专利名称:利用狭长孔下拉法生产薄板材料的成型设备及方法 目前用以生产薄板玻璃的制造方法中,美国第US3,338,696号专利公开的一种所谓‘溢流融合法’的方法,其优点在于所生产出的薄板玻璃两侧表面因未与任何物件接触,故可得到相当好的表面品质,且可在不需研磨的情形下,直接进行切割,得到所需的薄板玻璃成品。然而,由于在制作大尺寸薄板玻璃时,‘溢流融合法’中所使用的等压管(Isopipe),其设计技术不仅需相当精密,困难极高,且在生产过程中,所搭配的相关温度控制条件,又非常严苛,因此,为令传统的‘溢流融合法’制作出品质优良的薄板玻璃,业者在其生产设备及后续制程中,所需付出的成本及维护费用自然相当昂贵。‘溢流融合法’的另一缺点是此种制程产适宜用以制作厚度为0.5mm以下的薄板玻璃,此乃因玻璃越薄越不易成型,更何况利用‘溢流融合法’制作薄板玻璃时,其所成型的薄板玻璃为由两片薄板玻璃融合组成,此时,由于越薄的玻璃板在成型时辐射散热越快,致使两片薄板玻璃不易融合,易造成良品率大幅降低。此外,由于利用‘溢流融合法’制作薄板玻璃时,薄板玻璃是在等压管(Isopipe)的根部(root)融合成型,因此,在生产过程中,若等压管(Isopipe)的根部发生任何损伤导致残留气泡时,其所生产出的薄板玻璃均将变成不良品,此时,由于根部为与等压管一体成型,故无法单独更换受损的根部,而需更换整个等压管,其所需耗费的成本、人力及工时自然亦相当可观。另一种生产薄板玻璃的制造方法为‘狭长孔下拉成型法’。‘狭长孔下拉成型法’与前述的‘溢流融合法’不同,其被用以制作薄板玻璃的历史远较‘溢流融合法’为早。在传统的‘狭长孔下拉成型法’中,并未设置任何分配器,仅在其成型池下方装喷嘴成型装置,此可由美国第US2,880,551号专利得知,其优点是在通过喷嘴成型装置的融熔玻璃的液位压力一致,其缺点则是不易均匀控制成型池中融熔玻璃的温度,造成通过喷嘴成型装置的玻璃温度及黏度不一致,且不稳定,致使无法准确控制薄板玻璃厚度,因此,在利用‘狭长孔下拉成型法’制作薄板玻璃时,为有效控制融熔玻璃的温度,成型池的尺寸及容积无法太大,故所生产出的薄板玻璃的有效宽度亦不大。嗣,虽有业者为改进融熔玻璃温度不易控制的缺点,在美国第US2,880551号专利中,揭露了由白金分配器及喷嘴组成的成型设备取代成型池技术,并利用白金加热机制,有效控制分配器内融熔玻璃的温度分布,令分配器将融熔玻璃均匀分配至喷嘴出口,再以下拉法生产出较大尺寸的薄板玻璃。由于,在上述成型设备中,还是需借由控制分配器的温度以控制融熔玻璃的温度分布,始能达到均匀流量分配,此举将导致融熔玻璃自喷嘴拉出时,在玻璃上产生不同的温度分布,造成薄板玻璃在成型时易产生不平坦及刷痕,徒增薄板玻璃成型控制的困难度。
本发明的目的是提供一种制作优质大尺寸薄板材料、设备维修容易、成本低廉、有效提升生产效率的利用狭长孔下拉法生产薄板材料的成型设备及方法。本发明方法包括将呈融熔状均质热塑性材料导入流体分配管,令均质热塑性材料被均匀分配至流体分配管的两侧后,使得在流体分配管内均质热塑材料的流量沿流体分配管两侧长度方向作线性递减,并令流体分配管单位长度内流量一致,以使其内热塑性材料的静压力分布自动趋于平衡;令均质热塑性材料被均匀分配至流体分配管两侧时,可垂直地向下流向衔接于流体分配管下方渠道内,并使得均质热塑性材料能以一致的单位长度流量通过渠道底缘的出口;本发明设备包括用以导入热塑性材料的供料管、连接在供料管下方的接头、两个流体分配管及渠道;两个流体分