一种焙烧炉炉底用隔热砖及其制备方法 【技术领域】,具体地说涉及一种焙烧炉炉底用隔热砖及其制 备方法。 [0002] 近几年,大型炭素焙烧炉越来越多,焙烧温度高,焙烧周期短,炭素焙烧炉窑体结 构中底部的隔热砖在高温下长期承受上部砖体和焙烧制品的重量的作用,以及上部的电极 箱加热墙等部位高温作用和焙烧周期内温度变化的作用,由于焙烧炉炉底用隔热砖受力复 杂以及上述多种因素的影响,使得焙烧炉炉底用隔热砖成为焙烧炉中最容易、最先破坏的 部位,焙烧炉炉底用隔热砖的寿命决定着整个焙烧炉的使用寿命。对隔热砖来说,组成隔热 砖的轻质耐火材料的材质对隔热砖的寿命起着决定性的影响。 [0003] 从上述影响隔热砖使用寿命的多种因素分析,焙烧炉炉底用隔热砖的轻质耐火材 料必须具备高强度、低导热、线变化小等性能,以避免火道墙下陷变形。但目前,焙烧炉炉底 用隔热砖大多使用的是由粉煤灰和膨化珍珠岩烧结成的,存在着强度低、导热系数高、重烧 线变化大等弊端,易引起火道墙变形,焙烧炉的使用寿命短。
[0004] 本发明的目的在于克服上述现有技术的缺陷,提供一种焙烧炉炉底用隔热砖及其 制备方法,本发明所制备的焙烧炉炉底用隔热砖具有强度高、导热低、线变化小等性能。
[0005] 为了实现上述目的,本发明的技术方案是: 一种焙烧炉炉底用隔热砖,由蓝晶石粉、氧化铝粉、煅烧高岭土粉、生粘土粉挤压 煅烧而成,以质量百分比计,粒度彡〇. 1mm的蓝晶石粉的质量百分比为10?15%、细度 彡0. 073mm的氧化铝粉的质量百分比为5?10%、细度彡0. 088mm的煅烧高岭土粉的质量百 分比为35?40%、细度彡0. 088_的生粘土粉的质量百分比为40?45%。
[0006] 本发明并提供了该焙烧炉炉底用隔热砖的制备方法,该制备方法的工艺步骤为: (1) 、生粘土粉、煅烧高岭土粉分别用雷蒙磨研磨成细度< 0. 088mm的细粉; (2) 、选取质量百分比为35?40%、细度彡0. 088mm的煅烧高岭土粉、质量百分比为 10?15%、粒度彡0· 1mm的蓝晶石粉、质量百分比为5?10%、细度彡0· 073mm的氧化铝粉、 质量百分比为40?45%、细度< 0. 088mm的生粘土粉混合,制成混合料; (3) 、按与混合料质量比为100 :1?2的比例加入EPS小球和锯末,混炼7?10分钟; (4) 、加入水,混炼10?15分钟,得到混炼泥浆; (5) 、将混炼泥浆在挤泥机挤压成型,调整出泥口尺寸并切割,得到所需尺寸的隔热砖 砖坯; (6) 、将隔热砖砖坯经80?160°C干燥后,装入隧道窑中,在1350?1380°C温度中进行 煅烧制成焙烧炉炉底用隔热砖成品。
[0007] 本发明具有的优点和积极效果是: 本发明利用蓝晶石粉、氧化错粉、耐火粘土、锻烧商岭土粉通过AL203-Si02二兀相图, 设计出合成莫来石的化学成分,并依照该相图找出合成莫来石的最佳组合及温度,从而一 步合成莫来石相;再利用EPS小球和锯末作烧失物制成炭素炉炉底用隔热砖,所制备的焙 烧炉炉底用隔热砖具有强度高、导热低、线变化小等优点。
[0008] 下面结合具体的实施例对本发明作进一步地说明。
