氮化铝烧结助剂和制备方法及氮化铝陶瓷基片的制备方法 [0002]随着微电子技术的迅速发展,作为电绝缘材料的基板要求具有更高的热导率和优良的介电性能。氮化铝(AlN)陶瓷导热性能好,线膨胀系数与硅接近,体积电阻率高,介电常数和介电损耗小,无毒,耐高温和耐腐蚀,力学性能良好,是新一代半导体散热基片和电子器件封装的理想材料。由于氮化铝属于共价化合物,原子的自扩散系数小,一般在1800°C的高温下烧结才能获得致密的陶瓷材料;另一方面,由于Al和O具有很高的亲和力,O原子的进入会导致氮化铝晶格产生氧缺陷从而降低氮化铝陶瓷的热导率。目前的解决方法是添加少量的烧结助剂以实现致密化烧结并夺取晶格氧,以获得较高的热导率。目前采用的烧结助剂包括MgO、CaO、Li2O, Y2O3等氧化物,或者YF3、CaF2等氟化物。 [0003]专利CN951174622中采用了稀土金属氧化物或氟化物、碱土金属或碱金属氧化物以及III族氧化物中的两种或三种的组合作为烧结助剂,其烧结温度为1550°C至1800°C,烧结之间为2至6小时。这种制备方法烧结温度高,烧结周期过长,生产成本较高,整体热导率不高。
[0004]鉴于上述烧结温度高、烧结时间长的不足,本发明的目的是提供一种新的氮化铝烧结助剂及其制备方法,同时提供一种新的采用上述烧结助剂的氮化铝陶瓷基片的制备方法。 [0005]本发明的技术方案如下:
[0006]一种氮化铝烧结助剂,所述氮化铝烧结助剂为L1-B-Si共熔点氧化物和Mn-Cu共熔点氧化物的混合物,所述L1-B-Si共熔点氧化物和Mn-Cu共熔点氧化物之间的质量份数比为4~5:1~3 ;
[0007]其中所述L1-B-Si共熔点氧化物中L1、B和Si的摩尔比为:40~60:30~50:7~10,所述Mn-Cu共熔点氧化物中Mn和Cu的摩尔比为0.1~0.4:0.6~0.9。
[0008]其中,所述氮化铝烧结助剂的熔点为900-1100°C。
[0009]上述的氮化铝烧结助剂的制备方法,包括如下步骤:
[0010](1)配料:按上述比例分别配制Li2O-B2O3-S12的第一混合粉末以及MnCO3-CuO的第二混合粉末;将所述第一混合粉末和所述第二混合粉末按上述比例混合均匀得到原料粉末;
[0011](2)球磨:将配制好的原料粉末装入球磨罐中,再装入无水乙醇和磨球后进行球磨处理,其中原料粉末与无水乙醇的质量份数比为1:2~4,球磨时间为5~7小时;
[0012](3)烘料:将所述球磨处理后的得到的粉料置于110°C~130°C的烘箱中进行烘干处理得到烘干粉末;
[0013](4)过筛:将所述烘干粉末进行过筛处理得到过筛粉末;
[0014](5)预烧:将所述过筛粉末在空气气氛中在500°C至700°C下烧结即可得到所述氧化铝烧结助剂。
[0015]本发明还提供一种氮化铝陶瓷基片的制备方法,包括如下步骤:
[0016](I)配制氮化铝陶瓷粉体:在氮化铝粉体中加入烧结助剂,搅拌均匀即可得到氮化铝陶瓷粉体;其中所述烧结助剂为权利要求1或2所述的氮化铝烧结助剂;
[0017](2)制备浆料:在溶剂中依次加入分散剂、步骤⑴制得的氮化铝陶瓷粉体、粘结剂以及增塑剂并进行球磨处理和真空除泡处理,得到混合均匀的浆料混合物;
[0018](3)制备陶瓷生坯片:将所述浆料混合物通过流延成型机制成陶瓷生坯带;对所述陶瓷生坯带进行干燥处理制得固体生坯带,之后将固体生坯带裁制成坯片得到陶瓷生坯片;
[0019](4)排胶:将所述陶瓷生坯片放入排胶炉中进行排胶处理得到排胶陶瓷生坯片;
[0020](5)烧结:将所述排胶陶瓷生坯片进行微波烧结即可得到氮化铝陶瓷基片,微波烧结处理中烧结温度为1300°C至1450°C,保温时间为20分钟至40分钟。
