头孢美唑钠特种超细粉体制剂及其制备方法 【技术领域】。 [0002]头孢美唑钠,其英文名称为Cefmetazole Sudium,化学名称为(6R,7S)-7_[2_[(氰甲基)硫代]乙酰胺基]-7-甲氧基_3-[[ (1-甲基-1H-四唑-5-基)硫代]甲基]-8-氧代-5-硫杂-1-氮杂双环[4.2.0]辛-2-烯-2-羧酸钠盐。分子式为C15H16N7NaO5S3,分子量为 493.52。 [0003]头孢美唑钠为第二代头孢菌素,是日本三共公司创制的半合成头曲霉素类抗生素,对阴性杆菌产生的广谱β_内酰胺酶有较好的稳定性。大肠杆菌、克雷伯肺炎杆菌、奇异变形杆菌、志贺菌属、沙门菌属等阴性杆菌对本品有较好的敏感性。金葡菌、A组溶血性链球菌、卡他布拉汉菌对本品高度敏感。头孢美唑钠用于敏感菌引起的呼吸系统感染、胆道感染、泌尿系感染、妇产科细菌感染、皮肤软组织感染及手术后预防感染等。 [0004]现有的头孢美唑钠存在澄清度低、稳定性差、纯度低、杂质多、颗粒大、比表面积小、溶解性差、毒副作用大、容易过敏等缺点。
[0005]本发明的目的在于提供一种头孢美唑钠特种超细粉体制剂及其制备方法,使头孢美唑钠具有澄清度好、稳定性高、纯度高、杂质少、颗粒小、比表面积大、溶解性好、毒副作用小、不易过敏等优点。
[0006]为解决上述技术问题,本发明的头孢美唑钠特种超细粉体制剂以头孢美唑苄酯为原料,在二氯甲烷、苯甲醚与三氯化铁的体系中反应,经盐酸丙酮混合液酸解,收集的有机相用氯化钠溶液提纯,用碳酸氢钠溶液转相,收集的水相用活性炭和氧化铝脱色,用乙酸乙酯与盐酸转相,加晶种析晶制得头孢美唑酸,与碳酸氢钠反应制得头孢美唑钠,经提纯,气流超细粉碎制得。
[0007]为解决上述技术问题,本发明的头孢美唑钠特种超细粉体制剂的制备方法,该方法包括如下步骤:
步骤I,将头孢美唑苄酯加入到二氯甲烷中,降至低温后加入苯甲醚、三氯化铁,并在低温下进行反应,反应结束后将反应液加入到盐酸与丙酮的混合液中,搅拌后静置分层,收集有机相,将有机相倒入氯化钠溶液中,搅拌静置分层,收集有机相;
步骤2,在有机相中加入碳酸氢钠溶液调节pH,搅拌后静置分层,收集水相,将水相用乙酸调节ΡΗ,再加入活性炭脱色,过滤,在滤液中加入氧化铝,过滤,滤液加入乙酸乙酯,滴加盐酸调节ΡΗ,加入头孢美唑酸晶种搅拌析晶,过滤,二氯甲烷洗涤,经真空干燥制得头孢美唑酸;
步骤3 ,将头孢美唑酸加入纯化水中,加入碳酸氢钠反应制得头孢美唑钠,用乙酸乙酯多次萃取,静置分层后收集水相,向水相中加入乙醇钠乙醇溶液脱除杂质,过滤沉淀物,滤液进行减压浓缩,然后向浓缩液中加入丙酮,进行降温析晶,离心甩虑,滤饼用丙酮洗涤,经真空干燥得高纯度的头孢美唑钠白色固体;
步骤4,将干燥的高纯度头孢美唑钠用气流粉碎成超细粉体,进行回收,包装,制得头孢美唑钠特种超细粉体制剂。
[0008]作为本发明的改进,该步骤I中头孢美唑苄酯低温反应的温度为-30~-20°C,头孢美唑苄酯与二氯甲烷的重量比为1:5~1:10,头孢美唑苄酯与苯甲醚的重量比为1:11~1:15,头孢美唑苄酯与三氯化铁的重量比为1:2~1:3。
[0009]作为本发明的改进,该步骤I中组成混合液的盐酸溶液浓度为8~12%,头孢美唑苄酯与盐酸溶液的重量比为1:7~1:8.6,头孢美唑苄酯与丙酮的重量比为1:8~1:10,氯化钠溶液的浓度为8~12%。
[0010]作为本发明的改进,该步骤2中碳酸氢钠溶液浓度为3~8%,用碳酸氢钠溶液调节pH至7~8,水相用乙酸调节pH到5.5~6.5,活性炭用量为头孢美唑苄酯重量的10~30%,氧化铝用量为头孢美唑苄酯重量的30~40%。
