利用成份梯度设计制备高强高韧性层状氮化硅陶瓷的工艺制作方法
- 专利详情
- 全文pdf
- 权力要求
- 说明书
- 法律状态
利用成份梯度设计制备高强高韧性层状氮化硅陶瓷的工艺的制作方法[0002]氮化硅陶瓷具有良好的室温及高温机械性能,强度高,密度小,耐磨蚀,抗热震能力强,抗化学腐蚀,低热膨胀系数,是结构陶瓷中研究最为广泛深入的结构材料,亦是陶瓷发动机及其它高温结构件、切削工具、耐磨件等的主要候选材料。一直是结构陶瓷材料的研究热点。但是,因氮化硅陶瓷的脆性缺陷一直未得到彻底的改善,这大大限制了它的实际应用范围。如何提高氮化硅陶瓷的韧性仍是Si3N4陶瓷研究的焦点。目前从事氮化硅陶瓷研究的学者为了提高氮化硅陶瓷的韧性,主要是从显微结构设计和晶界组成设计两个方面提出了很多Si3N4陶瓷的增韧方法。比如从显微结构设计角度出发,有颗粒弥散增韧、晶须或纤维增韧、ZrO2的相变增韧及利用柱状P-Si3N4晶粒的自增韧等;从晶界组成设计角度出发,设计出力学性能优异的晶界结合相等。但这些途径取得的增韧效果依然有限,近年国内外学者从贝壳的层状结构可以产生较大的韧性得到启发,提出了陶瓷的层状结构复合增韧。主要是陶瓷层之间设计一层相对较“软”的弱界面层,比如石墨、氮化硼等。在这种强-弱界面交替组合的层状结构中,当强界面上的裂纹扩展至弱界面层时,裂纹将发生偏转,能量被部分吸收,从而产生增韧效果。这种强-弱界面结在陶瓷的层状结构增韧机制中研究的较多,并已成功制备出来多种氧化物与非氧化物层状复合陶瓷材料,例如,在氮化硅陶瓷材料方面,已有人制备出了 Si3N4/BN层状复合材料,使氮化硅的韧性得到较大提高。但是陶瓷材料的层状结构复合增韧途径除了上述强-弱界面交替结合的结构外,理论上还可以设计成强-强界面结合。这种强-强界面层状结构的增韧机理是利用各层之间的热膨胀系数之间的差异,在界面层上产生压应力效果,当裂纹扩展至界面时,首先要克服压应力,然后再继续扩展,这些预先设计的压应力就能额外吸收裂纹扩展的能量,从而起到增韧效果。利用这种机制近年国外有人在制备氧化锆/氧化铝复合材料进行了尝试取得了较为显著的增韧效果。但在氮化硅材质方面国内外均没有人进行这种强-强界面层增韧的研究。因为一方面,这种基于界面层压应力的设计需要调整好各层界面的热膨胀系数,界面两边层的热膨胀系数差异如果太大则容易造成界面剥离,差异太小则压应力效果不明显,增韧效果也就不理想。另一方面,还要避免因各层成份梯度过大,造成烧结温度差异太大,烧成控制困难。氧化锆和氧化铝二者的平均膨胀系数的差异相对比较小,详见表1,在用成份梯度控制各层的平均热膨胀系数时,相对较容易,由此造成的层间剥离也较容易避免,并且控制各层的烧成温度一致也相对容易; 表1各种材料的平均热膨胀系数(25°C -700°C)
查看更多专利详情
下载专利文献
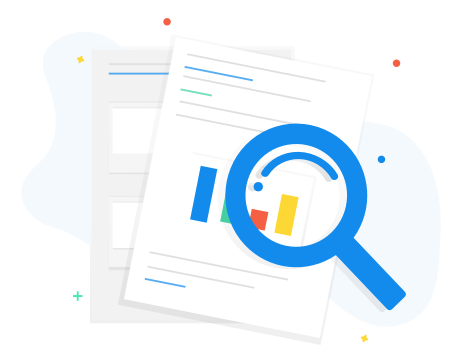
下载专利
同类推荐
-
乐红志, 杨赞中杰夫·斯科特·杜根, 蒂姆·保罗·麦钱特
您可能感兴趣的专利
-
杨志峰周延春, 陈声崎陈凯, 陈树德
专利相关信息
-
陈凯, 陈树德李明照埃胡德·马罗姆, 迈克尔·米治里特斯基I·基拉伊I·基拉伊乐红志, 杨赞中