一种不含稀土永磁铁氧体材料的制备方法[0002]铁氧体是由铁族元素和其它一种或几种适当的金属元素组成的复合氧化物。具有六角晶系的磁铅石型铁氧体是一类永磁铁氧体,自1952年被研制出来以来,因具有优越的性价比、较高的饱和磁化强度和矫顽力、高的磁晶各向异性和居里温度、优良的化学稳定性等特点,使其应用范围十分广泛,可用于各种电装电机,家用电器马达,汽车电动升降电机、雨刮器电机等各类汽车部件电机,医疗设驱动马达,办公用品马达等各个领域。[0003]现制备铁氧体材料的方法主要有以下几种: (O陶瓷法又称氧化法,主要是将粉末状原材料按预设比例混合、高温预烧,经过高温固相反应形成块状再经过粗粉碎、二次细磨、成型、烧结等工序制备而成。该法是目前的工业化生产方法,主要特点是:工艺过程简单可控,生产成本较低。缺点是:粒径分布范围较宽、颗粒形貌不均、预烧温度较高。[0004](2)喷雾燃烧法,该法由盐类分解法和喷雾燃烧技术结合发展而来,主要是将金属盐溶液与液体燃料混合,在高温下以雾化状态喷射燃烧,溶液被瞬间加热分解,得到高纯度的超细铁氧体粉末,主要特点是:粉末粒径分布均匀、化学计量比精确、样品烧结温度低、纯度较高。缺点是:分解的气体具有腐蚀性、对环境产生污染、实验条件要求高。该法目前难以实现工业化生产。[0005](3)共沉淀法,主要是将一定浓度的金属盐溶液按预设的化学计量比均匀混合,用一定浓度的碱性溶液(NaOH、NH4OH等)作为沉淀剂,使金属离子沉淀,再将沉淀物过滤、水洗烘干后高温烧结得到产品。该法的特点是:粒度均匀、化学活性较好、固相反应温度低。缺点是:配方设计稀土离子掺杂时,离子的共沉淀较困难且均匀性较差,制备的颗粒较易团聚。[0006](4)水热法,该法是将共沉淀得到的强碱性悬浊液放入高压釜中加热到水的沸点以上和零界温度以下,使沉淀物之间发生反应得到铁氧体。该法的特点是:在水溶液中反应因而颗粒不易团聚,制备的铁氧体粉料分散性好、粒径分布窄、结晶性好。缺点是:原料纯度及设备要求高,另外水热反应不可控,容易生成杂相。[0007](5)溶胶凝胶法,是将金属盐溶液按化学计量比混合配制成溶液,再加入有机酸作配体,然后调节PH值,缓慢蒸发得到凝胶状前驱体,经过高温烧结得到铁氧体。该法的特点是:容易实现离子取代,粒径小且分布均匀。缺点是:成本高,样品容易开裂。不适用于工业化生产,目前主要用于实验室研究。
[0008] 现使用最为广泛的永磁铁氧体是具有M型六角晶系结构的Sr铁氧体(SrFe12O19)和Ba铁氧体(BaFe12O19),随着近年来各类马达电机要求小型化、轻量化、精密化,这就要求M型永磁铁氧体需要具有更高的磁性能。目前报导的提高M型永磁铁氧体磁性能有以下几种方式:1)通过离子取代Sr2+、Ba2+、Fe3+获得比Sr铁氧体和Ba铁氧体性能更优的铁氧体。如专利申请号为200610169039公布了一种La、Co取代Sr、Ba的铁氧体材料,专利所述在粗粉碎工序后加入两次微粉碎工序,第一次微粉碎将平均粒径磨至0.08-0.8 μ m,更优选为0.1-0.2 μ m,然后经过热处理将不足0.1 μ m的超微粉和较粗粉反应。第二次微粉碎将热处理后的粉末粉碎至0.8 μ m以下,更优选为0.1-0.2 μ m,如此细的粉末在磁场成型过程中是非常困难的,成型效率大大降低,另外该专利实施例中为获得Br4510Gs和Hcj 5585 Oe的性能,Co的替代量达到0.4,生产成本较高。再如专利申请号为201110153849公布了一种稀土取代的永磁铁氧体材料,其化学式为DhRx0.nFe2_y_zLnzCoy03,所述的永磁铁氧体材料与传统的永磁铁氧体AB12O19相比,A位和B位都部分被镧系元素取代,其中:D为Ca ,Ba和Sr元素中的一种、两种或三种,A位可以不包括La,B位可以不包含Co。实施例中3中D位取代使用了摩尔比为0.41的Nd和0.23的La,Ln使用了摩尔比为0.38的Gd和0.26的Co,磁性能Br=0.47T, He j=430kA/m,最大磁能积(BH)max=43.3 kj/m3的性能,但大量使用了昂贵的Nd2O3和Gd2O3,大幅增加了生产成本,失去了 M型永磁铁氧体高性价比的特性。