[0011]作为本发明的改进,该步骤2中乙酸乙酯用量为头孢美唑苄酯重量的0.9~1.1倍,盐酸浓度为20~30%,用盐酸调节pH至I~2,头孢美唑酸晶种用量为头孢美唑苄酯重量的0.6~0.8%,搅拌析晶时间为4~6小时。
[0012]作为本发明的改进,该步骤3中纯化水用量为头孢美唑酸重量的15~25倍,头孢美唑酸与碳酸氢钠的摩尔比为1:1,乙酸乙酯萃取次数为2~4次,每次萃取的乙酸乙酯的用量为纯化水体积的30~40%,乙醇钠与头孢美唑酸的摩尔比为1:1~1:1.5,脱除杂质温度为55~65°C。
[0013]作为本发明的改进,该步骤3中减压浓缩温度为70~80°C,减压浓缩至原溶液体积的一半,重结晶用的丙酮体积为浓缩液的I倍,析晶温度为5~15°C,析晶时间为12~14小时。
[0014]作为本发明的改进,该步骤4中气流粉碎采用多级粉碎,超细粉体的颗粒直径为
0.5 ~3 μ m0
[0015]作为本发明的改进,该步骤4中气流粉碎采用二级对喷式气流粉碎,气流粉碎的气流速度为350~450m/s。
[0016]与现有技术相比,本发明的头孢美唑钠特种超细粉体制剂具有澄清度好、稳定性高、纯度高、杂质少、颗粒小、比表面积大、溶解性好的特点,避免了辅料的使用,减少了杂质,减少了毒副作用和过敏反应,增加了安全性。比表面积大,表面能也相应增加,使其具有较好的分散性和吸附性能。在配液时能够充分的溶解、迅速的溶解,可提高有效成分的利用率,降低药物消耗,增强药品疗效。随着粒度的变小,粒子的表面原子数成倍增加,使其具有较强的表面活性和催化性,更容易吸收,容易达到患病部位。可提高配液速度,降低在配液过程中产生有关杂质,提高药品质量。
[0017]下面结合具体实施例对本发明的实施方案作详细的说明。应当理解,本发明的实施并不局限于下面的实施例,对本发明所做的任何形式上的变通和/或改变都将落入本发明的保护范围。
[0018]实施例1
将头孢美唑苄酯30克加入到二氯甲烷150克中,降温至_30°C,以避免副反应的发生,然后加入苯甲醚330克、三氯化铁60克,在_30°C下进行反应,当头孢美唑苄酯残留≤1.0%时,视为反应结束,将反应液搅拌后加入到由8%盐酸溶液250ml (259克)、丙酮306ml (240克)组成的混合液中,搅拌30分钟后静置分层,收集有机相,将有机相倒入250ml浓度8%的氯化钠溶液中,搅拌静置分层,收集有机相。
[0019]在有机相中加入3%碳酸氢钠溶液,调节pH至7,搅拌20分钟后静置分层,收集水相,将水相用乙酸调节PH到5.5,再加入活性炭3克,搅拌脱色30分钟后过滤,在滤液中加入9克氧化铝,搅拌20分钟后过滤,滤液加入乙酸乙酯27克(30ml),滴加20%盐酸调节pH至2,搅拌30分钟后加入头孢美唑酸晶种0.18克,搅拌析晶4小时,过滤,晶体用二氯甲烷40ml洗涤,经真空干燥制得头孢美唑酸18.4克。
[0020]将9.4克(0.02mol)头孢美唑酸加入到141ml纯化水中,加入1.7克(0.02mol)碳酸氢钠使其完全溶解,反应制得头孢美唑钠。每次加入体积占水溶液体积40%的乙酸乙酯,萃取2次,充分搅拌后,静置分层,收集水相,向水相中加入浓度lmol/1的乙醇钠乙醇溶液20ml进行脱除杂质,脱除杂质温度为55°C,脱除时间为3小时,然后降温至室温,有沉淀析出,过滤后获得含水滤液。将所获得的头孢美唑钠水溶液升高至70°C进行减压浓缩,减压浓缩至原溶液的一半,然后向该水溶液中加入相同体积的丙酮,慢慢降温至5°C,进行重结晶,析出晶体,析晶时间为12小时,离心机离心甩滤,滤饼用丙酮洗涤,经真空干燥得高纯度的头孢美唑钠白色固体8.5 克,纯度为99.5%。
