一种高导热石墨材料及其制备方法和应用的制作方法[0002]高功率密度电子器件和高端电子工业器件等逐渐向小型化、结构紧凑化、高功率密度化发展,由此引发了散热问题,对电子元器件的工作稳定性和可靠性提出严峻的挑战。因此,热量的散发问题已经成为电子产品小型化、集成化的瓶颈。为了尽快地让电子元件运行过程中产生的热量及时散发出来,开发导热性能更好的材料变得越来越重要。目前一般的散热材料所使用的散热片基材(如民用高端电子器件、LED用芯片材料、工业装置用换热器等)主要是由金属材料(如铝、银和铜)制得的,但这些传统的金属散热材料由于自身密度较大、热膨胀系数较高和材料不纯使其导热率大幅下降,已很难满足散热需求。石墨材料的比热导率(热导率与材料体积密度之比)是传统金属材料的5~12倍,成为较为理想的金属替代材料,是近年来最具发展前景的一类散热材料。[0003]目如国内外已有不少关于闻导热石墨材料的报道和专利。传统的闻导热石墨材料制备方法是将原料破碎、煅烧、粉碎、筛分,再加粘结剂混捏成型,然后多次反复浸溃焙烧,最后石墨化处理,制备工艺复杂。最近改进的方法多数采用易石墨化的浙青为粘结剂(如煤焦油、中间相浙青等),与石油焦(刘朗,邱海鹏,宋永忠,一种高导热石墨材料的制备方法.中国,CNO1130544.4,2003.06.04)或中间相浙青焦(刘朗,高晓晴等,一种高导热石墨材料的制备方法.中国 ,CN200410012433.5,2005.03.23)混配,再在高温(2600。。~30000C )下热压(20~40MPa)处理得到高导热石墨制品。天然鳞片石墨与浙青焦和石油焦相比,本身具有极高的导热率,并且价格低廉。中国专利CN102659095A将天然鳞片石墨、中间相浙青以及短切纤维混合,采用热压制备出高导热石墨;中国专利CN102897753A将天然鳞片石墨插层氧化后,然后和液态碳源混合热压制备出高导热石墨;中国专利CN101708838A将天然鳞片石墨与粘结剂混合,然后经过热压成型、炭化和石墨化制得高导热石墨,上述专利所用的原料是将天然鳞片石墨粉碎成的特定粒径的石墨粉。[0004]锂离子电池因其工作电压高、能量密度大、循环寿命长、自放电小、无记忆效应等优点,成为上世纪九十年代以来继镍氢电池之后的新一代二次电池。在锂离子电池技术开发过程中,电池品质不断得到提高,生产成本不断下降。在对锂离子电池技术进步的贡献中负极材料起了很大作用。目前商品化锂离子电池的负极材料仍然是石墨类材料占主导地位,但在锂离子电池炭负极石墨材料的实际加工过程中,仅将粒径等级符合要求的石墨微粉加工成锂离子电池炭负极材料,通常会产生约占加工总量50~60%的石墨尾料而不被有效利用,以往这些石墨尾料仅作为废弃物或廉价废品进行堆放或销售处理,不仅存在资源浪费大、环境污染等隐患,也增加了锂离子电池负极材料的制造成本。另一方面,中间相碳微球(MCMB)也是锂离子电池常用的负极材料,加工过程中也会产生粒径较小的尾料。因此,如何有效利用这些尾料来生产附加值高的产品具有重要的意义。
[0005]本发明的目的在于克服上述现有技术的不足,提供一种新型的高密高强的高导热石墨材料。[0006]本发明的另一个目的在于提供一种原料来源广泛、工艺简单、重复性好、生产周期短的高导热石墨的制备方法。所述方法能解决锂离子电池炭负极材料加工过程中产生的石墨尾料所致的环境污染问题。[0007]本发明的再一个目的在于提供上述高导热石墨材料的应用,其用于民用高端电子器件、LED用芯片材料、工业装置用换热器等的散热片基材。[0008]本发明的第四个目的在于提供一种散热片基材,所述基材包括上述的高密高强的高导热石墨材料,所述散热片基材用于民用高端电子器件、LED用芯片材料、工业装置用换热器等。
[0009]本发明提供如下的技术方案:
[0010]一种高导热石墨材料,其以中间 相碳微球(MCMB)、锂离子电池炭负极材料加工过程中产生的石墨尾料及陶瓷组元为主要原料,通过冷模压成型和石墨化处理制得。
[0011]根据本发明,所述锂离子电池炭负极材料加工过程中产生的石墨尾料为天然鳞片石墨尾料或人造石墨尾料。
[0012]根据本发明,所述的中间相碳微球可以是直接购买的,也可以是锂离子电池炭负极材料加工过程中的尾料。优选为锂离子电池负极材料中间相碳微球加工过程中气流分级生成的粒度较细的尾料。