配管得以对称连接在接头下方两侧;使得由供料管导入的热塑性材料经过接头后分别进入两个流体分配管,并分别沿着两个流体分配管的中心线向两侧流动至流体分配管的末端,且在稳态生产时,令在其内流动且呈融熔状的均质热塑性材料的流量沿着流体分配管两侧的长度方向作线性递减,并令流体分配管单位长度内的流量一致,以使其内热塑性材料的静压力分布自动趋于平衡;渠道具有呈长方形截面的槽口,其一端沿长度方向与两个流体分配管的底缘衔接,并与两个流体分配管相导通;以令流入两个流体分配管的均质热塑性材料在被均匀分配至流体分配管两侧后,可经由渠道的槽口垂直地向下流至渠道底缘出口,且以一致的流量通过渠道底缘出口。其中流体分配管每一单位长度内均质热塑性材料借由其位能消除掉其在流体分配管内流动的静压损失,使流体分配管内任一位置的热塑性材料的静压力趋于一致。
流体分配管长度方向的每一单位长度中心线对应到其水平方向的夹角设计成向流体分配管两侧对称递减,以均匀分配流量,并令流体分配管内任一位置的热塑性材料的静压力趋于一致。
渠道的宽度,设计成可令流体分配管上任一单位长度内的均质热塑性材料流量能以自身重力沿地心引力方向流动至渠道内,令经过渠道的均质热塑性材料能以一致单位长度的流量通过渠道底缘的出口。
分配器流体分配管的每一单位长度的中心线所对应的水平夹角均设为相同,但沿流体分配管的长度方向,则令每一单位长度的流体分配管所对应的管径设计成向分配管两侧对称渐缩,以均匀分配流量,亦可令流体分配管每一单位长度内均质热塑性材料的静压力趋于一致。
渠道的宽度,设计成可令流体分配管上任一单位长度内的均质热塑性材料流量能以自身重力沿地心引力方向流动至渠道内,令经过渠道的均质热塑性材料能以一致单位长度的流量通过渠道底缘的出口。
均质热塑性材料以一致流量依序通过渠道底缘出口及其下方的狭长孔喷嘴后,依下拉法生产出厚度一致的薄板材料。
两个流体分配管沿其长度方向的任一位置的形成为根据流体力学理论被设计成借由其内均质热塑性材料的位能消除掉其在流体分配管内流动的静压损失,使流体分配管内任一位置的热塑性材料的静压力趋于一致。
两个流体分配管沿其长度方向的任一位置中心线对应到其水平线所形成的每一水平夹角,设计成愈往两个流体分配管末端,其水平夹角愈小。
衔接于两个流体分配管底缘的渠道宽度设计成可令流体分配管上任一单位长度内的均质热塑性材料流量能以自身重力沿地心引力方向流动至渠道内,令经过渠道的均质热塑性材料能以一致单位长度的流量通过渠道底缘的出口。
流体分配管的每一单位长度的中心线所对应的水平夹角均设为相同,但沿流体分配管的长度方向,则令每一单位长度的流体分配管所对应的管径设计成向分配管两侧对称渐缩。
衔接于两个流体分配管底缘的渠道宽度设计成可令流体分配管上任一单位长度内的均质热塑性材料流量能以自身重力沿地心引力方向流动至渠道内,令经过渠道的均质热塑性材料能以一致单位长度的流量通过渠道底缘的出口。
渠道下方衔接设有喷嘴,以令通过渠道的均质热塑性材料可以一致流量通过喷嘴。
