专利名称:玻璃板的制造方法在用于液晶显示屏或等离子体显示屏等平板显示器(下文称为FPD)的玻璃基板中,例如以厚度为0.5mm 0.7mm、尺寸为300mmX 400mm 2850mmX 3050mm玻璃板为主流。作为Fro用玻璃基板的制造方法,已知有溢流下拉法。溢流下拉法中,通过在成形炉中使熔融玻璃从熔融玻璃成形体的上部溢出而成形为板状玻璃,将成形后的板状玻璃缓慢冷却、并将其切断。之后,按照客户的规格将切断后的板状玻璃再切断成规定的尺寸,进行清洗、端面研磨等,进行发货。Fro用玻璃基板中、特别是液晶显示装置用玻璃基板中,在其表面形成有半导体元件,因此优选完全不含有碱金属成分或者即使含有也是对半导体元件等不会产生影响的程度的微量。另外,若在玻璃基板中存在气泡,则其成为显露缺陷的原因,因而有气泡存在的玻璃基板无法作为Fro用玻璃基板来使用。因此,要求在玻璃基板中无气泡残留。在玻璃基板的制造中,去除熔融玻璃的气泡的技术被称为澄清,该澄清中,利用As2O3等澄清剂的氧化还原反应来去除气泡。更具体地说,进一步提高粗熔解的熔融玻璃的温度,使澄清剂发挥功能而使气泡上浮、脱泡,其后通过降低温度而使未脱泡而残留的小泡溶解吸收在玻璃内。作为澄清剂,除As2O3外,近年来从环境负荷方面出发,还使用SnO2或Fe2O3等来代替As203。如上所述,对于完全不含有碱金属成分或碱金属成分为微量的玻璃基板的情况,与钠I丐玻璃等大量含有碱金属的玻璃基板相比,其高温粘性高、难以从制造中的熔融玻璃中去掉气泡,因而需要更高的澄清效果。另一方面,已知有下述澄清技术:通过使电流流经由钼或钼合金构成的管的澄清槽中来对澄清槽加热(通电加热),并使熔融玻璃在该加热后的澄清槽中流通,由此来提高熔融玻璃的温度,进行澄清。(专利文献I)。现有技术文献专利文献专利文献1:日本特表2011-502934号公报
发明所要解决的课题在将由钼或钼合金的管构成的澄清槽加热来提高熔融玻璃的温度时,熔融玻璃的温度有时不能均匀加热。例如,如图5所示,在通过管的熔融玻璃之中,由于与在壁面阻力大的管壁面附近流动的熔融玻璃的流速相比,在管路中心附近流动的熔融玻璃的流速更快,而且由于距离经加热的管的壁面远,因而在管路中心附近流动的熔融玻璃的温度低于在管壁面附近流动的熔融玻 璃的温度,未能上升到澄清所必须的温度,具有澄清不充分这样的问题。该问题也为在电流流经由钼或钼合金的管构成的澄清槽中的情况下所发生的问题。另外,在为了提高管中心附近的温度而增加由钼或者钼合金构成的澄清槽的加热量时,会促进钼或者钼合金的挥发,具有澄清槽的寿命缩短的问题。特别是近年来从环境负荷的方面出发在使用SnO2作为澄清剂来代替As2O3的情况下,由于使熔融玻璃的温度高于使用As2O3的情况的温度,因而愈加具有钼或者钼合金挥发的问题。因此对由钼或者钼合金构成的管进行过剩加热乃不利状况。另外,在澄清槽中,通过形成气泡易上浮的粘度可促进脱泡,但是,例如关于在液晶显示装置用玻璃基板等中优选使用的无碱玻璃,由于需要使其高温粘性高,使熔融玻璃的温度为高于碱性玻璃的高温,因而这样的无碱玻璃愈发具有钼或者钼合金挥发的问题。因此对由钼或者钼合金构成的管进行过剩加热乃不利状况。因此,本发明的目的在于提供玻璃基板的制造方法,在该制造方法中,与以往相t匕,可在熔融玻璃的澄清中防止构成澄清槽的管的钼或者钼合金的挥发,同时可提高熔融玻璃的澄清效果。 解决课题的手段本发明的一个方式为玻璃基板的制造方法,其包括一边使熔融玻璃在由钼或钼合金构成的外周壁被加热的管中流动一边进行澄清的澄清工序。上述澄清工序包括脱泡工序,在该脱泡工序中,使上述熔融玻璃中的气泡自熔融玻璃的液面向着上述管内的气相放出。在上述脱泡工序中,通过对上述熔融玻璃进行搅拌,使上述熔融玻璃沿上述管径向的温度分布均匀化。