专利名称:玻璃板的制造方法目前,作为液晶显示装置或等离子显示装置等平板显示器的显示部的零件,使用平面玻璃板。在液晶显示装置,玻璃板例如用作构成薄膜电晶体驱动液晶显示装置(TFT-LCD)的玻璃基板,除此以外亦用作覆盖显示部的覆盖玻璃。 制造过程中在玻璃中所形成的气泡令玻璃制造业者烦恼。尤其是液晶显示装置的玻璃基板用或覆盖玻璃用的玻璃板要求极少的气泡含量。因此,于玻璃的制造过程中,为了去除气泡曾在玻璃原料中添加氧化砷或氧化锑作为澄清剂。但是由于这些澄清剂对环境的影响令人担忧,故作为不使用这些澄清剂的气泡的去除方法,例如提出有如专利文献I (日本专利特表2001-503008号公报)中所揭示的藉由控制环境中的氢分压而抑制形成气泡的技术。
发明所要解决的问题但是,玻璃中所形成的气泡有多种多样,有即便使用如上所述的先前的方法亦无法将气泡充分去除的气泡。因此,依然要求寻找有效抑制玻璃中所形成的气泡的方法。本发明是鉴于上述课题而成,提供一种能够有效抑制玻璃中的气泡的玻璃板的制造方法。解决问题的手段本发明的发明者针对抑制玻璃中的气泡的形成的方法,进行努力研究,结果发现(i)尺寸为300 μ m以下的气泡较多是在将新的未使用的钼或钼合金制的搅拌翼(亦称为搅拌器)导入制造线中时形成,认为气泡是于澄清步骤之后所产生;(ii)在玻璃中所形成的气泡中有以02、N2、S02、C02为成分,尺寸为300μπι以下的气泡主要是以C02为成分;(iii)认为以C02为成分的气泡是源自有机物,且认为该有机物为油、树脂或灰尘等搅拌翼的制造过程中所使用的残留物,或者源自外部的飞来物附着于搅拌翼的表面而成。因此,本发明的发明者认为只要去除钼或钼合金制的搅拌翼的与熔融玻璃接触的表面的附着物,则能够有效抑制气泡的形成。本发明是根据上述观点而成,本发明的玻璃板的制造方法的特征在于包括如下准备步骤于使玻璃生产线正式运转之前,对钼或钼合金制的搅拌翼进行热处理,藉此去除搅拌翼的与熔融玻璃接触的表面的附着物。藉此,能够有效抑制因该附着物而在玻璃中形成气泡。本发明的玻璃板的制造方法较佳为,准备步骤包括将搅拌翼浸于比正式运转时高出30°C以上的温度的熔融玻璃中。本发明的玻璃板的制造方法较佳为,准备步骤包括将搅拌翼浸于黏度为120Pa · s以下的熔融玻璃中。本发明的玻璃板的制造方法较佳为,准备步骤包括将搅拌翼于偏离玻璃生产线的生产线外的状态下,浸于加热为比正式运转时与搅拌翼的表面所接触的熔融玻璃的温度高出50°C以上的环境中。发明效果依据本发明的玻璃板的制造方法,能够有效抑制在玻璃中形成气泡。 图I为本发明的实施例的玻璃板的制造方法的流程图;图2为本发明的实施例的玻璃板生产线的概略图;图3为本发明的实施例的搅拌槽的图。
质量%。再者,上述的液晶基板用玻璃较佳为实质上不含砷及锑。即,即便含有这些物质,这些亦作为杂质,具体而言,这些物质亦包括As2O3、及Sb2O3等氧化物在内较佳为O. I质量%以下。
除上述成分以外,为了调节玻璃的各种物理性、熔融、澄清、及成形的特性,本发明的玻璃可含有各种其他氧化物。作为如上所述的其他氧化物的例,可列举如下但不限定于这些SnO2 > Ti02、MnO> ZnO> Nb2O5、MoO3、Ta2O5、WO3、Y2O3、及 La2O3。上述(a) (r)中的(p)的RO的供给源可使用硝酸盐或碳酸盐。再者,为了提高熔融玻璃的氧化性,更理想为以适合于步骤的比例使用硝酸盐作为RO的供给源。与将一定量的玻璃原料供给至熔解用的炉中而进行批次处理的方式不同,本实施例中所制造的玻璃板是连续地进行制造。本发明的制造方法中所应用的玻璃板亦可为具有任意厚度及宽度的玻璃板。(1-2)玻璃制造步骤的概要本发明的一实施例的玻璃板的制造方法包括图I的流程图所示的一系列步骤,且使用图2所示的玻璃板生产线100。
