一种自供氧永磁铁氧体预烧料单孔径坯料的制备与烧结的制作方法【技术领域】[0001]本发明属于磁性功能材料制备【技术领域】,特别涉及到一种自供氧型永磁铁氧体预烧料单孔径坯料的制备与烧结工艺。[0002]M型永磁铁氧体属六方晶系,因其具有很高的单轴磁晶各向异性、优越的性价比、较高的居里温度以及化学稳定性等特点,被作为一种重要的永磁材料和磁记录材料,广泛应用于家电、计算机、汽车、通信等各个领域。[0003]近年来随着产品小型化、轻型化、薄型化与环保节能要求的不断提高,使得永磁铁氧体材料的需求量大大的增加。故探索和研发单批次成产更大量的永磁铁氧体材料及其制备技术,对满足工业化使用需求,具有重要的意义,一直以来也都是磁性材料研究领域的重点之一 O[0004]目前生产铁氧体预烧料的主要工艺是:原料配比一混料球磨一压坯一烧结一制粉。其中在压坯环节,为了提高铁氧体坯料的充分烧结,通常所制备的坯饼需要保持有孔径,即所压制的坯饼并非完整的圆柱体,而是中心有单一孔径。这样能再一定程度上保持坯料中铁氧体与氧气接触的表面积,提高烧结后材料的性能均匀性;但是,目前通用的单一的孔径坯料,实际生产过程中,由于烧结炉中不同位置的温度和空气密度不同,最终的成品预烧料有些区域并未烧结完全,影响了同批次产品的性能。若是将坯料的孔径数量增加,虽然能够加烧结过程中坯 料的供氧量,但是单批次烧结生产的铁氧体预烧料产量却大大的减小,不利于节能环保,能源高效的利用。[0005]目前单一的孔径坯料,制备永磁铁氧体预烧料,其一次预烧料的产品性能仅达到剩磁4值达到≤200mT,内禀矫顽力H。」值达到≤125kA/m,磁能积(BH)max值达到≤18.7kJ/m3 ;从而影响了采用该预烧料进行二次添加后的磁材的性能。采用本发明制备的预烧料,并辅助二次添加制备的高性能永磁铁氧体材料剩磁B,值达到> 392mT,内禀矫顽力H。」值达到≤ 343.lkA/m,磁能积(BH)max 值达到≤ 27.9kJ/m3。
[0006]本发明旨在提供一种工艺相对简单、成本相对较低且利于工业化批量生产的高性能永磁铁氧体材料及其制备方法,通过该方法制备的高性能永磁铁氧体材料具有较高的剩磁、内禀矫顽力和最大磁能积。
[0007]为达到上述目的,本发明所采用的技术方案为:
[0008]一种自供氧型永磁铁氧体预烧料单孔径坯料的制备与烧结工艺,其特征在于:所述的永磁铁氧体材料是六角晶系,其化学结构式为SivxBax0.nFe
(12—y)/nRy/n〇3, 其中
O≤X≤0.998,5.75≤η≤6.15,0〈y≤0.6,R为Mn ;其具体的制备方法包括下列步骤:
[0009](I)混料:按化学结构式SivxBax0.nFe(12_y)/nRy/n03的组成要求,将与所含组分的相应氧化物原料和碳酸盐原料粉末混合后,完成一次配料,且一次添加占所加原料(SivxBax0.nFe(12_y)/nRy/n03组成成分总和)的重量比分别为0.1~1.0wt %的SiO2,0.1~1.(^%的CaCO3 ;与水,钢球按照料:7jC -M= 1:1.5:15的重量比混合,进行一次球磨I~4小时,得到悬浮颗粒平均粒径为Ι.Ομηι~1.5 μ m的混料;
[0010](2)预烧:将步骤⑴中所得混料经过过滤、干燥和造粒后,在1150~1350°C下进行预烧,保温时间I~8小时,制备出永磁铁氧体预烧料;
[0011](3)制粉:将步骤(2)中所制备的永磁铁氧体预烧料,利用粉碎机破碎,过120目筛,得到永磁铁氧体预烧粉料;