发明的效果利用上述方式的玻璃基板的制造方法,可在熔融玻璃的澄清中防止钼或者钼合金的挥发,同时可提高熔融玻璃的澄清效果。[图1]本实施方式玻璃基板制造方法的流程图。[图2]进行图1所示熔解工序 切断工序的装置的示意图。[图3](a)为主要示出进行图1所示澄清工序的澄清槽的图,(b)为示出澄清槽外周壁温度的图。[图4](a) (C)对澄清槽中所用的板材进行说明的图。[图5]对现有澄清槽中的熔融玻璃流速与温度进行说明的图。[图6](a) (C)示出实施方式与图4(a) (C)所示板材不同的板材的实例的图。[图7]示出实施方式与由图4(a) (C)所示板材构成的搅拌机构不同的搅拌机构的实例的图。
(玻璃基板制造方法的整体概要)图1为本实施方式玻璃基板制造方法的流程图。玻璃板的制造方法主要具有熔解工序(STl)、澄清工序(ST2)、均质化工序(ST3)、供给工序(ST4)、成形工序(ST5)、缓慢冷却工序(ST6)以及切断工序(ST7)。此外还有磨削工序、研磨工序、清洗工序、检查工序、捆包工序等,在捆包工序中进行了堆叠的2个以上玻璃基板被运送至收货方的工作人员处。图2为进行熔解工序(STl) 切断工序(ST7)的装置的示意图。如图2所示,该装置主要具有熔解装置200、成形装置300、以及切断装置400。熔解装置200主要具有熔解槽201、澄清槽202、搅拌槽203以及玻璃供给管204,205,206。需要说明的是,用于将熔解槽201以后至成形装置300为止的各槽间连接的玻璃供给管204,205,206以及澄清槽202和搅拌槽203由金属管构成,金属管乃钼或者钼铑合金等钼合金制成。在熔解工序(STl)中,将添加有例如SnO2等澄清剂并被供给至熔解槽201内的玻璃原料利用未图示的火焰和电加热器进行加热熔解,从而得到熔融玻璃。具体地说,使用未图示的原料投入装置将玻璃原料M供给至熔融玻璃G的液面。玻璃原料通过利用火焰而变成高温的气相进行加热来缓慢熔解,溶于熔融玻璃MG中。熔融玻璃MG通过利用电加热器进行的通电加热来升温。澄清工序(ST2)至少在玻璃供给管204、澄清槽202和玻璃供给管205中进行。在澄清工序中,通过使澄清槽202内的熔融玻璃MG升温,熔融玻璃MG中所含有的包含02、C02或者SO2的气泡吸收例如由SnO2等澄清剂的还原反应所产生的O2而成长,并上浮到熔融玻璃MG的液面而被放出(脱泡工序)。另外,在澄清工序中,在脱泡后降低熔融玻璃MG的温度,从而使得例如由SnO2等澄清剂的还原反应而得到的SnO等澄清剂发生氧化反应,由此将残存于熔融玻璃MG的气泡中的O2等气体成分吸收到熔融玻璃MG中而使泡消失(吸收工序)。基于澄清剂的氧化反应和还原反应是通过控制熔融玻璃MG的温度来进行的。关于熔融玻璃MG的温度,通过在设于玻璃供给管204的未图示的加热电极与设于澄清槽202的后述加热电极202a (参照图3)之间流通电流、进一步在加热电极202a与相比于加热电极202a位于熔融玻璃MG下游侧且设 于澄清槽202的加热电极202b (参照图3 (a))之间流通电流,从而对澄清槽202进行加热、使熔融玻璃MG升温。进一步地,通过在加热电极202b与相比于加热电极202b位于熔融玻璃MG下游侧且设于澄清槽202的加热电极202c (参照图3)之间流通电流,可在对澄清槽202进行加热的同时使熔融玻璃MG降温。该通电加热并不限于利用3个区域的通电加热进行的温度控制,也可以进行I个或2个区域的通电加热来进行熔融玻璃MG的温度控制。关于澄清槽202中的澄清工序在下文详述。在均质化工序(ST3)中,使用搅拌器203a对通过玻璃供给管205进行供给的搅拌槽203内的熔融玻璃MG进行搅拌,由此来进行玻璃成分的均质化。搅拌槽203中,可使用I个搅拌器203a对熔融玻璃MG进行搅拌,也可以使用2个以上的搅拌器203a对熔融玻璃MG进行搅拌。