[0021]将干燥的高纯度头孢美唑钠用二级对喷式气流粉碎成超细粉体。头孢美唑钠结晶体通过加料斗,通过进料管线进入粗粉碎仓的喷枪,被喷枪的高速气流喷出在粗粉碎仓中进行对撞粉碎,通过循环管线进行反复循环对撞。达到一定粒度大小后,通过出料口进入细粉碎仓的喷枪,被喷枪的高速气流喷出在细粉碎仓中再次进行对撞粉碎,通过循环管线进行反复循环对撞,达到标准大小粒度后,通过产品回收管进入产品收集桶回收。通过控制气流速度,可以控制产品的粒径大小。控制粉碎气流速度为350m/s,得到超细粉体的颗粒直径为I~3 μ m,进行回收,包装,制得头孢美唑钠特种超细粉体制剂。
[0022]加速试验随机取实施例1制备的头孢美唑钠特种超细粉体制剂样品I批,将其批号命名为20120301,置于40°C且75%湿度避光环境中,分别于放置后第1、2、3、6个月取样考察,与O月考察数据进行比较,试验结果见表1。
[0023]该批样品在25°C且65%湿度避光环境中的长期试验结果见表2。
[0024]实施例2
将头孢美唑苄酯30克加入到二氯甲烷225克中,降温至_25°C,以避免副反应的发生,然后加入苯甲醚390克、三氯化铁75克,在_25°C下进行反应,当头孢美唑苄酯残留≤1.0%时,视为反应结束,将反应液搅拌后加入到由10%盐酸溶液220ml(230克)、丙酮344ml(270克)组成的混合液中,搅拌30分钟后静置分层,收集有机相,将有机相倒入250ml浓度10%的氯化钠溶液中,搅拌静置分层,收集有机相。
[0025]在有机相中加入5%碳酸氢钠溶液,调节pH至7.5,搅拌20分钟后静置分层,收集水相,将水相用乙酸调节PH到6,再加入活性炭6克,搅拌脱色30分钟后过滤,在滤液中加Λ 10.5克氧化铝,搅拌20分钟后过滤,滤液加入乙酸乙酯30克(33ml),滴加25%盐酸调节PH至1.5,搅拌30分钟后加入头孢美唑酸晶种0.21克,搅拌析晶5小时,过滤,晶体用二氯甲烷50ml洗涤,经真空干燥制得头孢美唑酸18.8克。
[0026]将9.4克(0.02mol)头孢美唑酸加入到188ml纯化水中,加入1.7克(0.02mol)碳酸氢钠使其完全溶解,反应制得头孢美唑钠。每次加入体积占水溶液体积35%的乙酸乙酯,萃取3次,充分搅拌后,静置分层,收集水相,向水相中加入浓度lmol/1的乙醇钠乙醇溶液25ml进行脱除杂质,脱除杂质温度为60°C,脱除时间为3小时,然后降温至室温,有沉淀析出,过滤后获得含水滤液。将所获得的头孢美唑钠水溶液升高至75°C进行减压浓缩,减压浓缩至原溶液的一半,然后向该水溶液中加入相同体积的丙酮,慢慢降温至10°C,进行重结晶,析出晶体,析晶时间为13小时,离心机离心甩滤,滤饼用丙酮洗涤,经真空干燥得高纯度的头孢美唑钠白色固体8.6克,纯度为99.6%。
[0027]将干燥的高纯度头孢美唑钠用二级对喷式气流粉碎成超细粉体。头孢美唑钠结晶体通过加料斗,通过进料管线进入粗粉碎仓的喷枪,被喷枪的高速气流喷出在粗粉碎仓中进行对撞粉碎,通过循环管线进行反复循环对撞。达到一定粒度大小后,通过出料口进入细粉碎仓的喷枪,被喷枪的高速气流喷出在细粉碎仓中再次进行对撞粉碎,通过循环管线进行反复循环对撞,达到标准大小粒度后,通过产品回收管进入产品收集桶回收。通过控制气流速度,可以控制产品的粒径大小。控制粉碎气流速度为400m/s,得到超细粉体的颗粒直径为0.8~1.5 μ m,进行回收,包装,制得头孢美唑钠特种超细粉体制剂。