由于本发明方法包括将均质热塑性材料导入流体分配管、沿流体分配管两侧长度方向以流量作线性递减且单位长度内流量一致被均匀分配至流体分配管的两侧以热塑性材料的静压力分布自动趋于平衡、垂直地向下流向衔接于流体分配管下方渠道内并使得均质热塑性材料能以一致的单位长度流量通过渠道底缘的出口;本发明设备包括供料管、连接在供料管下方的接头、对称连接在接头下方两侧的两个流体分配管及衔接于两个流体分配管底缘具有呈长方形截面槽口的渠道。本发明流体分配管内均质热塑性材料的压力分布自动趋于平衡而不受其长度方向上的限制,因此,特别适用于生产更宽且厚度一致的大尺寸薄板玻璃,其与传统的‘溢流融合法’相比较,不仅成本低廉、维修保养容易,且在作业期间,其分配器内融熔玻璃的温度、流量及拉引速度均较易被保持在固定状态,有效避免了传统‘溢流融合法’在利用两片薄板玻璃融结合成一片薄板玻璃时,因强烈的辐射冷却,造成两片薄板玻璃在融合成型上发生困难的缺点;本发明设备及环境上要求不需特别严苛,因此,可大幅缩减维护及保养所需的成本。不仅制作优质大尺寸薄板材料,而且设备维修容易、成本低廉、有效提升生产效率,从而达到本发明的目的。
图1、为本发明利用狭长孔下拉法生产薄板材料的成型设备结构示意立体图。
图2、为本发明利用狭长孔下拉法生产薄板材料的成型设备分配器结构示意正视图。
图3、为本发明利用狭长孔下拉法生产薄板材料的成型设备分配器内融熔玻璃流动分配过程示意图。
图4、为本发明利用狭长孔下拉法生产薄板材料的成型设备每一单位长度上流体分配管结构示意纵向剖视图。
图5、为本发明利用狭长孔下拉法生产薄板材料的成型设备分配器结构示意俯视图。
图6、为本发明利用狭长孔下拉法生产薄板材料的成型设备分配器结构示意横向剖视图。
图7、为本发明利用狭长孔下拉法生产薄板材料的成型设备分配器结构示意纵向剖视图。
本发明利用狭长孔下拉法生产薄板材料的成型设备及方法主要为根据流体力学理论,设计出分配器,分配器包括具有特殊轮廓的流体分配管及具有特殊宽度的渠道。
本发明利用狭长孔下拉法生产薄板材料的成型方法包括将呈融熔状均质热塑性材料导入流体分配管,令均质热塑性材料被均匀分配至流体分配管的两侧后,使得在流体分配管内均质热塑材料的流量沿流体分配管两侧长度方向作线性递减,并令流体分配管单位长度内流量一致,以使其内热塑性材料的静压力分布自动趋于平衡;令均质热塑性材料被均匀分配至流体分配管两侧时,可垂直地向下流向衔接于流体分配管下方渠道内,并使得均质热塑性材料能以一致的单位长度流量通过渠道底缘的出口。
其中流体分配管在稳态生产时,令其内均质且呈融熔状态的热塑性材料流量沿着流体分配管两侧的长度方向作线性递减,并令流体分配管的单位长度内的流量一致,以使其内热塑性材料的静压力分布自动趋于平衡,且令热塑性材料被均匀分配至液体分配管两侧后,可垂直地向下流向渠道,并以一致的单位长度流量通过渠道下方所设的狭长孔喷嘴,依下拉法沿分配器长度方向生产出厚度一致的薄板材料。
在此需特别声明,本发明在以下所述的各实施例中,均为以玻璃材料作为热塑性材料之一的实施态样。惟本发明在实际施作时,并不局限于此,任何熟悉该项技艺者,以其它热塑材料利用本发明的设备及方法,生产其它薄板材料,均属本发明所欲主张的保护范围。
如图1所示,本发明利用狭长孔下拉法生产薄板材料的成型设备由分配器20及喷嘴50构成。
分配器20由供料管10、接头33、两个流体分配管32及渠道40构成。
供料管10设置于分配器20上方,用以导入热塑性材料,在最佳实施例中,热塑性材料为已搅拌均匀的均质融熔玻璃。
接头33用以分别连接供料管10及两个流体分配管32,令两个流体分配管32得以对称地排列在分配器20两侧,使得由供料管10导入的为融熔玻璃的热塑性材料经过接头33后分别进入两个流体分配管32,并分别沿着两个流体分配管32的中心线321向两侧流动至流体分配管32的末端322,得以被均匀地分配至分配器20两侧。
为达此目的,两个流体分配管32必须被设计成可令其内为融熔玻璃的热塑材料的流量沿流体分配管32的长度方向线性递减。