[0009]本发明的目的在于提供一种不含稀土永磁铁氧体材料的制备方法,利用熔盐作为固相反应的媒介,以制造不含稀土元素的高磁性能永磁铁氧体材料,具有材料成本低,综合性能优异的特点,本发明的制备方法具有反应温度低、能耗小的优点。
[0010]本发明解决其技术问题所采用的技术方案是:
一种不含稀土永磁铁氧体材料的制备方法,包括以下步骤:
(I)配料与混料
主成分按(l-x-y)Sr0.x Ca0.yBa0.nFe203 组成式,其中 0.1 < x < 0.5,
0.1 ^ y ^ 0.7,5 ^ n ^ 6.4 ;
准确称取主成分各原料以及主成分各原料总重量计10%-20%的熔盐进行湿式球磨得混合料;
经湿式球磨混合料的平均粒径优选为0.6-1 μ m。颗粒粒径小,表面积大,颗粒与熔盐接触面积越大有利于熔盐反应,提高扩散速率,降低反应时间和温度。
[0011](2)预烧
将步骤(1)的混合料在标准大气压条件下先在400-600°C范围内保温l_3h,再升温至900-1050°C保温1-5小时,冷却后干式破碎得到预烧料;
(3)洗料及细磨
将步骤(2)的预烧料称量后放入沉淀池加水搅拌洗涤,经洗涤沉淀后将料浆转入砂磨机,加入预烧料重量0.2-1%助磨剂和1-1.5%分散剂磨至平均粒径为0.5-1.5 μ m,再转入离心式球磨机中,并添加副成分球磨2.5-4h ;
该细磨工艺配合熔盐法可以较好控制细磨粒径,提高了细磨效率,粒径大小均匀,晶型完整,呈正态分布。本领域公知的,细磨粒径过细,平均粒径0.5μπι以下时,排水时间增加,成型效率显著降低,影响生产效率。粒径过粗,则剩磁和矫顽力会下降。
[0012](4)成型
将步骤(3)处理完成后的料浆沉淀,达到含水率为25-40%,在10000-14000GS磁场下成
型;(5)烧结
将步骤(4)得到的成型体在100°C _400°C下保温1-3小时,再升温至800_850°C,然后在升温至1050°C -1200°C,保温1-3小时。
[0013]本发明制得的钡永磁铁氧体材料为M型六角晶系铁氧体。
[0014]熔盐作为高温固相反应的媒介,本身不参与到固相反应当中。达到一定温度时,熔盐能呈现熔融状态,使各反应组分在液相中的流动性明显增加,反应物不局限于相邻物料的直接接触界面,还有沿着反应物颗粒的自由表面同时进行,使得扩散速率显著提高,这可以显著降低反应的时间和温度。本领域公知的,铁氧体材料的烧结温度高达1200-1300°C,经过发明人的大量实验表明,采用熔盐作为反应媒介,可以使烧结温度降低至900-1050°C左右,降低了能源消耗,这对生产过程中的节能效果十分明显。另一方面,熔盐熔融后溶解和包裹组分颗粒物料,减轻了颗粒之间的相互粘结,因此得到的预烧料粉体颗粒团聚较少,仅有轻微弱团聚。
[0015]目前高性能M型铁氧体的专利报道多集中在离子掺杂提高饱和磁化强度和磁晶各向异性以及加入添加剂改善磁体密度、取向度等方面提高磁性能。
[0016]实验和SEM分析表明, 具有六角型片状的晶形,预烧料磁体中晶体的厚径比(晶体粒径与厚度之比)为2.5-4.5的比例20%以上,优选50%以上,晶体平均粒径3 μ m左右,烧结磁体中的晶体厚径比为1.5-3.5的比例20%以上,优选为50%以上,晶体粒径1-1.2μπι左右的比例20%以上,优选为50%以上,可得到高的Br、Hcj。若厚径比过大,晶体沿C轴方向过度生长,六角型片状晶体过长过薄,根据公式Hcj=0.48 (Ha-NMs)退磁因子增加,退磁场增加,导致Hcj降低。若厚径比过小,晶体沿C轴方向生长不完全,六角片状晶体变厚变短,导致Br下降。
[0017]实验表明利用熔盐可以很好的控制晶体的形貌和尺寸,这与熔盐与反应物之间的表面能、界面能有关。反应初始阶段,反应物溶解与熔融盐中形成饱和溶液,反应生成铁氧体后,由于铁氧体不溶于熔融盐,经过缓慢降温,铁氧体逐渐从熔融盐中析出,形成六角片状M型铁氧体晶体,熔盐法制备的铁氧体六角型片状晶体生成率高,晶型完整符合高性能铁氧体的要求。
