专利名称:液相强化烧结制备金属陶瓷增强的碳复合材料的方法 质子交换膜燃料电池(PEMFC)主要由三部分构成,即膜电极(MEA)、双极板和电池管理系统。双极板不仅是将单个PEMFC串联起来组装成电池堆的关键部件,而且还担负将燃料反应气导入燃料电池并传导电流,同时还担负起整个电池的散热功能和排水功能。因此双极板质量的好坏将直接决定燃料电池堆输出功率的大小和使用寿命的长短。经文献检索发现,Theodore M.Besmannd等人发表《Carbon/Carbon Composite Bipolar Plate for Proton Exchange Membrane FuelCells》(用于质子交换膜燃料电池的碳/碳复合材料双极板)一文,见《Journal of TheElectrochemical Society》(电化学学会通报)147(2000)4083-4086。该文介绍采用碳纤维增强酚醛树脂,然后高温炭化得到空隙率很高的碳制品,通过高温化学气相渗透工艺获得最终的碳/碳复合材料双极板。该方法制备的双极板导电导热性能好、强度高、空隙率低,但该工艺制备周期长,能源消耗量大,因而生产成本较高,其应用受到了一定的限制。
本发明的目的在于针对以上现有技术的不足,提供一种液相强化烧结制备金属陶瓷增强的碳复合材料的方法,通过搀杂双组员的钛镍、钛铬金属粉或三组员的钛铁钼金属粉进行液相强化烧结制备金属陶瓷增强碳复合材料的方法,使其可适用于工业化生产制备大尺寸高性能的碳复合材料双极板,同时该方法制造成本低,制备出的双极板电导率和强度优于现有的石墨双极板,高度致密化,通过模压工艺气体流道可一次成型。特别的,该方法可用于制备大尺寸而厚度比较薄的具有复杂结构的石墨层压板。本发明是通过以下技术方案实现的,本发明采用中间相碳微球或中间相焦碳粉为基材原材料,掺杂预合金化的具有确定组成的双组员的钛镍、钛铬金属粉或三组员的钛铁钼金属粉。在高温烧结过程中,基材炭化形成固相;掺杂的金属粉与碳反应生成多组员的具有低共熔点的合金和金属陶瓷,液相的合金和金属陶瓷在毛细管力的作用下渗透进固相的空隙中和晶间缺陷中形成增强相,完成液相强化烧结。通过水基流延工艺制备碳复合材料生坯,将多层流延生坯模压得到带有气体流道的层压生坯,再通过层压生坯的高温液相烧结工艺获得金属陶瓷增强的碳复合材料板。烧结后的坯体经过树脂浸渍、打磨和修饰后,最终得到质子交换膜燃料电池双极板。以下对本发明方法作进一步的说明,方法步骤如下(1)首先将重量比为3/1的双组员的钛镍、钛铬金属粉或重量比为10/4/1的三组员的钛铁钼金属粉通过高速球磨机进行球磨混合,球磨时间等于或者大于10小时以利于金属粉的预合金化;(2)根据材料流延工艺配方将中间相碳粉、预合金化的双组员的钛镍、钛铬金属粉或三组员的钛铁钼金属粉加入到水与酒精的混合溶剂中,然后加入分散剂并球磨2小时,向第一次球磨后的混合浆料中加入粘结剂、增塑剂和消泡剂并再次球磨2小时,通过将球磨好的浆料在真空中均化30分钟消除浆料中的气泡;(3)流延浆料制备采用如下配方设定中间相碳粉、预合金化的双组员的钛镍、钛铬金属粉或三组员的钛铁钼金属粉混合物120克,粘结剂聚乙烯醇8克,增塑剂聚乙二醇10克,分散剂吐温4克,溶剂水120克,增湿剂酒精20克;(4)将均一、稳定的混合浆料倒入流延机的料仓中进行流延,通过干燥、切片制得流延生坯;(5)将多片流延生坯放入模具中进行模压制得层压生坯,模压温度控制在85℃,模压压力控制在100MPa到250Mpa,气体流道通过模具一次模压成型;(6)将生坯进行真空烧结制得带有流道的金属陶瓷增强的碳复合材料板,烧结分两个阶段进行第一阶段为从室温到550℃,升温速率控制在5℃/分钟左右,并在550℃保温30分钟到1小时,中间相碳粉融并烧结形成固相骨架;第二阶段的烧结从550℃到1200℃以上,为液相强化烧结,升温速率控制在2℃/分钟左右,双组员的钛镍、钛铬金属粉或三组员的钛铁钼金属粉将和基材中的碳反应生成碳化物,同时金属粉相互之间及金属粉与金属碳化物之间生成具有低共熔点的合金和金属陶瓷,高温下,融化的合金和金属陶瓷形成液相并在毛细管力的作用下渗透到固相中的空隙和晶间缺陷中,填补孔隙和晶间缺陷形成增强相,完成液相强化烧结。