一种通用母模成型平台的制作方法[0002]目前,对于塑性混凝土预制部品的生产装置主要是平模装置和成组立模装置。[0003]利用平模装置来生产预制部品,最大的特征就是将混凝土预制部品最大的成型幅面呈水平状态放置成型,以结构最简单的长方体条形墙板为例,就是将以长度、宽度围成的最大成型幅面呈水平状态放置成型。利用平模装置来生产预制部品最为普遍,但在很多方面存在着很大的不足:(D基本上是靠手工来完成各种操作,生产效率低呈水平状态放置最大的成型幅面中的上面大多是利用手工抹面而成,大幅面的上面成型质量差;?平模生产需平放成型,模具占地面积大,需要生产场地面积较大。[0004]利用立模装置来生产预制部品,最大的特征就是将混凝土预制部品最大的成型幅面呈竖立状态放置,以结构最简单的长方体条形墙板为例,就是将以长度、宽度围成的最大成型幅面呈竖立状态放置。在实际操作过程中,“立模生产”与“平模生产”比,虽然机械化程度有所提高,生产效率也有了较大幅度地提升,但是这种传统“立模生产”本身仍存在以下不足:①所成型构件在成型模体内滞留时间过长,因为成型构件自身需要达到一定的脱模强度方可脱离模腔。这样一来,整体生产节奏较慢,制约了生产效率地提高。?所能
生产构件的灵活性差。一种立模只能生产相对应的一种品种类别的预制构件。当需要生产多种类别、多种不同规格尺寸的预制部品时,根本无法实现。
[0005]本发明的目的正是针对上述现有技术所存在的不足之处而提供一种能同时满足生产多种类别、多种不同规格尺寸的混凝土预制部品的通用母模成型平台。具体地讲,本发明的通用母模成型平台具有兼容性强的通用成型空腔和功能集中的特点,可与多种品种规格不同的可组合个性子模进行组配,从而以最低的成本来实现多种品种类别、多种不同规格尺寸的混凝土预制部品的生产。因此,本发明不仅极大地提高混凝土部品成型的灵活性及成型设备的适用范围;同时,可组合个性子模承载着成型部品只需在通用母模成型平台内稍经短期养护即可与之分离,故可以极大的缩短成型部品在通用母模成型平台的通用成型模腔中的养护时间、大大缩短了脱模时间、极大地提高设备的使用效率、大大缩短整个生产周期、提高成型部品的生产效率。
[0006]本发明的目的可通过下述技术措施来实现: 本发明的通用母模成型平台包括底部设置有动力行走系统的矩形结构的底盘,设置在底盘上的可组合个性子模的支承框架,对称设置在支承框架左、右立柱内侧的横向开合式左、右侧模,以与开合式左、右侧模相平行的方式设置在开合式左、右侧模之间并与底盘相固接的中隔板,所述开合式左、右侧模分别通过侧模开合油缸与相应侧支承框架的立柱相结合;在支承框架的左立柱与中隔板之间、右立柱与中隔板之间的底盘上分别设置有用于实现成型底模纵向位移运动的平面滚道或滑道;在开合式左、右侧模以及中隔板的上方通过与支承框架的中间横梁相连接的上模升降油缸安装有上模;在由中隔板与开合式左、右侧模之间的腔体组成的可变间距的左、右成型模腔的前端通过与支承框架的上横梁相连接的前端模升降油缸设置有插入式前端模,在左、右成型模腔的后端设置有翻转式后端模。
[0007]本发明在所述上模顶部设置有带有震动装置的振动架,所述振动架通过连接件与安装在上横梁上的振动架升降油缸相结合。
[0008]本发明中所述翻转式后端模的下端通过铰接方式与底盘,翻转式后端模的中上部两侧分别与后端模翻转油缸相连接。
[0009]本发明的成型平台还包括辅助实现部品成型所需控制系统、震动系统、压力浇注系统以及温度控制系统。由中隔板与开合式左、右侧模之间的腔体组成的可变间距的左、右成型模腔可以与多种品种类别、尺寸规格不同的可组合个性子模进行有机组配后共同围成多品种、多规格的混凝土部品形状完全吻合的浇注空腔。可组合个性子模进入所述通用母模成型平台的通用成型模腔时是通过可组合个性子模的支承架承载的成型衬模、前端衬模、后端衬模、沿着滚道或滑道纵向滚动或滑动的成型底模来实现的。可组合个性子模承载着成型部品经短暂的腔内初期养护后,可组合个性子模的支承架沿着设置在通用母模成型平台底盘上的滚道或滑道通过滚动或滑动纵向移出通用母模成型平台,完全脱离成型模腔而进行转移养护,而通用母模成型平台则分离出来进入循环利用。
