专利名称:一种生产粉末磷脂的新工艺的制作方法 提取制备粉末大豆磷脂所用溶剂为丙酮,公知技术已有诸多报道,如兽医大学学报.13(4)372~375.1993公布的“药用大豆卵磷脂的精制”。食品工业技术(7).18~23.1990公布的“新型高质量大豆磷脂的生产方法”,提出用乙醚-丙酮-水方法制备粉末大豆磷脂除去油,而乙醚-丙酮的分馏相对复杂。中国油脂.10(3).50~52.1991公布的“磷脂的溶剂法精致与分离”,提出用丙酮除油一次后再用水处理可以大幅度提高磷脂的收率,但再用丙酮萃取时除水则多了一个脱水工艺,再次用丙酮脱油时磷脂色泽深,丙酮用量并不减少。化学与粘合.(1).1991.36~40公布的“大豆磷脂的制备与应用”,用5℃丙酮提取粉末大豆磷脂,因为此时溶解度为0.003%,但在生产中必须建有冷库。中国油脂1985(5).40~47公布的“粉末大豆磷脂的制取工艺实验”;郑州粮食学院学报1991(2).1~8公布的“食用大豆磷脂的研制”,以丙酮做溶剂进行粉末大豆磷脂中试实验,除后者在搅拌萃取进口增加一个分料盘喷条装置及循环装置外,工艺的其它部分无大差异;二者均以大豆水化浓缩磷脂做原料,到目前,在我国以大豆水化浓缩磷脂做原料采用丙酮萃取工艺生产粉末磷脂已被厂家接受,但由于现在我国90%以上油脂厂采用加碱工艺,碱化或由其加工成的碱化乳状磷脂,或水化油脚制备的乳状磷脂厂家为降低酸值在其中加碱,采用以上工艺制成的乳状磷脂原料生产粉末磷脂极为困难,甘油及皂化的脂肪酸和正常磷脂混在一起烘干时不能形成粉末。利用碱化油脚生产粉末大豆磷脂是有待研究和市场前景广阔的新技术。本发明的发明人曾发明一种适合不同植物乳化磷脂原料的粉末磷脂生产法(中国专利申请号为200310105345.5),后来又发明了利用碱化乳状磷脂生产粉末磷脂的方法(中国专利申请号200410024223.8),利用碱化乳状磷脂生产粉末磷脂效果明显改善。但是由于生产的磷脂呈细小的粉末颗粒状,易结合成团或块,另外,生产过程采用的干燥方法为双锥干燥法,耗能多,加热抽真空干燥需要热能且时间较长,一个135L的双锥干燥一次处理最大产量为90Kg左右,产量大的厂家需同时上几个同样的设备,投资大,用人多,另外,产品成本高、色泽和质量欠佳。
本发明针对粉末磷脂生产存在的不足,提供一种可使粉末磷脂产品不会结合成团或块状,更节约热能,生产成本更低,产品质量更好的生产粉末磷脂的新工艺。本发明的目的可通过如下技术措施来实现先按照通常碱化乳状磷脂与丙酮的萃取配比将丙酮加入萃取器中,再于搅拌下加入乳状磷脂,搅拌萃取,静置,再将沉淀物用丙酮连续于搅拌下萃取至上清液大致无色澄明时,放出位于沉淀物上部的丙酮萃取液,然后再加入微量醋酸纤维素并搅拌溶解,待磷脂粉粒悬起后离心,自然干燥或真空干燥得粉末磷脂产品。本发明的目的还可通过如下技术措施来实现所述的醋酸纤维素为一醋酸纤维素或二醋酸纤维素或三醋酸纤维素,其中以二醋酸纤维素为最好;所述的微量醋酸纤维素是指醋酸纤维素∶干粉状磷脂=1∶1000~10000重量份;所述的真空干燥是在自然温度或低温下进行;所述的自然温度为35℃以下,所述的低温是指10~-30℃。本发明经离心后的磷脂可在室温状态下自然干燥或者自然温度下抽真空干燥并回收丙酮;或者在10~-30℃状态下抽真空回收丙酮;或者在高温天气阳光下晒干。本发明的加工助剂采用醋酸纤维素,无毒,溶于丙酮,具有很好的成膜性能,形成膜包裹粉状磷脂颗粒,适于在丙酮溶液中全方位包裹搅拌下悬浮的磷脂颗粒,在室温以下尤其低温下成膜更好,自然状态下裸露放置一年未发现颗粒吸潮粘结成团或块状,成膜有孔,更有利于磷脂的生物利用,可作为饲料添加剂,也可作为食品和饮料添加剂。本发明采用碱化油脚制作的碱化乳状磷脂为原料生产粉末磷脂,大大降低了生产成本,因为这之前的粉末磷脂生产的最后一步双锥干燥需在加热时抽真空干燥2~3小时。本工艺不需要加温,采用自然温度(或低温)且干燥时间很短,大大节约了能量,使碱化乳状磷脂生产粉末磷脂相对已有技术变的更容易,更有效,成本更低,且产品色泽和质量更好。
