一种氮化硅结合碳化硅复相耐高温材料及其制备方法【技术领域】。具体涉及一种氮化硅结合碳化硅复相耐高温材料及其制备方法。[0002]氮化硅(Si3N4)结合碳化硅(SiC)复相耐高温材料因具有优异的耐高温和耐磨性、良好的导热性、显著的抗蠕变和抗化学侵蚀等性能,在钢铁冶金和化学工业中被广泛地应用。特别是作为一种大中型高炉耐高温(耐火)材料,它在过去的几十年使用过程中对于延长高炉使用寿命发挥了重要作用。传统上Si3N4结合SiC的耐高温材料制品通常以硅粉(Si)、SiC颗粒和细粉为原料,以氧化铝(Al2O3)细粉、氧化镁(MgO)细粉或氧化钇(Y2O3)细粉等为添加剂,在氮气气氛和高温下(通常为1400-1450°C)进行原位氮化反应烧结制备得到。然而,较厚的氮化硅结合碳化硅耐火制品不仅使得其氮化温度高、氮化反应时间长,而且常出现氮化不完全,制品内部经常出现黑心、夹心等问题;同时由于原位氮化反应形成的Si3N4结合SiC复相耐高温材料的致密化是通过气相反应来完成,导致现行技术生产的Si3N4结合SiC的制品存在气孔率高、基质和骨料之间的结合需要进一步强化,材料的强度和抗热震性能需要进一步提高等问题。[0003]近些年来,我国纳米科技发展势头强劲,也正在致力于建立纳米技术产业。纳米结构具有大的比表面积、优异的力学性能,是复合材料理想的增强体,特别是在提高材料强度和韧性方面有显著效果。一般情况下,纳米粉可作为微量添加剂引入,能改善制品的烧结性和显微结构,从而强 烈地影响制品的力学性能。骨料颗粒中加入纳米粉后,纳米粉分布于颗粒间或颗粒内,使晶粒的晶格发生畸变,促进烧结,同时,在晶粒内形成很多次界面,在材料受力产生裂纹时,可引起裂纹偏转或裂纹被钉扎,从而提高制品的断裂强度和韧性,改善耐高温性能,提高抗热震性和抗高温蠕变性。如何采用先进的技术制备出纳米结构以及将其应用于耐火材料中以提升耐火材料的性能一直是耐火材料科技工作者思考的问题。[0004]实际上,在Si3N4结合SiC复相耐高温材料的显微结构中,SiC颗粒被Si3N4基质包裹,烧结后的氮化物通常会产生一些纤维状、针状晶须并形成网状编织结构,穿插于SiC颗粒之间,这样的结构使材料的力学性能虽得到一定程度的提高,但这种纤维和晶须结构在材料或者制品中通常出现在气孔中并且含量较少,导致这种提高作用是有限的。如何增加材料中的纤维含量尤其是纳米纤维的含量是提高Si3N4结合SiC复相耐高温材料致密度、强化基质和骨料、提高材料强度和抗热震性的关键。研究表明Fe、Co、Ni等金属由于不满的d轨道可接受电子或者电子对从而形成配合物,借助配体与受体的配位作用而形成活性中间体从而具有降低反应活化能的特性,其被许多研究证实是催化活性非常高的过渡金属,目前在煤气化催化、乙醇汽油车尾气净化催化、钼系双金属纳米催化和碳的一维耐米结构的催化合成中都得到广泛的应用,但是文献表明其在原位氮化反应Si3N4结合SiC复相耐高温材料中没有使用。
[0005]本发明旨在克服现有技术存在的不足,目的是提供一种氮化反应温度低、反应完全的氮化娃结合碳化娃复相耐高温材料的制备方法;用该方法制备的氮化娃结合碳化娃复相耐高温材料纯度高、强度大、寿命长、抗热震性优异、抗侵蚀性良好和产业化前景大。[0006]为实现上述目的,本发明采用的技术方案的具体步骤是:
步骤一、先将13~22wt%的硅粉和0.0riwt%的催化剂粉采用干法球磨0.5^2小时,再加入0.1~0.99wt%的三氧化二钇细粉和12~22wt%的碳化硅细粉,继续采用干法球磨0.5~5小时,得混合细粉料。