[0018]作为优选,所述助磨剂选自聚偏磷酸钠、六偏磷酸钠、硅酸钠、聚丙烯酸盐、乙二醇中的一种。
[0019]作为优选,所述分散剂选自葡萄糖酸钙、山梨糖醇中的一种。
[0020]作为优选,所述副成分包括CaCO3和SiO2,按照主成分各原料总重量计CaCO3添加量为0.5-1.5%,SiO2添加量为0.1-1%。CaCO3和SiO2,会形成CaSiO3,虽然它本身的熔点达到1540°C,但跟铁氧体结合以后,会显著降低达到1150°C左右,一方面能降低烧结温度,另一方面能促进烧结,增加磁体密度,提高剩磁,还可以抑制晶粒的过度长大,从而提高磁性倉泛。
[0021]作为优选,所述熔盐选自以下组合中的一种:NaBr +NaB02+KB02 (各自摩尔百分比:66%, 19%, 15%), K2CO3+ Na2B4O7+ Na2SO4 (各自摩尔百分比:30%,25%,4δ%),NaBr+KBr+NaB02(各自摩尔百分比:26%, 40%, 34%),NaBr+KBr+K2S04 (各自摩尔百分比:25%,35%,40%)。经过本发明人的大量探索实验表明,不同的熔盐对铁氧体晶体的影响十分显著,选取合适的熔盐对生成符合高性能铁氧体晶体十分重要。由于组合熔盐可以组合利用不同种类熔盐的优势,因此组合熔盐较单一熔盐更容易配比使用,组合熔盐中可以优选选用具有共晶的熔盐,共晶熔盐具有较低的熔点和高沸点,有助于方便搭配熔盐和较宽的温度调节空间。另外,选用的熔盐应具有较低的蒸汽压、低粘度、高表面张力的物理性质。因此本发明选用了上述特定的熔盐组合。
[0022]作为优选,步骤(5)中将步骤(4)得到的成型体在100°C _400°C下保温1_3小时,再以0.8-1.50C /min的升温速率升温至800_850°C,然后在以1.4-2.5°C /min的升温速率升温至1050°C -1200°C,保温1-3小时。在此烧结工艺下得到的晶粒厚径比为1.5-3.5的比例50%以上,晶体粒径1-1.2 μ m左右的比例可达50%以上,晶界清晰,晶型完整呈六角片状,符合高磁性能特征。
[0023]本发明的有益效果是:
采用本发明的工艺方法配合特定配比的主副成分制备的M型铁氧体,可获得4200-4300GS 左右的 Br,Hej3800-41000e 左右,(BH)max3.9-4.0MGOe 左右。
[0024]与现有技术相比,本发明具有以下独特的优点和创新之处:不同于传统方法依靠离子取代和引入添加剂等方法来提高磁性能,而着重于利用熔盐的独特优势及调整工艺方法对铁氧体微观晶体形貌、晶粒大小的控制来制备符合高性能永磁铁氧体材料。使用熔盐工艺法,较水热法、溶胶凝胶等方法具有工艺条件可控,无需增加额外设备,与传统固相法结合性强,利于工业化生产,反应温度低,能耗低等优点,通过调整熔盐种类和配比,烧结曲线的控制,得到高性能的永磁铁氧体。
[0025]下面通过具体实施例,对本发明的技术方案作进一步的具体说明。
[0026]本发明中,若非特指,所采用的原料和设备等均可从市场购得或是本领域常用的。下述实施例中的方法,如无特别说明,均为本领域的常规方法。
[0027]实施例1:将主成分原材料按(1-x-y) Sr0.x Ca0.yBa0.nFe203组成式。其中x=0.2,y=0.4, η=5.65称取重量(主成分原材料具体为:Fe203,SrC03,BaCO3, CaCO3),再称取熔盐:NaBr +NaB02+KB02(各自摩尔百分比:66%,19%,15%),熔盐重量按主成分各原料总重量计10%, —起放入球磨机中湿式球磨,球磨时间8小时(平均粒径0.6-1 μ m),将得到的混合料干燥后在大气条件下500°C保温2小时,再以3°C /分升温至990°C,保温3小时,降温后将预烧料用振动式破碎机破碎成粉末状,测得粒径D50为2.3 μ m,再将预烧料粉末称重后转入沉淀池中,用水多次洗涤沉淀后将料浆转入砂磨机,加入预烧料重量0.3%的聚偏磷酸钠和1.0%山梨糖醇,砂磨3小时,检测料浆D50为1.2 μ m,再转入离心式球磨机中,并加入SiO20.4%(主成分各原料总重量计),CaCO30.8%(主成分各原料总重量计),转速控制在500转/分,细磨2.5小时,料浆检测DlO为0.27ym,D50为0.71ym,D90为1.54 μ m将料浆转入沉淀池沉淀,使其含水量为35%左右,在用成型机湿式成型,成型磁场10000Gs-14000 Gs,成型压力5MPa,所得成型毛坯直径43.2mm,高度13 mm。