渠道40设有呈长方形截面的槽口,其一端沿长度方向与两个流体分配管32的底缘衔接,并与两个流体分配管32相导通;其另一端与喷嘴50衔接,以令流入两个流体分配管32的融熔玻璃被均匀分配至流体分配管两侧后,可经由渠道40的槽口垂直地向下流至渠道40底缘的喷嘴50处,且以一致的流量通过喷嘴50的出口501,依下拉法沿分配器20长度方向制作出厚度一致的薄板玻璃。
为能更具体地说明融熔玻璃在分配器20内的流动路径及如何生产出厚度一致的薄板玻璃,特以如图2、图3、图4所示的分配器20为例详细说明如下在最佳实施例中,为令流经分配器20的融熔玻璃能以一致的流量通过喷嘴50的出口501,两个流体分配管32的中心线321必须根据流体力学理论,依特殊的数学公式,计算设计出流体分配管32及渠道40的形状及宽度,以令分配器20在稳态下生产薄板玻璃时,可令流体分配管32内的融熔玻璃的流量沿着流体分配管32长度方向作线性递减,并令流体分配管32单位长度内的流量一致,以使其内融熔玻璃的静压力分布自动趋于平衡,并令融熔玻璃被均匀分配至两个流体分配管32两侧后,可垂直地流向渠道40,并以一致的流量通过喷嘴50,以下拉法沿着分配器20长度方向生产出厚度一致的薄板玻璃。
如图3所示,当融熔玻璃自供料管10被导入接头33后,其流量Q将被一分为二,分别向两个流体分配管32的两侧流动,直到分别流动至两个流体分配管32的末端322时,为融熔玻璃的热塑性材料的流量始变为零。
如图4所示,若将两个流体分配管32沿其长度方向的任一位置中心线321对应到其水平线所形成的每一水平夹角θZ,设计成愈往两个流体分配管32末端322,其水平夹角θZ愈小,令两个流体分配管32内的热塑性材料的流动速度愈往末端322流动速度越慢,亦即令流体分配管32内的为融熔玻璃的热塑性材料的流量可沿着流体分配管32的长度方向作线性递减,并使流体分配管32单位长度内的流量一致,以达均匀分配流量的目的。
如此,在两个流体分配管32中心线321上任一位置内流动的为融熔玻璃的热塑性材料,将因各对应的水平夹角θZ的设计,可同时借由其位能消除掉其在流体分配管32内流动的静压损失,使流体分配管32内任一位置的为融熔玻璃的热塑性材料的静压力趋于一致且更趋于稳定。
衔接于两个流体分配管32底缘的渠道40亦需经由流体力学分析,以令所设计出的槽口宽度能使经由两个流体分配管32适当分配,且在每一单位长度上流量趋于一致的融熔玻璃得以保持一致的流量通过喷嘴50。此外,由于在分配器20中,渠道40内融熔玻璃受地心引力影响垂直地向下流动,因此,最佳实施例在设计渠道40的槽口宽度时,乃利用此一特性,使融熔玻璃向下流动的能力完全借由重力或融熔玻璃本身的重量来达成,完全不需对其施加额外的作用力,亦即完全不依靠压力差来维持单位长度上的流量,更加确保流经渠道40的融熔玻璃能以一致的流量通过喷嘴50的出口501,生产出厚度一致的薄板玻璃。
据此,若欲改变所生产的薄板玻璃的厚度,仅需借由更换喷嘴50,改变其出口501的宽度,即可生产出不同厚度的薄板玻璃。
最佳实施例中,为令两个流体分配管32内任一位置的热塑性材料的静压力趋于一致,在根据流体力学理论依数学公式设计流体分配管32时,由于两个流体分配管32整体结构呈左右对称状,如图2、图3、图4所示,故在此仅以其一半结构,根据黑根-波苏流量方程式(Hogen-Poiseuille equation),分析流体分配管32上对应于某一水平夹角θZ的任一位置z的截面流量如下(Q2)z=π×D4128×η×ΔPΔS]]>其中