以成为上述组成的方式所调配的玻璃的原料是首先于熔解步骤(步骤S101)中熔解。原料是投入熔解槽101中,并加热直至特定的温度。在制造例如具有上述组成的平板显示器用的玻璃基板时,特定的温度较佳为1550°C以上。经加热的原料熔解而形成熔融玻璃。熔融玻璃是通过第I输送管(transfertube) 105a而运送至进行后续的澄清步骤(步骤S102)的澄清槽102中。于后续的澄清步骤(步骤S102)中,澄清熔融玻璃。具体而言,若于澄清槽102中加热熔融玻璃直至特定的温度,则熔融玻璃中所含的气体成分形成气泡,或者汽化而排出于熔融玻璃的外部。在制造例如具有上述组成的平板显示器用的玻璃基板时,特定的温度较佳为1610°C以上。经澄清的熔融玻璃是通过第2输送管105b,而运送至进行作为后续的步骤的均质化步骤(步骤S103)的搅拌槽103中。于后续的均质化步骤(步骤S103)中,熔融玻璃均质化。图3表示搅拌槽103。具体而言,熔融玻璃是藉由于搅拌槽103中,利用搅拌槽103所具备的下述搅拌翼103a进行搅拌而均质化。运送至搅拌槽103中的熔融玻璃加热至特定的温度范围。在制造例如具有上述组成的平板显示器用的玻璃基板时,特定的温度范围较佳为1440°C (黏度约为121Pa*s) 1500°C (黏度约为60Pa *s)。经均质化的熔融玻璃是自搅拌槽103运送至第3输送管105c中ο于后续的供给步骤(步骤S104)中,熔融玻璃是于第3输送管105c中加热至适合于成形的温度,并运送至进行后续的成形步骤(步骤S105)的成形装置104中。在制造例如具有上述组成的平板显示器用的玻璃基板时,适合于成形的温度较佳为约1200°C。于后续的成形步骤(步骤S105)中,熔融玻璃成形为板状的玻璃。于本实施例中,熔融玻璃是利用溢流下拉法连续地成形为带状。所成形的带状的玻璃经切割而成为玻璃板。溢流下拉法其本身为公知的方法,例如为如美国专利第3,338,696号说明书中所记载的方法流入成形体中而溢出的熔融玻璃沿着该成形体的各外表面溢流,并于在该成形体的底面合流的处向下方延伸而成形为带状的玻璃。(1-3)搅拌槽及搅拌翼图3表示搅拌槽103。搅拌槽103是收容钼或钼合金制的熔融玻璃的容器,具备钼或钼合金制的搅拌翼103a。采用钼合金时,较佳为使用例如具有钼90质量%、铑10质量%的成分的钼-铑合金。又,亦可使用将氧化锆等金属氧化物分散于钼中而得的作为强化钼的钼-铑-锆合金。搅拌翼103a具有旋转轴、及安装于该旋转轴上的多个翼。旋转轴是自容器的顶部垂直插入容器内。多个翼是以旋转轴为中心成放射状安装于旋转轴上。旋转轴是藉由马达等驱动部而旋转。若旋转轴旋转,则安装于旋转轴上的多个翼搅拌熔融玻璃。(2)准备步骤详细情况未使用的新装置有可能于与熔融玻璃接触的表面上附有附着物。认为附着物有于搅拌翼103a的制造过程或完成时附着于其表面的灰尘或树脂、油等有机物等各种,由于这些附着物通常对于玻璃成分成为杂质,故藉由清洗而极力将其去除。但是,本发明的发明者在调查玻璃中形成极微细的气泡的原因的过程中,发现于以目视观察为平滑的搅拌翼103a的表面存在非常微细的研磨痕或凹凸,于该研磨痕或凹凸中残留有无法由通常的清洗而完全去除的附着物。尤其是,于附着物的中有机物很有可能成 为玻璃中的气泡形成的原因。即,认为有机物中所含的碳与氧结合而生成二氧化碳气体,且该气体被封闭在玻璃中而形成气泡。因此,于将搅拌翼103a等新的未使用的装置投入玻璃板生产线100中时,较佳为于进行去除这些附着物的准备步骤之后,使玻璃板生产线100正式运转。准备步骤是如以下所说明,对搅拌翼103a的与熔融玻璃接触的表面进行热处理,去除该表面的附着物。具体而言,较佳为进行后续的生产线外热处理或生产线上热处理中的任一者。