本发明采用的原料为碱化或水化的大豆油脚制备的乳状磷脂,提取溶剂为丙酮,先按照乳状磷脂∶丙酮=1∶10重量份的配比,将丙酮泵入搅拌萃取罐中,开启搅拌器(搅拌速度为80转/分钟左右),边搅拌边泵入乳状磷脂,连续搅拌0.5h。停止搅拌,静止分层。放出上层液体,第二、三、四、五次萃取所用丙酮量分别为乳状磷脂原料重量份的5、5、5、2倍,搅拌萃取时间与上述相同,沉淀。如果是新鲜的水化油脚经过离心,烘干即可成为粉末磷脂,但如果原料是碱化油脚生产的乳状磷脂或水化油脚加工的乳状磷脂,为防止酸值升高加了碱中和,或乳状磷脂搁置时间太久已经氧化产生了较多的脂肪酸等等,在后续的离心烘干过程中极难形成粉末。即便是再继续用高比例的丙酮萃取,离心烘干也不能形成粉末。不仅丙酮用量极大,回收负担大,消耗多,而且磷脂丢失多,提取量少,色泽差,磷脂发粘,产品内总有残余丙酮,价格低且产品寿命短,难以应用。
但如果在最后一次提取,放出大部分丙酮上清液后(使剩余丙酮液刚好没过磷脂沉淀为宜),向有丙酮液的磷脂沉淀内加入二醋酸纤维素或一醋酸纤维素或三醋酸纤维素,加入量为二醋酸纤维素或一醋酸纤维素或三醋酸纤维素∶粉末磷脂产品=1∶1000~10000;搅拌至二醋酸纤维素或一醋酸纤维素或三醋酸纤维素完全溶解于丙酮,并使其在磷脂粉末颗粒中分布均匀。搅拌下放入离心机,离心(1400转/分钟左右)5~10分,离心出的溶有二醋酸纤维素或一醋酸纤维素或三醋酸纤维素的丙酮液另存(与前几次的丙酮提取液分开),代替下次磷脂萃取时最后一次所用的丙酮液(经过蒸去丙酮知其中二醋酸纤维素或一醋酸纤维素或三醋酸纤维素的含量),循环使用。离心半干的磷脂可在室温下自然干燥,风干挥去丙酮,节约能量,但丢失少量丙酮。也可以采用磷脂生产厂已有的双锥干燥,自然温度下抽真空回收丙酮。
此工艺最适合已采用丙酮生产工艺的粉状磷脂生产厂,离心半干的磷脂采用10~-30℃低温状态下抽真空回收丙酮而干燥的方法,相对已有技术不仅节约丙酮,节约干燥能源,节约时间,粉状磷脂色泽好,质量高。本工艺也适于菜籽和花生磷脂的提取生产。
实施例2本发明采用原料为碱化的或水化的大豆油脚制备的乳状磷脂,生产过程同实施实例1,所不同的是在加入了二醋酸纤维素或一醋酸纤维素或三醋酸纤维素并经离心后,干燥采用10~-30℃低温状态下抽真空回收丙酮而干燥。这样得到的产品色泽和质量均很好。但低温生产的粉末磷脂应立即包装,易吸潮。本工艺也适于菜籽和花生乳状磷脂生产粉末磷脂的工艺。
实施例3本发明采用原料为碱化的或水化的大豆油脚制备的乳状磷脂,生产过程大部分同实施实例1,所不同的是在加入了二醋酸纤维素或一醋酸纤维素或三醋酸纤维素并经离心后,干燥也可采用室温以上的温度,在35℃左右阳光照射下自然干燥,效果也很好。如加热干燥应控制绝不可超过55℃,否则加有二醋酸纤维素或一醋酸纤维素或三醋酸纤维素的磷脂干燥时易焦化,色泽易变成棕黑,发粘,难成粉末。本工艺也适于菜籽和花生乳状磷脂生产粉末磷脂的工艺。
本发明提供一种利用大豆,花生或菜籽等不同植物的碱化油脚制作的碱化乳状磷脂为原料生产粉末磷脂的新工艺,先按照通常碱化乳状磷脂与丙酮的萃取配比将丙酮加入萃取器中,再于搅拌下加入乳状磷脂,搅拌萃取,静置,再将沉淀物用丙酮连续于搅拌下萃取至上清液大致无色澄明时,放出位于沉淀物上部的丙酮萃取液,然后再加入微量醋酸纤维素,搅拌溶解,待磷脂粉粒悬起后离心干燥得粉末磷脂。所述的醋酸纤维素为一醋酸纤维素或二醋酸纤维素或三醋酸纤维素;加入量为醋酸纤维素∶干粉状磷脂=1∶1000~10000重量份。
一种生产粉末磷脂的新工艺制作方法
- 专利详情
- 全文pdf
- 权力要求
- 说明书
- 法律状态
查看更多专利详情
下载专利文献
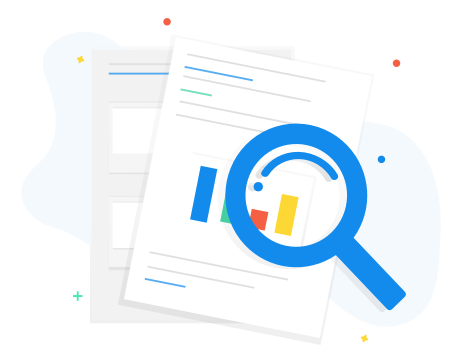
下载专利
同类推荐
-
张亚锋, 胡长坤张亚锋, 胡长坤杨雅婷刘代成崔桂玲
您可能感兴趣的专利
-
崔桂玲崔桂玲F.桑帕里斯, H.哈兰德F.桑帕里斯, H.哈兰德F.桑帕里斯, H.哈兰德
专利相关信息
-
A.L.邦奇, P.G.哈里斯A.L.邦奇, P.G.哈里斯A.L.邦奇, P.G.哈里斯A.L.邦奇, P.G.哈里斯陈春雷, 施绍安陈春雷, 施绍安王卫刚