 1% (g/ml)针用活性炭,保温搅拌30分钟,滤过,冷藏12小时。步骤9.用每分钟10 000转管式高速离心机进行离心,取清液。步骤10.加注射用水至相对密度I. 01(60°C),用4mol/L盐酸溶液调节pH至2. 5,冷藏24小时。步骤11.用每分钟10 000转管式高速离心机进行离心,取清液。步骤12.用5000截留分子量的超滤膜进行超滤,透过液即为丹参精制液——用于制备丹参注射液或滴注液的配制原料。实施例2
步骤I.取300kg净制丹参原药材,用8、8、6倍量纯化水煎煮提取3次。每次2小时,滤过,三次提取液合并。步骤2.提取液减压浓缩至相对密度I. 15 (70°C),冷藏24小时。步骤3.用每分钟4500转碟式沉降分离机进行离心,取清液。步骤4.用每分钟10 000转管式高速离心机进行离心,取清液。步骤5.用O. 22微米的无机陶瓷膜进行超滤,取透过液。步骤6.用40% (g/ml)盐酸溶液调节pH至9,煮沸I小时,再用4mol/L盐酸溶液调节pH至6,冷藏24小时。步骤7.用每分钟10 000转的管式高速离心机进行离心,取清液。
步骤8.用4mol/L盐酸溶液调节pH至4,煮沸,加O. 3% (g/ml)针用活性炭,保温搅拌30分钟,滤过,冷藏24小时。步骤9.用每分钟10 000转管式高速离心机进行离心,取清液。步骤10.加注射用水至相对密度I. 05 (70°C),用4mol/L盐酸溶液调节pH至3,冷藏36小时。步骤11.用每分钟10 000转管式高速离心机进行离心,取清液。步骤12.用8000截留分子量的超滤膜进行超滤,透过液即为丹参精制液一用于制备丹参注射液或滴注液的配制原料。实施例3
步骤I.取300kg净制丹参原药材,用8、8、6倍量纯化水煎煮提取3次。每次2小时,滤过,三次提取液合并。步骤2.提取液减压浓缩至相对密度I. 12 (65°C),冷藏24小时。步骤3.用每分钟4500转碟式沉降分离机进行离心,取清液。步骤4.用每分钟10 000转管式高速离心机进行离心,取清液。步骤5.用O. 22微米的无机陶瓷膜进行超滤,取透过液。步骤6.用40% (g/ml)盐酸溶液调节pH至9,煮沸I小时,再用4mol/L盐酸溶液调节pH至6,冷藏18小时。步骤7.用每分钟10 000转的管式高速离心机进行离心,取清液。步骤8.用4mol/L盐酸溶液调节pH至4,煮沸,加O. 2% (g/ml)针用活性炭,保温搅拌25分钟,滤过,冷藏18小时。步骤9.用每分钟10 000转管式高速离心机进行离心,取清液。步骤10.加注射用水至相对密度1.03 (65°C),用4mol/L盐酸溶液调节pH至2,冷藏30小时。步骤11.用每分钟10 000转管式高速离心机进行离心,取清液。步骤12.用10000截留分子量的超滤膜进行超滤,透过液即为丹参精制液——用于制备丹参注射液或滴注液的配制原料。本发明通过丹参滴注液提取工艺方法的改进,用超滤除杂的方法替代丹参滴注液提取部分的75%及85% 二次醇沉。实验结果显示本发明的制备方法能够大幅降低生产周期和原辅料成本,并能够显著提高丹参精制液中有效成分丹参素和原儿茶醛的含量,收率大于82%,所得产品质量稳定。
本发明涉及一种用于制备注射剂的中药提取液的除杂方法。其步骤包括丹参原药材或饮片,用纯化水提取;提取液减压浓缩、冷藏;经离心,取清液;超滤,取透过液;煮后调节pH;冷藏后进行离心,取清液;调节pH,煮沸,保温搅拌,滤过,冷藏后进行离心,取清液;用3000~10000截留分子量的超滤膜进行超滤,透过液即为丹参精制液——用于制备丹参注射液或滴注液的配制原料。
一种丹参酚酸类成分提取除杂方法
- 专利详情
- 全文pdf
- 权力要求
- 说明书
- 法律状态
查看更多专利详情
下载专利文献
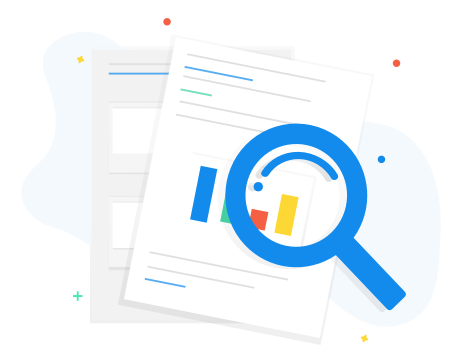
下载专利
同类推荐
-
江善祥, 沈克姑王绍宗
您可能感兴趣的专利
-
克提·瑞屋, 瓦斯里奥斯·帕帕佐普洛斯刘樟艳崔为正
专利相关信息
-
付铁军, 李伯刚周嘉琳刘云华