亦可进行这两种热处理。(2-1)生产线上热处理生产线上热处理是于将搅拌翼103a设置于玻璃板生产线100中的状态下(生产线上),对搅拌翼103a进行热处理。具体而言,较佳为使比正式运转时温度更高的熔融玻璃流入搅拌槽103中并使搅拌翼103a旋转,藉此使搅拌翼103a的与熔融玻璃接触的表面浸于该熔融玻璃中。熔融玻璃是藉由使玻璃板生产线100上的上述各装置运转而生成。SP,以与正式运转时相同的方式依据图I所示的上述玻璃板的制造步骤,使玻璃的原料于熔解槽101中熔解而生成熔融玻璃,进而使该熔融玻璃依序流入第I输送管105a、澄清槽102、第2输送管105b以及搅拌槽103中。然而,如上所述与搅拌翼103a所接触的熔融玻璃的温度以高于正式运转时为佳。较佳为熔融玻璃的温度比正式运转时与搅拌翼103a所接触的温度高出30°C左右以上。例如,若将正式运转时与搅拌翼103a所接触的熔融玻璃的温度设为约1440°C,则较佳为比该温度高出30°C以上,S卩,较佳为使1470°C以上的熔融玻璃流入搅拌槽103中。但是,若熔融玻璃的温度过高,则有时缩短搅拌槽103及位于其下游的玻璃板生产线100上的其他装置的寿命,故而较佳为与搅拌翼103a所接触的熔融玻璃的温度并未比正式运转时的温度高出100°C以上。熔融玻璃的黏度以低于正式运转时为佳,较佳为120Pa *s以下。熔融玻璃是随着温度变高而黏度变低。藉由使搅拌翼103a的表面浸于黏度较低即流动的熔融玻璃中,可使残留于其表面的附着物浸于高温下,藉由对其表面擦涂熔融玻璃,亦可更确实地冲洗进入细小凹处的附着物,故而较佳。但是,若熔融玻璃的黏度过低,则对搅拌翼103a的表面的摩擦力过小,无法获得擦落附着物的效果。熔融玻璃的黏度较佳为50Pa · s以上。(2-2)生产线外热处理生产线外热处理是于搅拌翼103a偏离玻璃板生产线100的状态(生产线外)下,对搅拌翼103a进行热处理。具体而言,较佳为将搅拌翼103a放入生产线外状态的钼或钼合金等耐火金属制的炉中,并对该炉内的环境加热,使搅拌翼103a的与熔融玻璃接触的表面浸于高温的环境中。炉内的环境的加热较佳为藉由利用气体燃烧器而对环境进行加热。进而,较佳为藉由利用电源设备使该炉通电而进行加热。环境的温度较佳为比正式运转时与搅拌翼103a所接触的熔融玻璃的温度高出50°C以上的温度。例如,若正式运转时与搅拌翼103a所接触的熔融玻璃的温度为1445°C,则较佳为较其高出50°C以上的温度(例如,1500°C )。较佳为使搅拌翼103a的与熔融玻璃接触的表面浸于该高温的环境下至少24小时。再者,作为生产线外热处理,对于上述搅拌翼103a的利用高温的环境的热处理并非必需于生产线外的炉中进行,亦可在设置于玻璃板生产线100上的状态的搅拌槽103中进行。(3)实施例 (3-1)生产线上热处理的实施例利用未使用且新品的搅拌翼103a,依据图I的流程图所示的上述一系列玻璃板制造步骤,使图2所示的上述玻璃板生产线100运转而制造玻璃板。再者,玻璃原料是以所制造的玻璃板的组成成为如下所示的方式进行调配Si02 :60. 9质量%、B2O3 :11.6质量%、Al2O3 16. 9 质量 %、MgO 1. 7 质量 %、CaO 5. I 质量 %、SrO 2. 6 质量 %、BaO 0. 7 质量 %、K2O O. 25质量%、Fe2O3 0. 15质量%、SnO2 0. 13质量%。与搅拌翼103a所接触的熔融玻璃的温度与玻璃板生产线100的正式运转时相同约为1445°C (黏度约为113Pa *s)。测量所制造的玻璃板中的气泡的数量,首先确认尺寸为300 μ m以下的气泡的数量于Ikg的玻璃中约为O. 24个。又,分析尺寸为300 μ m以下的气泡的成分,确认成分主要为C02。