[0012](4) 二次球磨:将步骤(3)中制备的永磁铁氧体预烧粉料和所要加入的二次添加剂 0.1 ~1.8wt%^ CaCO3>0.1 ~1.0wt % ^ Si02、0.1 ~1.0wt % ^ Η3Β03、0.I ~2.0wt %的SrCO3>0.1~1.0wt %的葡萄糖酸钙、0.1~1.0wt % ^ K2MnO4,与水,钢球仍按照料:/Κ:球=1:1.5:15的重量比混合,进行二次球磨,得到悬浮颗粒平均粒径为0.50~1.ΟΟμπι的料衆;所采用钢球的直径分别为3mm、4mm、5mm,重量配比为1:1:1 ;
[0013](5)压制生坯:根据实际使用要求,控制模具形状的大小,在取向磁场> 380kA/m中进行压制生还,成型压力为6~12MPa,保压10~20s,压制成密度> 3.6g/cm3的中心单孔径圆柱体生坯;
[0014](6)烧结:将步骤(5)中的生坯在650°C下保温30分钟,随后在1130~1250°〇下,空气氧化性气氛中进行烧结,保温时间为I~6小时,升温速率为5°C /min ;
[0015](7)磨削与测量:将烧结后冷却至室温的磁块进行切割和磨削,按照GB/T3217-92国家标准进行检验、测量。
[0016]如上所述的一种高性能永磁铁氧体材料及其制备方法,其特征在于:步骤(1)中所述的氧化物原料包括Fe203、Fe3O4, K2MnO4,碳酸盐原料包括SrCO3和BaCO3 ;且均为工业纯原料。
[0017]如上所述的一种高性能永磁铁氧体材料及其制备方法,其特征在于:步骤(4)中的二次添加剂还包括工业纯的氧化物Ce02、GeO2, MnO2的一种或两种以上,氧化物(Ce02、Ga2O3^MoO3的一种或两种以上)的总量占预烧料重量比为0.01~10.0wt%。
[0018]采用本发明所述的预烧料进行二次辅料添加烧结,在烧结温度为1130°C~1200°C时,制备的高性能永磁铁氧体材料剩磁Br值达到> 392mT,内禀矫顽力H。」值达到≤ 343.lkA/m,磁能积(BH)max 值达到≤ 27.9kJ/m3。
[0019]本发明采用一次烧结制备铁氧体预烧料原料中添加一定量的K2MnO4,同时在二次添加辅料中加入MnO2,其中的K2MnO4在烧结过程中分解产生的氧气,能够提高预烧过程中铁氧体的烧结度,提高同一批次产品的性能均匀性;同时其分解的产物KMnO4起到了分散剂的作用,在烧结过程中对铁氧体成核晶粒之间产生包覆作用,利于晶粒的细化,不仅有效的解决了目前国内常用传统添加剂(CaC03、H3BO3等)不能解决剩余磁感应强度和内禀矫顽力H。」之间“相克”的难题,而且制备的永磁铁氧体SivxBax0.nFe
(12—y)/nRy/n〇3 拥有较高的
剩磁和内禀矫顽力。本发明所述的高性能永磁铁氧体材料与传统锶钡铁氧体相比,降低了烧结温度,降低了生产相同重量铁氧体预烧料的能耗,增加了产品的性能均匀性;与稀土掺杂的永磁锶或钡铁氧体相比,性价比更高;通过一次烧结过程中的经历包覆作用,起到了晶粒细化的作用,同时降低了超细粉末粒子所占的比例,从而避免了因粒子过细造成的磁件成型困难,提高了制造产品的效率。[0020]为达到上述目的,本发明通过X射线衍射仪(XRD)和扫描电子显微镜(SEM)确定物相组成和形貌,用B— H永磁特性测量仪测量永磁特征参量。
[0021]图1是实施例1中采用本发明专利预烧料制备的高性能永磁铁氧体材料的XRD衍射图谱;
[0022]图2是图1所述的高性能永磁铁氧体材料的SEM形貌图;
[0023]图3是图1所述的高性能永磁铁氧体材料的退磁曲线。
[0024]下面结合具体实施例,进一步阐述本发明。应理解,这些实施例仅用于说明本发明而不用于对本发明保护范围的限制。本发明可以按