当温度升到预先设定的最高烧结温度时应保温1小时到2小时以利产品的致密化。烧结后的产品自然冷却;(7)将烧结后的碳复合材料板用环氧树脂浸渍封孔首先用丙酮或酒精擦洗碳复合材料板表面,去除表面的污垢和灰尘,然后放入环氧树脂溶液中,环氧树脂的粘度小于或者等于200秒,在真空环境下,浸渍压力为5MPa,将碳碳复合材料板浸渍半小时到1小时后取出,当环氧树脂在85℃~100℃下完全固化后,通过机械打磨除去碳碳复合材料板表面浸渍的多余的环氧树脂,浸渍过程进行一次或多次,得到经过环氧树脂封孔并带有气体流道的质子交换膜燃料电池碳复合材料双极板。本发明的主要原材料中间相碳粉可采用中间相碳微球、机械粉粹的针状焦颗粒为碳前驱体,其平均粒径为5~100微米。中间相碳微球可从煤焦油沥青、石油焦沥青或低级稠环芳烃化合物在一定的条件下合成制备。掺杂的双组员的钛镍、钛铬金属粉或三组员的钛铁钼金属粉在烧结过程中形成具有低共熔点的合金,或和生成的金属碳化物形成具有低共熔点的金属陶瓷,在混合物中,掺杂金属粉的质量控制在0%~60%。并且这种低共熔点的合金或金属陶瓷形成的液相在高温下对基材碳具有一定的浸润性。平均粒径小的金属粉有利于液相强化烧结。烧结后的碳复合材料板可进行石墨化处理,也可不进行石墨化处理。本发明的碳复合材料板由于具有较高的导电导热性,可采用热固性树脂如环氧树脂在真空条件和一定的压力下进行浸渍封孔进一步降低材料的空隙率,而最终产品双极板的导电导热性不会有大幅度的降低,但是双极板的耐气体渗透性和机械性能会有大幅度的提高。本发明具有实质性特点和显著进步,本发明首次采用流延成型和液相强化烧结工艺制备金属陶瓷增强的碳复合材料双极板,并通过层板模压工艺一次性加工出气体流道,省却了传统工艺流道后续机械加工的局限,从而大大降低机械加工费用,提高产品成品率,缩短产品生产周期。本发明制备的碳复合材料双极板具有优异的导电导热性,便于提高燃料电池的功率密度和散热性,保证燃料电池的运行稳定,具有较好的的机械强度,以提供电池堆装配所需的机械支撑;同时重量轻,有利于电池的小型化和薄型化,还具有自密封特点和良好的化学稳定性。所采用的工艺能成型质量均匀的大面积薄板,这有利于燃料电池的小型化薄型化,对制作笔记本电脑、电动车及移动通讯电源具有突出重要的意义;流道可一次成型,不仅可缩短生产周期,更有利于大幅降低加工成本;产品孔隙率低,可提高耐气体渗透性;工艺简单,加工成本低。
结合本发明方法的内容提供以下三个实施例实施例一将重量为115克的中间相碳微球和重量比为3/1的预合金化的双组员钛镍金属粉45克加入40克的水与20克酒精的混合溶剂中,然后加入吐温4克球磨混合2小时,再加入88克浓度为9.1%的聚乙烯醇水溶液,10克聚乙二醇并继续球磨2小时得到稳定、均一的流延浆料。将此浆料在真空度低于200毫巴条件下静置30分钟然后在流延机上流延,经过室温干燥后得到厚度约为1毫米左右的流延生坯。将4块尺寸为120×90毫米的流延生坯放入模具中,在压力为150MPa、温度为85℃下模压,获得带有气体流道的模压生坯。将模压生坯放入烧结炉中在1400℃下烧结。从室温到550℃,升温速率为5℃/分钟并在550℃时保温30分钟,然后升温速率控制在2℃/分钟加热至1400℃,并保温1小时得到烧结后的半成品。然后用丙酮清洗烧结半成品的表面,放入粘度小于200秒(4号粘度杯)的环氧树脂中,在真空中浸渍40分钟后取出放入85℃的烘箱中,等环氧树脂完全固化后,通过机械打磨除去半成品表面多余的树脂后得到最终产品,即金属陶瓷增强的碳复合材料双极板。该法制备的双极板具有非常好的导电导热性,较高的机械强度和一定的韧性,以及较低的气孔率。