然后,使与搅拌翼103a所接触的熔融玻璃的温度较玻璃板生产线100的正式运转时的约1445°C高出30°C以上,约为1484°C (黏度约为71Pa *s)。在持续该状态3天之后,制造玻璃板,若测量所制造的玻璃板中所含的气泡的数量,则尺寸为300 μ m以下的气泡的数量于Ikg的玻璃中约为O. 16个。(3-2)比较例利用未使用且新品的搅拌翼103a,依据图I的流程图所示的上述一系列玻璃板制造步骤,使图2所示的上述玻璃板生产线100运转而制造玻璃板。再者,玻璃原料是以所制造的玻璃板的组成成为如下所示的方式进行调配Si02 :60. 9质量%、B2O3 :11.6质量%、Al2O3 16. 9 质量 %、MgO 1. 7 质量 %、CaO 5. I 质量 %、SrO 2. 6 质量 %、BaO 0. 7 质量 %、K2O O. 25质量%、Fe2O3 0. 15质量%、SnO2 0. 13质量%。与搅拌翼103a所接触的熔融玻璃的温度与玻璃板生产线100的正式运转时相同约为1445°C (黏度约为113Pa · s)。若测量第I天所制造的玻璃板中的气泡的数量,则尺寸为300 μ m以下的气泡的数量于Ikg的玻璃中约为O. 24个。进而,使玻璃板的制造持续20天,若测量第21天所制造的玻璃板中的气泡的数量,则尺寸为300 μ m以下的气泡的数量于Ikg的玻璃中约为O. 35个。再者,分析尺寸为300 μ m以下的气泡的成分,结果成分主要为C02。根据上述(3-1)及(3-2)的例可知,若使与搅拌翼103a所接触的熔融玻璃的温度高于玻璃板生产线100的正式运转时的温度,又,黏度低于正式运转时,则有所制造的玻璃板中所含的300 μ m以下的气泡的数量减少的倾向。
(3-3)生产线外热处理的实施例使搅拌翼103a偏离制造玻璃板的玻璃板生产线100,上述玻璃板包含超过作为制品的容许范围的数量的尺寸为300 μ m以下的气泡,并对该搅拌翼103a进行上述的生产线外热处理。具体而言,将搅拌翼103a放入生产线外的钼合金制的炉中,利用电源设备使炉通电,并且利用氧燃烧器对炉内的环境进行加热。于炉内的环境的温度约为1500°C的状态下,将搅拌翼103a放入炉内24小时。其后,再次将搅拌翼103a投入玻璃板生产线100中,使用与上述先前例相同的原料及玻璃板生产线100,并利用相同的方法连续制造玻璃板。流入玻璃板生产线100中的熔融玻璃的温度及黏度与正式运转时相同。即,与搅拌翼103a所接触的熔融玻璃与正式运转时相同,温度约为1445°C,黏度约为113Pa · S。若测量所制造的玻璃板所含有的气泡的数量,则Ikg的玻璃中的尺寸为300 μ m以下的气泡的个数于Ikg的玻璃中约为O. 12个。根据上述(3-2)及(3-3)的例可知,若使搅拌翼103a的与熔融玻璃接触的表面在较玻璃板生产线100的正式运转时与该表面所接触的熔融玻璃高出50度以上的温度的环境下,浸至少24小时,其后制造玻璃板,则可减少玻璃板中所含的300 μ m以下的气泡的数 量。(4)特征(4-1)本发明的玻璃板的制造方法的特征在于包括如下准备步骤于使玻璃板生产线100正式运转之前,对钼或钼合金制的搅拌翼103a进行热处理,藉此去除搅拌翼103a的与熔融玻璃接触的表面的附着物。于本发明的上述(3-1)及(3-3)的实施例中,于对钼或钼合金制的搅拌翼103a的与熔融玻璃接触的表面进行热处理之后,制造玻璃板,藉此能够有效抑制玻璃中所形成的气泡。(4-2)本发明的玻璃板的制造方法较佳为,准备步骤包括使搅拌翼103a浸于比正式运转时高出30°C左右以上的温度的熔融玻璃中。