[0021]其中,步骤⑴中,所述氮化铝粉体与所述烧结助剂的质量份数比为100:2~9。
[0022]其中,所述分散剂为BYK-180,所述粘结剂为PVB,所述增塑剂为DBP和PEG。
[0023]其中,所述氮化铝粉体、所述分散剂、所述粘结剂、所述增塑剂和所述溶剂的质量份数比为100:3~8:5~8:2.5~4:40~70。
[0024]其中,所述溶剂为无水乙醇和丁酮的混合物,所述无水乙醇和所述丁酮的份数比为 1:1。
[0025]其中,步骤(3)中所述干燥处理为将所述陶瓷生坯带附着在PET膜上,使所述PET膜以一定的速率进入烘干通道,所述烘干通道的温度为25°C至75°C,干燥处理的时间为30分钟至40分钟。
[0026]其中,步骤(5)中,所述烧结温度为1400±100°C,保温时间为30±5分钟。
[0027]本发明的有益效果是:
[0028](I)本发明的烧结助剂成本低,制备方法简单;
[0029](2)本发明的氮化铝陶瓷基片的制备方法采用了上述烧结助剂,降低了烧结温度,缩短了烧结时间;
[0030](3)本发明的氮化铝陶瓷基片的制备方法采用了微波烧结,微波烧结起到了抑制氮化铝氧化的作用;
[0031](4)本发明的氮化铝陶瓷基片的制备方法制备的产品微观结构优良,晶粒细小,分布均匀,在晶界处有液相包裹,整体致密度高,热导率能达到220W/(m.K)。
[0032]为了使本发明的目的、技术方案及优点更加清楚明白,以下结合具体实施例,对本发明进行进一步详细说明。
[0033]需要说明的是,在不冲突的情况下,本申请中的实施例及实施例中的特征可以相互组合。
[0034]氮化铝属于共价化合物,自扩散系数小,烧结致密化非常困难,烧结成本非常高,这阻碍了氮化铝的推广应用。由于纯净的氮化铝粉末烧结温度非常高,加上在烧结中由于氮化铝对氧有很强的亲和力,部分氧会融入氮化铝晶格中形成铝空位,导致了热导率下降。由此高温烧结的氮化铝的缺点在于生产成本高,产品含氧量高。再者,目前人们对节能减排的要求越来越高。因此,氮化铝的低温烧结是必然的发展方向。所谓低温烧结是指将氮化铝的烧结温度降低1600°C及以下实现致密度高的烧结。一般的氮化铝表层的氧在高温下才开始向其晶格内部扩散的,因此,低温烧结的另一个好处是延缓高温烧结时表层氧向氮化铝晶格内部扩散,增进后续热处理过程中的排氧效果,有利于制备出高热导率的陶瓷材料。
[0035]为了降低氮化铝的烧结温度,本发明提供了一种新的氮化铝烧结助剂,该氮化铝烧结助剂为L1-B-Si共熔点氧化物和Mn-Cu共熔点氧化物的混合物,所述L1-B-Si共熔点氧化物和Mn-Cu共熔点氧化物之间的质量份数比为4~5:1~3。L1-B-Si共熔点氧化物为Li2O-B2O3-S12共熔点氧化物,Mn-Cu共熔点氧化物为MnCO3-CuO的共熔点氧化物。本实施例中的氮化铝烧结助剂为L1-B-Si共熔点氧化物和Mn-Cu共熔点氧化物的混合物,其中所述L1-B-Si共熔点氧化物中L1-B-S i的摩尔比为:40~60:30~50:7~10,Mn-Cu共熔点氧化物中Mn-Cu的摩尔比为0.1~0.4:0.6~0.9。
[0036]其中,所述氮化铝烧结助剂的熔点为900~1100°C。
[0037]上述氮化铝烧结助剂的制备方法,包括如下步骤:
[0038](I)配料:按上述比例分别配制Li2O-B2O3-S12的第一混合粉末以及MnCO3-CuO的第二混合粉末;将所述第一混合粉末和所述第二混合粉末按上述比例混合均匀得到原料粉末;即将Li20、B2O3和S12三种原料按上述比例混合均匀即可得到第一混合粉末,将MnCO3和CuO按上述摩尔比称量并混合均匀即可得到第二混合粉末,之后再将第一混合粉末和第二混合粉末混合均匀即可得到原料粉末;
