专利名称:改进的过渡金属络合物催化反应方法本申请是1986年5月20日提交的美国专利申请No.865061的继续部分,后者是1984年12月28日提交的美国专利申请No.685025的继续,而No.685025又是1984年2月17日提交的美国专利申请No.581352的继续。本发明是关于增溶铑-亚磷酸盐络合物液态催化循环加氢醛化方法。使烯烃不饱和化合物与一氧化碳和氢在有增溶铑-亚磷酸盐配位体络合物催化剂存在的条件下进行反应,可以很容易地制取醛类产品,这一点已为公知。在这些方法中优先选用的类型包括连续加氢醛化及催化剂的再循环,如美国专利4599206中所描述的。尽管这类增溶铑-亚磷酸盐络合物液态催化循环加氢醛化方法带来一定的益处,但在一定的条件下,某些铑-亚磷酸盐络合物催化剂中的铑在加氢醛化过程中会以金属铑或铑原子团的形式从溶液中沉淀出来。观察表明,在液态循环工艺中的铑损失现象可能是由于在加氢醛化过程中、在缺少CO和H2混合气(合成气)或合成气浓度低于正常情况时对该络合物催化剂加热而引起的。这种情况可发生在从含增溶铑-亚磷酸盐络合物催化剂和醛产物溶液中蒸馏回收醛产品的液态循环加氢醛化过程中。这表明,蒸馏回收醛工序是造成铑损失的主要原因,尽管确切的沉淀点尚未被确定。现已被发现,在含有极性官能团的有机聚合物存在的条件下进行该方式的醛产物蒸馏回收可防止增溶铑-亚磷酸盐络合物液态催化循环加氢醛化过程中铑的沉淀,或将其减至最少,所说的官能团选自酰胺、酮、氨基甲酸酯、脲和碳酸盐。本发明的目的是提供一种改进的增溶铑-亚磷酸盐络合物液态催化循环作业方法,其中,通过使用本文所公开的含极性官能团的有机聚合物添加剂而防止络合物催化剂中的铑从溶液中沉淀出来或将其减至最少。本发明的其它目的和优点可从下述文字说明及权利要求1.一种防止铑-亚磷酸盐络合物催化剂中的铑从溶液中以金属铑或铑原子团的形式沉淀出来或将其减至最少的方法,这种沉淀发生于利用一氧化碳与烯不饱和化合物反应,并通过蒸馏生产醛产物的增溶铑-亚磷酸盐络合物液体催化循环加氢醛化过程中,该方法包括进行蒸馏以便将醛产物从含有增溶铑-亚磷酸盐络合催化剂和醛产物以及有机聚合物的反应产物溶液中分离出来,所说的有机聚合物含有极性官能团,该官能团选自酰胺、酮、氨基甲酸酯、脲和碳酸盐原子团。2.如权利要求1规定的方法,其中使用的有机聚合物添加剂的量以被蒸馏的反应溶液的总重量计为0.1~5.0%Wt。
3.如权利要求
2规定的方法,其中使用的有机聚合物添加剂的量以被蒸馏的反应溶液的总重量计为0.3~3.0%Wt。
4.如权利要求
2规定的方法,其中有机聚合物是聚乙烯吡咯烷酮或含乙烯吡咯烷酮的共聚物。
5.如权利要求
3规定的方法,其中有机聚合物是乙烯吡咯烷酮-乙烯基乙酸酯共聚物。
6.如权利要求
1规定的方法,其中所述的蒸馏温度为50℃~140℃。
7.如权利要求
1规定的方法,其中上述的有机聚合物存在于加氢醛化反应介质中并贯穿于整个液体再循环加氢醛化过程。
使用一种有机聚合物添加剂来防止铑—亚磷酸盐络合物催化剂中的铑在液体再循环加氢醛化过程期间从溶液中沉淀出来或将其减至最少。
改进的过渡金属络合物催化反应方法
-
专利名称改进的过渡金属络合物催化反应方法
-
发明者约翰·迈克尔·马尔, 戴维·罗伯特·布赖恩特
-
公开日1988年6月8日
-
申请日期
-
优先权日
-
申请人联合碳化公司导出引文BiBTeX, EndNote, RefMan
-
文档编号
-
关键字
-
权利要求中清楚地看出本发明可概括地描述为这样一种方法,它可被用来防止铑-亚磷酸盐络合物催化剂中的铑以金属铑或铑原子团的形式从溶液中沉淀出来,或者将其减至最少所说的铑沉淀现象发生在用烯烃不饱和化合物与CO和H2反应并通过蒸馏从含有增溶铑-亚磷酸盐络合物催化剂和醛产品的反应产物溶液中回收醛产物的、增溶铑-亚磷酸盐络合物液态催化循环加氢醛化过程中该方法包括从含有增溶铑-亚磷酸盐络合物催化剂、醛产物并添加有含极性官能团的有机聚合物的反应产物溶液中蒸馏醛产物,其中所说的官能团选自酰胺、酮、氨基甲酸酯、脲和碳酸盐本发明包括,通过在有本文所指定的含极性官能团的有机聚合物存在的条件下从含络合物催化剂和醛产物的反应产物溶液中蒸馏回收醛产物,来改善任何增溶铑-亚磷酸盐液态催化循环加氢醛化循环加氢醛化过程中铑的稳定性可能发生铑沉淀的增溶铑-亚磷酸盐络合物液态催化循环加氢醛化方法包括如美国专利4482749和4599206以及美国专利申请No.772859和No.772891(均是1985年9月5日提交的)及No.012329(1987年2月9日申请)中所描述的方法,在此提出上述文献以供参考通常,这种加氢醛化反应包括在有增溶铑-亚磷酸盐络合物催化剂存在的情况下,使烯烃不饱和化合物与CO和H2在液体介质中反应该介质还含有催化剂溶剂及游离亚磷酸盐配位体例如不与活性络合物催化剂中的金属铑络合的配位体这种循环工艺通常包括,从加氢醛化反应区连续或间歇地抽出部分含催化剂和醛产物的液体反应介质,于常压、减压或高压下在一分离的蒸馏区中一步或几步蒸馏该介质以回收醛产物及其它挥发物蒸汽,将含残留物的未挥发铑催化剂重新循环至反应区中挥发物的冷凝、分离及回收可用任何常规方式进行(如蒸馏法),如果需要,醛产物可继续加工作进一步提纯回收的反应剂如烯烃原料及合成气可以任何方式重新循环至反应区回收到的含残渣的未挥发铑催化剂在循环到反应区之前可经进一步处理,也可不经处理可以说,本发明的这些处理方法与迄今为止所知的处理方法相对应本发明所包括的、用于加氢醛化反应的铑-亚磷酸盐络合物催化剂包括上述专利及专利申请中所公开的催化剂如同参考文献所述,通常这种催化剂可予先制备也可现场生成它们基本上是由铑与有机亚磷酸盐配位体络合而成人们相信,CO也是存在的并与活性物中的铑络合活性催化物还可以含直接键合于铑的氢本发明所包括的用于加氢醛化反应的与铑催化剂络合的亚磷酸盐和/或游离亚磷酸盐的有机亚磷酸盐配位体可以是各种叔有机亚磷酸盐,诸如具有下述结构式的二有机亚磷酸盐 