实施例二将重量为115克的中间相碳微球和重量比为10/4/1的预合金化的三组员钛铁钼金属粉45克加入40克的水与20克酒精的混合溶剂中,然后加入吐温4克球磨混合2小时,再加入88克浓度为9.1%的聚乙烯醇水溶液,10克聚乙二醇并继续球磨2小时得到稳定、均一的流延浆料。将此浆料在真空度低于200毫巴条件下静置30分钟然后在流延机上流延,经过室温干燥后得到厚度约为1毫米左右的流延生坯。将4块尺寸为400×350毫米的流延生坯放入模具中,在压力为200MPa、温度为85℃下模压,获得带有气体流道的模压生坯。将模压生坯放入烧结炉中在1400℃下烧结。从室温到550℃,升温速率为5℃/分钟并在550℃时保温30分钟,然后升温速率控制在2℃/分钟加热至1400℃,并保温1小时得到烧结后的半成品。然后用丙酮清洗烧结半成品的表面,放入粘度小于200秒(4号粘度杯)的环氧树脂中,在真空中浸渍40分钟后取出放入85℃的烘箱中,等环氧树脂完全固化后,通过机械打磨除去半成品表面多余的树脂后得到最终产品,即金属陶瓷增强的碳复合材料双极板。该法制备的双极板具有很好的导电导热性,较高的机械强度和一定的韧性,以及较低的气孔率。该法可制备大尺寸的带有气体流道的碳复合材料双极板。
实施例三将重量为115克的针状焦碳粉和重量比为3/1的预合金化的双组员钛铬金属粉45克加入40克的水与20克酒精的混合溶剂中,然后加入吐温4克球磨混合2小时,再加入88克浓度为9.1%的甲基纤维素水溶液,10克聚乙二醇并继续球磨2小时得到稳定、均一的流延浆料。将此浆料在真空度低于200毫巴条件下静置30分钟然后在流延机上流延,经过室温干燥后得到厚度约为0.2毫米左右的流延生坯。将2块尺寸为400×350毫米的流延生坯放入模具中,在压力为200MPa、温度为85℃下模压得到模压生坯。将模压生坯放入烧结炉中在1400℃下烧结。从室温到550℃,升温速率为5℃/分钟并在550℃时保温30分钟,然后升温速率控制在2℃/分钟加热至1400℃,并保温1小时得到烧结后的半成品。然后用丙酮清洗烧结半成品的表面,放入粘度小于200秒(4号粘度杯)的环氧树脂中,在真空中浸渍40分钟后取出放入85℃的烘箱中,等环氧树脂完全固化后,通过机械打磨除去半成品表面多余的树脂后得到最终产品,即金属陶瓷增强的碳复合材料双极板。该法制备的双极板具有较大的尺寸和薄的厚度,具有很好的导电导热性,一定的机械强度和韧性,并有较低的气孔率。
一种液相强化烧结制备金属陶瓷增强的碳复合材料的方法,属于燃料电池领域。本发明采用中间相碳微球或中间相焦炭颗粒为基材原材料,掺杂预合金化的双组员的钛镍、钛铬金属粉或三组员的钛铁钼金属粉,通过水基流延工艺制备碳复合材料生坯,将多层流延生坯模压得到带有气体流道的层压生坯,再通过层压生坯的高温液相烧结工艺获得金属陶瓷增强的碳复合材料板,烧结后的坯体经过树脂浸渍、打磨和修饰后,最终得到质子交换膜燃料电池双极板。本发明首次采用搀杂预合金化的双组员的钛镍、钛铬金属粉或三组员的钛铁钼金属粉制备碳复合材料双极板,并通过层板模压工艺一次性加工出气体流道,大大降低机械加工费用,提高产品成品率,缩短产品生产周期。
液相强化烧结制备金属陶瓷增强的碳复合材料的方法
- 专利详情
- 全文pdf
- 权力要求
- 说明书
- 法律状态
查看更多专利详情
下载专利文献
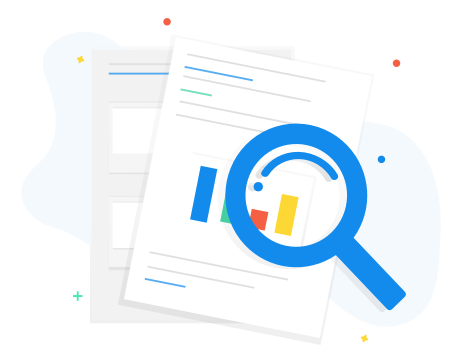
下载专利
同类推荐
-
郑木莲, 李欣熊刚
您可能感兴趣的专利
-
孙妙囡马塞路斯·皮苛特马塞路斯·皮苛特陈凯, 陈树德
专利相关信息
-
李明照埃胡德·马罗姆, 迈克尔·米治里特斯基I·基拉伊I·基拉伊I·基拉伊