供给工序(ST4)中,通过玻璃供给管206的熔融玻璃MG被供给至成形装置300。在成形装置300中进行成形工序(ST5)和缓慢冷却工序(ST6)。在成形工序(ST5)中,将熔融玻璃MG成形为片状玻璃G,制作片状玻璃G的连续体(流Λ)。在本实施方式中,采用的是使用后述成形体310的溢流下拉法。在缓慢冷却工序(ST6)中,成形且连续的片状玻璃G按照形成所期望的厚度、不产生内部变形的方式进行冷却。在切断工序(ST7)中,在切断装置400中将由成形装置300供给的片状玻璃G切断成规定长度,从而得到板状的玻璃基板。切断后的玻璃基板进一步被切断成规定的尺寸,制作目标尺寸的玻璃基板。之后进行玻璃基板端面的磨削、研磨和玻璃基板的清洗,进一步检查有无气泡或波筋等缺陷,之后将检查合格品的玻璃基板作为最终制品进行捆包。(澄清工序)如上所述,澄清工序(ST2)的脱泡工序和吸收工序至少在玻璃供给管204、澄清槽202和玻璃供给管205中进行。脱泡工序主要在供给管204和澄清槽202的前半部进行。另外,吸收工序主要在澄清槽202的后半部进行。此外,脱泡工序有时也在澄清槽202的后半部进行。这种情况下的吸收工序在澄清槽202的后半部或其以后的供给管205中进行。下面自脱泡工序起对澄清工序进行说明。对于由熔解槽201供给至玻璃供给管204的熔融玻璃MG,在玻璃供给管204和澄清槽202的前半部,其在供给至澄清槽202之前进行加热,以促进SnO2等澄清剂中氧的放出反应且使粘度达到在澄清槽202的前半部气泡容易上浮的粘度(优选为120 [poise (poise) ] ~ 400 [poise]: 1poise=0.1Pa.秒)。例如,在无碱玻璃或仅含有微量碱的微量含碱玻璃(高温粘性玻璃)(例如在为与102 5 [poise]的粘度相当的温度为1500°C以上的玻璃)的情况下,例如,以1580°C 1620°C、更优选以1,600°C 1620°C供给至玻璃供给管204,以使澄清槽202的入口处例如为1610°C 1650°C、更优选为1630°C 1650°C的方式进行加热。进一步地,在澄清槽202中,通过在后述的加热电极202a与加热电极202b之间流通电流,对澄清槽202进行加热,使熔融玻璃MG升温至例如1670°C 1710°C、优选至1690°C 1710°C。即,需要使澄清槽202的温度升高到构成澄清槽202的金属管的钼或者钼合金的耐热温度附近。即,在脱泡工序中,为了对熔融玻璃MG进行加热,需要有一定长度以上的管。并且,需要按照澄清槽202的内径大于玻璃供给管204的内径、在熔融玻璃MG的液面与管之间有气相空间的方式来构成。采用这样的构成,在玻璃供给管204中开始的脱泡可在澄清槽202中为气泡易于上浮的粘度时急剧地放出、可有效促进澄清效果。此处,澄清槽202的管由于如上所述内径较大,因而管径向的温度分布容易不均匀。需要说明的是,该问题在内径较小的玻璃供给管204中不易产生。接着对吸收工序进行说明。在吸收工序中,通过在加热电极202b与加热电极202c(参照图3)之间流通电流,来一边对澄清槽202进行加热一边使熔融玻璃MG降温,在使用SnO2作为澄清剂的情况下,通过使经SnO2的还原反应得到的SnO进行氧化反应,残存在熔融玻璃MG的气泡中的O2等气体成分被吸收到熔融玻璃MG中,气泡消失。(澄清槽)图3(a)为具体示出主要进行上述澄清工序的澄清槽202的构成的图。具体地说,澄清槽202具有加热电极202a,202b, 202c与金属管202d。金属管202d为钼或钼合金制造的管。熔融玻璃MG以金属管202d的管路为流路流经金属管202d的内部。