式中R1代表一个二价有机基团,W代表一个取代或未取代的一价烃基团Ⅰ式中R1所代表的典型二价基团包括二价无环基团或二价芳族基团典型的二价无环基团可以是亚烷基、亚烷基-氧基-亚烷基、亚烷基-NX-亚烷基,其中的X是氢或一价烃基、亚烷基-S-亚烷基、环亚烷基、以及在美国专利3415906和4567306中所给出的例子,以及在此引入的参考文献所公开的例子典型的二价芳族基团例如有亚芳基、二-亚芳基、亚芳基-亚烷基、亚芳基-亚烷基-亚芳基、亚芳基-氧基-亚芳基、亚芳基-氧基-亚烷基、亚芳基-NX-亚芳基和亚芳基-NX-亚烷基其中的X是氢或一价烃基、亚芳基-S-亚烷基、以及亚芳基-S-亚芳基等R′优先选用二价芳基团优先选用的叔二有机亚磷酸盐的代表是具有下述结构式的二有机亚磷酸盐 式中W是一个取代或未取代的一价烃基;Ar是一个取代或未取代的芳基,每个Ar可以相同也可不同;每个Y分别取值0或1;Q是选自-CR3R4-、-O-、-S-、-NR5-、SiR6R7-和-CO-的一个二价桥接基团,其中每个R3和R4独立地选自氢、具有1~12个碳原子的烷基、苯基、甲苯基和甲氧苯基,每个R5、R6和R7可独立地选自氢或甲基;n的值为0或1在美国专利No.4599206和美国专利申请No.865061(1986年5月20日申请)中对Ⅱ式所述的二有机亚磷酸盐作了较为详细的描述,在此引入作为参考优先选用的二有机亚磷酸盐中有下述结构式的二有机亚磷酸盐 式中Q是-CR1R2,每个R1和R2分别代表选自氢或烷基的基团;每个y分别取值0或1;n值为0到1;W代表一个未取代的或取代的一价烃基,它选自具有1~18个碳原子的烷基(诸如伯烷基、仲烷基和叔烷基,如甲基、乙基、正-丙基、丁基、仲-丁基、叔-丁基、叔-丁基乙基、叔-丁基丙基、正-己基、戊基、仲-戊基、叔-戊基、异-辛基、2-乙基己基、癸基、十八烷基等)以及象α-萘基、β-萘基这样的芳基和下述结构式的芳基 每个X1、X2、y1、y2、Z2、Z3和Z4分别表示由下组中选取的一个基氢、具有1~8个碳原子的烷基、取代或未取代的芳基、烷芳基、芳烷基和脂环族基团(如苯基、苄基、环己基、1-甲基环己基等)、羟基(-OH)以及象-OR8这样的醚(即含氧的)基,其中R8是含1~18个碳原子的烷基,在美国专利4599206的权项中及美国专利申请No.685061(1986年5月20日申请)中所公开的、具有上述式Ⅲ所述结构的那些二有机亚磷酸盐亦在优先选择之列典型的二有机亚磷酸盐还包括下列结构式所表示的例子式中t-Bu是叔丁基;Me是甲基还有一组可用于本发明所包括的加氢醛化反应的叔有机亚磷酸盐,它们是叔有机多亚磷酸盐这些亚磷酸盐可以含有两个或两个以上的三价磷原子,例如下面结构式的亚磷酸盐 式中W代表一个取代或未取代的m价烃基;R1与前面式Ⅰ中的规定相同;每个R任意地是一个取代或未取代的一价烃基;a和b的值为0~6,且a+b需满足条件a+b=2~6及m=a+b典型的叔有机多亚磷酸盐可包括如结构式Ⅴ、Ⅵ、Ⅶ所示的双亚磷酸盐 式中R1是如式Ⅰ所定义的二价有机基;W是一个取代或未取代的二价烃基; 式中每个R可任意地是一个取代或未取代的一价烃基;W是一个取代或未取代的二价烃基; 式中R1是如式Ⅰ所定义的二价有机基;每个R可任意地是一个取代或未取代的一价烃基;W是一个取代或未取代的二价烃基可用于本发明所述的加氢醛化反应的另一类叔有机双亚磷酸盐的代表是具有下述结构的双亚磷酸盐 式中每个Ar代表一个相同或不同的、取代或未取代的芳基;W代表一个由下组选取出的二价基亚烷基、亚烷基一氧基-亚烷基、亚芳基和亚芳基-(CH2)y-(Q)n-(CH2)y-亚芳基,其中每个亚芳基与前面规定的Ar相同,每个Q分别代表选自下组的一个二价桥接基团-CR3R4-、-O-、-S-、-NR5-、-SiR6R7和-CO-,其中每个R3和R4分别代表一个选自氢或烷基的基团,每个R5、R6和R7分别代表-H或-CH3;每个y和n分别地取0或1在美国专利4351759中以及分别于1985年9月5日和1987年2月9日提交的美国专利申请No.772859和12329中对此作了更为详细的描述,在此引入上述文献作为参考另一类可用于本发明所述的加氢醛化反应的叔有机双亚磷酸盐的代表具有下述结构式; 式中每个Ar代表一个相同或不同的、取代或未取代的芳基;W代表一个选自亚烷基、亚芳基和-亚芳基-(CH2)y-(Q)n-(CH2)y-亚芳基-的二价基团,其中的亚芳基与上面规定的Ar相同;每个Q分别代表从-CR3R4-、-O-、-S-、-NR5-、-SiR6R7-和-CO-中选取的一个二价桥接基团,其中的R3和R4分别代表一个选自氢或烷基的基团,R5、R6和R7分别代表-H或-CH3;每个y和n分别取值0或1;每个R分别代表一个取代或未取代的一价烃基如烷基、芳基、芳烷基、烷芳基和脂环族基在美国专利申请No.772891(1985年9月5日提交)中对式Ⅸ型双亚磷酸盐作了更为详细的描述,在此引入作为参考可用于本发明所述的加氢醛化反应的另一类叔有机亚磷酸盐是具有下述结构式的叔单-有机亚磷酸盐 