[0013]根据本发明,所述的中间相碳微球的粒径D5tl为3~10 μ m,优选粒径D5tl为3~5 μ m0
[0014]根据本发明,所述的陶瓷组元为T1、TiC、TiB2、B4(^PSiC中的一种或多种。所述陶瓷组元的添加量为原料总重量的I~5% (重量),优选为2~4% (重量),更优选为3%
(重量)。
[0015]根据本发明,所述石墨尾料、中间相碳微球及陶瓷组元的重量比为32~68:68~32:1 ~5。
[0016]根据本发明,所述原料由中间相碳微球(MCMB)、锂离子电池炭负极材料加工过程中产生的石墨尾料及陶瓷组元组成。
[0017]根据本发明,所述石墨材料的导热率在300W/m.K以上。优选所述导热率在300~500ff/m.K之间,更优选在320-460W/m.K之间。
[0018]根据本发明,所述石墨材料的密度介于1.80-1.95g/cm3之间。
[0019]根据本发明,所述石墨材料的弯曲强度在30MPa以上。优选所述弯曲强度在30-1OOMPa之间,更优选在30_70MPa之间。
[0020]根据本发明,所述石墨材料的石墨化度达96%以上。优选所述石墨化度介于96%~99%之间。
[0021]根据本发明,所述石墨材料的电阻率达2.0μ Ω.πι以上。优选所述电阻率介于
2.0~3.0 μ Ω.πι之间,更优选介于2.0~2.6 μ Ω.πι之间。
[0022]本发明还公开如下的技术方案:[0023]—种高导热石墨材料的制备方法,其以中间相碳微球(MCMB)、锂离子电池炭负极材料加工过程中产生的石墨尾料及陶瓷组元为主要原料,通过冷模压成型和石墨化处理制得所述闻导热石墨材料。
[0024]根据本发明,所述方法具体包括如下步骤:
[0025](I)将所述中间相碳微球、石墨尾料及陶瓷组元充分混合;
[0026](2)取步骤(1)的混合料,将其装入一钢模内冷压成型,得到生坯体;
[0027](3)将生坯体置于一石墨化炉内进行石墨化处理。
[0028]根据本发明,所述步骤(1)中所述中间相碳微球、石墨尾料及陶瓷组元的重量比为68~32:32~68:1~5 ;所述混合在高速混合机中进行,混合时间为I~3小时。
[0029]根据本发明,所述步骤(2)中的冷压成型可以采用模压成型和等静压成型,优选模压成型;所用的压力为100~240MPa,优选200MPa。
[0030]根据本发明,所述步骤(3)的石墨化处理,是在氮气保护下,首先以I~5°C/min的升温速度升温至900°C,保温20~30min ;然后以5~10°C /min的升温速度升温至1300°C,保温10~30min ;最后以10~20°C /min的升温速度升温至2000~2800°C,保温30 ~60mino
[0031]根据本发明,所述锂离子电池炭负极材料加工过程中产生的石墨尾料为天然鳞片石墨尾料或人造石 墨尾料。
[0032]根据本发明,所述的中间相碳微球可以是直接购买的,也可以是锂离子电池炭负极材料加工过程中的尾料。优选为锂离子电池负极材料中间相碳微球加工过程中气流分级生成的粒度较细的尾料。
[0033]根据本发明,所述的中间相碳微球的粒径D5tl为3~10 μ m,优选粒径D5tl为3~5 μ m0
[0034]根据本发明,所述的陶瓷组元为T1、TiC、TiB2、B4C和SiC中的一种或多种。所述陶瓷组元的添加量为为原料总重量的I~5% (重量),优选为2~4% (重量),更优选为3% (重量)。
[0035]根据本发明,所述原料由中间相碳微球(MCMB)、锂离子电池炭负极材料加工过程中产生的石墨尾料及陶瓷组元组成。
[0036]根据本发明,所述石墨材料的导热率在300W/m.K以上。优选所述导热率在300~500ff/m.K之间,更优选在320-460W/m.K之间。
[0037]根据本发明,所述石墨材料的密度介于1.80-1.95g/cm3之间。
[0038]根据本发明,所述石墨材料的弯曲强度在30MPa以上。优选所述弯曲强度在30-1OOMPa之间,更优选在30_70MPa之间。
[0039]根据本发明,所述石墨材料的石墨化度达96%以上。优选所述石墨化度介于96%~99%之间。
