轨道交通安全站台生产系统和生产方法[0002]目前在轨道(铁路、地铁、轻轨等)交通站台施工中普遍采用的现场浇筑方式,手工绑扎钢筋骨架,现场浇注混凝土 ;轨道与站台的间距较近,无躲避(逃生)空间;现场浇筑施工中一般不采取防腐措施。[0003]并且现有站台施工环境差、周期长、工效低;由于轨道与站台的间距较近,机车驶来时,轨道维护工作人员或跌入轨道的旅客无躲避(逃生)空间,往往造成人身伤亡事故;无防腐措施,耐久性较差,影响使用寿命。
[0004]为克服现有的缺陷,本发明提出一种轨道交通安全站台生产方法以及实施该方法所用的轨道交通安全站台生产系统。[0005]根据本发明的一个方面,提出了一种现场浇筑轨道交通安全站台的方法,所述方法包括以下步骤:制作站台构件;和在将多个制作好的站台构件设置到适当位置处后现场烧筑站台主体,使站台主体与所述站台构件齐平,其中制作站台构件包括以下步骤:在站台构件成型模具内涂刷脱模剂;制作耐腐蚀混凝土轨道交通站台的站台构件的钢筋骨架并检验;将所述站台构件的钢筋骨架装入所述站台构件模具内;将制备耐腐蚀混凝土并将制备好的耐腐蚀混凝土浇注到所述模具内;采用振动工艺使耐腐蚀混凝土浇注成型;完成上口抹平;将浇注成型的耐腐蚀混凝土连同所述模具一起放入养护工位;将浇注成型的耐腐蚀混凝土连同所述模具一起进行蒸养处理;和脱模、并将已固化的站台构件转入堆场自然养护。[0006]优选地,所述耐腐蚀混凝土为碱激发矿渣粉煤灰混凝土。[0007]优选地,所述耐腐蚀预制装配式混凝土轨道交通站台为耐腐蚀介质范围为pH值
2.0-13.0的站台。
[0008]优选地,所述蒸汽养护温度控制在50-10(TC,升温速率控制在20_25°C /h,整个蒸汽养护过程时间控制在6-8h。
[0009]优选地,所述混凝土为强度等级> C35,预制构件设计承载力> 4.0kPa0
[0010]优选地,浇筑所述站台主体的耐腐蚀混凝土与制作所述站台构件的耐腐蚀混凝土相同。
[0011]优选地,在将多个站台构件设置在适当位置处的步骤包括使多个站台构件的凹入部面对轨道设置。
[0012]根据本发明的另一方面,提出了一种实施该轨道交通安全站台生产方法所用的轨道交通安全站台生产系统,所述系统包括:站台构件生产系统,所述站台构件生产系统用于生产站台构件;和站台主体生产系统,所述站台主体生产系统与生产好的站台构件在所述轨道交通安全站台的现场安置位置相邻接,其中所述站台构件生产系统包括:1区、2区、3区、4区、5区、6区、7区、8区、9区、10区和11区,I区通过第一水平传动装置与2区相连接,2区通过第一传动装置与3区相连接,3区通过第一推送装置与4区相连接,4区通过第二水平传动装置与5区相连接,5区通过第二传动装置与6区相连接,6区通过第二传动装置与7区相连接,7区通过第二传动装置与8区相连接,8区通过第二推送装置与9区相连接,9区通过第一水平传动装置与10区相连接,10区与11区相连接,和11区与I区相连接,从而使所述站台构件生产系统构成闭环生产系统。
[0013]优选地,待生产的站台构件在I区完成喂料、成型、振动工艺;由第一水平传动装置将制作的站台构件连同所述站台构件成型模具一起运送到2区,在2区完成上口抹平工序,再运送至3区;所述3区为摆渡区,由第一推送装置将制作的站台构件连同模具一起从3区推送至4区,在4区完成静停工序;由4区通过第二水平传动装置按顺序将制作的站台构件连同模具依次运送到5区、6区、7区,在5区、6区、7区分别完成制品养护过程中的升温、恒温、降温阶段;7区完成降温工序之后,运送到8区;所述8区为另一摆渡区,在8区由第二推送装置将养护后的站台构件连同模具一起推送到9区;在9区完成拆模工艺;9区完成拆模之后,站台构件由起重设备吊运至成品堆场,模具由第一水平传动装置运送到10区、11区分别完成清模、装模工艺;模具由第一水平传动装置送回到I区,从而形成一个首尾相连的闭环生产流水线。