[0039](2)球磨:将配制好的原料粉末装入球磨罐中,再装入无水乙醇和磨球后进行球磨处理,其中原料粉末与无水乙醇的质量份数比为1:2~4,球磨时间为5~7小时;本实施例中球料比为10~20:1。
[0040](3)烘料:将所述球磨处理后的得到的粉料置于110°C~130°C的烘箱中进行烘干处理得到烘干粉末;本步骤中烘干处理的同时去除粉料中的无水乙醇;
[0041](4)过筛:将所述烘干粉末进行过筛处理得到过筛粉末;过筛处理采用的是150目至250目(最好为200目)的筛网。
[0042](5)预烧:将所述过筛粉末在空气气氛中在500°C至700°C下烧结即可得到所述氧化铝烧结助剂。本步骤中烧结温度最好为600°C。
[0043]进一步的,本发明还提供一种氮化铝陶瓷基片的制备方法,包括如下步骤:
[0044](I)配制氮化铝陶瓷粉体:在氮化铝粉体中加入烧结助剂,搅拌均匀即可得到氮化铝陶瓷粉体;其中所述烧结助剂为上述的氮化铝烧结助剂;
[0045](2)制备浆料:在溶剂中依次加入分散剂、步骤⑴制得的氮化铝陶瓷粉体、粘结剂以及增塑剂并进行球磨处理和真空除泡处理,得到混合均匀的浆料混合物;
[0046](3)制备陶瓷生坯片:将所述浆料混合物通过流延成型机制成陶瓷生坯带;对所述陶瓷生坯带进行干燥处理制得固体生坯带,之后将固体生坯带裁制成坯片得到陶瓷生坯片;
[0047](4)排胶:将所述陶瓷生坯片放入排胶炉中进行排胶处理得到排胶陶瓷生坯片;
[0048](5)烧结:将所述排胶陶瓷生坯片进行微波烧结即可得到氮化铝陶瓷基片,本步骤中的烧结温度为1300°C至1450°C,保温时间为20分钟至40分钟。
[0049]进一步的,步骤(1)中,所述氮化铝粉体与所述烧结助剂的质量份数比为100:2~
9。即所述氮化铝粉体以100份为基数,氮化铝烧结助剂为2~9份。
[0050]进一步的,所述分散剂为BYK-180,所述粘结剂为PVB,所述增塑剂为DBP和PEG。
[0051]进一步的,所述氮化铝粉体、所述分散剂、所述粘结剂、所述增塑剂和所述溶剂的质量份数比为100:3~8:5~8:2.5~4:40~70。即所述氮化铝粉体以100份为基数,所述分散剂为3~8份,粘结剂为5~8份,增塑剂为2.5~4份,溶剂为40~70份。
[0052]进一步的,所述溶剂为无水乙醇和丁酮的混合物,所述无水乙醇和所述丁酮的份数比为1:1。
[0053]进一步的,步骤(3)中所述干燥处理为将所述陶瓷生坯带附着在PET膜上,使所述PET膜以一定的速率进入烘干通道,所述烘干通道的温度为25°C至75°C,干燥处理的时间为30分钟至40分钟。
[0054]进一步的,步骤(5)中,所述烧结温度为1400±100°C,保温时间为30±5分钟。
[0055]本发明的氮化铝的制备方法采用了新的烧结助剂和新的烧结方法,与以往的制备方法相比,烧结温度降低至1300°C至1450°C,烧结时间大大缩短为20分钟至40分钟,达到了致密烧结,工艺和设备简单,同时烧结温度较低可以保证基片表面的平整度和粗糙度。显微结构显示采用本发明的制备方法制备的氮化铝陶瓷基片晶粒细小且分布均匀,其热导率高达220W/(m.K)。烧结后的陶瓷呈黑褐色,经研究发现黑褐色的陶瓷基板比传统的白色基板更有利于吸热和散热。
[0056]下面具体介绍本发明的具体实施例。
[0057]以下实施例中除烧结助剂外,其余原料均为市售,所采用的设备均为市售。
[0058]制备烧结助剂实施例一
[0059]包括如下步骤:
[0060](I)配料:按一定比例分别配制Li2O-B2O3-S12的第一混合粉末(即原料为Li20、B2O3和S12)以及MnCO3-CuO的第二混合粉末(即原料为MnCO3和CuO);将所述第一混合粉末和所述第二混合粉末按上述比例混合均匀得到原料粉末;本步骤中L1、B和Si元素的摩尔比为:40:30:10 ;Mn和Cu的摩尔比为0.1:0.9,本实施例中所述L1-B-Si共熔点氧化物和Mn-Cu共熔点氧化物之间的质量份数比为4:1。
[0061](2)球磨:将配制好的原料粉末装入球磨罐中,再装入无水乙醇和磨球后进行球磨处理,其中原料粉末与无水乙醇的质量份数比为1:2,球磨时间为5小时;球料比为10:1 ;
[0062](3)烘料:将所述球磨处理后的得到的粉料置于110±5°C的烘箱中进行烘干处理得到烘干粉末;
[0063](4)过筛:将所述烘干粉末进行过筛处理得到过筛粉末;
[0064](5)预烧:将所述过筛粉末在空气气氛中在500±10°C下烧结即可得到所述氧化铝烧结助剂。
[0065]制备烧结助剂实施例二
[0066]包括如下步骤:
[0067](I)配料:按一定比例分别配制Li2O-B2O3-S12的第一混合粉末以及MnCO3-CuO的第二混合粉末;将所述第一混合粉末和所述第二混合粉末按上述比例混合均匀得到原料粉末;本步骤中L1、B和Si元素的摩尔比为:50:40:8 ;Mn和Cu的摩尔比为0.2:0.8。本实施例中所述L1-B-Si共熔点氧化物和Mn-Cu共熔点氧化物之间的质量份数比为3:2
[0068](2)球磨:将配制好的原料粉末装入球磨罐中,再装入无水乙醇和磨球后进行球磨处理,其中原料粉末与无水乙醇的质量份数比为1:3,球磨时间为7小时;球料比为15:1 ;
[0069](3)烘料:将所述球磨处理后的得到的粉料置于120±5°C的烘箱中进行烘干处理得到烘干粉末;
[0070](4)过筛:将所述烘干粉末进行过筛处理得到过筛粉末;
[0071](5)预烧:将所述过筛粉末在空气气氛中在600±10°C下烧结即可得到所述氧化铝烧结助剂。
[0072]制备烧结助剂实施例三
[0073]包括如下步骤:
[0074](1)配料:按一定比例分别配制Li2O-B2O3-S12的第一混合粉末以及MnCO3-CuO的第二混合粉末;将所述第一混合粉末和所述第二混合粉末按上述比例混合均匀得到原料粉末;本步骤中L1、B和Si元素的摩尔比为60:50:7 ;Mn和Cu的摩尔比为0.4:0.6。本实施例中所述L1-B-Si共熔点氧化物和Mn-Cu共熔点氧化物之间的质量份数比为5:3
[0075](2)球磨:将配制好的原料粉末装入球磨罐中,再装入无水乙醇和磨球后进行球磨处理,其中原料粉末与无水乙醇的质量份数比为1:4,球磨时间为6小时;球料比为20:1 ;
[0076](3)烘料:将所述球磨处理后的得到的粉料置于125±5°C的烘箱中进行烘干处理得到烘干粉末;
[0077](4)过筛:将所述烘干粉末进行过筛处理得到过筛粉末;
[0078](5)预烧:将所述过筛粉末在空气气氛中在700°C下烧结即可得到所述氧化铝烧结助剂。
[0079]氮化铝陶瓷基片的制备实施例一
[0080](1)配制氮化铝陶瓷粉体:在氮化铝粉体中加入烧结助剂,搅拌均匀即可得到氮化铝陶瓷粉体;本实施例中氮化铝粉体的粒径为2um,氮化铝粉体以100份为基数,氮化铝烧结助剂为2份;
[0081](2)制备浆料:在溶剂中依次加入分散剂、步骤⑴制得的氮化铝陶瓷粉体、分散剂、粘结剂以及增塑剂并进行球磨处理和真空除泡处理,得到混合均匀的浆料混合物;本步骤中分散剂为ΒΥΚ-180(德国毕克公司生产),粘结剂为PVB,增塑剂为DBP和PEG ;溶剂为无水乙醇和丁酮的混合物(无水乙醇和丁酮的份数比为1:1);本实施例中所述氮化铝粉体以100份为基数,所述分散剂为3份,粘结剂为5份,增塑剂为2.5份,溶剂为70份。DBP和PEG的质量份数比为1:1。