加热电极202a, 202b, 202c使电流自金属管202d的外周壁面流至金属管202d,使用由金属管202d的电阻产生的焦耳热对金属管202d进行加热,将熔融玻璃MG的温度提高到特定温度,并使用熔融玻璃MG中的澄清剂进行熔融玻璃MG的脱泡。S卩,金属管202d包括钼或钼合金的外周壁,该外周壁被加热。加热电极202a,202b,202c自金属管202d长度方向——X方向的上游侧依序设有加热电极202a、加热电极202b、加热电极202c,加热电极202a和加热电极202c位于金属管202d的两端。加热电极202b位于加热电极202a与加热电极202c之间的大致中间的位置。S卩,加热电极202a与加热电极202b之间的区域为第I加热区域,加热电极202b与加热电极202c之间的区域为第2加热区域。本实施方式中设有3个加热电极202a 202c,但也可以设有2个加热电极。SP,对金属管202d进行加热的区域可以为I个。进一步地,在金属管202d的内部,熔融玻璃MG并未流经金属管202d的整个流路截面,而在上方设有气相空间。为了使熔融玻璃MG中应进行脱泡的气泡在熔融玻璃MG的液体表面破裂而使气泡中的气体成分放出到大气中,在金属管202d的上部设置未图示的气体排气孔,该气体排气孔用于将气体成分从金属管202d的气相中放出到大气中。金属管202d优选为圆筒状的形状。金属管202d的厚度例如优选为Imm 1.5mm。金属管202d的内径大于玻璃供给管204,205的内径,优选与玻璃供给管204,205内径相比大30%以上、更优选大40%以上。金属管202d的内径例如为300mm以上。通过使金属管202d的内径例如为300mm以上的内径,可降低在金属管202d内流动的熔融玻璃MG的流速、延长熔融玻璃MG在金属管202d中停留的时间,可效率良好地进行熔融玻璃MG的澄清。在澄清槽202中,通过在加热电极202a,202b, 202c中流通电流,使得熔融玻璃MG的温度成为图3(b)所示的沿着X方向的分布。由熔解槽201传送的熔融玻璃MG经玻璃供给管204加热而缓慢地升温,进而在加热电极202a与加热电极202b之间按照使熔融玻璃MG的温度为最大的方式对熔融玻璃MG进行加热,在加热电极202b与加热电极202c之间按照使熔融玻璃MG的温度缓慢降低的方式对熔融玻璃MG进行加热。即,在加热电极202a与加热电极202b之间的区域使熔融玻璃MG升温,以利用熔融玻璃MG所含有的澄清剂、例如SnO2(氧化锡)的还原作用而使例如SnO2放出氧。另一方面,在加热电极202b与加热电极202c之间的区域使熔融玻璃MG降温,以通过熔融玻璃MG所含有的澄清剂、例如SnO (SnO2还原而成的澄清剂)的氧化作用而使SnO吸收氧。进一步地,熔融玻璃MG在玻璃供给管205被缓慢降温。图4(a)为在X方向切断澄清槽202的金属管202d而得到的截面图。金属管202d在作为熔融玻璃MG的流路的金属管202d的内壁面交替设有多个板材202e,202f,该板材202e,202f成为与X方向正交的壁。板材202e,202f为静态搅拌机构,该静态搅拌机构在金属管202d内固定于金属管202d,由以钼或钼合金等材质形成的部件构成。S卩,板材202e, 202f通过对流经金属管202d内的熔融玻璃MG进行搅拌,使得熔融玻璃MG沿管径向的温度分布均匀化。此处,所谓熔融玻璃MG沿径向的温度的均匀化指的是,在温度分布中,温度差为20°C以内、更优选为10°C以内,更优选指的是5°C以内。