[0014]优选地,通过所述站台构件生产系统制成的站台构件被送到所述轨道交通站台处,所述站台构件在一侧具有凹入部,并且所述凹入部面向轨道安置,而与所述站台构件的所述凹入部相对的侧部与所述站台主体生产系统相邻接,从而在轨道交通安全站台现场进行站台主体的浇筑。
[0015]图1为根据本发明实施例的轨道交通安全站台生产系统的平面图。
[0016]图2为图1中的根据本发明实施例的轨道交通安全站台的站台构件生产系统的平面图。
[0017]图3为根据本发明实施例的轨道交通安全站台的立体示意图。
[0018]图4为根据本发明实施例的轨道交通安全站台的站台构件的立体透视图。
[0019]图5A-5F为根据本发明实施例的轨道交通安全站台的站台构件的截面图。
[0020]图6为生产根据本发明实施例的交通站台的流程图。
[0021]下面结合附图和具体实施例对本发明提供的轨道式交通安全站台的结构、生产该轨道式交通站台的系统以及生产方法进行详细描述。
[0022]图1示出了根据本发明实施例的轨道交通安全站台的生产系统。如图1所示,轨道交通安全生产系统包括站台构件生产系统1000、和与站台构件安置现场位置相邻接的站台主体生产系统2000。具体地,在站台构件生产系统1000处所生产的站台构件被送到轨道交通安全站台现场安置位置3000处,而站台主体生产系统2000与该现场安置位置相邻接。[0023]图2显示了图1中所描述的站台构件生产系统1000的具体结构。如图2所示,站台构件生产系统1000包括I区、2区、3区、4区、5区、6区、7区、8区、9区、10区、和11区。具体地,I区通过第一水平传动装置与2区相连接,2区通过第一传动装置与3区相连接,3区通过第一推送装置与4区相连接,4区通过第二水平传动装置与5区相连接,5区通过第二传动装置与6区相连接,6区通过第二传动装置与7区相连接,7区通过第二传动装置与8区相连接,8区通过第二推送装置与9区相连接,9区通过第一水平传动装置与10区相连接,10区与11区相连接,和11区与I区相连接,这样,整个站台构件生产系统本身可以构成一个闭环生产系统。
[0024]具体的站台构件生产流程如图2所示,在I区完成喂料、成型、振动工艺;由第一水平传动装置将产品连同成型模具运送到2区,在2区完成上口抹平工序,再运送至3区;3区为摆渡区,由第一推送装置将制作的站台构件连同模具一起从3区推送至4区,在4区完成静停工序;由4区通过第二水平传动装置按顺序将制作的站台构件连同模具依次运送到5区、6区、7区,在5区、6区、7区分别完成制品养护过程中的升温、恒温、降温阶段;7区完成降温工序之后,运送到8区;8区为另一摆渡区,在8区由第二推送装置将养护后的站台构件连同模具一起推送到9区;在9区完成拆模工艺;9区完成拆模之后,站台构件由起重设备吊运至成品堆场,模具由第一水平传动装置运送到10区、11区分别完成清模、装模工艺;模具由第一水平传动装置送回到I区,从而形成一个首尾相连的闭环生产流水线。
[0025]站台构件的具体生产步骤如下:首先,将预制耐腐蚀混凝土轨道交通站台的站台构件成型模具进行清理(这将在10区内进行);然后,在所述内模具内涂刷脱模剂(在10区内进行);之后,制作耐腐蚀混凝土轨道交通站台的站台构件的钢筋骨架并检验;然后将所述站台构件的钢筋骨架装入所述模具内(在11区内进行);然后将装有钢筋骨架的模具运送到I区准备进行浇筑;在浇筑前,首先要制备耐腐蚀混凝土 (在I区进行);然后将制备好的耐腐蚀混凝土浇注到装有钢筋骨架的模具内(在I区进行);之后,采用振动工艺使耐腐蚀混凝土浇注成型(在I区进行);然后将在I区内浇筑的构件及其模具一起运送到2区进行上口抹平工序(在2区进行);之后,将浇注成型的耐腐蚀混凝土连同所述模具一起放入养护工位(在3、4区进行);然后,将浇注成型的耐腐蚀混凝土连同所述模具一起进行蒸养处理(在