[0040]根据本发明,所述石墨材料的电阻率达2.0μ Ω.πι以上。优选所述电阻率介于
2.0~3.0 μ Ω.πι之间,更优选介于2.0~2.6 μ Ω.πι之间。
[0041]本发明还公开如下的技术方案:
[0042]上述的高导热石墨材料或所述方法制得的高导热石墨材料的应用,其用于民用高端电子器件、LED用芯片材料、工业装置用换热器等的散热片基材。[0043]一种散热片基材,其包括上述的高导热石墨材料或所述方法制得的高导热石墨材料。
[0044]根据本发明,所述散热片基材用于民用高端电子器件、LED用芯片材料、工业装置用换热器等。
[0045]本发明的有益效果是:
[0046]1.与常规的石墨材料制备工艺相比,该工艺经冷压成型和石墨化处理后即完成材料制备,不需要进行多次浸溃、炭化等循环过程,因此材料的制备周期短,且制得的材料的尺寸可放大,容易实现批量生产,大大地降低材料的制作成本。
[0047]2.本发明创造性地将锂离子电池炭负极材料加工过程中生成的石墨尾料制成附加值高的高导热石墨材料,很好地解决了石墨尾料所致的堆放填埋和环境污染等问题和隐患,实现废弃资源的综合利用,使锂离子电池复合负极材料加工企业的综合成本降低10%以上。
[0048]3.本发明工艺简单,有序化、高致密与石墨化为一次完成,相应成本较低。又因制备过程中使用了自烧结性好的中间性碳微球,没有外加第二相粘结剂所引起的热传导缺陷,所制得的高导热石墨材料具有更好的导热性能。
[0049]4.本发明的高导热石墨材料,将MCMB和石墨尾料及陶瓷组元混合,不仅提高MCMB的C/Η比,而且改善MCMB的粘结性能和石墨化程度,制备出高密高强的高导热石墨材料。
[0050]5.本发明的石墨材料,导热率高、密度高、弯曲强度高,石墨化度达96%以上,电阻率达2.0 μ Ω.m以上,特别适合于作为民用高端电子器件、LED用芯片材料、工业装置用换热器等的散热片基材。
[0051]如上所述,本发明公开了一种高导热石墨材料,其以中间相碳微球(MCMB)、锂离子电池炭负极材料加工过程中产生的石墨尾料及陶瓷组元为主要原料,通过简单冷模压成型和石墨化处理制得。
[0052]一般而言,纯石墨材料粘结性能差,不易成型和机械加工;纯的MCMB烧结性能差,易出现各种缺陷。 申请人:经过长期的研究发现:把MCMB和石墨尾料及陶瓷组元混合,可以提高MCMB的C/Η比,改善MCMB的粘结性能和石墨化程度,制备出高密高强的高导热石墨材料。基于上述发现, 申请人:完成了本发明。
[0053]根据本发明,所述以锂离子电池炭负极材料加工过程中产生的石墨尾料为天然鳞片石墨尾料或人造石墨尾料。
[0054]本发明所使用的锂离子电池炭负极材料加工过程中产生的天然鳞片石墨尾料,碳含量>95%,粒径为1000~1500目;人造石墨尾料,碳含量> 99%,粒径为1800~4000目。上述天然鳞片石墨和人造石墨都属于晶体碳,所含杂质(如硫、磷、氮)含量低且质量稳定,勿需另外磨粉或磨碎,从而简化了制备工艺,有利于规模化生产,可显著提高产量,有效降低生产成本,是一类理想的新型高导热材料。
[0055] 本发明所使用的石墨尾料和中间相碳微球为球形或近似球形,振实密度高,颗粒堆积密度更紧密,减少复合材料的孔洞缺陷,从而改善材料的热学性能。所述石墨材料的导热率高于300W/m.K、密度为1.80-1.95g/cm3、弯曲强度高(大于30MPa),石墨化度达96 %以上,电阻率达2.0 μ Ω.m以上。
[0056]以下结合实施例对本发明作进一步的详细说明,但本发明的保护范围不仅限于以下实施例。根据本发明公开的内容,本领域技术人员将认识到在不脱离本发明技术方案所给出的技术特征和范围的情况下,对以上所述实施例做出许多变化和修改都属于本发明的保护范围。
[0057]实施例
[0058]下述实施例中使用的石墨尾料的碳含量≥95%,粒径为1000~1500目,中间相碳微球可以是锂离子电池炭负极材料加工过程中的尾料,也可以是市场购买的,粒径D5tl为3 ~10 μ m
[0059]实施例1