板材202e, 202f按照其垂直于金属管202d的X方向的截面积为金属管202d垂直于X方向的截面积的1/3 2/3来进行设置,即优选按照对熔融玻璃MG的流动进行限制的方式来进行设置。对熔融玻璃MG的流动进行限制的板材202e,202f的截面积(遮断面积)若过小,则搅拌效果小;遮断面积若过大,则阻碍熔融玻璃MG流动的要素变得过大。优选上述遮断面积为金属管202d垂直于X方向的截面积的二分之一左右。如图4(b)所示,板材202e按照通过金属管202d的包括流路截面中心的中央区域、在水平方向(图4(b)的左右方向)横切金属管202d的方式进行设置,对于流路截面中的处于上述中央区域的熔融玻璃MG的流动进行限制,并且可使熔融玻璃MG通过流路上部与下部。另一方面,如图4(c)所示,与板材202e的配置不同,板材202f按照夹着金属管202d包括流路截面中心的中央区域、在水平方向(图4(c)的左右方向)分别横切流路截面的上部与下部的方式进行设置,对于流路截面中的处于上部与下部的熔融玻璃MG的流动进行限制,并且可使熔融玻璃MG通过金属管202d的包括流路截面中心的中央区域。即,按照对金属管202d管路中的熔融玻璃MG的流路截面进行限制的方式,利用设置在管路流路方向的不同位置的2种以上的板材202e,202f来进行构成。在相邻的板材202e,202f组中,流路截面的限制部分彼此不同。另外,板材202f可按照夹着中央区域、在水平方向(图4(c)的左右方向)分别横切流路截面的上部与下部的方式进行设置,也可按照将板材202f在流路截面的面内旋转90度而成的形状进行设置,即按照夹着管路的包括流路截面中心的中央区域、在垂直方向(图4(c)的上下方向)分别横切流路截面左右两侧的部分的方式进行设置。这种情况下,作为板材202e优选使用图4 (b)所示的形状。并且作为板材202f也可使用图4 (c)所示的形状,另外可设置将图4(b)所示的板材202e在流路截面的面内旋转90度而成的形状。本实施方式中,对板材202e,202f的流路截面进行限制的部分彼此不同,但对流路截面进行限制的部分也可以相同。但是,从防止熔融玻璃MG自上游侧至下游侧直线流动并且在对熔融玻璃MG进行上下方向的搅拌的同时其还流动的方面考虑,优选板材202e, 202f中对流路截面进行限制的部分彼此不同。此外,在本实施方式中,设置了 2种板材202e,202f,但也可以仅设置I种板材来对熔融玻璃MG的流路截面进行限制。
`
在澄清槽202中,一边使由玻璃供给管204供给的熔融玻璃MG在金属管202中流动一边进行脱泡,该金属管202的由钼或钼合金形成的外周壁被通电加热。这种情况下,在被加热的金属管202d的壁附近流动的熔融玻璃MG容易随着金属管202d的通电加热而升温,但熔融玻璃MG中的流路截面中心的部分由于远离被加热的金属壁202d而难以升温。即,熔融玻璃MG容易沿着金属管202d的径向产生温度分布。因此,在未设有板材202e,202f的现有澄清槽中,流动的熔融玻璃沿着管径向的温度分布不均匀,并且远离金属管壁的流路截面中心部分的熔融玻璃的流速比在金属管壁附近流动的熔融玻璃的流速快。因而,在流路截面中心流动的熔融玻璃MG容易在未加热的状态下穿过澄清槽。在由于上述理由使得熔融玻璃MG沿着金属管202d的径向产生温度分布时,需要将金属管202的加热温度设定得较高,以使得在温度分布中温度最低的部分的温度适合于澄清剂发挥出还原作用而放出氧的脱泡,并且使熔融玻璃MG呈现出具有使气泡易于上浮的粘度的温度。但是,若设定这样的加热温度,则构成金属管202d的钼或钼合金等金属成分的挥发剧烈,金属管202d的消耗剧烈。因此,在本实施方式中,为了使熔融玻璃MG在金属管202d径向的温度分布接近于均匀(为使其均匀化),在金属管202d的流路上设置板材202e,202f,该板材202e,202f为对熔融玻璃MG进行搅拌的机构。由此,与现有技术相比,可防止构成金属管202d的钼或钼合金的挥发,同时可提高熔融玻璃MG的澄清效果。