5、6、7区进行);和在9区进行脱模处理、并将已固化的站台构件转入堆场自然养护。
[0026]图3示出了根据本发明实施例的轨道交通安全站台的立体示意图。如图3所示,轨道交通安全站台100主要由多个站台构件110和站台主体120两部分组成,其中站台构件110和站台主体120在高度上和宽度上都齐平。
[0027]以下,将参照图4-5F具体描述站台构件110的结构。
[0028]站台构件110是具有近似U形横截面的构件,其面向轨道的一侧具有向内凹入的凹入部。可以按照图中沿着站台构件设置单层或者多层配筋,根据实际需要可全部选用预应力筋或者预应力筋和非预应力筋搭配使用。
[0029]具体地,该配筋可以是加强肋的形式,例如图4-5F所示,可以在凹入部的内表面从凹入部的顶部到凹入部的底部横跨地设置有至少一条加强肋A,或者不设有加强肋A。
[0030]图5A为不具有加强肋的站台构件的截面图、图5B为具有一条加强肋的站台构件的截面图、图5C和为具有两条加强肋的站台构件的截面图、图5E和5F为具有3条加强肋的站台构件的截面图。如图5A-5F所示,加强肋的数量可以是I条或2条或多条,或者不设有加强肋。当设置I条加强肋时,可以将加强肋设置在凹入部的中间位置处;当设置2条加强肋时,可以将2条加强肋对称地设置在凹入部的两端或靠近两端的位置处;当设置3条及其以上加强肋时,加强肋均匀分布,可以将最外侧2条加强肋对称地设置在凹入部的两端或靠近两端的位置处。图中仅显示了设置1-3条加强肋以及不设置加强肋的情况,但是本发明不局限于此,加强肋的数量可以根据站台所需要的客流承载要求增加或减少,具体的数量可以由设计人员根据不同客流承载要求进行选择采用。
[0031]此外,还可以在站台构件的侧部设置接口,从而使多个站台构件彼此契合地紧密接合在一起。接口可以是相应地设置在站台构件的侧部的顶部位置处的顶部接口、设置在中部位置处的中部接口或者设置在拐角位置处的拐角接口,相邻的两个站台构件可以通过这些接口紧密地接合在一起。
[0032]接口可以被设置成弧形、梯形等凹凸承插口形式,但是本发明不局限于此,接口也可以被设置成其它形状,只要相邻的两个接口能够彼此契合地接合在一起即可。采用承插式接口主要是为了方便拼装,并使所有站台保持同一高度不(上下、前后)错位,使不同形式的接口按形状一一对应。
[0033]在本发明中,如图3所示,多个站台构件彼此契合地紧密接合在一起,其凹入部也彼此连通,从而在拼装铺设后,整条站台的凹入部分均可作为安全逃生空间,不需要再设定其它固定安全逃生位置,这是与现有平面站台的最大区别。
[0034]图2显示了轨道交通安全站台的站台构件生产系统。如图2所示,该生产系统包括I区、2区、3区、4区、5区、6区、7区、8区、9区、10区、和11区。具体地,I区通过第一水平传动装置与2区相连接,2区通过第一传动装置与3区相连接,3区通过第一推送装置与4区相连接,4区通过第二水平传动装置与5区相连接,5区通过第二传动装置与6区相连接,6区通过第二传动装置与7区相连接,7区通过第二传动装置与8区相连接,8区通过第二推送装置与9区相连接,9区通过第一水平传动装置与10区相连接,10区与11区相连接,和11区与I区相连接,这样,整个生产系统构成一个闭环生产系统。
[0035]具体生产流程如图2所示,在I区完成喂料、成型、振动工艺;由第一水平传动装置将产品连同成型模具运送到2区,在2区完成上口抹平工序,再运送至3区;3区为摆渡区,由第一推送装置将制作的站台构件连同模具一起从3区推送至4区,在4区完成静停工序;由4区通过第二水平传动装置按顺序将制作的站台构件连同模具依次运送到5区、6区、7区,在5区、6区、7区分别完成制品养护过程中的升温、恒温、降温阶段;7区完成降温工序之后,运送到8区;8区为另一摆渡区,在8区由第二推送装置将养护后的站台构件连同模具一起推送到9区;在9区完成拆模工艺;9区完成拆模之后,站台构件由起重设备吊运至成品堆场,模具由第一水平传动装置运送到10区、11区分别完成清模、装模工艺;模具由第一水平传动装置送回到I区,形成一个首尾相连的闭环生产流水线。