式中Z5代表一个三价有机基,这一点在美国专利4567306中有更为详细的描述,在此引入作为参考最后还有一组可用于本发明所述的加氢醛化反应的叔有机亚磷酸盐,它们包括三有机亚磷酸盐,诸如三(邻-苯基)苯基亚磷酸盐、三(邻-甲基)苯基亚磷酸盐、三(邻-叔-丁基)苯基亚磷酸盐等如上所述,在本发明所述的加氢醛化反应中可用来作为铑-亚磷酸盐络合物催化剂的亚磷酸盐配位体和/或作为游离亚磷酸盐配位体(在整个醛化过程中存在于反应介质和液体溶液中)的亚磷酸盐配位体可以是选自一有机亚磷酸盐、二有机亚磷酸盐、三有机亚磷酸盐和有机多亚磷酸盐本发明所述的加氢醛化方法可以在任何所需要的过量游离亚磷酸盐配位体的条件下进行,例如从至少1摩尔游离亚磷酸盐配位体/每摩尔铑到100摩尔游离亚磷酸盐配位体/每摩尔铑(存在于反应介质中),如果需要还可以更高通常,对于多数情况下合适的亚磷酸盐配位体的量为4摩尔~50摩尔/每摩尔铑,所说的量是指络合的与游离的亚磷酸盐配位体的总和当然,如果需要的话,为维持反应介质中游离配位体的预定含量;可以任何适宜的方式随时向反应介质中供入补偿的亚磷酸盐配位体此外还需清楚地认识到尽管在一给定的工艺阶段中,铑-亚磷酸盐络合物催化剂中的亚磷酸盐配位体与游离的亚磷酸盐配位体通常是相同的,但如果需要,在任何工艺阶段亦可使用不同的配位体或使用两种或两种以上不同亚磷酸盐配位体的混合物在本发明所述的一个确定的醛化工艺过程中,存在于反应介质中的铑-亚磷酸盐络合物催化剂的量只需是为提供必要的铑浓度所需要的最低量,这就为催化某个特定的醛化阶段所需之铑量提供了一个基础,正如前述专利及申请文件中的例子所公开的通常,对大多数工艺过程,若以游离的铑来计算,醛化反应介质中铑的浓度范围在10ppm~1000ppm就足够了,优先选用的范围为10ppm~500ppm,最好是25ppm~350ppm本发明所述的加氢醛化反应所用的烯属原料反应剂可以是末端不饱和或内部不饱和的,可以是直链、支链或环状结构,如同上述专利和申请中公开的那样这些烯烃可以含2~2.0个碳原子,可以含有一个或一个以上的烯不饱和基此外,这些烯烃可以含有对加氢醛化过程基本上无妨碍作用的基或取代基,诸如羟基、羰氧基、氧基、羰基、氧羰基、卤素、烷氧基、芳基、烷基、卤代烷基等典型的烯不饱和化合物包括α烯烃、内烯烃、烷基、链烯酸酯、链烯基链烷酸酯、链烯基烷基醚、链烯醇等,例如乙烯、丙烯、1-丁烯、1-戊烯、1-己烯、1-辛烯、1-癸烯、1-十二烯、1-十八烯、2-丁烯、异丁烯、2-甲基丁烯、2-己烯、3-己烯、2-庚烯、环己烯、丙烯二聚物、丙聚三聚物、丙聚四聚物、2-乙基-1-己烯、苯乙烯、3-苯基-1-丙烯、1,4-己二烯、1,7-辛二烯、3-环己基-1-丁烯、烯丙醇、己-1-烯-4-醇、辛-1-烯-4-醇、乙烯基乙酸盐、烯丙基乙酸盐、3-丁烯基乙酸盐、乙烯基丙酸盐、烯丙基丙酸盐、烯丙基丁酸盐、异丁烯酸甲酯、3-丁烯基乙酸盐、乙烯基乙基醚、乙烯基甲基醚、烯丙基乙基醚、正-丙基-7-辛烯酸酯、3-丁烯腈、5-己烯酰胺等当然,如果需要也可使用不同烯烃原料的混合物优先选用的烯不饱和原料是含2~20碳原子的α烯烃和含4~20个碳原子的内烯烃以及它们的混合物如同前述,本发明所述的加氢醛化反应也可在有有机溶剂(用于铑-亚磷酸盐络合物催化剂)存在的情况下进行任何对所进行的醛化过程没有过分妨碍的溶剂都可以被使用典型的溶剂包括上述专利及申请中所公开的那些溶剂当然,如果需要可以使用一种或多种不同溶剂的混合物优先选用的溶剂应当是本发明所述的烯属原料、催化剂及有机聚合物添加剂均可溶于其中(基本上都溶解)的溶剂最好使用对应的所要制取的醛产物的醛化合物和/或高沸点醛液体冷凝付产品作为初始溶剂,例如在加氢醛化过程中现场产生的高沸点醛液体冷凝付产品尽管在连续工艺过程的开始;人们可以使用任何适宜的溶剂,但由于该过程的本质,初始溶剂最终仍会变成既含醛产物又含高沸点醛液态冷凝付产物如果需要,也可予先制备这些醛冷凝付产物然后使用当然,溶剂的用量对本发明并不是关键的对于一给定的工艺,其用量只需向反应介质提供该过程所需的一定浓度的铑就足够了通常,以反应介质总重量计算,溶剂的使用量为5%~95%(Wt)本发明所述的加氢醛化工艺所使用的反应条件包括迄今为至在上述专利和申请中公开的、任何适宜的连续液体催化剂循环加氢醛化工艺的工艺条件,例如,该工艺中氢、一氧化碳和烯不饱和化合物原料的气体总压力为1~10000磅/吋2,但通常优先选用<1500磅/吋2的压力,最好是大约<500磅/吋2最小总压力主要由获得必需的反应速率所要求的反应剂数量来决定更具体地说,一氧化碳的分压取1~120磅/吋2较好,最好是3~90磅/吋2;氢分压取15~160磅/吋2较好,最好为30~100磅/吋2通常,气态氢与一氧化碳的摩尔比(H2∶CO)为1∶10~100∶1或更高,优选的范围是1∶1~10∶1另外,加氢醛化过程可以在45℃~150℃下进行一般情况下,对所有类型的烯原料优先选用的反应温度范围为50℃~120℃,因为在显著高于120℃的反应温度下进行反应看不到任何明显的好处,这可能是由于催化剂活性下降所致,正如美国专利4599206中所述的那样此外,本发明所述的增溶铑-亚磷酸盐络合物催化连续加氢醛化工艺包括一液态催化剂循环工序,如同上述专利及申请中所公开的那样既然任何常规催化剂循环工序都可以为本发明所使用,因此,在此就不作详述一般地讲,在这类液体催化剂循