所述的任一方式实施。
[0025]实施例1
[0026]按化学结构式SivxBax0.nFe(12_y)/nRy/n03 (x = 0.0, η = 6.0, y = 0.2, R 为 Mn 的组成要求,以工业生产的铁红(纯度为99.5% )、碳酸锶(纯度为99.05% )和工业纯的K2MnO4为原料,进行一次配料,并同时添加0.2wt% CaC03、0.3wt% SiO2作为一次添加剂,与水,钢球按照料:水:球=I:1.5:15的重量比混合,进行一次球磨2小时,得到悬浮颗粒平均粒径为1.0~1.5 μ m的混料。
[0027]混料经过滤、干 燥和造粒后,在1290°C下预烧,保温3小时,制备出M型永磁铁氧体预烧料;
[0028]随后在经粉碎、过筛后得到的预烧粉料中,加入二次添加剂,添加剂各组份添加量与所要添加的预烧粉料重量比分别如下:1.1wt % CaC03、0.3wt% SiO2,0.2wt % H3BO3>1.5wt% SrCO3和0.5wt%葡萄糖酸|丐,0.Iwt% Μη02。用滚筒式球磨机进行二次球磨,磨至平均粒径为0.65 μ m的粉粒;
[0029]在取向磁场为380kA/m,成型压力为lOMPa,保压12s,压制成平均密度为3.54g/cm3的生还。
[0030]生坯在烧结温度为1176°C下,空气氧化性氛围中烧结2小时得成品,温升速率为6°C /min。
[0031]本实施例所制备的永磁铁氧体产品经检测:剩余磁化强度Br为401.4mT ;磁感应矫顽力Hcb为302.9kA/m ;内禀矫顽力Hcj为343.lkA/m ;最大磁能积(BH)max为30.5kJ/m3。
[0032]实施例2
[0033]按化学结构式SivxBax0.ηΡθ(12_y)/ηΚy/η03 (x = 0.0, η = 6.0, y = 0.25, R 为 Mn 的组成要求,以工业生产的铁红(纯度为99.5% )、碳酸锶(纯度为99.05% )和工业纯的K2MnO4为原料,进行一次配料,并同时添加0.2wt% CaC03、0.3wt% SiO2作为一次添加剂,与水,钢球按照料:水:球=I:1.5:15的重量比混合,进行一次球磨2小时,得到悬浮颗粒平均粒径为1.0~1.5 μ m的混料。
[0034]混料经过滤、干燥和造粒后,在1290°C下预烧,保温3小时,制备出M型永磁铁氧体预烧料。
[0035]随后在经粉碎、过筛后得到的预烧粉料中,加入二次添加剂,添加剂各组份添加量与所要添加的预烧粉料重量比分别如下:1.1wt % CaC03、0.3wt% SiO2,0.2wt % H3BO3>1.5wt% SrCO3和0.5wt%葡萄糖酸|丐,0.8wt% Ce02。用滚筒式球磨机进行二次球磨,磨至平均粒径为0.64 μ m的粉粒;
[0036]在取向磁场为380kA/m,成型压力为lOMPa,保压10s,压制成平均密度为3.34g/cm3的生还。
[0037]生坯在烧结温度为1155°C下,空气氧化性氛围中烧结2小时得成品,温升速率为5°C /min。
[0038]本实施例所制备的永磁铁氧体产品经检测:剩余磁化强度Br为398.1mT ;磁感应矫顽力Hcb为295.8kA/m ;内禀矫顽力Hcj为356.3kA/m ;最大磁能积(BH)max为30.lkj/m3。
[0039]实施例3