[0007]步骤二、将3~8wt%的结合剂加入到35~50wt%的碳化娃粗颗粒和10~18wt%的碳化硅中颗粒中,搅拌0.1~0.5小时,得润湿后的碳化硅颗粒料。
[0008]步骤三、将步骤一得到的混合细粉料加入到步骤二得到的润湿后的碳化硅颗粒料中,混炼0.5飞小时,机压成型,再对成型后的坯体进行冷等静压处理,冷等静压处理的压力为1OO~3OOMPa ;然后将冷等静压处理后的坯体在50~60°C条件下干燥广3小时,在90~100℃条件下干燥2~4小时,得烧结前驱体。
[0009]步骤四、将步骤三得到的烧结前驱体置于管式电炉内,在氮气气氛下:先以2~10°C /min的升温速率升至1150~l200°C,保温0.5~2小时;再以2~5°C /min的升温速率升至1280~l300C,保温0.5~2小时;然后以2~5°C /min的升温速率升至1320~l400°C,保温2~20小时,最后在氮气气氛下随炉自然冷却至室温,即得氮化硅结合碳化硅复相耐高温材料。
[0010]所述娃粉中的Si含量> 95wt%,粒径< 0.1_。
[0011]所述催化剂为金属Fe粉、Co粉和Ni粉中的一种以上,金属Fe粉、Co粉和Ni粉中对应的Fe、Co和Ni的含量≥95wt%,粒径均≤lOMm。
[0012]所述三氧化二I乙细粉中Y2O3的含量≥95wt%,粒径≤0.1mm。
[0013]所述碳化硅细粉中的SiC含量≥90wt%,碳化硅细粉的粒径≤0.1mm。
[0014]所述碳化娃粗颗粒中的SiC含量≥ 90wt%,碳化娃粗颗粒的粒径为0.5~1.2mm。
[0015]所述碳化硅中颗粒中的SiC含量≥90wt%,碳化硅中颗粒的粒径为0.1`0.5mm。
[0016]所述结合剂为浓度为30%的工业糊精、浓度为30%的木质素磺酸钙溶液和浓度为10%的聚乙烯醇溶液中的一种。
[0017]由于采用上述技术方案,本发明与现有技术相比具有如下积极效果和突出特点:
1、本发明添加Fe、Co和Ni超细金属粉为催化剂,降低氮化反应温度和缩短反应时间。
[0018]2、本发明添加Fe、Co和Ni超细金属粉为催化剂,促进了硅粉氮化并原位形成Si3N4纳米纤维。所制备的氮化硅结合碳化硅复相耐高温材料中存在着大量的Si3N4纳米纤维,Si3N4纳米纤维提高了所制备的氮化硅结合碳化硅复相耐高温材料的强度。
[0019]3、本发明添加Fe、Co和Ni超细金属粉为催化剂,促进硅粉的氮化反应,解决了目前氮化制品中存在的氮化不完全和“硅芯”的问题,本发明所制得的氮化硅结合碳化硅复相耐高温材料的显气孔率为16.5^17.5%,体积密度为2.70~2.80g/cm3,常温抗折强度为60~70MPa,耐压强度为240~270MPa ;提高了所制备的氮化硅结合碳化硅复相耐高温材料的纯度、抗热震性和抗侵蚀性,延长了制品的使用寿命。
[0020]因此,本发明具有反应温度低和反应时间短的特点,所得氮化硅结合碳化硅复相耐高温材料纯度高、强度大、寿命长、抗热震性优异、抗侵蚀性良好和产业化前景大。
[0021]图1为本发明制备的一种氮化硅结合碳化硅复相耐高温材料断面的SEM图;
图2是图1所述氮化硅结合碳化硅复相耐高温材料中晶须的SEM图。
[0022]下面结合附图和对本发明做进一步的描述,并非对其保护范围的限制。
[0023]为避免重复,先将本所涉及的原料统一描述如下,实施例中不再赘述:
所述娃粉中的Si含量≥95wt%,粒径< 0.1mm。
[0024]金属Fe粉、Co粉和Ni粉中对应的Fe、Co和Ni的含量≥95wt%,粒径均≤lOMm。