[0060]首先将天然鳞片石墨尾料、中间相碳微球及TiB2按重量比为32:63:5进行称量,在高速混合机中混合2小时。然后取一定量的混合料将其装入一钢模内,在平板硫化机上用IOOMPa的压力成型,保压10分钟脱模得到生坯体。将生坯体置于一石墨化炉内,在氮气的保护下,首先以2V /min的升温速度升温至900°C,保温30min ;然后以5°C /min的升温速度升温至1300°C,保温20min ;最后以10°C /min的升温速度升温至2000°C,保温60min,自然冷却到100°C得到本发明的高导热石墨材料。其物理性能见表1。
[0061]实施例2
[0062]首先将人造石墨尾料、中间相碳微球及TiC按重量比为50:46:4进行称量,在高速混合机中混合I小时。然后取一定量的混合料将其装入一钢模内,在平板硫化机上用200MPa的压力成型,保压5分钟脱模得到生坯体。将生坯体置于一石墨化炉内,在氮气的保护下,首先以2V /min的升温速度升温至900°C,保温20min ;然后以3°C /min的升温速度升温至1300°C,保温30min ;最后以15°C /min的升温速度升温至2200°C,保温40min,自然冷却到100°C得到本发明的高导热石墨材料。其物理性能见表1。
[0063]实施例3
[0064]首先将天然鳞片石墨尾料、中间相碳微球及B4C按重量比为64:33:3进行称量,在高速混合机中混合3小时。然后取一定量的混合料将其装入一钢模内,在平板硫化机上用240MPa的压力成型,保压I分钟脱模得到生坯体。将生坯体置于一石墨化炉内,在氮气的保护下,首先以1°C /min的升温速度升温至900°C,保温20min ;然后以5°C /min的升温速度升温至1300°C,保温20min ;最后以20°C /min的升温速度升温至2000°C,保温40min,自然冷却到100°C得到本发明的高导热石墨材料。其物理性能见表1。
[0065]实施例4
[0066]首先将人造石墨尾料、中间相碳微球及SiC按重量比为60:35:5进行称量,在高速混合机中混合2小时。然后取一定量的混合料将其装入一钢模内,在平板硫化机上用150MPa的压力成型,保压5分钟脱模得到生坯体。将生坯体置于一石墨化炉内,在氮气的保护下,首先以2V /min的升温速度升温至900°C,保温30min ;然后以3°C /min的升温速度升温至1300°C,保温30min ;最后以10°C /min的升温速度升温至2200°C,保温30min,自然冷却到100°C得到本发明的高导热石墨材料。其物理性能见表1。
[0067]实施例5
[0068]首先将天然鳞片石墨尾料、中间相碳微球及TiB2按重量比为45:50:5进行称量,在高速混合机中混合I小时。然后取一定量的混合料将其装入一钢模内,在平板硫化机上用ISOMPa的压力成型,保压6分钟脱模得到生坯体。将生坯体置于一石墨化炉内,在氮气的保护下,首先以2V /min的升温速度升温至900°C,保温30min ;然后以3°C /min的升温速度升温至1300°C,保温30min ;最后以10°C /min的升温速度升温至2200°C,保温30min,自然冷却到100°C得到本发明的高导热石墨材料。其物理性能见表1。
[0069]实施例6
[0070]首先将人造石墨尾料、中间相碳微球及Ti按重量比为60:37:3进行称量,在高速混合机中混合I小时。然后取一定量的混合料将其装入一钢模内,在平板硫化机上用150MPa的压力成型,保压5分钟脱模得到生坯体。将生坯体置于一石墨化炉内,在氮气的保护下,首先以2V /min的升温速度升温至900°C,保温30min ;然后以3°C /min的升温速度升温至1300°C,保温30min ;最后以10°C /min的升温速度升温至2000°C,保温50min,自然冷却到100°C得到本发明的高导热石墨材料。其物理性能见表1。
[0071]表1
[0072]
一种高导热石墨材料及其制备方法和应用制作方法
- 专利详情
- 全文pdf
- 权力要求
- 说明书
- 法律状态
查看更多专利详情
下载专利文献
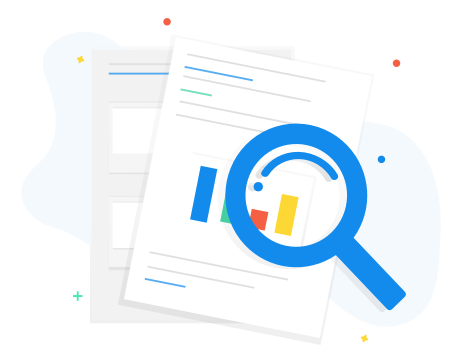
下载专利
同类推荐
-
范颖芳, 张世义何玉明胡世莲胡世莲
您可能感兴趣的专利
-
胡世莲胡世莲吴其修, 刘明东黄安平, 赵引康黄安平, 赵引康
专利相关信息
-
张志义H·朗瓦拉