[0082]本步骤中球磨处理采用球磨机,球磨处理的时间为36小时,球磨处理后得到物料混合均匀的初级流延浆料;然后对初级流延浆料进行真空除泡处理即可得到适于流延成型用的浆料混合物。
[0083](3)制备陶瓷生坯片:采用流延成型工艺,将所述浆料混合物通过流延成型机制成0.2~Imm厚的陶瓷生坯带;对所述陶瓷生坯带进行干燥处理制得固体生坯带,之后将固体生坯带裁制成坯片得到陶瓷生坯片;所述干燥处理的具体操作步骤为将所述陶瓷生坯带附着在PET膜上,使所述PET膜以一定的速率进入烘干通道,所述烘干通道中通入温度为25°C至75°C的热风,干燥处理的时间为30分钟至40分钟,PET膜的速率为120~300cm/
mir1
[0084](4)排胶:将所述陶瓷生坯片放入排胶炉中进行排胶处理得到排胶陶瓷生坯片;排胶处理的温度为250°C至600°C,排胶处理在还原气氛中进行,排胶处理的目的是排除生坯中的各种有机物,获得不含残余碳的排胶陶瓷生坯片;
[0085](5)烧结:将所述排胶陶瓷生坯片进行微波烧结即可得到氮化铝陶瓷基片。具体操作步骤是将排胶陶瓷生坯片放入微波烧结炉中,使微波烧结炉快速升温至烧结温度,一般在10分钟内升温至烧结温度。本步骤中的烧结温度为1300°C,保温时间为40分钟。本步骤中的微波烧结在微波烧结炉中进行。
[0086]实施例二
[0087]本实施例中步骤(1)中氮化铝粉体的粒径为3um,氮化铝粉体以100份为基数,氮化铝烧结助剂为6份;
[0088]本实施例中步骤⑵中分散剂为BYK-180,粘结剂为PVB,增塑剂为DBP和PEG ;溶剂为无水乙醇和丁酮的混合物(无水乙醇和丁酮的份数比为1:1);本实施例中所述氮化铝粉体以100份为基数, 所述分散剂为5份,粘结剂为6份,增塑剂为3份,溶剂为50份。DBP和PEG的质量份数比为1:1.5。
[0089]本实施例中步骤(5)中的烧结温度为1400°C,保温时间为30分钟。
[0090]其余步骤与实施例一相同。
[0091]实施例三
[0092]本实施例中步骤(1)中氮化铝粉体的粒径为5um,氮化铝粉体以100份为基数,氮化铝烧结助剂为9份;
[0093]本实施例中步骤⑵中分散剂为BYK-180,粘结剂为PVB,增塑剂为PEG和DBP ;溶剂为无水乙醇和丁酮的混合物(无水乙醇和丁酮的份数比为1:1);本实施例中所述氮化铝粉体以100份为基数,所述分散剂为8份,粘结剂为8份,增塑剂为4份,溶剂为40份。且PEG和DBP的份数比为1:2。
[0094]本实施例中步骤(5)中的烧结温度为1450°C,保温时间为20分钟。
[0095]其余步骤与实施例一相同。
[0096]以上所述实施例仅表达了本发明的几种实施方式,其描述较为具体和详细,但并不能因此而理解为对本发明专利范围的限制。应当指出的是,对于本领域的普通技术人员来说,在不脱离本发明构思的前提下,还可以做出若干变形和改进,这些都属于本发明的保护范围。因此,本发明专利的保护范围应以权利要求为准。
氮化铝烧结助剂和制备方法及氮化铝陶瓷基片的制备方法
- 专利详情
- 全文pdf
- 权力要求
- 说明书
- 法律状态
查看更多专利详情
下载专利文献
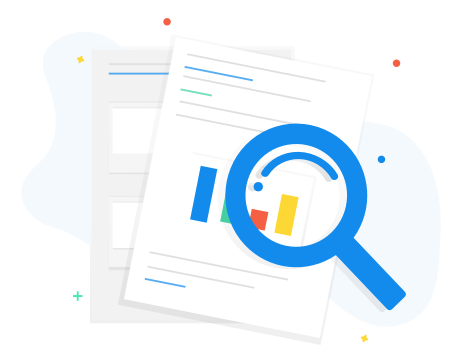
下载专利
同类推荐
-
王艳辉熊刚陈继新马塞路斯·皮苛特
您可能感兴趣的专利
-
王刚C·J·黄, A·J·皮兹克付伟峰, 窦涛
专利相关信息
-
余仲达张乃从