本实施方式的使用板材202e,202f进行的熔融玻璃MG的搅拌在自澄清槽202金属管202d内熔融玻璃MG的入口起至通过对熔融玻璃MG进行加热而形成的最高温度(参照图3(b))附近为止的区间中的至少一部分进行。由于在上述区间中进行熔融玻璃MG的脱泡工序,因而在该脱泡工序中,通过使熔融玻璃MG沿着金属管202d径向的温度分布均匀化,可抑制金属管202d的多余加热,可防止构成金属管202d的钼或者钼合金的挥发、同时可提高熔融玻璃MG的澄清效果。此处的“最高温度附近”的“附近”指的是相对于最高温度为例如10°C以内的范围,优选为5°C以内的范围。因而,上述区间指的是自金属管202d内熔融玻璃MG的入口处起到上述“附近”边缘为止的区间,该“附近”为超过对熔融玻璃MG进行加热而形成的最高温度的位置而温度降低了 10°C的位置。在澄清槽202中,在使熔融玻璃MG升温进行脱泡之后,通过对加热电极202b,202c之间的金属管202d进行通电加热,使熔融玻璃MG的温度降低至低于澄清槽202前半部的熔融玻璃MG的温度的、适于吸收工序的温度。此处,所谓澄清槽202的前半部的熔融玻璃MG的温度指的是可促进澄清剂中氧的放出反应、且呈现出使熔融玻璃MG中的气泡易于上浮的粘度(优选为120[poiSe] 400[poise])的温度,例如在无碱玻璃仅含有微量碱的微量含碱玻璃(高温粘性玻璃)、例如与102 5[poise]相当的温度为1500°C以上的玻璃中使用SnO2作为澄清剂的情况下,所谓澄清槽202的前半部的熔融玻璃MG的温度处于例如1610°C 1710°C的范围内。对于适于吸收工序的温度,在上述碱性玻璃或微量含碱玻璃中使用SnO2作为澄清剂的情况下,其处于1200°C 1650°C的范围内。由此,澄清槽202内熔融玻璃MG所生成的最高温度处于1670°C 1710°C、或处于1690°C 1710°C。并且,在该情况下,图3(b)所示最高温度的上限例如为1700度 1710度。如此,使熔融玻璃MG所含有的澄清剂发挥出氧化作用,使澄清剂吸收残留在熔融玻璃MG中的气泡所含有的氧,来进行澄清。此时,由于熔融玻璃MG的温度高于管壁面的温度,因而在澄清槽202中不进行搅拌的情况下,在管路中心附近流动的熔融玻璃MG的温度高于在管壁面附近流动的熔融玻璃的温度。即,具有无法降低至适于吸收工序的温度、澄清不充分的问题。此时,澄清槽202可使用板材202e,202f作为熔融玻璃MG的搅拌机构对熔融玻璃MG进行搅拌。在气泡吸收时,若在熔融玻璃MG中存在上述温度分布,则由于上述理由,难以效率良好地对残存在熔融玻璃MG中的气泡进行吸收。因此,在本实施方式中,如图4(a)所示,不仅是在熔融玻璃MG脱泡时、而且在泡的吸收时,也使用板材202e,202f作为熔融玻璃MG的搅拌机构。通过在熔融玻璃MG脱泡时对熔融玻璃进行搅拌、或者除了在熔融玻璃MG脱泡时以外还在泡的吸收时对熔融玻璃进行搅拌,与不对熔融玻璃进行搅拌的情况相比,可使管壁面的温度降低例如几。C 十几。C。即,即使将管壁面的温度降低例如几°C 十几。C,也可为与未搅拌熔融玻璃的情况下的熔融玻璃温度相同的温度。本实施方式的澄清工序中,不仅在熔融玻璃MG进行脱泡时、而且在进行泡的吸收时均使用了板材202e,202f作为熔融玻璃MG的搅拌机构,但只要至少在使熔融玻璃MG升温进行脱泡的部分对熔融玻璃MG进行搅拌以使上述温度分布均匀化即可。