[0025]所述三氧化二乾细粉中Y2O3的含量≥95wt%,粒径< 0.1mm。
[0026]所述碳化硅细粉中的SiC含量≥90wt%,碳化硅细粉的粒径≤0.1mm。
[0027]所述碳化娃粗颗粒中的SiC含量> 90wt%,碳化娃粗颗粒的粒径为0.5~1.2mm。
[0028]所述碳化硅中颗粒中的SiC含量≥90wt%,碳化硅中颗粒的粒径为0.1-0.5mm。
[0029]实施例1
一种氮化硅结合碳化硅复相耐高温材料及其制备方法。本实施例的具体步骤是:步骤一、先将19~22wt%的硅粉和0.01-0.3wt%的金属Co粉采用干法球磨0.5~I小时,再加入0.1-0.3wt%的三氧化二钇细粉和18~22wt%的碳化硅细粉,继续采用干法球磨0.5^2小时,得混合细粉料。
[0030]步骤二、将3~5wt%的浓度为10%的聚乙烯醇加入到4(T45wt%的碳化硅粗颗粒和14"l8wt%的碳化硅中颗粒中,搅拌0.1-0.2小时,得润湿后的碳化硅颗粒料。
[0031]步骤三、将步骤一得到的混合细粉料加入到步骤二得到的润湿后的碳化硅颗粒料中,混炼0.5~2小时,机压成型,再对成型后的坯体进行冷等静压处理,冷等静压处理的压力为IOOlOOMPa ;然后将冷等静压处理后的坯体在5(T60°C条件下干燥广3小时,在9(T10(TC条件下干燥2~4小时,得烧结前驱体。
[0032]步骤四、将步骤三得到的烧结前驱体置于管式电炉内,在氮气气氛下:先以8^10°C /min的升温速率升至118(Tl200°C,保温0.5^1小时;再以2~3°C /min的升温速率升至129(Tl300°C,保温0.5~I小时;然后以2~3。。/min的升温速率升至138(Tl40(TC,保温2飞小时,最后在氮气气氛下随炉自然冷却至室温,即得氮化硅结合碳化硅复相耐高温材料。
[0033]实施例2
一种氮化硅结合碳化硅复相耐高温材料及其制备方法。本实施例的具体步骤是:步骤一、先将19~22wt%的硅粉和0.01-0.3wt%的金属Fe粉采用干法球磨0.5~I小时,再加入0.1-0.3wt%的三氧化二钇细粉和18~22wt%的碳化硅细粉,继续采用干法球磨0.5^2小时,得混合细粉料。
[0034]步骤二、将3~5wt%的浓度为10%的聚乙烯醇加入到40~45wt%的碳化娃粗颗粒和14"l8wt%的碳化硅中颗粒中,搅拌0.1~0.2小时,得润湿后的碳化硅颗粒料。
[0035]步骤三、将步骤一得到的混合细粉料加入到步骤二得到的润湿后的碳化硅颗粒料中,混炼0.5~2小时,机压成型,再对成型后的坯体进行冷等静压处理,冷等静压处理的压力为IOOlOOMPa ;然后将冷等静压处理后的坯体在5(T60°C条件下干燥广3小时,在9(T10(TC条件下干燥2~4小时,得烧结前驱体。
[0036]步骤四、将步骤三得到的烧结前驱体置于管式电炉内,在氮气气氛下:先以8^10°C /min的升温速率升至118(Tl200°C,保温0.5^1小时;再以2~3°C /min的升温速率升至129(Tl300°C,保温0.5~I小时;然后以2~3。。/min的升温速率升至138(Tl40(TC,保温2飞小时,最后在氮气气氛下随炉自然冷却至室温,即得氮化硅结合碳化硅复相耐高温材料。
[0037]实施例3
一种氮化硅结合碳化硅复相耐高温材料及其制备方法。本实施例的具体步骤是:步骤一、先将16~19wt%的硅粉和0.15~0.3wt%的金属Fe粉和0.15~0.3wt%的金属Ni粉采用干法球磨1~1.5小时,再加入0.3~0.6wt%的三氧化二钇细粉和15~20wt%的碳化硅细粉,继续采用干法球磨2~3.5小时,得混合细粉料。