环工序中共同的作法是连续地从反应器中抽取部分液体反应产物介质送至蒸馏区如汽化器/分离器中,该介质中含有诸如醛产物、铑-亚磷酸盐络合催化剂、游离配位体、有机溶剂和加氢醛化过程中当场产生的付产品如醛冷凝付产物等,以及溶解在该反应介质中的未反应的烯烃原料、一氧化碳和氢(合成气)在蒸馏区中根据需要在常压、减压或增压下一步或分几步将所需要的醛产物从液体介质中蒸馏出来然后用前述的任何常规方法对其进行冷凝回收余下的未挥发液体残留物含有铑-亚磷酸盐络合催化剂、溶剂、游离配位体,通常还含有一些未蒸馏的醛产物该液体残留物随后以任何常规方法经过或不经过进一步处理,与可能还存在的溶于该残留物中的未挥发气体反应剂及付产物一起重新循环到反应器中,如同上述专利及申请中所述的那样此外,如需要也可将从汽化器中蒸馏出的气体反应剂重新循环至反应器从产物溶液中蒸馏分离所希望的醛产物可以在任何适宜的温度下进行一般应在低温如<150℃下进行,<140℃时较好,最好是50℃~130℃醛的蒸馏应在减压下进行,如当涉及的是低沸点醛类(如C4~C6),则总压力要大大低于在反应过程中所使用的总压力,当涉及的是高沸点醛类(如C7或更高),则应在真空下进行作为一个例子,通常的作法是将由反应器中抽出的液体反应产物介质置于减压条件下,以使溶解于该介质中的绝大部分未反应气体挥发,然后将气体和含合成气体的液体介质(其合成气体的浓度远低于反应介质中的浓度)送至蒸馏区,例如汽化器/分离器,在此蒸馏所需的醛产物对多数目(碳原子)的醛来说,蒸馏压力为真空压力(或更低)~50磅/吋2(总压)如上所述,本发明可归结于这样一个发现在含极性官能团的有机聚合物存在的条件下进行从含铑-亚磷酸盐催化剂的产物溶液中蒸馏所希望的醛产物可防止本文所述的铑沉淀,或将其可能性减至最小,其中所说的官能团选自酰胺(即任意 或 基团,不管是否进一步取代)、酮(即任意的 基团,不管是否进一步取代)、甲氨酸盐(即 或 基团,不管是否进一步取代)、脲(即任意的 基团,不管是否进一步取代)和碳酸盐(即 基团,不管是否进一步取代)基团本发明所用的、添加于从中蒸馏所需醛产物的含铑催化剂的产物溶液中的有机聚合物添加剂,如同其制备方法一样均为人们所熟知,通常可以从商业渠道买到任何含有所述官能团的有机聚合物,包括均聚物、共聚物、三元共聚物和低聚物都可使用此外还应认识到,这些极性官能团可以作为侧接于(stemming off)聚合物骨架的取代基和/或作为结合到聚合物骨架并构成其一部分的基而存在于有机化合物中所说的极性官能团可以具有非环状性质或是环状基的一部分当然,有机化合物可以只含一种类型的极性官能团,也可含两种或两种以上不同的极性官能团本发明所用的含这类极性官能团的典型有机化合物包括聚乙烯吡咯烷酮、乙烯基吡咯烷酮-乙烯基乙酸盐的共聚物、聚丙烯酰胺、乙烯基吡咯烷酮和β-二甲基氨基乙基异丁烯酸盐的共聚物、氨基甲酸、N-〔聚亚甲基(聚苯基)〕甲酯、N-〔聚亚甲基(聚苯基)〕N′-二异丙基脲、乙烯基吡咯烷酮和长链α烯烃的共聚物、乙烯基吡咯烷酮和苯乙烯的共聚物、聚丙烯酸酰肼、聚-N-乙烯基-5-甲恶唑烷酮(methoxazolidone)、多肽例如聚-L-吡咯啉和聚-L-苯基丙氨酸等这些有机聚合物的平均分子量不一定要限制得范围很窄,其范围可以是400~10000000或更高聚合物中极性官能团的数量也不一定要限制得范围很窄本发明优先选用的有机聚合物是至少含有三个极性官能团的,特别是酰胺官能团的有机聚合物由于乙烯基吡咯烷酮-乙烯基乙酸盐共聚物在含铑催化剂的加氢醛化溶液中具有良好的溶解性,故被首先选用本发明所述工艺中所采用的这类有机聚合物添加剂,其数量可通过在同一条件下对同一工艺进行操作来确定,以维持铑损失量最少为标准(维持铑损失量最少所需要的最少量)对于大多数目的来说,以反应产物溶液的总重量计算有机聚合物添加剂的量为0.01~10%(Wt),如果需要还可以更高当然,随着醛产物不断从产物溶液中蒸馏出去,溶液中的未挥发组分(如催化剂和有机聚合物添加剂)的浓度相应地将会增加,因此,本发明中使用的有机聚合物添加剂数量的上限主要根据该有机聚合物在蒸馏分离出所需数量的醛产物后所余下的、含未挥发的液体铑催化剂的残留物中的溶解度极限来决定当然,有机聚合物添加剂的量还分别取决于所用的特定铑催化剂、回收醛产物的蒸馏温度以及特定的有机聚合物添加剂本身通常,以所蒸馏的醛化反应产物总重量计算,有机聚合物添加剂的用量为0.1~5.0%(Wt),最好为0.3~3.0%(Wt)使用数量如此低的有机聚合物添加剂就可防止铑从溶液中沉淀或将其减至最少,这是本发明的另一个重要的优点,因为如此少量的添加剂远不会像使用大量添加剂那样对铑催化剂组合物和/或加氢醛化过程造成过分有害的影响例如,在连续的不带有催化剂循环的铑-亚磷酸盐络合物催化丁烯-2加氢醛化实验中,于介质中少量的聚乙烯吡咯烷酮和乙烯基吡咯烷酮-乙烯基乙酸盐共聚物的存在,与没有这种聚合物存在的情况相比,基本不影响反应速度,也不影响获得的醛产物异构物的比例在另一个对异丁烯加氢醛化的试验中(没有催化剂再循环),聚乙烯吡咯烷酮的存在加速了反应的速度;而在又一个丁烯-2加氢醛化试验中,没有催化剂再循环并使用下述定义的配位体A,添加乙烯吡咯烷酮-乙烯基乙酸盐共聚物可改善配位体的稳定性此外,本发明中使用的有机聚合物添加剂是高度不挥发性的,因此在醛产物精炼中不存在污染问题本发明所用的添加于从中蒸馏醛产物的反应产物溶液中的有机聚合物添加剂,可以任何合适的方法来添加,如可将有机聚合物添加剂