[0009] 实施例一: 1、 将煅烧高岭土粉、生粘土粉分别研磨成细度< 〇. 〇88mm的细粉; 2、 选取细度彡0· 073mm的氧化铝粉5%、细度彡0· 088mm的生粘土粉40%、细度 彡0· 088mm的煅烧高岭土粉40%、粒度彡0· 1mm的蓝晶石粉15%混合,制成混合料; 3、 按与混合料质量比为100 :1的比例加入EPS小球和锯末,混炼7分钟; 4、 加入水后混炼10分钟,得到混炼泥浆; 5、 将混炼泥浆在挤泥机挤压成型,通过调整出泥口尺寸并切割,得到所需尺寸的砖 坯; 6、 将隔热砖砖坯经80°C干燥后,装入隧道窑中,在1350°C温度中进行煅烧制成焙烧炉 炉底用隔热砖成品。
[0010] 实施例二: 1、 将煅烧高岭土粉、生粘土粉分别研磨成细度< 0. 088mm的细粉; 2、 选取细度彡0.073mm的氧化铝粉10%、细度彡0.088mm的生粘土粉45%、细度 彡0· 088mm的煅烧高岭土粉35%、粒度彡0· 1mm的蓝晶石粉10%混合,制成混合料; 3、 按与混合料质量比为100 :2的比例加入EPS小球和锯末,混炼10分钟; 4、 加入水后混炼15分钟,得到混炼泥浆; 5、 将混炼泥浆在挤泥机挤压成型,通过调整出泥口尺寸并切割,得到所需尺寸的砖 坯; 6、 将隔热砖砖坯经160°C干燥后,装入隧道窑中,在1380°C温度中进行煅烧制成焙烧 炉炉底用隔热砖成品。
[0011] 实施例三: 1、 将煅烧高岭土粉、生粘土粉分别研磨成细度< 0. 088mm的细粉; 2、 选取细度彡0· 073mm的氧化铝粉8%、细度彡0· 088mm的生粘土粉43%、细度 彡0· 088mm煅烧高岭土粉38%、粒度彡0· 1mm的蓝晶石粉11%混合,制成混合料; 3、 按与混合料质量比为100 :1. 5的比例加入EPS小球和锯末,混炼12分钟; 4、 加入水后混炼12分钟,得到混炼泥浆; 5、 将混炼泥浆在挤泥机挤压成型,通过调整出泥口尺寸并切割,得到所需尺寸的砖 坯; 6、 将隔热砖砖坯经KKTC干燥后,装入隧道窑中,在1360°C温度中进行煅烧制成焙烧 炉炉底用隔热砖成品。
[0012] 实施例四: 1、 将煅烧高岭土粉、生粘土粉分别研磨成细度< 〇. 〇88mm的细粉; 2、 选取细度彡0· 073mm的氧化铝粉6%、细度彡0· 088mm的生粘土粉44%、细度 彡0· 088mm的煅烧高岭土粉36%、粒度彡0· 1mm的的蓝晶石粉14%混合,制成混合料; 3、 按与混合料质量比为100 :1. 5的比例加入EPS小球和锯末,混炼11分钟; 4、 加入水后混炼14分钟,得到混炼泥浆; 5、 将混炼泥浆在挤泥机挤压成型,通过调整出泥口尺寸并切割,得到所需尺寸的砖 坯; 6、 将隔热砖砖坯经120°C干燥后,装入隧道窑中,在1370°C温度中进行煅烧制成焙烧 炉炉底用隔热砖成品。
[0013] 本发明的焙烧炉炉底用隔热砖与普通隔热砖理化性能比较,强度高、导热低、线变 化小,与普通隔热砖相比,其性能的优异性如下表:
一种焙烧炉炉底用隔热砖及其制备方法
- 专利详情
- 全文pdf
- 权力要求
- 说明书
- 法律状态
查看更多专利详情
下载专利文献
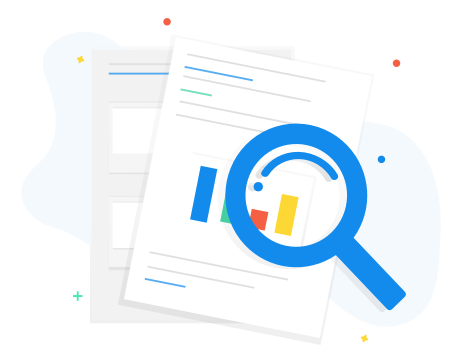
下载专利
同类推荐
-
王志明, 张立王志明, 张立
您可能感兴趣的专利
-
李志强陈凯, 陈树德陈凯, 陈树德李明照
专利相关信息
-
埃胡德·马罗姆, 迈克尔·米治里特斯基埃胡德·马罗姆, 迈克尔·米治里特斯基I·基拉伊I·基拉伊I·基拉伊I·基拉伊I·基拉伊