[0010]本发明的原理及有益效果如下:
从上述可以看出,利用本发明来生产品种类别不同、尺寸规格不同的混凝土预制部品时,只需将相应的可组合个性子模与通用母模成型平台的通用成型模腔中通过有机组配后共同围成与混凝土部品形状完全吻合的浇注成型模腔;然后浇注料浆;后经短暂的初期养护,可组合个性子模承载着成型部品移出通用母模成型平台来实现。同时借助通用母模成型平台中的控制系统、动力系统、行走系统、开合系统、震动系统、压力浇注系统以及温度控制系统来辅助配合相应生产环节的自动化操作。
[0011]综上所述,本发明的通用母模平台具有兼容性强的通用成型空腔和功能集中的特点,可与多种规格的可组合个性子模进行组配,从而以最低的成本来实现多种品种类别、多种不同规格尺寸的混凝土预制部品的生产。因此,本发明不仅极大地提高混凝土部品成型的灵活性及成型设备的适用范围;同时,可组合个性子模承载着成型部品只需在通用母模平台内稍经短期养护即可与之分离,故可以极大的缩短成型部品在通用母模平台的模腔中的养护时间、大大缩短了脱模时间、极大地提高设备的使用效率、大大缩短整个生产周期、提闻成型部品的生广效率。
[0012]图1是本发明的结构主视图。[0013]图2是图1的左视图。
[0014]图3是图1的俯视图。
[0015]图4是本发明与可组合个性子模进行模腔组配前后的状态示意图。
[0016]图5是图4的俯视图。
[0017]图6是向组配模腔中浇注料浆时和模内初养后子母模分离时的状态示意图。
[0018]图7是图6的俯视图。
[0019]图中序号:件I——动力行走系统;件2——底盘;件3——滚道或滑道;件4——
上骨架;件5-开合式左、右侧模;件6-中隔板;件7-上模;件8-插入式前端
模;件9——前端模定位块;件10——翻转后端模;件11——铰链;件12——振动架;件13——振动装置;件14——支撑框架;件15——成型底模;件16——成型衬模;件17——前端衬模;件18——后端衬模;件19——活连件;件20——成型部品;件(5-1)——侧模开合油缸;件(7-1)——上模升降油缸;件(8-1)——前端模升降油缸;件(10-1)——后端模翻转油缸;件(12-1)——振动架升降油缸;HDMHM——后端模合模状态;HDMDK——后端模打开状态。
[0020]本发明以下将结合实施例(附图1?7)作进一步描述:
如图1?图3所示,本发明通用母模成型平台包括底部设置有动力行走系统(I)的矩形结构的底盘(2),设置在底盘(2)上的可组合个性子模的支承框架(14),对称设置在支承框架左、右立柱内侧的横向开合式左、右侧模(5),以与开合式左、右侧模(5)相平行的方式设置在开合式左、右侧模(5)之间并与底盘(2)相固接的中隔板(6),所述开合式左、右侧模(5)分别通过侧模开合油缸(5-1)与相应侧支承框架的立柱相结合;在支承框架的左立柱与中隔板(6)之间、右立柱与中隔板(6)之间的底盘(2)上分别设置有用于实现成型底模
(15)纵向位移运动的平面滚道或滑道(3);在开合式左、右侧模(5)以及中隔板(6)的上方通过与支承框架的中间横梁相连接的上模升降油缸(7-1)安装有上模(7);在由中隔板(6)与开合式左、右侧模(5 )之间的腔体组成的可变间距的左、右成型模腔的前端通过与支承框架的上横梁相连接的前端模升降油缸(8-1)设置有插入式前端模(8),在左、右成型模腔的后端设置有翻转式后端模(10);在所述上模(7)顶部设置有带有震动装置(13)的振动架