本实施方式中进行脱泡的金属管202d为相对于玻璃供给管204阶梯性扩大的扩径管,但其也可为连续扩径的扩径管。由于至少金属管202d为相对于玻璃供给管204扩大的管,因而在金属管202d内在熔融玻璃MG的上方存在气相空间,可使熔融玻璃MG具有液面,并且由于流路扩大,因而熔融玻璃MG的流速降低、在金属管202d内的停留时间延长;此外由于熔融玻璃MG的液面面积扩大,因而可效率良好地进行脱泡。(玻璃组成)通过本实施方式玻璃基板的制造方法制造出的玻璃基板适用于平板显示用玻璃基板。从可效率良好地发挥出本实施方式效果的方面考虑,例如优选具有不含有L1、Na以及K中的任意一种成分的玻璃组成,或者具有下述玻璃组成:该组成中,即使含有L1、Na以及K中至少任意I种成分,内部含有L1、Na以及K成分的总量也为0.5质量%以下。玻璃组成可优选示例出下述组成。玻璃基板的玻璃组成可以举出例如下述组成。以下所示组成的含量表示为质量%。优选为含有下述成分的无碱玻璃:SiO2:50 70%、B2O3:5 18%、Al2O3:0 25%、MgO:0 10%、CaO:0 20%、
SrO:0 20%、BaO:0 10%、R0:5 20%(其中,R选自Mg、Ca、Sr和Ba中的至少一种,为玻璃板所含有的成分)。另外,玻璃基板的玻璃可举出下述玻璃组成:SiO2:50 70%、B2O3:1 10%、Al2O3:0 25%、MgO:0 10%、CaO:0 20%、SrO:0 20%、BaO:0 10%、RO:5 30%(其中,R 为 Mg、Ca、Sr 和 Ba 的合计量),含有上述组成的无碱玻璃亦同样优选。此外,玻璃基板的玻璃可举出下述玻璃组成:SiO2:50 70%、B2O3:3 15%、Al2O3:8 25%、MgO:0 10%、CaO:0 20%、SrO:0 20%、BaO:0 10%、RO:5 30%(其中,R 为 Mg、Ca、Sr 和 Ba 的合计量),含有上述成分的无碱玻璃亦同样优选。
需要说明的是,本实施方式中为无碱玻璃,但玻璃基板也可以使含有微量碱金属(碱金属的合计含量大于O质量%)的微量含碱玻璃。在含有碱金属的情况下,优选含有合计为0.10质量%以上0.5质量%以下的R’ 20(其中,R’为选自L1、Na和K中的至少一种,为玻璃基板G所含有的物质)。并且,为使玻璃容易熔解,从降低比电阻的方面考虑,玻璃中氧化铁的含量换算成Fe2O3优选为0.01质量% 0.2质量%、更优选为0.01质量% 0.15质量%、进一步优选为0.01质量% 0.10质量%。并且,添加SnO2作为澄清剂的情况下,更优选SnO2的含量为0.01质量% 0.5质量%。另外,在本实施方式中,由于SnO2为容易使玻璃失透的成分,因此,为了在提高澄清性的同时不引起失透,其含量优选为0.01质量%
0.5质量%、更优选为0.05质量% 0.4质量%、进一步优选为0.1质量% 0.3质量%。并且优选实质上不含有As203、Sb2O3> PbO0除上述成分外,在本实施方式的玻璃基板中,为了对玻璃进行各种物理、熔融、澄清、以及成形特性的调节,也可以含有其它各种氧化物。作为这样的其它氧化物的示例,可以举出 TiO2、MnO、ZnO、Nb2O5、MoO3、Ta2O5、TO3、Y2O3 以及 La2O3,并不限于上述物质。在本实施方式的制造方法中,通过对熔融玻璃MG进行搅拌,使熔融玻璃MG沿着金属管202d径向的温度分布均匀化。因此,即使在由于玻璃组成的不同而使用熔解性低、熔融玻璃的粘性高的熔融玻璃的情况下,只要将熔融玻璃加热到使熔融玻璃的粘度适于脱泡的程度即可,无需如现有技术那样为了提高在金属管中心附近流动的熔融玻璃的温度而对熔融玻璃进一步加热。因而,可抑制由钼或钼合金构成的金属管202d的挥发、同时可有效进行澄清工序。即,即使与102.5 [poise]对应的温度为1500。。以上(例如1500。。以上1650。。以下)的高粘性玻璃,在本实施方式的制造方法中也可适当地作为构成玻璃基板的玻璃进行使用,可抑制由钼或钼合金构成的金属管202d的挥发、同时可有效进行澄清工序。另外,即使并非为粘性高的玻璃,在近年来从环境负荷的方面出发不使用As2O3而使用SnO2作为澄清剂的情况下,与使用As2O3作为澄清剂的情况相比,熔融玻璃为高温,因此愈发有钼或者钼合金挥发的问题。