[0028]加速试验随机取实施例2制备的头孢美唑钠特种超细粉体制剂样品I批,将其批号命名为20120302,置于40°C且75%湿度避光环境中,分别于放置后第1、2、3、6个月取样考察,与O月考察数据进行比较,试验结果见表1。
[0029]该批样品在25°C且65%湿度避光环境中的长期试验结果见表2。
[0030]实施例3
将头孢美唑苄酯30克加入到二氯甲烷300克中,降温至_20°C,以避免副反应的发生,然后加入苯甲醚450克、三氯化铁90克,在_20°C下进行反应,当头孢美唑苄酯残留 ≤1.0%时,视为反应结束,将反应液搅拌后加入到由12%盐酸溶液200ml(211克)、丙酮382ml(300克)组成的混合液中,搅拌30分钟后静置分层,收集有机相,将有机相倒入250ml浓度12%的氯化钠溶液中,搅拌静置分层,收集有机相。
[0031]在有机相中加入8%碳酸氢钠溶液,调节pH至8,搅拌20分钟后静置分层,收集水相,将水相用乙酸调节PH到6.5,再加入活性炭9克,搅拌脱色30分钟后过滤,在滤液中加入12克氧化铝,搅拌20分钟后过滤,滤液加入乙酸乙酯33克(37ml ),滴加30%盐酸调节pH至1,搅拌30分钟后加入头孢美唑酸晶种0.24克,搅拌析晶6小时,过滤,晶体用二氯甲烷60ml洗涤,经真空干燥制得头孢美唑酸18.6克。
[0032] 将9.4克(0.02mol)头孢美唑酸加入到236ml纯化水中,加入1.7克(0.02mol)碳酸氢钠使其完全溶解,反应制得头孢美唑钠。每次加入体积占水溶液体积30%的乙酸乙酯,萃取4次,充分搅拌后,静置分层,收集水相,向水相中加入浓度lmol/1的乙醇钠乙醇溶液30ml进行脱除杂质,脱除杂质温度为65°C,脱除时间为3小时,然后降温至室温,有沉淀析出,过滤后获得含水滤液。将所获得的头孢美唑钠水溶液升高至80°C进行减压浓缩,减压浓缩至原溶液的一半,然后向该水溶液中加入相同体积的丙酮,慢慢降温至15°C,进行重结晶,析出晶体,析晶时间为14小时,离心机离心甩滤,滤饼用丙酮洗涤,经真空干燥得高纯度的头孢美唑钠白色固体8.5克,纯度为99.5%。
[0033]将干燥的高纯度头孢美唑钠用二级对喷式气流粉碎成超细粉体。头孢美唑钠结晶体通过加料斗,通过进料管线进入粗粉碎仓的喷枪,被喷枪的高速气流喷出在粗粉碎仓中进行对撞粉碎,通过循环管线进行反复循环对撞。达到一定粒度大小后,通过出料口进入细粉碎仓的喷枪,被喷枪的高速气流喷出在细粉碎仓中再次进行对撞粉碎,通过循环管线进行反复循环对撞,达到标准大小粒度后,通过产品回收管进入产品收集桶回收。通过控制气流速度,可以控制产品的粒径大小。控制粉碎气流速度为450m/s,得到超细粉体的颗粒直径为0.5~1.2 μ m,进行回收,包装,制得头孢美唑钠特种超细粉体制剂。
[0034]加速试验随机取实施例3制备的头孢美唑钠特种超细粉体制剂样品I批,将其批号命名为20120303,置于40°C且75%湿度避光环境中,分别于放置后第1、2、3、6个月取样考察,与O月考察数据进行比较,试验结果见表1。
[0035]该批样品在25°C且65%湿度避光环境中的长期试验结果见表2。
[0036]表1
头孢美唑钠特种超细粉体制剂及其制备方法
- 专利详情
- 全文pdf
- 权力要求
- 说明书
- 法律状态
查看更多专利详情
下载专利文献
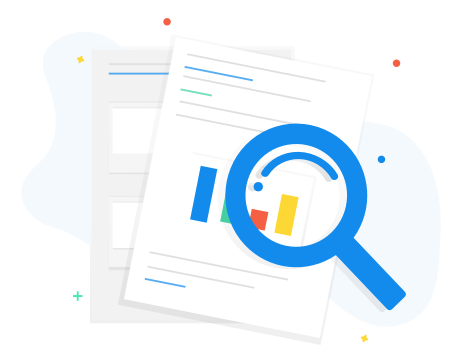
下载专利
同类推荐
-
徐立伽D·泰, G·塔尔博特张仁寿, 吴秀俊张仁寿, 吴秀俊
您可能感兴趣的专利
-
李琦, 杨磊李琦, 杨磊刘全胜刘全胜
专利相关信息
-
M.德希亚, Y.葛M.德希亚, Y.葛张光春