在产物溶液由反应器中取出后,于蒸馏前或蒸馏期间加入如果需要,也可从蒸馏后的含未挥发液态铑催化剂的残余物中将其除去(例如在该残余物再循环之前或期间),以保证反应器中的反应介质中没有这样的有机聚合物添加剂存在无论怎样,既然认为这样的有机聚合物添加剂通常对加氢醛化反应本身没有任何显著的有害影响,一般均选择直接将有机聚合物添加剂加到反应介质中,并允许其在整个循环过程均存在于溶液中事实上,如果人们有理由认为前所讨论的铑沉淀肯定会在液体催化剂再循环加氢醛化过程中出现,则可希望将有机聚合物添加剂添加到所采用的起始催化剂母液中,使这样的有机聚合物添加剂从醛化过程之开始就存在当然,亦应认识到,由于为获得最佳效果和效率,本发明的最佳化选择取决于人们在应用本发明过程中所具有的经验,因此,一定数量的试验是必要的,以便确定在给定情况下的最佳条件,这一点对普通技术人员是熟知的,且按照下面所阐明的最佳方式和/或按照简单的常规实验是很容易实现的在此,申请人建议了一个快速实验工艺,用以证实在包括有铑-亚磷酸盐络合物催化剂的使用及所需醛产物的蒸馏回收阶段的连续液体再循环加氢醛化过程中,有机聚合物添加剂阻止或减少铑损失(从溶液中沉淀出来)的潜在效果该方法被概括于下面的例子中它包括将增溶活化的铑-亚磷酸盐络合物催化剂置于此醛产物蒸馏阶段更苛刻的条件下,以便在更短并易于控制的时间内获得有意义的结果例如,在正常的醛蒸馏回收工艺中,对铑损失进行定量的确定可能花费几天,因为铑损失率在正常情况下不大于百分之几/每天申请人的加速铑损失实验是在没有一氧化碳和氢(合成气)共同存在的条件下,通过将催化剂溶液置于醛蒸馏的温度下维持一较长的时间,而在几个小时内完成此外,还应认识到,在较高温度下进行实验和/或采用铑黑的实验(已观检到有促进铑沉淀的现象)被认为是比其它实验更苛刻的实验下面的例子是说明本发明的而不是限制此外在实施例中使用符号和条件如下Texanol2,2,4-三甲基-1,3-戊二醇单异丁酸酯t-Bu叔丁基原子团Me 甲基团配位体A一种有机亚磷酸盐,结构式为 配位体B一种有机亚磷酸盐,结构式为 配位体C一种有机亚磷酸盐,结构式为 配位体D一种有机亚磷酸盐,结构式为 配位体E一种有机亚磷酸盐,结构式为 配位体F一种有机亚磷酸盐,结构式为 配位体G一种有机亚磷酸盐,结构式为 配位体H一种有机亚磷酸盐,结构式为 配位体I一种有机亚磷酸盐,结构式为 配位体J一种有机亚磷酸盐,结构式为 配位体K一种有机亚磷酸盐,结构式为 配位体L一种有机亚磷酸盐,结构式为 %铑损失=滤过液中的铑量除以起始溶液中的铑量乘100实施例1将20毫升含一种亚磷酸盐配位体和浓度为250ppm的铑溶液(以Rh4(CO)12的形式溶于Texanol 溶剂中)的金属络合物催化剂起始溶液,在氮气保护下注入装有磁搅拌棒的充满氮气的三盎司玻璃气溶胶罐中如使用,可添加铑黑将一根充满氮气的导管连到罐上用合成气(CO/H2=1∶1,摩尔比)将该系统充到压力为60磅/英吋2,并重复排充气五次(最终罐内仍为60磅/英吋2的CO/H2=1∶1的合成气)将罐置于指定温度下的油槽中搅拌1小时使催化剂活化,随后排出CO/H2合成气,并充入10磅/英吋2的氢气或60磅/英吋2的氮气,排气五次并最终充入10磅/英吋2的氢气或60磅/英吋2的氮气在指定的温度下搅拌20小时,随后用压力吸管取出一个试样,并通过Millipore 5微米型LS过滤器(Waters有限公司)过滤,用原子吸收光谱方法分析铑含量结果如下表所示(各试样操作均相同)表Ⅰ序号配位体配位体/铑a温度铑黑b气体铑损失℃1 A 10 120 有 H291.72 A 10 120 无 H2703 B 10 120 无 H2704 C 10 120 无 H2605 J 10 120 无 H2646 D 10 120 无 H2777 E 15 130 有 N2968 E 10 130 无 N2419 F 10 130 无 N26310 F 10 130 有 N26911 G 10 130 有 N28412 H 10 130 有 N29413 I 10 130 有 N289a配位体的摩尔当量/每摩尔铑b使用时为50毫克铑黑上述实验证明在120℃和130℃下从溶液中沉淀出来大量的铑实施例2将20毫升含10摩尔当量/每摩尔铑的亚磷酸盐配位体(在此为E)和浓度为250ppm的铑溶液(以Rh4(CO)12的形式溶于Texanol 中)的金属络合物催化剂起始溶液,在氮气保护下注入一个充满氮气的3盎司玻璃气溶胶罐中,该罐装有磁搅拌棒添加50毫克铑黑和一种指定的有机聚合物将一根充满氮气的导管连到该罐上,然后用合成气(CO/H2=1∶1,摩尔比)将该系统充到60磅/英吋2的压力,并排充气5次(如实施例1)将该罐放入130℃的油槽中搅拌1小时使催化剂活化,随后排出CO/H2合成气,并用氮气给罐充气至60磅/英吋2的压力排气5次,使最终罐内仍保持60磅/英吋2的氮气在130℃下搅拌20小时,随后用压力吸管取出试样,用Millipore 5微米型LS过滤器(Waters有限公司)过滤,用原子吸收光谱法分析铑含量结果如下表所示(各试验操作均相同)表Ⅱ序号 配位体 有机聚合物添加剂 使用的有 铑损失机聚合物(平均分子量) 重量% %1 E PMVK 1.0 02 E PVP(40000) 0.1 03 E PVP(40000) 0.25 04 E PVP(40000) 0.5 05 E PVP(40000) 1.0 06 E PVP(10000) 