[0038]步骤二、将5~7wt%的浓度为10%的聚乙烯醇加入到35~43wt%的碳化硅粗颗粒和13"l8wt%的碳化硅中颗粒中,搅拌0.2^0.4小时,得润湿后的碳化硅颗粒料。
[0039]步骤三、将步骤一得到的混合细粉料加入到步骤二得到的润湿后的碳化硅颗粒料中,混炼2~3.5小时, 机压成型,再对成型后的坯体进行冷等静压处理,冷等静压处理的压力为20(T250MPa ;然后将冷等静压处理后的坯体在5(T60°C条件下干燥1~3小时,在9(T10(TC条件下干燥2~4小时,得烧结前驱体。
[0040]步骤四、将步骤三得到的烧结前驱体置于管式电炉内,在氮气气氛下:先以6^80C /min的升温速率升至117(Tll80°C,保温f 1.5小时;再以3~4°C /min的升温速率升至1285~1290°C,保温I~1.5小时;然后以3~4°C /min的升温速率升至135(Tl380°C,保温6^14小时,最后在氮气气氛下随炉自然冷却至室温,即得氮化硅结合碳化硅复相耐高温材料。
[0041]实施例4
一种氮化硅结合碳化硅复相耐高温材料及其制备方法。本实施例的具体步骤是:步骤一、先将16~19wt%的硅粉和0.3~0.6wt%的金属Ni粉采用干法球磨I~1.5小时,再加入0.3^0.6wt%的三氧化二钇细粉和15~20wt%的碳化硅细粉,继续采用干法球磨2~3.5小时,得混合细粉料。
[0042]步骤二、将5~7wt%的浓度为30%的木质磺酸钙加入到35~43wt%的碳化娃粗颗粒和13~18wt%的碳化硅中颗粒中,搅拌0.2^0.4小时,得润湿后的碳化硅颗粒料。
[0043]步骤三、将步骤一得到的混合细粉料加入到步骤二得到的润湿后的碳化硅颗粒料中,混炼2~3.5小时,机压成型,再对成型后的坯体进行冷等静压处理,冷等静压处理的压力为20(T250MPa ;然后将冷等静压处理后的坯体在5(T60°C条件下干燥1~3小时,在9(T10(TC条件下干燥2~4小时,得烧结前驱体。
[0044]步骤四、将步骤三得到的烧结前驱体置于管式电炉内,在氮气气氛下:先以6^80C /min的升温速率升至117(Tll80°C °C,保温f 1.5小时;再以3~4°C /min的升温速率升至1285~1290°C,保温1~1.5小时;然后以3~4°C /min的升温速率升至1350-l380°C,保温6~14小时,最后在氮气气氛下随炉自然冷却至室温,即得氮化硅结合碳化硅复相耐高温材料。
[0045]实施例5
一种氮化硅结合碳化硅复相耐高温材料及其制备方法。本实施例的具体步骤是:步骤一、先将13~16wt%的硅粉和0.3~0.45wt%的金属Fe粉和0.3~0.45wt%金属Co粉采用干法球磨1.5^2小时,再加入0.6^0.99wt%的三氧化二钇细粉和12~17wt%的碳化硅细粉,继续采用干法球磨3.5飞-5小时,得混合细粉料。
[0046]步骤二、将6~8wt%的浓度为30%的工业糊精加入到45~50wt%的碳化硅粗颗粒和l(Tl3wt%的碳化硅中颗粒中,搅拌0.4^0.5小时,得润湿后的碳化硅颗粒料。
[0047]步骤三、将步骤一得到的混合细粉料加入到步骤二得到的润湿后的碳化硅颗粒料中,混炼3.5飞小时,机压成型,再对成型后的坯体进行冷等静压处理,冷等静压处理的压力为250~300MPa ;然后将冷等静压处理后的坯体在5(T60°C条件下干燥1~3小时,在9(T10(TC条件下干燥2~4小时,得烧结前驱体。