但是,在本实施方式的制造方法中,无需如现有技术那样为了提高在金属管的中心附近流动的熔融玻璃的温度而更进一步对熔融玻璃进行加热。因而,可抑制由钼或者钼合金构成的金属管202d的挥发,同时可有效进行澄清工序。(变形例)在本实施方式中,如图4(a)所不交替配置有多个设于金属管202d内的板材202e, 202f,但也可配置I组板材202e,202f。另外,如图6(a)所示,也可在金属管202d中交替设有下述板材202e,202f,该板材202e,202f自金属管202d的管壁朝向管路内侧延伸,但延伸高度不同。即,由于相邻的板材202e,202f的高度不同,因而板材202e,202f组中,对流路截面进行限制的部分彼此不同。这种情况下,通过利用板材202e,202f进行搅拌,熔融玻璃MG如图中所示虚线那样起伏流动。即,图6 (a)所示的板材202e,202f作为对熔融玻璃MG进行搅拌的搅拌机构来使用。
进一步地,也可不使用本实施方式图4(a)、图4(b)所示的板材202e,202f而如图6(b)所示在金属管202d中交替设置板材202e以及板材202f,所述板材202e开有2个以上圆形或半圆形的孔,所述板材202f设有与该孔配置不同的孔。
此外,也可不使用本实施方式图4(a)、图4(b)所示的板材202e,202f而如图6 (C)所不在金属管202d中交替设置板材202e以及板材202f,所述板材202e在一个方向上开有2个以上的狭缝孔,所述板材202f设有与该狭缝孔的方向不同的狭缝孔。在图6(b)、图6(c)的情况下,板材202e,202f组中对流路截面进行限制的部分均彼此不同。因此,熔融玻璃MG可通过板材202e,202f进行有效搅拌。进一步地,也可不像本实施方式那样使用板材202e,202f作为用于对熔融玻璃MG进行搅拌的单元(静态搅拌机构),而如图7所示在金属管202d中设置搅拌机202i作为动态搅拌机构来对熔融玻璃MG进行搅拌,该搅拌机202i在旋转轴202g上设有桨叶202h并使旋转轴202g旋转。上面对本发明玻璃基板的制造方法进行了详细说明,但本发明并不限于上述实施方式,当然可以在不脱离本发明宗旨的范围内进行各种改良及变形。符号的说明200熔解装置201熔解槽202澄清槽202a, 202b, 202c 加热电极202d 金属管202e,202f 板材202g 旋转 轴202h 桨叶202i 搅拌机203搅拌槽203a 搅拌器 204, 205, 206 玻璃供给管300成形装置310成形体400切断装置
本发明涉及玻璃基板的制造方法,该制造方法包括一边使熔融玻璃在下述管中流动一边进行澄清的澄清工序,所述管包含铂或铂合金的外周壁被加热。上述澄清工序包括脱泡工序,在该脱泡工序中,使上述熔融玻璃中的气泡自熔融玻璃的液面向着上述管内的气相放出。在上述脱泡工序中,通过对上述熔融玻璃进行搅拌,使上述熔融玻璃沿上述管径向的温度分布均匀化。
玻璃板的制造方法
- 专利详情
- 全文pdf
- 权力要求
- 说明书
- 法律状态
查看更多专利详情
下载专利文献
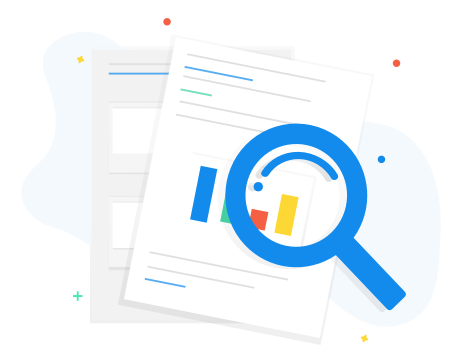
下载专利
同类推荐
-
苅谷浩幸, 前田伸广苅谷浩幸, 前田伸广苅谷浩幸, 前田伸广苅谷浩幸, 前田伸广村上次伸, 日冲宣之村上次伸, 日冲宣之村上次伸, 日冲宣之
您可能感兴趣的专利
-
藤本慎吾, 村上次伸藤本慎吾, 村上次伸藤本慎吾, 村上次伸藤本慎吾, 村上次伸藤本慎吾, 村上次伸藤本慎吾, 村上次伸王新, 王桂英
专利相关信息
-
堀顺士J·H·阿伦斯J·H·阿伦斯J·H·阿伦斯蒂莫·皮沃斯基, 贝恩德·威尔维斯蒂莫·皮沃斯基, 贝恩德·威尔维斯