1.0 07 E PVPVA(30%乙烯吡咯烷酮) 1.0 138 E PVPVA(50%乙烯吡咯烷酮) 1.0 09 E PVPVA(60%乙烯吡咯烷酮) 0.5 010 E PVPVA(70%乙烯吡咯烷酮) 1.0 011 E PAA(5000000~6000000) 1.0 012 E GAFQUAT 755(1000000) 1.0 013 E GAFQUAT 734(100000) 1.0 014 E GANEX V220(8600) 1.0 9915 E GANEX V220(8600) 5.0 3316 E GANEX V216(7300) 1.0 2117 E PM(pp)MC(400) 1.0 018 E PM(pp)DMU(470) 1.0 519 E POLECTRON 430 1.0 020 E PLP(1000~10000) 0.5 021 E PLPA(2000~5000) 0.5 023 E NCHP 0.5 94PMVK=聚甲基乙烯基酮(Aldrich化学公司销售)PVP=聚乙烯吡咯烷酮(序号2-5,特级,Aldrich化学公司销售,序号6,PVPK-15 GAF有限公司销售)PVPVA=乙烯吡咯烷酮-乙烯基乙酸酯聚合物(序号7,E-335,序号8,I-535,序号9,S-630,序号10,E-735,均为GAF有限公司销售)PAA=聚丙烯酰胺(Aldrich化学公司销售)GAFQUAT 755=乙烯吡咯烷酮和β-二甲胺乙基异丁烯酸酯的共聚物(GAF有限公司)PM(pp)MC=氨基甲酸,N-〔聚亚甲基(聚苯)〕-甲酯PM(pp)DMU=N-〔聚亚甲基(聚苯)〕N′-二异丙基脲NCHP=N-环己基吡咯烷酮单体GAFQUAT 734=乙烯吡咯烷酮和β-二甲胺乙基异丁烯酸酯的共聚物,20%的水溶液(GAF有限公司销售)GANEX V220=乙烯吡咯烷酮和长链α烯烃的共聚物(GAF有限公司销售)GANEX V216=乙烯吡咯烷酮和长链α烯烃的共聚物(GAF有限公司销售)Polectron 430=乙烯吡咯烷酮和苯乙烯的共聚物(GAF有限公司销售;使用前烘干)PLP=聚-L-脯氨酸(Sigma有限公司销售)PLPA=聚-L-苯基丙氨酸(Sigma有限公司销售)上述实验1到21(除去实验14)证明本发明包含的有机聚合物添加剂,在130℃下对防止铑由溶液中沉淀是很有效的,而在实验23中的有机单体添加剂是无效的看来实验14表明长链烷基原子团对极性功能酰胺氮的取代影响聚合物防止铑损失的能力,尽管增加聚合物的量(实验15)改进了它的性能实施例3在每个实验中,将20毫升含一种指定的亚磷酸盐配位体(10摩尔当量配位体/每摩尔铑)和溶度为250ppm的铑溶液(以Rh4(CO)12的形式溶于Texanol 中)的金属络合物催化剂起始溶液,在氮气保护下注入装有磁搅拌棒的充满氮气的三盎司玻璃气溶胶罐中如果使用铑黑,则应添加指定的(PVP)聚乙烯吡咯烷酮(平均分子量10000的PVP K-15,GAF有限公司)或(PVPVA)乙烯吡咯烷酮-乙烯基乙酸酯共聚物(60%乙烯吡咯烷酮,S-630,GAF有限公司)将一根充满氮气的导管连到罐上该系统充入60磅/英吋2压力的合成气(CO/H2=1∶1,摩尔比)并排充气5次(最终罐中为60磅/英吋2压力的合成气)将罐放进指定温度的油槽中搅拌1小时使催化剂活化,随后排出合成气并充入10磅/英吋2压力的氢或60磅/英吋2压力的氮,排气5次,最终使罐内含10磅/英吋2压力的氢或60磅/英吋2压力的氮在指定温度下搅拌20小时,随后用压力吸管取出一个试样,用Millipore 5微米型LS过滤器(Waters有限公司)过滤,并用原子吸收光谱法测定铑含量,结果示于表3表3序号配位体有机聚合使用的有温度铑黑b气体铑损失机聚合物 %物添加剂 重量%1 A PVPVA 0.1 115 无 H202 A PVPVA 0.2 115 无 H203 A PVPVA 0.5 115 无 H204 A PVPVA 1.0 120 无 H205 A PVPVA 1.0 110 无 H206 A PVPVA 1.0 130 无 H20-37 A PVPVA 1.0 140 无 H268 A PVP 0.1 120 无 H249 A PVP 0.2 120 无 H2410 A PVP 0.5 120 无 H2011 A PVP 1.0 120 无 H2012 A PVPVA 1.0 120 有 H2013 E PVP 1.0 130 无 N2014 E PVP 1.0 120 有 N2015 E PVPVA 1.0 130 有 N2016 F PVP 1.0 130 有 N2017 H PVP 1.0 130 有 N2018 K PVP 1.0 130 有 N22819 I PVP 1.0 130 有 N2020 L PVPVA 1.0 120 无 H2021 B PVPVA 1.0 120 无 H23b当使用时为50毫克铑黑上述实验证明本发明包括的PVP和PVPVA有机聚合物添加剂可有效地阻止铑从溶液中沉淀出来或将其限制到最少,该溶液使用各种二有机亚磷酸盐配位体实施例4用作比较,重复实施例2并用下边指定的有机添加剂代替实施例2中的,结果如下表表4序号 配位体 有机聚合物添加剂 有机聚合物添 铑损失加剂重量% %1 E 无 - 932 E PMMA 1.0 763 E PVA 1.0 764 E PAN 1.0 955 E PS 1.0 906 E