[0048]步骤四、将步骤三得到的烧结前驱体置于管式电炉内,在氮气气氛下:先以2~6°C /min的升温速率升至115(Tll70°C,保温1.5~2小时;再以4~5°C /min的升温速率升至1280~1285°C,保温1.5~2小时;然后以4~5°C /min的升温速率升至1320-l350°C,保温14-20小时,最后在氮气气氛下随炉自然冷却至室温,即得氮化硅结合碳化硅复相耐高温材料。
[0049]实施例6
一种氮化硅结合碳化硅复相耐高温材料及其制备方法。本实施例的具体步骤是:步骤一、先将13~16wt%的硅粉和0.3~0.45wt%的金属Co粉和0.3~0.45wt%金属Ni粉采用干法球磨1.5^2小时,再加入0.6^0.99wt%的三氧化二钇细粉和12~17wt%的碳化硅细粉,继续采用干法球磨3.5-5小时,得混合细粉料。
[0050]步骤二、将6~8wt%的浓度为30%的工业糊精加入到45~50wt%的碳化硅粗颗粒和l(Tl3wt%的碳化硅中颗粒中,搅拌3.5-5小时,得润湿后的碳化硅颗粒料。
[0051]步骤三、将步骤一得到的混合细粉料加入到步骤二得到的润湿后的碳化硅颗粒料中,混炼3.5-5小时,机压成型,再对成型后的坯体进行冷等静压处理,冷等静压处理的压力为250~300MPa ;然后将冷等静压处理后的坯体在50-60°C条件下干燥1~3小时,在90-100°C条件下干燥2~4小时,得烧结前驱体。
[0052]步骤四、将步骤三得到的烧结前驱体置于管式电炉内,在氮气气氛下:先以2~6°C /min的升温速率升至1150-ll70°C,保温1.5~2小时;再以4~5°C /min的升温速率升至1280~1285°C,保温1.5~2小时;然后以4~5°C /min的升温速率升至1320-l350°C,保温14-20小时,最后在氮气气氛下随炉自然冷却至室温,即得氮化硅结合碳化硅复相耐高温材料。
[0053]本与现有技术相比具有如下积极效果和突出特点:
1、本添加Fe、Co和Ni超细金属粉为催化剂,降低氮化反应温度和缩短反应时间。
[0054]2、本添加Fe、Co和Ni超细金属粉为催化剂,促进了硅粉氮化并原位形成Si3N4纳米纤维。图1是实施例1制备的一种氮化娃结合碳化娃复相耐高温材料断面的SEM图;图2为该氮化硅结合碳化硅复相耐高温材料中晶须的SEM图,从图1和图2可知制品中存在着大量的Si3N4纳米纤维,Si3N4纳米纤维提高了所制备的氮化硅结合碳化硅复相耐高温材料的强度。
[0055]3、本添加Fe、Co和Ni超细金属粉为催化剂,促进硅粉的氮化反应,解决了目前氮化制品中存在的氮化不完全和“硅芯”的问题,本所制得的氮化硅结合碳化硅复相耐高温材料的显气孔率为16.5^17.5%,体积密度为2.7(T2.80g/cm3,常温抗折强度为6(T70MPa,耐压强度为24(T270MPa ;提高了所制备的氮化硅结合碳化硅复相耐高温材料的纯度、抗热震性和抗侵蚀性,延长了制品的使用寿命。
[0056]因此,本具体实施 方式具有反应温度低和反应时间短的特点,所得氮化硅结合碳化硅复相耐高温材料纯度高、强度大、寿命长、抗热震性优异、抗侵蚀性良好和产业化前景大。
一种氮化硅结合碳化硅复相耐高温材料及其制备方法
- 专利详情
- 全文pdf
- 权力要求
- 说明书
- 法律状态
查看更多专利详情
下载专利文献
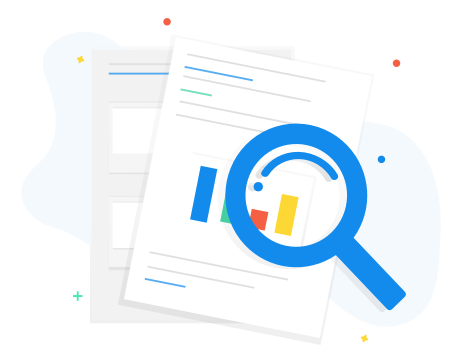
下载专利
同类推荐
-
郭伟明
您可能感兴趣的专利
-
邓树军邓树军C·J·黄, A·J·皮兹克付伟峰, 窦涛杜平凡
专利相关信息
-
方宁象盛蕾, 盛志义姚秀敏