Q为融熔玻璃的流量(cm3/sec);η为融熔玻璃的黏度(poise);D为流体分配管32的直径(cm);ρ为融熔玻璃的密度(g/cm3);ΔS为沿流体分配管32中心线由点S1到点S2的流动路径距离。
ΔP为流动时所需的全压力差。
此时,由点S1到点S2的全压力差ΔP可表示为ΔP=Ps1-Ps2+ρ×g×ΔH其中ΔH为位差;Ps1为在点S1的静压力;Ps2为在点S2的静压力;g为重力加速度980(cm/sec2)。
若融熔玻璃流动时所需的全压力差ΔP完全由位差ΔH提供,则流动时将不会造成静压力差,即Ps1=Ps2。故在流体分配管32的长度方向上的任一位置z的压力梯度可表示为ΔPΔs=ρ×g×sinθz]]>因此,流体分配管32在对应于某一水平夹角θZ的任一位置z的截面流量,将可改写成如下所示(Q2)z=K1×D4η×sinθz]]>其中K1为常数。
据上所述,由于最佳实施例期望融熔玻璃在流体分配管32的每一单位长度上的流量能趋于一致,意即由供料管10导入的融熔玻璃中,一半流量(Q/2)in分别沿着流体分配管32的长度方向作线性递减,其公式如下d(Q/2)indz=-const.]]>若代入其入口条件z=0⇒(Q2)0=(Q2)in]]>及端点条件z=L2⇒(Q2)L2=0,]]>并经微分方程式,可解析得其流量分配公式如下(Q2)z=(Q2)in×(1-zL/2)]]>借由上述流量分配公式,可决定沿流体分配管32长度上任一位置z的流量大小,嗣后再借由流体分配管32的截面流量公式,即可决定中心线321上每一位置z水平夹角θZ的特性均不会造成流动的静压损失。
如图5、图6所示,为令流经渠道40的融熔玻璃能以一致的流量通过喷嘴50的出口501,最佳实施例在根据流体力学理论,依数字公式计算渠道40的特定宽度401时,特将渠道40视为两垂直竖立且相互平行的平板,并将两平板间的融熔玻璃的流动视为在无限延伸平板间的垂直流动,加以分析计算。理论上,在稳态流动情形下,配合质量守衡方程式(Continuous equation),且仅考虑沿地心引力方向y的流动,可得其流体动量方程式(Navier-Stokesequation)如下0=-∂P∂y-ρ×g+η×(∂2v∂2x)]]>其中v为地心引力方向y的流动速度(cm/sec); 表示沿地心引力方向的流动压力差。
若带入其边界条件,解析上述方程式,将求得流动速度v,此时由于为以无限平板进行分析,故其流量可以z方向的单位长度的流量 表示,即q=QL=∫-bbv×dx,]]>再经解析后,即可得到如下公式q=QL=-K×b3η(∂P∂y+ρ×g)]]>
其中K为常数;负号(-)仅代表向下流动的物理意义;b为渠道40槽口的一半宽度(cm)。
最佳实施例中,由于已将流体分配管32设计成不需流动压力差,仅靠融熔玻璃自身重力流动,故可令流体分配管32上任一单位长度内的融熔玻璃流量q趋于一致,因此,欲使流体分配管32内单位长度流量为q的融熔玻璃以自身重量沿地心引力方向流动,理论上,此种流动并不受y方向流动距离影响,渠道40槽口一半宽度b可以如下公式表示Q×η=K2×b3×L其中K2为常数;L为流体分配管32在水平方向长度或分配器20的长度。
因此,依前述公式所设计的分配器20,在融熔玻璃呈稳态流动的操作环境下,不仅使各流体分配管32内任一位置的融熔玻璃的静压力可趋于一致,流经渠道40的融熔玻璃亦能以一致流量分布通过喷嘴50的出口501。