于本发明的上述(3-1)的实施例中,于将钼或钼合金制的搅拌翼103a的与熔融玻璃接触的表面浸于较在玻璃板生产线100的正式运转时与该表面所接触的熔融玻璃的温度1445°C高出30°C以上的1484°c的熔融玻璃中,其后制造玻璃板,藉此,能够有效抑制在玻璃中形成气泡。(4-3)本发明的玻璃板的制造方法较佳为,准备步骤包括使搅拌翼103a浸于黏度为120Pa · s以下的熔融玻璃中。于本发明的上述(3-1)的实施例中,于使钼或钼合金制的搅拌翼103a的与熔融玻璃接触的表面浸于黏度约为71Pa *s的熔融玻璃中之后,制造玻璃板,藉此能够有效抑制在玻璃中形成气泡。(4-4)本发明的玻璃板的制造方法较佳为,准备步骤包括使搅拌翼103a于偏离玻璃板生产线100的生产线外的状态下,浸于加热为比正式运转时与搅拌翼103a的表面所接触的熔融玻璃的温度高出50°C以上的环境下。于本发明的上述(3-3)的实施例中,于使钼或钼合金制的搅拌翼103a的与熔融玻璃接触的表面浸于较在玻璃板生产线100的正式运转时与该表面所接触的熔融玻璃的温度1445°C高出50°C以上的1500°c的环境,其后制造玻璃,藉此能够有效抑制在玻璃中形成气泡。(5)变形例(5-1)变形例 A上述实施例调配更适用于制造平板显示器用的玻璃基板的原料,并使用本发明的玻璃板制造方法来制造玻璃板。但是,于其他实施例中,亦可将本发明的玻璃板制造方法用于例如制造覆盖玻璃用的玻璃板中。于该情形时,较佳为以具有以Na20、K20或者Li2O为代表的碱金属氧化物的浓度的合计大于2. O质量%的组成的方式,调配玻璃原料。
于制造具有如上所述的组成的玻璃板时,于玻璃板生产线100正式运转时,与搅拌翼103a的表面所接触熔融玻璃的温度较佳为约1350°C (黏度约为74Pa · s)。因此,为了有效抑制气泡的形成,较佳为于将搅拌翼103a的表面浸于比该温度高出30°C以上的温度(例如,1380°C或其以上)的熔融玻璃的上述生产线上热处理,或于将搅拌翼103a的表面浸于比该温度高出50°C以上的温度(例如,1400°C或其以上)的环境的上述生产线外热处理,或者于进行这两者之后,制造玻璃板。再者,于具有本变形例的如上所述的组成的玻璃时,于1380°C下黏度成为约56Pa · S。以上,以抑制因搅拌翼103a的表面的附着物所引起的气泡的形成的玻璃板的制造为例,详细说明了本发明,但本发明的应用并不限定于此。本发明例如亦可用于如下玻璃板的制造抑制由于第I输送管105a、第2输送管105b、第3输送管105c、澄清管102、成形装置104等及其他玻璃制造用装置的与熔融玻璃接触的表面的附着物所引起的气泡的形成。符号说明100 玻璃板生产线101 熔解槽102 澄清槽103 搅拌槽103a 搅拌翼104 成形装置现有技术文献专利文献专利文献I :日本专利特表2001-503008号公报
本发明是一种玻璃板的制造方法,其特征在于包括如下准备步骤于使玻璃板生产线正式运转之前,对铂或铂合金制的搅拌翼(103a)进行热处理,藉此去除上述搅拌翼(103a)的与熔融玻璃接触的表面的附着物。
玻璃板的制造方法
- 专利详情
- 全文pdf
- 权力要求
- 说明书
- 法律状态
查看更多专利详情
下载专利文献
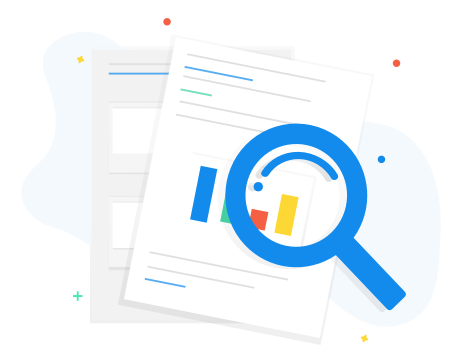
下载专利
同类推荐
-
苅谷浩幸, 前田伸广苅谷浩幸, 前田伸广苅谷浩幸, 前田伸广苅谷浩幸, 前田伸广村上次伸, 日冲宣之村上次伸, 日冲宣之村上次伸, 日冲宣之
您可能感兴趣的专利
-
藤本慎吾, 村上次伸藤本慎吾, 村上次伸藤本慎吾, 村上次伸藤本慎吾, 村上次伸藤本慎吾, 村上次伸藤本慎吾, 村上次伸王新, 王桂英
专利相关信息
-
堀顺士J·H·阿伦斯J·H·阿伦斯J·H·阿伦斯蒂莫·皮沃斯基, 贝恩德·威尔维斯蒂莫·皮沃斯基, 贝恩德·威尔维斯