[0040]按化学结构式SivxBax0.nFe(12_y)/nRy/n03 (x = 0.0, η = 6.0, y = 0.3, R 为 Mn 的组成要求,以工业生产的铁红(纯度为99.5% )、碳酸锶(纯度为99.05% )、工业纯K2MnO4为原料,进行一次配料,并同时添加0.2wt% CaCO3>0.3wt% SiO2作为一次添加剂,与水,钢球按照料:水:球=I:1.5:15的重量比混合,进行一次球磨2小时,得到悬浮颗粒平均粒径为
1.0~1.5 μ m的混料。
[0041]混料经过滤、干燥和造粒后,在1290°C下预烧,保温3小时,制备出M型永磁铁氧体预烧料样块;
[0042]随后在经粉碎、过筛后得到的预烧粉料中,加入二次添加剂,添加剂各组份添加量与所要添加的预烧粉料重量比分别如下:1.1wt % CaCO3>0.3wt% SiO2,0.05wt % Mo03>
0.2wt% H3BO3> 1.5wt% SrCO3和0.5wt%葡萄糖酸钙,0.7wt%、Ge02。用滚筒式球磨机进行二次球磨,磨至平均粒径为0.65 μ m的粉粒;
[0043]在取向磁场为380kA/m,成型压力为lOMPa,保压12s,压制成平均密度为3.Mg/cm3的生还。
[0044]生坯在烧结温度为1185°C下,空气氧化性氛围中烧结2小时得成品,温升速率为5°C /min。
[0045]本实施例所制备的永磁铁氧体产品经检测:剩余磁化强度Br为396.7mT ;磁感应矫顽力Hcb为295.0kA/m ;内禀矫顽力H。」为362.7kA/m ;最大磁能积(BH)max为30.4kJ/m3。
[0046]实施例4
[0047]按化学结构式SivxBax0.ηΡθ(12_y)/ηΚy/η03(χ = 0.15, η = 6.0, y = 0.15, R 为 Mn,以工业生产的铁红(纯度为99.5% )、碳酸锶(纯度为99.05% )、碳酸钡和工业纯的K2MnO4为原料,进行一次配料,并同时添加0.2wt% CaC03、0.3wt% SiO2作为一次添加剂,与水,钢球按照料:水:球=I:1.5:15的重量比混合,进行一次球磨2小时,得到悬浮颗粒平均粒径为1.0~1.5 μ m的混料。
[0048]混料经过滤、干燥和造粒后,在1290°C下预烧,保温3小时,制备出M型永磁铁氧体预烧料。
[0049]随后在经粉碎、过筛后得到的预烧粉料中,加入二次添加剂,添加剂各组份添加量与所要添加的预烧粉料重量比分别如下:1.1wt% CaCO3>0.3wt% SiO2,0.15wt% CeO2,
0.2wt% H3BO3> 1.5wt% SrCO3和0.5wt%葡萄糖酸钙,0.3wt%、Mn02。用滚筒式球磨机进行二次球磨,磨至平均粒径为0.64 μ m的粉粒。[0050]在取向磁场为380kA/m,成型压力为8MPa,保压12s,压制成平均密度为3.14g/cm3的生坯。
[0051]生坯在烧结温度为1185°C下,空气氧化性氛围中烧结2小时得成品,温升速率为5°C /min。
[0052]本实施例所制备的永磁铁氧体产品经检测:剩余磁化强度Br为392.5mT ;磁感应矫顽力Hcb为292.4kA/m ;内禀矫顽力Hcj为373.0kA/m ;最大磁能积(BH)max为30.4kJ/m3。
一种自供氧永磁铁氧体预烧料单孔径坯料的制备与烧结制作方法
- 专利详情
- 全文pdf
- 权力要求
- 说明书
- 法律状态
查看更多专利详情
下载专利文献
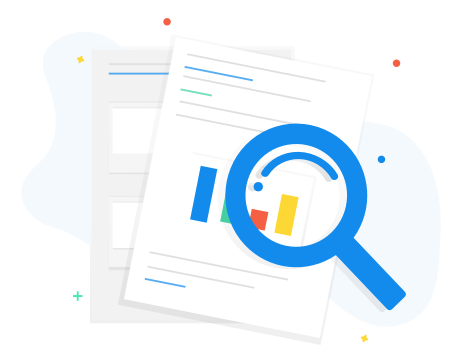
下载专利
同类推荐
-
齐锦刚齐锦刚李小龙许建益, 郑杰李前军
您可能感兴趣的专利
-
建方方建方方须佐昌司牛晓飞
专利相关信息
-
于树红吴云飞任新民任新民任新民任新民