由于在前述最佳实施例中,当均质融熔玻璃在分配器20内稳定流动时,其内部压力分布将受分配器20外型的限制,会自动往平衡状态变化,以达到令经过渠道40内的融熔玻璃以一致的流量分布在喷嘴50出口501的最终结果。因此,基于同样道理,在本发明的其它最佳实施例中,亦可根据流体力学理论及前述数学公式,将各流体分配管32及渠道40设计成其它的轮廓及槽口宽度。
如图7所示,本发明实施例亦可将分配器70流体分配管82的每一单位长度的中心线821所对应的水平夹角θZ均设为相同,但沿流体分配管82的长度方向z,则令每一单位长度的流体分配管82所对应的管径D呈渐缩状态,如此,亦可令流体分配管82每一单位长度内融熔玻璃的静压力趋于一致,且令流经渠道90的融熔玻璃能以一致流量通过渠道90的出口901。本实施例在设计流体分配管82及渠道90时,分别利用下列两公式计算流体分配管82的轮廓及渠道90的宽度(Q2)z×η=K1×D4×sinθz,Q×η=K2×b3×L]]>其中Q为融熔玻璃的流量(cm3/sec);η为融熔玻璃的黏度(poise);D为流体分配管82的管径(cm);K1及K2分别为常数;b为渠道90槽口的一半宽度(cm);L为流体分配管82在水平方向的长度或分配器70的长度。
依上述两个最佳实施例所述可知,在设计流体分配管时,无论采用管径固定、但每单位长度所对应的水平夹角沿其长度方向递减的设计;或采用每一单位长度所对应的水平夹角固定、但管径沿其长度方向递减的设计;薄板玻璃成型黏度或产量变化无需符合Q1×η1=Q2×η2的限制。
综上所述,由于前述两最佳实施例所设计出的分配器,可令分配器内融熔玻璃的压力分布自动趋于平衡而不受其长度方向上的限制,因此,本发明的方法及设备特别适用于生产更宽且厚度一致的大尺寸薄板玻璃,其与传统的‘溢流融合法’相比较,不仅成本低廉、维修保养容易,且在作业期间,其分配器内融熔玻璃的温度、流量及拉引速度均较易被保持在固定状态,有效避免了传统‘溢流融合法’在利用两片薄板玻璃融结合成一片薄板玻璃时,因强烈的辐射冷却,造成两片薄板玻璃在融合成型上发生困难的缺点。虽然,本发明的方法及设备所生产出的薄板玻璃表面未若‘溢流融合法’的优良,惟由于表面的品质仅需经由初步研磨,即可轻易达到客户的要求,故本发明在成型后的设备及环境上要求不需特别严苛,因此,可大幅缩减维护及保养所需的成本。
一种利用狭长孔下拉法生产薄板材料的成型设备及方法。为提供一种制作优质大尺寸薄板材料、设备维修容易、成本低廉、有效提升生产效率的玻璃成型工艺及设备,提出本发明方法包括将均质热塑性材料导入流体分配管、沿流体分配管两侧长度方向以流量作线性递减且单位长度内流量一致被均匀分配至流体分配管的两侧以热塑性材料的静压力分布自动趋于平衡、垂直地向下流向衔接于流体分配管下方渠道内并使得均质热塑性材料能以一致的单位长度流量通过渠道底缘的出口;本发明设备包括供料管、连接在供料管下方的接头、对称连接在接头下方两侧的两个流体分配管及衔接于两个流体分配管底缘具有呈长方形截面槽口的渠道。
利用狭长孔下拉法生产薄板材料的成型设备及方法
- 专利详情
- 全文pdf
- 权力要求
- 说明书
- 法律状态
查看更多专利详情
下载专利文献
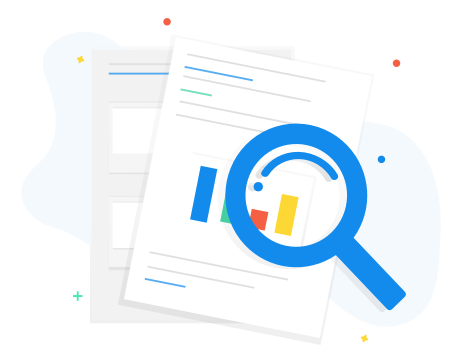
下载专利
同类推荐
-
张亚锋, 胡长坤张亚锋, 胡长坤张亚锋, 胡长坤崔桂玲
您可能感兴趣的专利
-
何玉明何玉明何玉明何玉明何玉明
专利相关信息
-
张柏清张柏清张柏清贾小平陈春雷, 施绍安