[0036]轨道交通安全站台的站台构件的具体生产步骤如下:将预制耐腐蚀混凝土轨道交通站台的站台构件成型模具进行清理(在第10区进行);在所述内模具内涂刷脱模剂(在第10区进行);制作耐腐蚀混凝土轨道交通站台的站台构件的钢筋骨架并检验;将所述站台构件的钢筋骨架装入所述模具内(在第11区进行);制备耐腐蚀混凝土并将制备好的耐腐蚀混凝土浇注到所述模具内(在第I区进行);采用振动工艺使耐腐蚀混凝土浇注成型(在第I区进行);完成上口抹平(在第2区进行);将浇注成型的耐腐蚀混凝土连同模具一起放入养护工位(在第3区、4区进行);将浇注成型的耐腐蚀混凝土连同模具一起进行蒸养处理(在第5区、6区、7区进行);和脱模(在第9区进行)、并将已固化的站台构件转入堆场自然养护。
[0037]在本发明中,浇筑站台主体和站台构件所用的耐腐蚀混凝土采用“碱激发矿渣粉煤灰混凝土”来取代传统的普通混凝土。混凝土中采用低碱的碱激发矿渣粉煤灰替代传统的高碱度硅酸盐水泥作为胶凝材料,有效降低了混凝土的碱度和碱集料反应。实验表明:碱激发粉煤灰矿渣混凝土在酸、碱、盐中都有较好的耐腐蚀能力,比普通混凝土的耐腐蚀能力高2~3倍以上。因此,采用“碱激发矿渣粉煤灰混凝土”制作耐腐蚀预制轨道交通安全站台产品也具备了对酸、碱、盐中都有较好的耐腐蚀能力。具体而言,由上述耐腐蚀混凝土浇筑的轨道交通站台为耐腐蚀介质范围为PH值2.0-13.0的站台。混凝土的强度等级≥C35,预制构件设计承载力≥4.0kPa0因此,与现有的现场浇筑式混凝土站台相比,其耐腐蚀能力高2~3倍以上,耐腐蚀预制轨道交通安全站台的使用寿命也可增加2~3倍,延长了预制轨道交通安全站台的使用寿命,尤其适用于地铁或高盐高碱腐蚀地区的站台建设,降低后期维护成本。
[0038]在铺设轨道之前或之后,将预制好的多个站台构件放置在适当的位置(站台构件在安置时其凹入部面向轨道),并使多个站台构件在轨道站台施工现场通过拼插等方式紧密地接合在一起,并使多个站台构件表面齐平(接合不发生错位),然后,在安置好的站台构件的凹入部的相对侧现场设置安全轨道交通站台的站台主体生产系统,从而可以通过在现场搭设钢筋等支承结构进行站台主体的浇筑(也可采用预制混凝土块进行现场拼装)。由于多个站台构件的凹入部互相连通,从而构成了逃生空间,因此在现场浇筑过程中大大缓解了施工安全以及工效低的问题,并且由于采用“碱激发矿渣粉煤灰混凝土”来取代传统的普通混凝土进行站台构件以及站台主体的浇筑,不仅解决了站台混凝土抗性差的问题,还大大提高了工作效率,降低了劳动强度,改善了施工环境。
[0039]本发明采用工厂化生产,施工现场组装,可有效缩短施工周期,降低施工人员的劳动强度,施工现场文明;本发明带有的安全逃生空间,可有效降低或避免人身伤亡事故的发生,并且可取消地铁和轻轨站台常用的隔离门,降低工程造价;
[0040] 最后应说明的是,以上实施例仅用以描述本发明的技术方案而不是对本技术方法进行限制,本发明在应用上可以延伸为其他的修改、变化、应用和实施例,并且因此认为所有这样的修改、变化、应用、实施例都在本发明的精神和教导范围内。
轨道交通安全站台生产系统和生产方法
- 专利详情
- 全文pdf
- 权力要求
- 说明书
- 法律状态
查看更多专利详情
下载专利文献
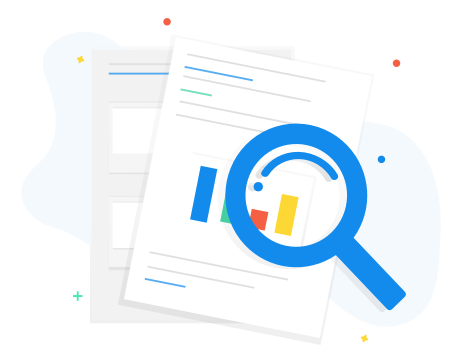
下载专利
同类推荐
-
匡红杰S·兰兹张亚锋, 胡长坤蓝润宾, 陈建议蓝润宾, 陈建议蓝润宾, 陈建议
您可能感兴趣的专利
-
蓝润宾, 陈建议刘夫娟刘夫娟崔桂玲
专利相关信息
-
崔桂玲裴明, 郑诗阳裴明, 郑诗阳刘占杰刘占杰