Gantrez ES-225 1.0 627 E Gantrez ES-335 1.0 608 E Gantrez AN-8194 1.0 869 E PVPY 1.0 91PMMA=聚甲基丙烯酸甲酯(Aldrich化学公司销售)PVA=聚乙烯醇(Aldrich化学公司销售)PAN=聚丙烯腈(Aldrich化学公司销售)PS=聚苯乙烯(Aldrich化学公司销售)Gantrez ES-225=甲基·乙烯基醚马来酐共聚物的-乙基酯(GAF有限公司销售)Gantrez ES-335=甲基·乙烯基醚-马来酐共聚物的一异丙酯(GAF公司销售)Gantrez AN-8194=十八烷基·乙烯基醚/马来酐共聚物(GAF有限公司销售)PVPY=聚乙烯吡啶(Aldrich化学公司销售)上述实验证明本发明不包括的有机聚合物添加剂对防止铑从溶液中沉淀是无效的实施例5作为比较,重复表3中的11号试验,使用下面指定的有机聚合物添加剂代替聚乙烯吡咯烷酮结果如下所示表5序号 配位体 温度℃ 有机聚合物添加剂 铑损失%1 A 120 PS 412 A 120 PMVE 70PS=聚苯乙烯(Aldrich化学公司销售)PMVE=聚甲基·乙烯基醚(Aldrich化学公司销售)上述实验证明本发明不包括的有机聚合物添加剂对防止铑从溶液中沉淀是无效的实施例6在每个试验中,将20毫升含亚磷酸盐配位体(这里是指配位体A)(10摩尔当量/每摩尔铑)和不同浓度的铑(以Rh4(CO)12的形式溶于Texanol 中)溶液的金属络合物催化剂初始溶液,在氮气气氛下注入装有磁搅拌棒的充满氮气的三盎司玻璃气溶胶罐中,然后添加铑黑(如果使用),和约1.0%(Wt)的聚乙烯吡咯烷酮(平均分子量10000的PVP K-15,GAF有限公司)或乙烯吡咯烷酮-乙烯基乙酸酯共聚物(60%的乙烯吡咯烷酮,S-630,GAF有限公司)将一根充满氮气的导管连到罐上该系统充入60磅/英吋2压力的合成气体(CO/H2=1∶1,摩尔比)并排充5次(最终罐内为合成气,60磅/英吋2)将罐放入120℃油槽中搅拌1小时使催化剂活化,随后排出合成气并充入10磅/英吋2压力的氢,排气5次(最终罐内为10磅/英吋2压力的氢)在120℃下搅拌20小时,随后用压力吸管取出试样用Millipore 5微米型LS过滤器(Waters有限公司)过滤,并用原子吸收光谱法分析铑含量,结果如下表6序号 配位体 有机聚合物添加剂 铑(ppm) 铑损失%1 A PVPVA 500 62 A PVPVA 1000 33 A PVP 500 04 A PVP 1000 0上述实验证明,使用的有机聚合物添加剂在高浓度铑情况下对防止铑的损失仍是有效的实施例7在每个实验中,将20毫升含1.3%(Wt)的亚磷酸盐配位体(A)和浓度不同的铑溶液(以Rh4(CO)12的形式溶于Texanol 中)的金属络合物催化剂初始溶液,在氮气下注入装有磁搅拌棒的充满氮气的三盎司玻璃气溶胶罐中然后添加指定量的聚乙烯吡咯烷酮(平均分子量10000的PVP K-15,GAF有限公司)或乙烯吡咯烷酮-乙烯基乙酸酯共聚物(60%的乙烯吡咯烷酮,S-630,GAF有限公司)将一根充满氮气的导管连到罐上该系统充入60磅/英吋2压力的合成气(CO/H2=1∶1,摩尔比),并排充气5次(最终罐内为60磅/英吋2压力的合成气)将罐置于指定温度的油槽中搅拌1小时使催化剂活化随后排出CO/H2气,并充入10磅/英吋2压力的氢气,排气5次(最终罐内为10磅/英吋2压力的氢)在指定温度下搅拌20小时,随后用压力吸管取出试样用Millipore 5微米型LS过滤器(Waters有限公司)过滤,并用原子吸收光谱法分析铑含量,结果示于表7表7序号 配位体 有机聚合物 使用的有机聚 铑 铑损失添加剂 合物重量% ppm %1 A PVP 1.0 577 02 A PVP 1.0 853 03 A PVP 1.0 1040 04 A PVPVA 1.0 484 05 A PVPVA 1.0 717 06 A PVPVA 1.0 907 37 A PVPVA 2.0 371 08 A PVPVA 2.0 634 09 A PVPVA 2.0 786 0上述实验证明当配位体浓度恒定,铑浓度增加时,使用的有机聚合物添加剂对防止铑损失是有效的实施例8用美国专利4599206中例10所述的方法及一种增溶铑-二亚磷酸盐络合物催化剂,对丁烯-1和丁烯-2的混合物进行为期23天的连续加氢醛化处理,其中使用的配位体是配位体E,蒸馏器温度110℃,观察到有铑损失发生在第24天,添加0.25%(Wt)的聚乙烯吡咯烷酮(平均分子量10000的PVP K-15,GAF有限公司)到反应器2中(以水溶液的形式)在110℃下,其后两天的醛化过程中没有观察到铑损失将蒸馏温度提高至115℃后,直到第35天均观察到有铑损失发生在第36天再添加0.5%(Wt)的同样的有机添加剂(共添加了0.75%Wt)到反应器2中,在其后的6天中没有观察到进一步的铑损失但是将温度提高到125℃后又产生了铑损失实施例9用丁烯-1和丁烯-2(顺式和反式)作为混合烯料,以2-t-丁基-4-甲氧苯基〔3,3′-双-t-丁基-5,5′-二甲氧基-1,1′-联苯基-2,2′双基〕亚磷酸盐作为配位体促进剂进行如美国专利4599206例10所述的连续加氢醛化实验起始及一般操作均与美国专利4599206之例10相同通过将1.03升二羰基乙酰丙酮铑(155ppm的铑)催化剂起始溶液,其中含3.4%Wt2-t-丁基-4-甲氧苯基(3,3′-双-t-丁基-5,5′-二甲氧基-1,1′-联苯基-2,2′双基)亚磷酸盐配位体(39.9摩尔当量的配位体/每摩尔铑),1%(Wt)乙烯吡咯烷酮-乙烯基乙酸酯共聚物(S-630,60%乙烯吡咯烷酮,GAF有限公司)和95.6%(Wt)的C5醛(86.2%Wt的戊醛和9.4%Wt的戊醛三聚物作溶剂),添加到反应器1中进行加氢醛化反应将1.2升同样的催化剂起始液加到反应器2中在31天的连续加氢醛化过程中,反应条件以及按每小时每升克分子计算的C5醛的产生速率,和直链正戊醛产物对支链2-异戊醛产物的比例均示于表8中在106℃~110℃及18~21磅/英吋2的压力下从液体反应液中分离出醛在上述的31天连续加氢醛化过程中没有观察到铑损失表8操作天数 