(12),所述振动架(12)通过连接件与安装在上横梁上的振动架升降油缸(12-1)相结合。
[0021]本发明中所述翻转式后端模(10)的下端通过铰接方式与底盘(2),翻转式后端模
(10)的中上部两侧分别与后端模翻转油缸(10-1)相连接(参见图2)。
[0022]所述通用母模成型平台还包括辅助实现部品成型所需控制系统、压力浇注系统以及温度控制系统。所述通用母模成型平台的通用成型空腔中可以与多种品种类别、尺寸规格不同的可组合个性子模进行有机组配后共同围成多品种、多规格的混凝土部品形状完全吻合的浇注空腔。
[0023]本发明的具体操作使用情况如下(如图4?图7所示):
1、模腔组配(如图4、图5所示):选取与成型部品(20)对应的可组合个性子模(包括支撑框架14、成型底模15、成型衬模16、前端衬模17、后端衬模18、活连件19等,在同日申请的另一专利中有详细说明,此处不再具体介绍),并沿着设置在通用母模成型平台的底盘(2)上部的滚道或滑道(3)通过滚动或滑动纵向平移使之进入通用成型母模平台中的通用成型空腔中,直到前端的端衬模(17)与已经沿着前端模定位块(9)向下移动到位的插入式前端模(8)相贴合,可组合个性子模长度方向组配到位。
[0024]2、合模(如图4、图5所示):然后,将翻转后端模(10)通过翻转进行合模,直到与后端衬模(18)相贴。开合式左、右侧模(5)在液压或机械动力的作用下向内侧移动或翻转进行合模,直到夹紧可组合个性子模宽度方向的侧面;上模(7)在液压或机械动力的作用下下移,直到压紧开合式左、右侧模(5)、成型衬模(16)、前端衬模(17)、后端衬模(18)的上平面为止;此时,由开合式左、右侧模(5)、插入式前端模(8)、翻转后端模(10)、上模(7)共同围成的通用成型空腔与可组合个性子模组配成同混凝土成型部品(20)的外形完全吻合的封闭浇注成型空腔。
[0025]3、浇注(如图6、图7所示):启动控制系统中的浇注程序,料浆通过泵车、浇注管道经通用母模成型平台的上模(7)中的通用浇注孔进入浇注成型空腔。
[0026]4、震动(如图6、图7所示):由震动装置产生特定频率的震动来震击模腔中的料浆使之流动均匀、布料密实。
[0027]5、部品成型:待料浆注满浇注成型空腔后会慢慢初凝,并成型出外形与封闭浇注成型空腔完全吻合的所需部品(20)。
[0028]6、开模(如图6、图7所示):开合式左、右侧模(5)在液压或机械动力的作用下向外侧移动;上模(7)在液压或机械动力的作用下上移;此时,可组合个性子模、成型部品与开合式左、右侧模(5)和上模(7)之间各拉开一定的脱模空隙。
[0029]7、子母模分离:可组合个性子模承载着成型部品(20)沿经短暂的腔内初期养护后,便可沿滚道或滑道(3)通过滚动或滑动纵向移出通用母模成型平台,完全脱离母模成型模腔而转移到特定的养护场所进行较长周期的后期养护;而通用成型母模平台则首先分离出来并经清模、涂隔离剂等预处理工序后与新的可组合子模重新组配进入下一轮生产中循环使用。
[0030]8、子模与成型部品分离:后期养护到足够的强度后,可组合个性子模与成型部品进行分离。可组合个性子模经清模、涂隔离剂等预处理工序后可以与通用母模成型平台进行重新组配进入新一轮生产中循环利用。
一种通用母模成型平台制作方法
- 专利详情
- 全文pdf
- 权力要求
- 说明书
- 法律状态
查看更多专利详情
下载专利文献
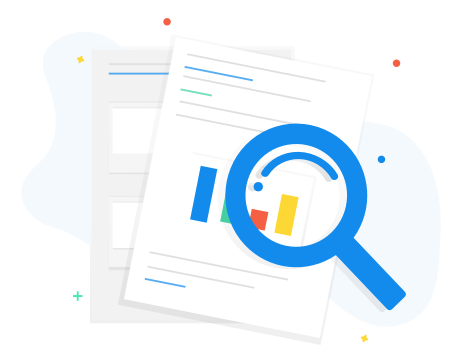
下载专利
同类推荐
-
彭威秦升益秦升益秦升益沈忠山王小锋
您可能感兴趣的专利
-
李欢欢迈克尔·R·贝里根迈克尔·R·贝里根孟宪安慧 张, 李洪盛
专利相关信息
-
刘必成方世峰, 张锦安井英明, 丸山刚安井英明, 丸山刚