将成型毛坯在350°C下保温I小时,以去除成型体中的水和分散剂,再升温至850°C左右,升温速率控制在1.50C /min,850°C以后升温速率控制在2.2°C/ min,然后在1198°C下,保温I小时,将烧结后的样品抽取表面研磨后测量磁性能(见表1)。
[0028]实施例2熔盐用量为主成分各原料总重量15%,其余同实施例1。[0029]实施例3熔盐用量为主成分各原料总重量20%,其余同实施例1。
[0030]实施例4熔盐组成为:K2C03+ Na2B4O7+ Na2SO4(各自摩尔百分比:30%,25%,45%),熔盐用量为主成分各原料总重量10%,预烧时以2°C /分升温至950°C,其余同实施例1。
[0031]实施例5熔盐用量为主成分各原料总重量15%,其余同实施例4。
[0032]实施例6熔盐用量为主成分各原料总重量20%,其余同实施例4。
[0033]实施例7将主成分原材料按(1-x-y) Sr0.x Ca0.yBa0.nFe203组成式。其中x=0.3, y=0.5, n=5.65称取重量,其余同实施例1。
[0034]实施例8熔盐用量为主成分各原料总重量15%,其余同实施例7。
[0035]实施例9熔盐用量为主成分各原料总重量20%,其余同实施例7。
[0036]实施例10将主成分原材料按(1-x-y) Sr0.x Ca0.yBa0.nFe203组成式。其中x=0.3, y=0.5, n=5.65称取重量,其余同实施例4。
[0037]实施例11熔盐用量为主成分各原料总重量15%,其余同实施例10。
[0038]实施例12熔盐用量为主成分各原料总重量20%,其余同实施例10。
[0039]对比例1:将主成分原材料按(1-x-y) Sr0.x Ca0.yBa0.nFe203组成式。其中x=0.2, y=0.4, n=5.65称取重量,放入球磨机中湿式球磨,球磨时间5小时,将得到的原料混合物干燥后在大气条件下再以4°C /分升温至1220°C分别保温3小时,降温后将预烧料用振动式破碎机破碎成粉末状,测得粒径D50为2.5 μ m,再将预烧料粉末及SiO20.4%(主成分原料总重量计)、CaC030.8% (主成分原料总重量计)、葡萄糖酸钙1.3% (预烧料重量计)加入球磨机中球磨18小时,料浆检测DlO为0.12 μ m、D50为0.80 μ m、D90为4.01 μ m,将料浆转入沉淀池沉淀,使其含水量为35%左右,在用成型机湿式成型,成型磁场10000GS-14000Gs,成型压力5MPa,所得成型毛坯直径43.2mm,高度13mm。将成型毛坯在350°C下保温I小时,以去除成型体中的水和分散剂,再升温至1200°C左右,升温速率控制在:TC /min,保温I小时,将烧结后的样品抽取表面研磨后测量磁性能(见表1)。
[0040] 对比例2:将主成分原材料按(1-x-y) Sr0.x Ca0.yBa0.nFe203组成式。其中x=0.3,y=0.5,n=5.65称取重量,其它同对比例I。
[0041]
一种不含稀土永磁铁氧体材料的制备方法
- 专利详情
- 全文pdf
- 权力要求
- 说明书
- 法律状态
查看更多专利详情
下载专利文献
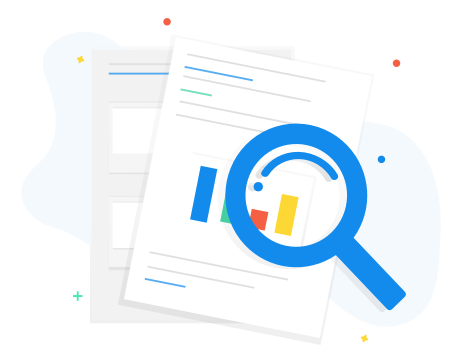
下载专利
同类推荐
-
齐锦刚齐锦刚牛德仲, 马德良
您可能感兴趣的专利
-
陈凯, 陈树德李小龙
专利相关信息
-
何玉明李明照许建益, 郑杰埃胡德·马罗姆, 迈克尔·米治里特斯基I·基拉伊I·基拉伊