6.9 13.9 20.9 30.8丁烯原料,摩尔%丁烯-1 5.6 5.4 5.3 5.4丁烯-2(顺式或反式)磅/英吋294.2 91.5 91.2 90.2n-丁烯 0.2 3.1 3.5 4.4反应器1温度(℃) 80.4 80.4 80.4 80.5压力(磅/英吋2) 185 185 185 185H2(磅/英吋2) 65.2 68.2 61.3 65.2CO(磅/英吋2) 75.5 71.9 68.5 66.5丁烯-2(顺式或反式)(磅/英吋2) 31.1 30.0 30.9 30.3丁烯-1(磅/英吋2) 0.5 0.4 0.4 0.4反应器2温度(℃) 85.0 85.0 85.3 85.4压力(磅/英吋2) 165 165 165 165H2(磅/英吋2) 49.9 56.2 53.9 59.0CO(磅/英吋2) 71.9 66.5 66.6 63.7丁烯-1(磅/英吋2) 0.2 0.2 0.4 0.2丁烯-2(顺式或反式)(磅/英吋2) 14.3 12.8 12.1 12.5结果n-戊醛 0.40 0.38 0.38 0.372-异戊醛 1.31 1.23 1.25 1.21(克分子/升/小时)实施例10按实施例9所述进行一类似的连续加氢醛化实验,所用烯料为丁烯-1,配位体促进剂为2-t-丁基-4-甲氧苯基(3,3′-双-t-丁基-5,5′-二甲氧基-1,1′-联苯基-2,2′双基)亚磷酸盐(在此为配位体A)其起始及一般操作均与美国专利4599206例10中所述的相同通过将658.5克的二羰基乙酰丙酮铑(含200ppm的铑)的催化剂溶液,其中含3.7%(Wt)的2-t-丁基-4-甲氧苯基(3,3′-双-t-丁基-5,5′-二甲氧基-1,1′-联苯基-2,2′双基)亚磷酸盐配位体(33.7摩尔当量的配位体/每摩尔铑),1%(Wt)乙烯吡咯烷酮-乙烯基乙酸酯共聚物(E-735,70%的乙烯吡咯烷酮,GAF有限公司),89.25%(Wt)的C5醛和5.0%(Wt)的Texanol ,添加到反应器1中进行加氢醛化反应将752.5克同样的催化剂起始溶液加到反应器2中在15天的处理过程中的反应条件,按每小时每升克分子计算的C5醛的平均生产速率以及直链正戊醛对支链2-异戊醛产物的平均比均示于表9在1~5天内,113℃及19磅/英吋2的压力下,从液体反应溶液中分离出醛,在此5天中没有观察到铑损失在第6天,将分离温度提高到134℃并在29磅/英吋2的压力下保持9天,在此9天中没有观察到铑损失表9在15天中的操作条件丁烯原料,摩尔%丁烯-1 99.9丁烯-2 0.1反应器1/2温度℃ 90/90压力磅/英吋2205/185H2磅/英吋295/90CO 磅/英吋274/61丁烯-1磅/英吋22.6/0.1丁烯-2磅/英吋210/3(顺式或反式)结果n-戊醛/2-异戊醛 1.35到1醛速率(克分子/升/小时) 5.7实施例11重复实施例10的实验,将638.5克的起始溶液加到反应器1中;将725克的同样溶液加到反应器2中(其余条件与实施例10相同)进行39天的加氢醛化处理,按下面指定的条件蒸馏和回收醛产品反应条件,按每小时每升克分子计算的C5醛的平均生产速率和在34天中直链n-戊醛产物对支链2-异戊醛产物的平均比例,均列于表10分离醛的条件为第1~第25天,温度为112℃~114℃,压力为17磅/英吋2;在第26~第29天,温度为120℃,压力为17磅/英吋2在上述的29天中没有观察到铑损失从第30天起到第39天,温度为150℃,压力为25磅/英吋2在此9天中观察到的铑损失速率为2%/每天表10在39天中的操作条件丁烯原料,摩尔%丁烯-1 99.9丁烯-2 0.1反应器1/2温度℃ 85/85压力磅/英吋2207/185H2磅/英吋292/87CO 磅/英吋279/70丁烯-1 磅/英吋24.1/0.1丁烯-2(顺式或反式)磅/英吋27/3结果n-戊醛/2-异戊醛 1.5到1醛速率(克分子/升/小时) 5.4对本发明进行各种变化和改动,对熟练的技术人员来说是易于实行的,应该认识到这样的变化和改动均包括在申请的构思和权利要求的权限范围之中
- 专利详情
- 全文pdf
- 权力要求
- 说明书
- 法律状态
查看更多专利详情
下载专利文献
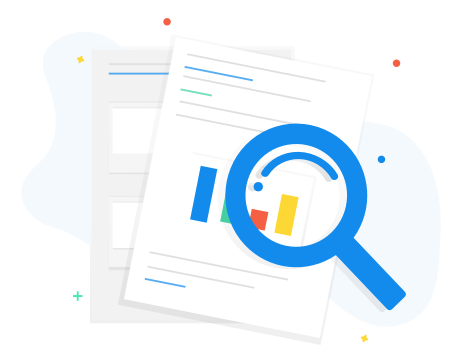
下载专利
同类推荐
-
牛茂计苓, 杨健计苓, 杨健梁锁页, 赵松源
您可能感兴趣的专利
-
梁锁页, 赵松源J·F·香利J·F·香利J·F·香利J·F·香利J·F·香利J·F·香利
专利相关信息
-
希尔雅斯·布安达里余水林, 荣继华余水林, 荣继华余水林, 荣继华余水林, 荣继华